1. General provisions
1.1 To reduce energy consumption and extend the life of the nozzle and electrode, “low quality” cutting should be used as much as possible when cutting thin parts.
1.2 When the “thickness selection” switch is set to “high grade”, non-contact cutting should be used for cutting (except in special circumstances) and the water cutting torch should be prioritized.
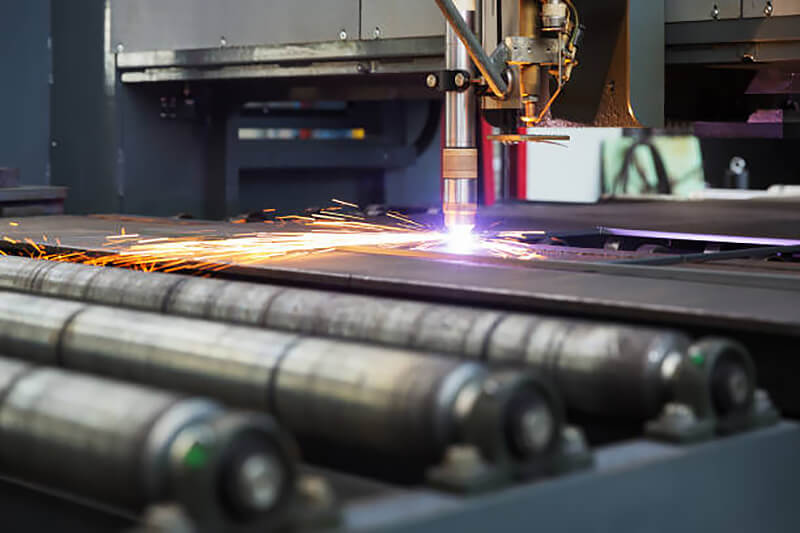
1.3 When it is necessary to change the position of the “thickness selection” switch, the main switch must be turned off first to avoid damage to machine parts.
1.4 When installing, disassembling or moving the host machine, the power supply must be turned off first before proceeding to avoid danger.
1.5 After turning off the main switch, the host machine accessories and components (such as cutting torches, cutting ground wire, electrodes, nozzles, distributors, pressure caps, protective caps, etc.) can be installed or removed. Avoid repeatedly and quickly turning on the cutting torch switch to avoid damage to the arc ignition system or related components.
1.6 When it is necessary to start arc cutting from the middle of the part and the stainless steel is ≤20 mm thick, direct drilling cutting can be used. The method is: place the cutting torch at the starting point of the cut and make the axis of the cutting torch nozzle at an angle of about 75° with the surface of the workpiece.
Then turn on the cutting torch switch to ignite the drilling arc; at the same time, slowly adjust the angle between the nozzle axis and the workpiece surface until it reaches 90° when cutting the workpiece.
After cutting the workpiece, normal cutting can be performed along the cutting direction. However, if it is necessary to use drill cutting beyond the thickness mentioned above, a small hole (diameter not limited) must be made at the starting point of cutting, and the arc must be lit to cut from the small hole.
Otherwise, it is easy to damage the cutting torch nozzle.
1.7 The continuous work rate of the host machine is 70% (“thickness selection” switch set to low degree, continuous work can be close to 100%). If the continuous working time is too long and the temperature of the host machine is too high, the temperature protection system will automatically shut down and must be cooled for about 20 minutes before continuing to work.
1.8 When the compressed air pressure is less than 0.22 MPa, the equipment must immediately enter the protective shutdown state. At this time, the gas supply system must be inspected and the fault must be eliminated before the pressure can be restored to 0.45 MPa before continuing work.
1.9 If there is a phase loss in the three-phase input power supply, the host machine cannot function properly. For some models, the red “phase loss indication” light is on. The fault must be cleared before normal cutting can be performed.
1.10 For water-cooled models, the water tank must be filled with tap water and the water pump power plug must be connected.
1.11 Turn the power switch to the “on” position. If the “low air pressure” indicator light is on, adjust it to 0.45 MPa as needed. Then the “low air pressure” indicator light will go out. The fan direction must follow the indication. The rotation direction of the water pump of the water-cooled machine must meet the requirements. Otherwise, the “low water pressure” indicator light will come on and the input power phase must be adjusted.
1.12 According to the thickness of the workpiece, rotate the “thickness selection” switch to the corresponding position and choose the appropriate cutting torch. There are many specifications for the cutting torch, from small to large, according to the usage range. It is prohibited to exceed the rated current range, otherwise damage will occur. Place the cutting torch at the starting point of the workpiece and press the cutting torch switch. If it does not light, press the cutting torch switch again. After the arc is successfully ignited, start cutting.
1.13 Every four to eight hours of work (the interval depends on the dryness of the compressed air), loosen the drain screw of the “air filter pressure reducer” as necessary to release accumulated water and prevent too much water from entering the machine or cutting the torch and causing malfunction.
1.14 When the water cooling system is circulating poorly, the host machine will enter the protective shutdown state. At this time, follow the methods described in the relevant sections of this text for inspection and troubleshooting. Only when the water pressure returns to normal and the water return port of the water tank flows smoothly from the cooled cutting torch can water continue to be used.
1.15 When working in cold environments, attention should be paid: when the ambient temperature is below freezing point, water cooling should not be used for cutting. Otherwise, the water-cooling system will not work properly and the water-cooled cutting torch may be damaged.
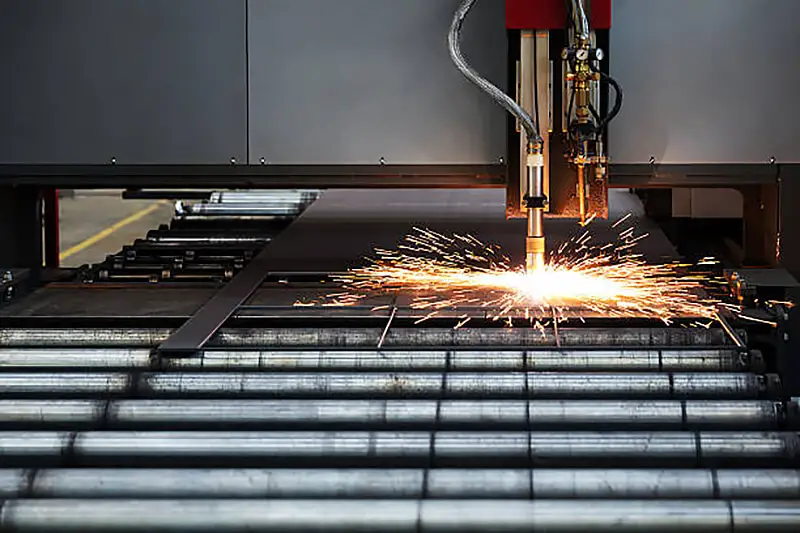
2. Preparation before operation
2.1 After connecting the equipment (pay special attention to the safety ground wire connection), inspect it carefully. If everything is normal, the next step can be taken.
2.2 Close the power button and supply power to the host machine.
Note: The input AC current is about 65A, which cannot be too small, otherwise the host machine will not work properly. At the same time, check whether the fan inside the host machine meets the requirements. If not, adjust the input power phase until it matches the direction of rotation.
2.3 Turn the “on/off switch” of the host machine to the “on” position. At this time, the “power indicator” light is on. However, the “phase loss indicator” light must not be on, otherwise there may be phase loss in the three-phase power supply, and it must be checked and resolved.
Note: If the host machine housing is not properly grounded, the phase loss indicator light may display an incorrect result.
2.4 Supply air to the host machine and set the “test air” and “cut off” switches to the “test air” position. At this time, compressed air should be sprayed through the cutting torch nozzle. Test for three minutes during which the red “low air pressure” light should not illuminate. Check that the pressure gauge on the “air filter pressure reducer” should not indicate less than 0.42MPa. Otherwise, it indicates that the gas source pressure is less than 0.45 MPa or the flow rate is less than 300L/min. It could also be due to the gas pipeline being too small and the gas pressure drop being too large.
If the above problems exist, they must be checked and resolved. Also, check if the “air filter pressure reducer” is misaligned. If so, it must be readjusted. The adjustment method consists of turning the lever clockwise to increase pressure and counterclockwise to decrease pressure. Adjust the indicator value on the pressure gauge to 0.42 MPa. If the gas supply is normal, the “low air pressure” indicator light will go out. At this point, turn the “cut” and “air test” switches to the “cut” position.
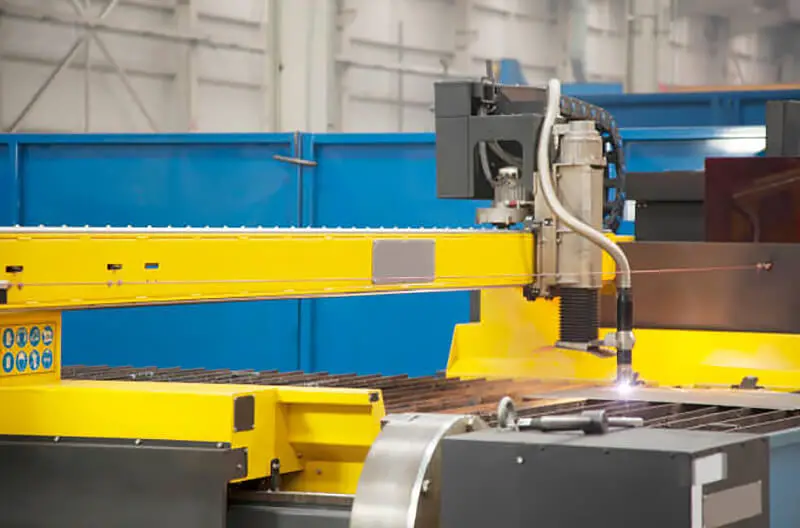
2.5 Safety checks before use
- The cutting machine must operate in a dry environment at normal temperature, avoiding strong sunlight, rain, dust, corrosive gases and areas with high air flow.
- The host machine should be placed at least 0.3 meters away from surrounding objects, with the cooling fan running normally to maintain good ventilation.
- Check whether the external power supply is accurate and correct.
- Confirm that the workpiece grounding cable is secured to the workpiece.
- Connect the air source and discharge accumulated water.
- Check that the power switch is in the off position.
- Close the main power switch, the cooling fan starts to rotate, and the correct direction of the fan should blow on the host machine.
- Turn the power switch on the back to “ON” position, the power indicator light will turn on.
- Open the air control valve, adjust the pressure and air flow to the 0.4 MPa (Megapascal) position, and allow the gas to circulate for a few minutes to remove any condensate from the cutting torch.
- Set the appropriate cutting current according to the workpiece material, thickness and process requirements.
- When pressing the cutting torch switch, the solenoid valve will be activated. You will hear the high frequency spark discharge sound inside the host machine, at the same time, the plasma arc will be expelled from the cutting torch nozzle.
3. Operating procedures
3.1 Contactless manual cutting
3.1.1 Roll the cutting torch wheel in contact with the workpiece and adjust the distance between the nozzle and the workpiece plane to 3-5 mm. (When the host machine is cutting, turn the “thickness selection” switch to high gear).
3.1.2 Turn on the cutting torch switch to ignite the plasma arc. After cutting the workpiece, move at a uniform speed in the cutting direction. The cutting speed should be fast but not too slow. Too slow will affect the quality of the cut and may even cause the arc to terminate.
3.1.3 After cutting, turn off the cutting torch switch and the plasma arc will extinguish. At this time, compressed air will be sprayed after a delay to cool the cutting torch. After a few seconds, the air spray will stop automatically. Move the cutting torch away to complete the entire cutting process.
3.2 Manual contact cutting
3.2.1 Turn the “thickness selection” switch to low gear for single thin sheet cutting.
3.2.2 Place the cutting torch nozzle at the starting point of the workpiece to be cut, turn on the cutting torch switch to ignite the plasma arc, and cut the workpiece. Then move evenly along the direction of the cutting seam.
3.2.3 After cutting, open and close the cutting torch switch. At this time, compressed air is still being sprayed. After a few seconds, the air spray will stop automatically. Move the cutting torch away to complete the entire cutting process.
3.3 Automatic cutting
3.3.1 Automatic cutting is mainly suitable for cutting thicker parts. Select the “thickness selection” switch position.
3.3.2 After removing the cutting torch wheel, firmly attach the cutting torch to the semi-automatic cutting machine. Connecting parts are included in the random accessories.
3.3.3 Connect the power supply of the semi-automatic cutting machine and install the guide rail or radius rod according to the shape of the workpiece (use a guide rail for straight line cutting and choose a radius rod for cut circles or arcs).
3.3.4 If the cutting torch switch plug is removed, replace it with a remote control switch plug (included in random accessories).
3.3.5 Adjust the appropriate walking speed according to the thickness of the workpiece. Adjust the “reverse” or “forward” switch of the semi-automatic cutting machine in the cutting direction.
3.3.6 Adjust the distance between the nozzle and the workpiece to 3-8 mm, and adjust the center position of the nozzle to the starting range of the workpiece cutting seam.
3.3.7 Turn on the remote control, cut the workpiece, turn on the switch of the semi-automatic cutting machine and start cutting. In the initial stage of cutting, pay attention to the cutting seam and adjust the appropriate cutting speed. Pay attention to whether both machines are working properly at all times.
3.3.8 After cutting, turn off the remote control and power button of the semi-automatic cutting machine. At this point, the entire cutting process is complete.
3.4 Manual circular cutting
According to the material and thickness of the workpiece, choose the cutting method with single machine or combined machine and select the corresponding cutting method. Screw the crossbar of the random accessories into the screw hole of the cutting torch bracket.
If one length is not enough, connect them one by one until you reach the required radius length and tighten them. Then adjust the top to the distance between the cutting torch nozzle according to the length of the workpiece radius (taking into account the width of the cutting seam).
After adjustment, tighten the upper fixing screws to prevent loosening and loosen the fixing bracket fixing screws.
At this point, you can start cutting circles into the workpiece.
3.5 Operational steps
1. The flow rate of the air compressor used should not be less than 0.3m3/min, with a working range of 0.4~0.8MPa.
2. When starting the arc cut, start at the edge of the workpiece. For workpieces that are to be cut from the middle, first drill a small hole, then start the arc from the edge of the hole.
Turn on the power switch, let the gas flow for a few minutes to remove condensation from the cutting torch, and then begin cutting.
The cutting torch nozzle should touch the workpiece (if it is a non-contact torch, the nozzle should be 3~5mm away from the workpiece). Press the cutting torch switch, wait for the plasma arc to automatically ignite and cutting officially begins.
During the cutting process, make sure that the cutting speed is sufficient to cut the workpiece. Cutting too fast can result in incomplete cuts and cause slag damage to the nozzle, while cutting too slowly can lead to overheating of the nozzle and reduce its life, widen the cut, increase slag and potentially cause arc interruption.
When stopping cutting, first release the cutting torch switch and then move the torch away from the workpiece.
3. Regularly check the motor and nozzle. If there is serious wear, replace them immediately to avoid affecting the thickness and width of the cut. If the alloy wire in the electrode is consumed by more than 2.0 mm or cannot start an arc, the electrode can be installed backwards or replaced.
The output voltage of the cutting machine is too high.
When assembling or replacing the electrode or nozzle, you must turn off the power and wear protective gloves. Screw the electrode and nozzle vertically upwards and tighten again after two or three minutes of use.
4. Safety Precautions
1. Operators must undergo relevant theoretical and practical training and examinations before operating this equipment.
2. Cutting work must be carried out in a well-ventilated environment. If ventilation is poor or work is carried out in a container, effective measures must be taken to improve ventilation.
3. After the cutting machine is turned on, do not disassemble the housing or touch the electrified parts (including the nozzle).
4. Before replacing cutting torch parts, the main power supply must be cut off.
5. Before work, operators must wear protective clothing, gloves, shoes, hats and light-colored face shields or UV protection glasses.
6. The cutting place should not contain flammable or explosive items.
7. During operation, make sure that the cutting torch hose and cable are not damaged, and prevent sparks from damaging the cutting machine main body, accessories or other items.
8. When the cutting machine is not in use, turn off the power first and then the gas supply.
9. Regular checks must be carried out to maintain the good condition of the machine and ensure good earthing.
V. Maintenance and Review
1. Maintenance
1. All maintenance and repairs must be carried out with the power completely disconnected. Make sure the power plug has been removed before opening the machine case.
2. Perform regular maintenance on the main machine once a month by blowing out dust with clean, dry compressed air.
3. Inspect and mark once a quarter.
4. The compressed air pressure must be around 0.4 MPa (megapascals). Too low or too high can damage the small components of the cutting machine.
5. Check the internal circuit connections of the cutting machine once a month to ensure that the connections are correct and the connectors are secure (especially insert connectors or components). If rust or looseness is found, use sandpaper finer than P120# to remove the rust layer or oxide film, reconnect and fix them.
6. Prevent liquid or steam from entering the main machine. If such situations occur, immediately dry the inside of the main machine. Then use a megohmmeter to measure the insulation condition of the cutting machine (mainly between the external connection points). If there are no abnormalities, you can continue to operate the machine.
7. If the main machine is not used for more than a month, clean it, package it and store it in a dry place.
2. Review
(1) Confirm that the air switch is closed
1. The screen shows nothing and the fan does not rotate.
2. Confirm power supply at the input cable connection.
3. Confirm that there is no phase loss in the power supply.
(2) Check for any bad contacts on various internal connections
1. The screen and fan rotation are normal.
2. The cutting torch control wire is broken or the microswitch is damaged; the cutting torch button does not work.
3. The control circuit is damaged (contact the supplier or manufacturer).
(3) Check whether the high voltage package has been punctured
1. The IGBT is damaged; the abnormal indicator light is on, but the screen is normal.
2. The quick recovery rectifier tube is damaged; fan rotation is normal.
3. The control board is defective.
4. The feedback circuit is defective (abnormality indicator light is on).
(4) There are problems in the arc initiation part
1. The discharge nozzle is too far away or there is sticking; fan rotation and screen are normal.
2. The high voltage package is damaged; the solenoid valve works, but there is no arc maintenance output, indicating an anomaly.
3. The arc initiation relay is damaged; the indicator light is not on.
4. The control circuit is defective.
5. The feedback circuit is faulty and the indicator light is damaged.
(5) Air switch quality problems
1. The air switch cannot be closed.
2. The silicon bridge is damaged and needs to be replaced.
3. Check for a short circuit inside the machine.