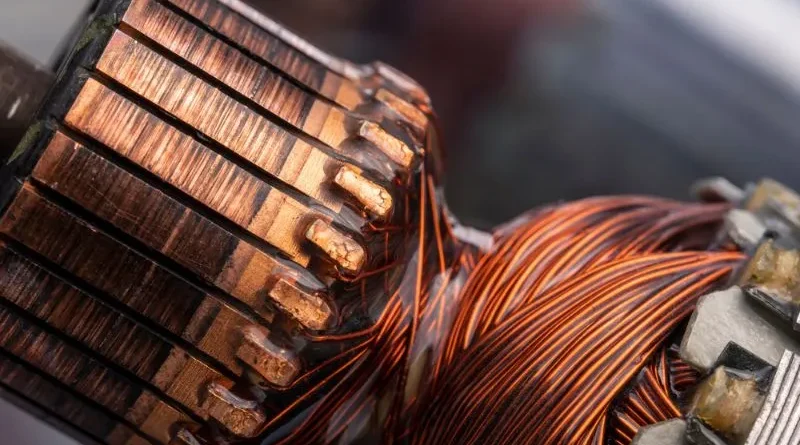
In this article we would like to demystify the concept of switching in DC machines and clarify its fundamental principles and mechanisms. We will examine the complex interaction between brushes, armature coils, and commutator, which is crucial for proper current flow and direction reversal. Additionally, we will cover the challenges and considerations associated with commutation, including brush wear, sparks, and the effects of various operating conditions.
Communications in DC machinery
The voltage generated in the coil (armature) of a DC generator, placed in a strongly rotating magnetic flux, usually fluctuates. DC machine commutation or more precisely DC generator commutation is the process in which the AC armature coil windings generated from a DC machine are converted into DC current by the commutator and stationary brushes.

Commutation in DC motors
Manage mobile contacts
During this conversion of current from the rotating coil of a DC machine to the stationary brushes, constantly moving contacts must be maintained between the commutator segment and the brush.
Switching Process in DC Machines
As soon as the armature begins to rotate, the coils rotate under a pole (N-pole) between a positive and a negative brush, and electric current flows through this coil in a different direction than that within the commutator segment. Now the coil is short-circuited using a brush for a small fraction of time (1/500 sec). This is called the switching period. During this short circuit, the armature coil rotates under the S pole and between a negative brush and the subsequent positive brush. Now the direction is reversed in the opposite direction to the commutator segments. This development of current reversal is called the switching process. We get power from the brush connection.
Switching quality
Switching is considered optimal when the method of switching or current reversal is completed at the end of the short circuit period or switching interval. Assume that the current reversal is completed during the entire tangency time. In this case, sparks occur at the brush contacts and the commutator surface is damaged due to heating and the machine is said to be poorly commutated.
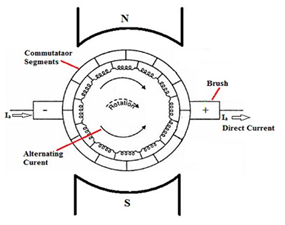
Commutation in ring-wound armature
Consider an armature wound DC machine with ring winding for the switching method. Let us additionally consider that the width of the switched rod is equal to the width of the brush and the current flowing through the conductor is I C .
Brush movement and current flow
The brush can move from right to left while the commutator moves from left to right.
The brushes connected to commutator blade B are shown in the initial position in Fig. Then the total current conducted from commutator bar B to the brush is 2I C.
When the armature begins to maneuver just before the brush makes contact with rod A, armature current flows through 2 paths and rods A and B (as shown in Fig. B). The total current (2I C ) remains absorbed by the brush.
Completion of switching

Switching characteristics in direct current machines
Here are some switching characteristics in DC machines;
Current reversal
During commutation, the direction of current within the armature windings of a DC machine is reversed. This ensures continuous rotation and efficient power generation or engine operation.
Segmented switch
The commutator, made of copper lamellas, is an essential component in switching. Allows current transfer between the rotating armature and the stationary brushes.
Brush material and design
The brushes, usually made of carbon or graphite, come into contact with the commutator segments. The choice of brush material and design is crucial for effective commutation, ensuring good electrical conductivity, low friction and durability.
Time and synchronization
For efficient commutation, proper timing and synchronization between the rotating commutator segments and the stationary brushes are essential. The brushes must immediately touch the commutator segments to switch the current flow.
Sparks and arcing
Improper commutation can cause sparks and brush arcing. Excessive sparks can result in brush and commutator damage, reduced efficiency, and electrical noise. Minimizing sparks is critical for optimal performance.
Mechanical and electronic switching
DC machines use mechanical or electronic switching. Mechanical switching uses brushes and a commutator, while electronic switching replaces brushes with semiconductor devices such as transistors or thyristors to improve reliability and control.
Switching Constraints
Due to switching, DC machines have certain limitations, for example in terms of speed and current-carrying capacity. Higher speeds and larger currents may require advanced switching techniques and design considerations to ensure reliable operation.
Influence of load and anchoring reaction
Changes in load and armature response can affect switching. Variations in load conditions can affect switching time and quality, requiring adjustments and compensation measures.
Brush maintenance and wear
Commutation in DC machines is subject to wear, which mainly affects the brushes and commutator. Regular maintenance and monitoring of brush condition is essential to maintain effective commutation and extend machine life.
Efficiency and energy loss
Effective switching contributes to the overall efficiency of DC machines. Improper switching can result in power loss, reduced efficiency and suboptimal performance, highlighting the importance of understanding and optimizing this process.
Understanding the switching characteristics of DC machines is crucial for engineers, technicians, and enthusiasts who work with these machines. By understanding the principles and factors that affect switching, you can optimize performance, mitigate issues such as sparks and wear, and ensure the reliability of DC machines in a variety of applications.