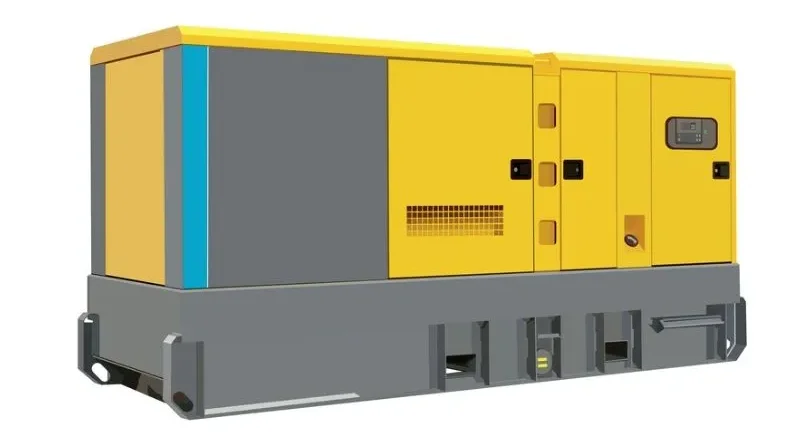
Understanding the complexities of building and maintaining a diesel plant is like climbing Everest. But what if that's not the case? On this journey, we unlock the secrets of these technological giants, simplify complex principles into easily digestible chunks of knowledge, and provide the knowledge you need to evaluate or even manage your diesel plant. Rethink your knowledge of diesel power plants as we delve beneath the surface of these industry giants.
A diesel power plant is a thermal power generation system that uses diesel engines to generate electricity through compression ignition. The mechanical energy from the diesel engine is connected to an electrical generator, which converts it into electrical energy. Diesel power plants are versatile due to their reliability and ability to provide continuous power supply and can be used in a variety of areas such as industrial plants, hospitals, data centers, ships, and remote and off-grid locations.
Components of a diesel power plant
Diesel power plants are essential for industrial production, hospital operations, ships, remote off-grid locations and other applications that may not be connected to the electrical grid. Simply put, a diesel power plant generates electricity by using diesel fuel to convert mechanical energy into electrical energy. At the heart of the diesel power plant are these main components: diesel engine, generator, fuel tanks and control systems.
The purpose of these components is to work together in harmony to produce electricity when connected to load circuits, either directly or through transformers.
- Diesel plants represent around 18% of the world's electricity generation capacity.
- According to Environment Canada, diesel engines used primarily to generate electricity can produce up to 75% fewer emissions than older models, thanks to advances in emissions control technology.
- According to a US Department of Energy report, modern diesel power plants have an efficiency of over 40 percent, which is significantly higher than comparable power plants from a few decades ago.
Role of main engine and generator
The main engine and generator are undoubtedly the most important components of a diesel power plant. The diesel engine is the heart of a diesel power plant and works with compression ignition. It burns fuel to produce heat, producing gases that drive pistons associated with rotational movement. This mechanical energy produced by the engine rotates a shaft that is connected to an electrical generator.
The electrical generator used in a conventional diesel power plant uses electromagnetic induction principles to convert mechanical energy into electrical energy. The rotary movement of the main motor causes the magnets in the copper coils to rotate in a magnetic field, generating alternating current (AC) that is fed into the transformers.
Regular maintenance and lubrication are necessary for the longevity and reliability of all components, but especially these two main components. They require tests like oil analysis, fuel analysis, bore inspection, turbocharger integrity testing, etc.
For example, a common problem with diesel engines is overheating caused by faulty cooling systems that damage piston rings and cylinder liners. This damage can be detected early through regular maintenance testing.
Fuel Storage and Control System
A fuel storage system in a diesel power plant is essential for the efficient operation of the plant. Diesel fuel is stored in tanks that range from small capacities for emergency generators to much larger tanks that can provide several days or even weeks of uninterrupted operation.
But what benefit can the control system bring?
The control system controls the flow of fuel from the tank and ensures it is synchronized with the engine's needs. This synchronization helps maintain engine speed and ensures efficiency and smooth operation. Control systems monitor several parameters, including fuel level, pump operation, temperature and pressure.
Modern control systems include programmable logic controllers (PLCs), human-machine interfaces (HMI), and supervisory control and data acquisition (SCADA) systems that provide real-time monitoring of critical parameters. These advanced systems are necessary to increase efficiency while maintaining reliability.
For example, an HMI operator can display a warning message on its screen in the event of a malfunction or irregularities in fuel flow or level. They can then take immediate action to fix the problem before more serious problems arise.
The control system in the fuel storage system of a diesel power plant plays a crucial role in efficient and smooth operation. It controls the flow of fuel from the tanks and synchronizes it with the engine's needs to maintain its speed and efficiency. Modern control systems use advanced technologies such as PLCs, HMIs and SCADA systems to monitor critical parameters in real time. These systems allow operators to receive alarms and take immediate action in the event of errors or irregularities, ensuring reliability and preventing potential problems.
Construction of a diesel power plant
When building a diesel power plant, certain steps must be followed. First, determine your power needs – this will determine what type of generator you need for your specific needs. After determining your energy needs, obtain all necessary permits from local authorities before construction.
Next comes the construction of the foundation. At this stage, a trench is dug where power lines and cables will later be installed. After pouring concrete into this trench and installing rebar or mesh in the trench walls, wait for the concrete to harden before erecting steel or metal structures.
After the structures that serve as support structures for equipment such as engines or turbines are built, piping systems are installed that run through these structures and transport coolant, fuel, and waste products such as diesel exhaust.
After the piping systems are installed, the generators can be mounted on their structures according to the manufacturer's instructions. Electrical cables are installed immediately after the generators are installed. Make sure everything is properly connected and grounded.
The final step is testing. At this stage, all equipment is checked for functional problems such as leaks or malfunctions. After successful tests, licenses are obtained before the diesel plant comes into operation.
Now that we have established the basic steps for building a diesel power plant, we need to make some important considerations.
Important Considerations
Diesel power plants have become indispensable for many industries that require a reliable and uninterrupted power supply. Before building a diesel power plant, several factors must be considered to ensure optimal performance and longevity. First, the energy requirements of the system must be determined. Secondly, licenses must be obtained, environmental impact assessments carried out and emissions regulations respected during the planning phase. Additionally, fuel storage and availability, cooling systems, and compatibility of motor generators with electrical loads must be important considerations.
Important considerations |
Power Requirements |
Licenses and environmental impact assessments |
Compliance with emissions regulations |
Fuel storage and availability |
Cooling systems |
Deadlines and phases
Building a diesel power plant is a mammoth task and can take anywhere from six months to several years, depending on capacity and complexity. The general phases of this process include site preparation, installation of generators, fuel storage systems, exhaust gas treatment systems, refrigeration systems (and sometimes heaters), installation of monitoring equipment with wiring throughout the facility. (for monitoring purposes) and other components. Construction times are not limited to these aspects and may vary depending on project plans.
The first phase of building a diesel power plant involves preparing the site by removing existing trees or structures. Once the site is clear, excavation can begin, which may take a few weeks or months depending on the earthmoving equipment used.
After the site preparatory works have been completed, the generators and their respective control systems must be installed, as they form the backbone of any diesel power plant. Generators must then be thoroughly tested before being connected to a power source.
Then, fuel storage tanks must be built, if they do not already exist, or if new ones are needed to expand capacity. Fuel storage tanks require special delivery for a clean environment and adequate safety measures.
Cooling systems must then be installed as they play an essential role in preventing the diesel engine from overheating. Finally, exhaust gas treatment systems are installed to reduce the harmful environmental impact of plant operations.
Depending on the manufacturer's recommendations, this equipment may require phased maintenance procedures and scheduled lubrication.
Routine maintenance and lubrication
Diesel power plant components, like any other mechanical system, require regular maintenance to ensure smooth operation. The professional who maintains the diesel engine must follow strict guidelines to avoid accidents or malfunctions. This includes keeping combustion chambers clean and regularly checking fuel filters, fans, nozzles and ignition systems. Equally important is regular lubrication of the engine room, which includes checking auxiliary systems and monitoring oil levels in various parts of the machine.
Think of it as taking your car for routine maintenance – every few thousand kilometers, oil change, belt and filter checks, among other things. Routine maintenance is performed to increase efficiency while reducing wear and tear that can lead to costly repairs.
Importance for longevity
Proper routine maintenance and lubrication of diesel power plants is essential to extending their useful life. Increases efficiency and minimizes downtime, which can be time-consuming and expensive.
For example, a small leak in the engine oil reservoir can damage the entire machine if not addressed immediately during routine checks. Likewise, exhaust systems are designed to operate within specific temperature ranges to minimize pollutant emissions (as mentioned in the previous section). However, due to failure of critical engine components, lack of care or proper routine maintenance can result in excessive heat generation, resulting in costly downtime.
Regular inspections help identify defects or areas that need cleaning before they become serious problems. For example, an infrared thermometer gun can be used to measure exhaust pipe temperatures to prevent overheating incidents that result in costly replacements.
Through regular maintenance schedules, companies can ensure their diesel plants are operating safely and within performance expectations, while also extending operational life. Maintenance providers typically offer plans based on consumption rates and manufacturer specifications.
So far, we have looked at the importance of regular maintenance and lubrication to maximize the life of diesel power plant components. In the next section we will look at emissions control and environmental impacts.
Emissions control and environmental impact
Diesel power plants are known for their high efficiency, reliability and versatility. However, the combustion process of diesel engines leads to the emission of pollutants such as nitrogen oxides (NOx), sulfur oxides (SOx), carbon dioxide (CO2) and particulate matter (PM). The environmental impact of these emissions is a significant concern, given their contribution to air pollution and climate change.
Although diesel engines emit less carbon dioxide per unit of energy produced than gasoline engines, they emit greater amounts of nitrogen oxides and particulates. The main sources of these emissions are the combustion of fuel in the engine cylinders and post-combustion reactions in the exhaust system.
Over the years, several initiatives have been implemented to mitigate these environmental impacts.
Mitigation measures and regulations
Governments around the world have enacted regulations that require diesel engines to meet strict emissions standards. These standards limit the emission levels of various pollutants released into the environment by diesel power plants. Compliance with these regulations can be achieved by retrofitting existing facilities with emissions control technologies or introducing cleaner fuels.
National regulations specify a series of measures to reduce emissions from diesel power plants. Possible solutions include installing selective catalytic reduction systems that convert nitrogen oxides into nitrogen gas and water vapor, or filtration systems that remove particulates from exhaust gases.
Think of it like driving a car: if too much smoke comes out of the exhaust, you run the risk of being stopped by a traffic cop. It is equally important for governments to ensure that operators regulate emissions from their facilities through laws and regulations.
To ensure accountability, these regulators conduct audits to ensure compliance with these standards and to penalize delinquent payers who do not adhere to these standards.
In addition to regulatory requirements, diesel power plant operations teams can take proactive steps to reduce the environmental impact of emissions from their facilities. For example, organizing regular maintenance schedules for equipment, air and oil filters, exhaust pipes and injectors. This helps to improve system performance efficiency and reduce the release of pollutants into the environment.
With this in mind, we want to explore some options for diesel power plants to regulate their emissions.
palliative measures | function |
Exhaust aftertreatment systems | Reduction of nitrogen oxide (NOx) emissions |
Extremely low sulfur diesel fuel consumption | Reduction of particulate matter (PM) and sulfur oxide (SOx) emissions |
Fuels emulsified in water | Reduce PM emissions by transferring heat from combustion to water droplets. |
Engine modification and replacement | Upgrade engines with less powerful engines or modify existing engines to reduce emissions |
Related article
Ensuring a Reliable Power Supply: A Guide to Generator Protection