Guía
El control de calidad del proceso de corte es crucial en la primera etapa de producción para las empresas. Dado que el oxicorte es el principal método de corte y corte, garantizar la calidad de la producción tendrá un gran impacto en el proceso general de corte y corte.
Este artículo se centra en los factores que influyen en la calidad del oxicorte y proporciona soluciones a problemas de corte comunes a través de métodos de proceso.
A pesar de su importancia como principal método de corte para pequeñas, medianas y grandes empresas, el oxicorte tiene sus desafíos.
Con el paso de los años, el oxicorte ha evolucionado y los equipos de corte CNC se han vuelto avanzados y sofisticados. Como resultado, se han desarrollado varios métodos y técnicas de proceso para mejorar la calidad del oxicorte.
En este artículo, utilizamos el software de anidamiento automático XSuperNEST para examinar los factores que afectan la calidad de las piezas cortadas mediante oxicorte y las formas de mejorar su rendimiento.
Factores que influyen en el equipo de corte
Actualmente, el mercado ofrece una variedad de métodos y equipos de corte, como corte por láser, plasma y agua, que ofrecen mejor calidad de corte y eficiencia de producción que el corte por llama. A pesar de esto, el oxicorte sigue siendo popular debido a su menor costo y todavía se usa ampliamente como método de corte primario.
Las máquinas de corte por llama CNC se utilizan cada vez más en el proceso de producción de corte. Estas máquinas ofrecen la ventaja de una programación sin intervención, pero esta característica también hace imposible que los trabajadores compensen la deformación térmica durante el proceso de corte, lo que genera desviaciones en la precisión dimensional.
Además, algunos factores relacionados con la propia máquina de corte CNC también pueden afectar la calidad del corte.
Factores que afectan la calidad del corte.
(1) Selección de gas de corte
La elección del gas de corte tiene un impacto significativo en la calidad de los cortes de las máquinas de oxicorte. Actualmente los gases disponibles son acetileno, propileno, propano y MPS. Cada gas tiene características de combustión únicas, lo que lleva a diferentes escenarios de corte, y elegir el gas apropiado puede maximizar los beneficios del corte con gas, lo que lleva a un corte eficiente y económico.
La llama de acetileno se caracteriza por su calor concentrado, alta temperatura, corto tiempo de precalentamiento, bajo consumo de oxígeno, alta eficiencia de corte y mínima deformación de los componentes. Esto lo hace adecuado para cortar láminas finas y piezas cortas.
Por otro lado, la llama de propano tiene calor disperso, baja temperatura y mayor tiempo de precalentamiento en comparación con el acetileno. También da como resultado un borde superior liso y plano del corte y menos escoria en el borde inferior, que es más fácil de eliminar. Además, su coste relativamente bajo lo convierte en una opción económica para cortar grandes piezas de chapa gruesa.
La llama de propileno tiene una temperatura más alta y un tiempo de precalentamiento más corto en comparación con el propano, ligeramente superior al del acetileno. Su alto contenido de calor en la llama externa lo hace adecuado para cortar grandes piezas de chapa gruesa.
(2) Selección de concentración de oxígeno, velocidad y altura de la boquilla de corte.
Además de la selección adecuada del gas, la presión de oxígeno de corte, la velocidad y el ajuste de la altura de la boquilla también son factores cruciales que afectan la calidad del corte con llama.
Se observó que al aumentar la concentración de oxígeno disminuye el tiempo de corte y reduce la demanda de oxígeno, con la misma presión de oxígeno.
La elección de la velocidad de corte es especialmente importante. Si la velocidad es demasiado alta, puede causar defectos de calidad como apagado, corte irregular y reducción de la eficiencia del corte. Por otro lado, si la velocidad es demasiado lenta, puede provocar la adhesión de escoria de oxidación y una superficie de corte desigual.
Según la experiencia práctica, la mejor velocidad de corte debe estar en el rango medio superior a medio superior de la velocidad nominal de la boquilla de corte. Por ejemplo, cuando se utiliza una boquilla número 5 para cortar una placa de acero de 40 mm, el rango de velocidad nominal es de 250 ~ 380 mm/min, con una velocidad promedio de 315 mm/min. Al dividir el rango en 10 niveles, la mejor velocidad está entre 336,6 ~ 358 mm/min, siendo 340 mm/min la opción ideal.
La elección de la altura de la boquilla de corte también influye en la calidad del corte. Si el centro de la llama es demasiado bajo, puede entrar en contacto con la superficie de la pieza, provocando que el corte colapse, que salpique escoria que bloquee la boquilla o incluso que se temple. Por otro lado, si la altura es demasiado alta, la llama no puede calentar completamente el corte, reduciendo la capacidad de corte y dificultando la eliminación de la escoria. Generalmente se recomienda mantener una distancia de 3 a 5 mm entre el centro de la llama y la superficie de trabajo para obtener mejores resultados.
(3) Orden de corte y aplicación de plomo
Un orden de corte razonable promueve un calentamiento uniforme de la placa de acero y compensa las tensiones internas, reduciendo la deformación térmica de las piezas.
Al cortar el contorno de las piezas, se recomienda seguir el principio de primero adentro y luego afuera, primero pequeño y luego grande, primero redondo y luego cuadrado, talón cruzado, primero complicado y luego simple, para evitar desplazamientos, deformaciones y desviaciones de tamaño. de las partes.
Una posición y forma de avance adecuadas pueden mantener la integridad de la muesca de la pieza de trabajo y mejorar la estabilidad del corte, asegurando la calidad del contorno.
En la producción práctica, la posición de entrada del contorno exterior suele estar situada en el lado derecho de la parte inferior del contorno, y la forma del contorno interior se representa mejor mediante un arco circular.
Proceso optimizado
Incluso después de una perfecta configuración y depuración de los parámetros del equipo de oxicorte, no hay garantía de que las piezas se corten sin defectos. La forma de la pieza, el grosor de la placa, la posición del material de encaje y el método de corte pueden afectar la calidad del corte.
Por ejemplo, las placas oxicorte se pueden dividir en placas delgadas (espesor <20 mm), placas de espesor medio y placas gruesas.
Las tablas delgadas son fáciles de perforar durante el proceso de corte, pero son propensas a deformarse térmicamente. Para reducir la deformación térmica y la curvatura de las piezas, se recomienda cortar desde el interior de la chapa de acero en lugar de en la posición del borde. Esto ayuda a mantener la integridad de la estructura externa de la placa de acero.
El uso del proceso de “corte continuo” puede reducir la cantidad de perforaciones, mientras que el proceso de “corte permanente” puede reducir efectivamente la deformación térmica.
Para placas gruesas y medianas, la deformación térmica es mínima durante el proceso de corte, pero los pinchazos pueden provocar escoria y daños en la boquilla de corte. Para reducir las perforaciones se recomienda precalentar los bordes antes de comenzar a cortar. La Figura 1 muestra el método de corte convencional con precalentamiento de bordes.
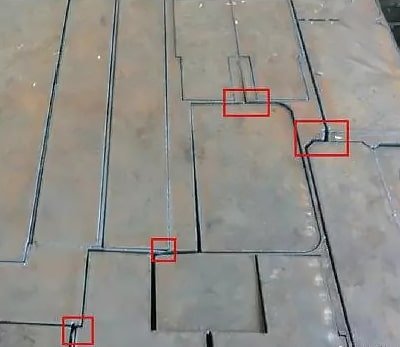
Figura 1 Método de corte de plomo convencional con precalentamiento de bordes
(1) Perforación con precalentamiento reducido mediante el proceso “perforación I”
El método convencional de corte de plomo con precalentamiento de bordes puede resolver eficazmente el problema de perforación del corte de placas gruesas y medianas, pero requiere muchos ajustes humanos en la descarga y requiere personal de colocación de alta calidad y precisión de la máquina de corte.
Para resolver este problema, el software XSuperNEST ofrece un nuevo "proceso I-drilling" para optimizar la ruta de corte y perforación.
El método de corte de plomo con precalentamiento del borde del punzón I encuentra automáticamente un lugar adecuado para cortar un orificio circular inferior según el contorno exterior de la pieza cortada y utiliza el orificio circular para introducir la siguiente pieza para precalentar, reduciendo las perforaciones.
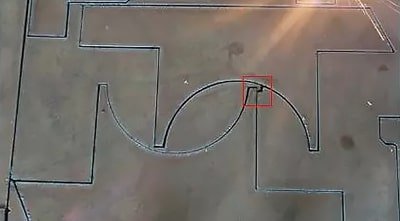
Figura 2 I Método de corte de plomo con precalentamiento de borde perforado
(2) Uso del proceso de “corte continuo” para mejorar la eficiencia del corte
Para mejorar la utilización del material, las piezas pequeñas a menudo se anidan dentro del contorno interior de piezas más grandes, y la ruta de corte generalmente implica cortar primero la parte del contorno interior, luego pasar a cortar la siguiente parte del contorno interior y, finalmente, cortar los dos contornos interiores por separado. Esto da como resultado una baja eficiencia de corte ya que la máquina cortadora tiene que levantar la pistola varias veces y perforar el agujero varias veces.
Para resolver este problema, la trayectoria de corte se puede optimizar utilizando el proceso de “corte continuo” para reducir el proceso de perforación y vaciado. La Figura 3 muestra la secuencia de corte optimizada después de utilizar el proceso de “corte continuo”.
En la Figura 3, cada parte dentro del contorno interior se corta en una fila, seguido del corte del contorno interior en una fila. Esto permite cortar piezas dentro del contorno interior y del contorno interior con un solo orificio, lo que mejora significativamente la eficiencia del corte.
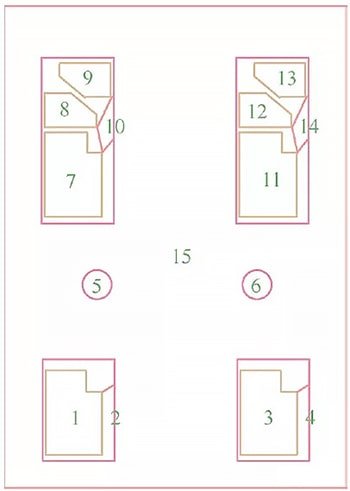
Figura 3 Secuencia de corte después de la optimización del proceso de “corte continuo”
(3) Utilizar el proceso de “permanecer cortado” para reducir la deformación térmica de las piezas
En el proceso de cortar el contorno interior de una pieza, puede haber una discrepancia entre el tamaño real y el tamaño teórico entre los contornos interior y exterior.
Por ejemplo, como se muestra en la Figura 4, las dimensiones teóricas marcadas para una pieza con un espesor de 50 mm son 610 mm, pero las dimensiones reales después del corte son de 3 a 5 mm más pequeñas.
Esto se debe a la acumulación de calor al cortar el contorno interior, que aumenta aún más al cortar el contorno exterior. Dado que no hay soporte en el contorno interior al cortar el contorno exterior, el calor extruye el contorno exterior hacia dentro, provocando la deformación de la pieza.
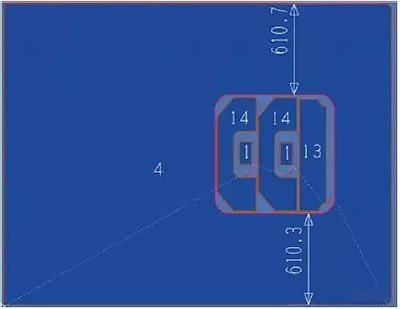
Figura 4 Diagrama de agrupación de piezas
En esta situación, agregar un proceso de “mantener el corte” puede ser una solución.
Como se muestra en la Figura 5, el "corte fijo" se agrega alrededor del contorno interior para mantener el contorno del marco del contorno interior y proporcionar soporte a la pieza.
Este método reduce eficazmente los errores de corte y mejora la precisión del corte, pero la desventaja es que el contorno interior requiere pulido.
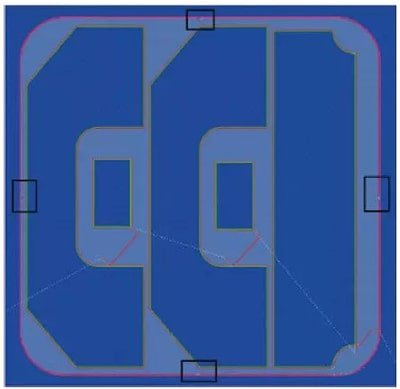
Figura 5 Ruta de corte después de la optimización del proceso de “mantener corte”
(4) El uso de la introducción de arco para reducir la quema excesiva del orificio redondo interior.
El método de entrada tradicional implica cortar el contorno de la pieza usando una línea recta a lo largo del borde recto del contorno y luego a lo largo del borde recto de la entrada. Esto no afecta la calidad del corte siempre y cuando el inicio de la inserción de la pieza sea recto.
Sin embargo, al cortar el orificio circular interior, el método de inserción tradicional provoca una falta de transición suave al cortar directamente en el contorno, lo que provoca una quema excesiva del contorno y afecta la calidad del corte, como se muestra en la Figura 6.
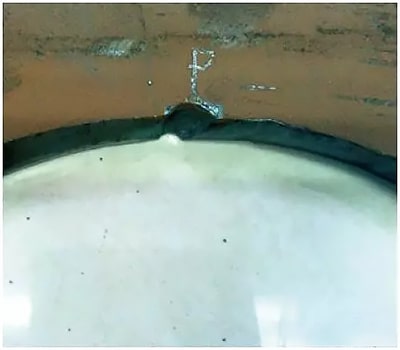
Figura 6 Quemado excesivo del orificio redondo interior
Durante el proceso de investigación, XSuperNEST introdujo el método de introducción de arco para evitar que el arco se queme excesivamente y mejorar la calidad de corte del orificio circular interior de la pieza de trabajo.
El método de corte por inserción de arco, que se muestra en la Figura 7, utiliza un arco tangente al orificio circular interior para crear una transición suave, dejando un espacio con el punto de inserción inicial y conectándose suavemente con un arco circular.
Se ha verificado y confirmado que este método es efectivo mediante la producción real, como se muestra en la Figura 8.
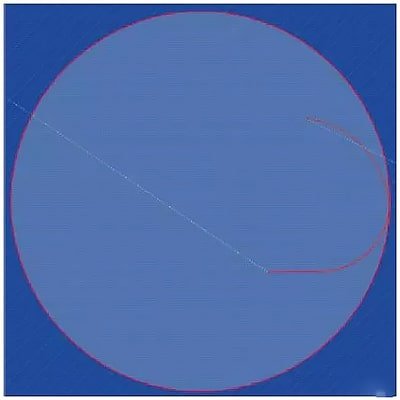
Figura 7 Arco circular que conduce al corte.
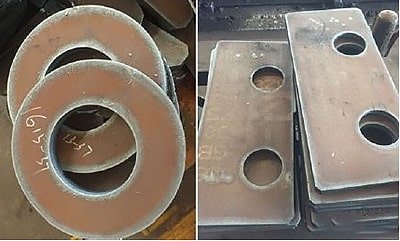
Figura 8 Uso de arcos circulares para guiar las piezas cortadas
Conclusión
El moldeado, como etapa inicial de la producción, es fundamental para el éxito de una empresa. El oxicorte, al ser el principal método de corte, tiene un impacto directo en la calidad y productividad de la producción.
Por lo tanto, es imperativo controlar eficazmente la calidad del oxicorte.
Hay varios factores que afectan la calidad del corte, incluido el equipo en sí, la elección del gas, la velocidad de corte, la altura de la boquilla, la secuencia de corte y más.
Al utilizar parámetros apropiados basados en las condiciones de producción reales, se puede mejorar la calidad del corte y aumentar la tasa de piezas calificadas.
Además, al optimizar la trayectoria de corte mediante el uso del proceso de corte apropiado en función del espesor, la forma del contorno y otras características de las piezas, se puede reducir el error de producción de las piezas y se puede mejorar la eficiencia y la calidad del corte de las piezas. y, en última instancia, se puede aumentar la eficiencia de producción de la empresa.