Air, the vital “life gas” we breathe daily, is made up of 78% nitrogen, 21% oxygen, 0.94% rare gases (such as helium, neon, argon, krypton and xenon), 0.03 % carbon dioxide and 0.03% carbon dioxide. % of other substances (such as water vapor and impurities).
Now, let's delve into the benefits of air cutting in the laser cutting process.
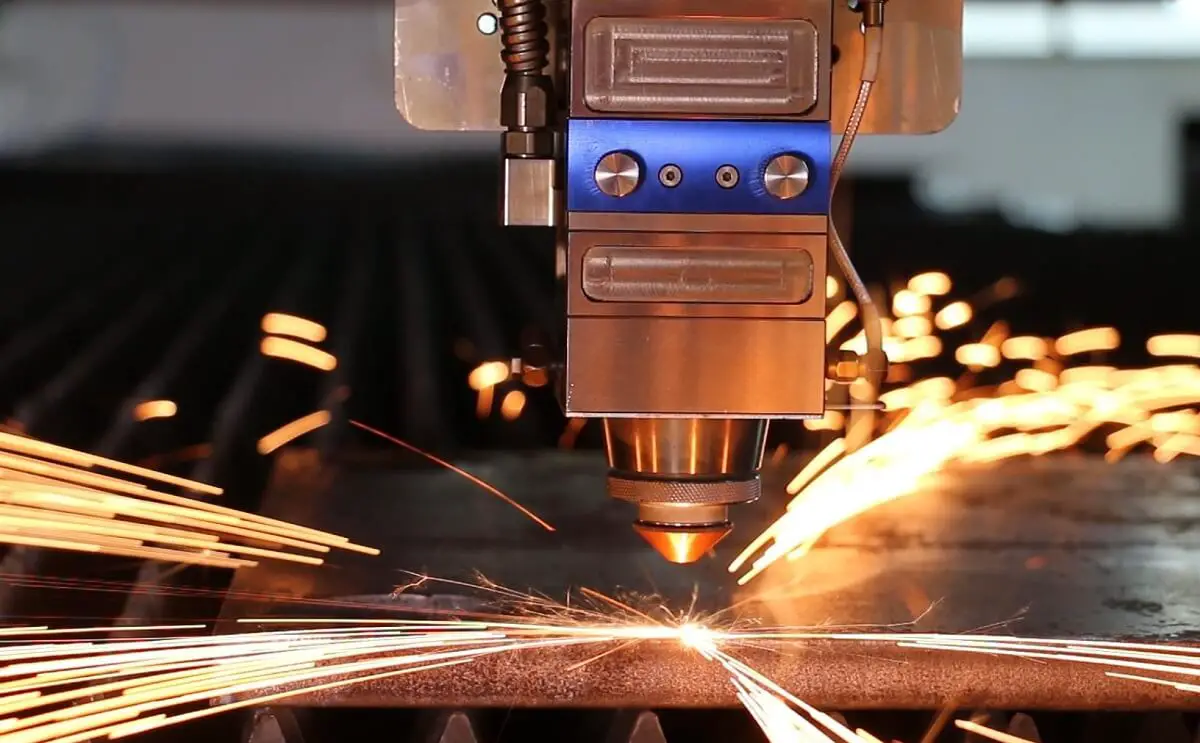
Air cut off principle
The principle of cutting air is actually similar to that of nitrogen. It uses laser energy to melt the metal and high pressure to remove the molten material. During the process, some metallic substances may oxidize or burn, leaving metallic oxides on the cutting surface, such as solid gray alumina (Al 2 Ó 3 ), solid black iron oxide (Fe 3 Ó 4 ) and copper oxide (CuO) .
Air, which is naturally present in the atmosphere, can be compressed in an air storage tank, filtered, cooled and dried to remove water and oil, making it usable for cutting. The 21% oxygen content in the air can partially compensate for the lack of oxygen and nitrogen.
In theory, air can cut through any metallic material that can be melted by laser energy.
Air cutting efficiency and effect experiment
Evaluation of cutting performance on stainless steel, carbon steel and aluminum alloy plates using a 6kW laser cutting machine with air and nitrogen/oxygen as cutting gases.
Try 1: Comparison of Nitrogen and Air Cutting in Stainless Steel
⊙ Comparison of the effect of nitrogen and air cutting section
⊙ Comparison of cutting speed with nitrogen and air
Effect analysis:
The figure above shows the results of cutting stainless steel from 10mm to 4mm, in that order.
Compared to nitrogen cutting, the air cutting section appears darker, but there is no slag present. After polishing, the cut section can also achieve a brighter appearance.
In terms of speed, air cutting of stainless steel is slightly faster than nitrogen, but the difference is not significant.
Try 2: Comparison of Oxygen and Air Cutting in Carbon Steel
⊙ Comparison of the effects of oxygen and air cutting section
⊙ Comparison of cutting speed with air and oxygen
Effect analysis:
The figure above shows the results of cutting carbon steel from 10mm to 3mm, in that order.
Compared to oxygen cutting, 8mm carbon steel has a slight slag residue, and 10mm carbon steel has a more severe slag residue.
Therefore, air cutting is not recommended for cutting carbon steel sheets thicker than 10mm.
Experiment 3: Comparison of Aluminum Alloy for Nitrogen and Air Cutting
⊙ Comparison of the effect of nitrogen and air cutting section
⊙ Comparison of cutting speed with nitrogen and air
Effect analysis:
The figure above shows the results of cutting aluminum plates from 10 mm to 3 mm, in that order.
Compared to nitrogen cutting, air cutting results in a thinner section and less slag residue.
In terms of speed, air cutting of aluminum plates is slightly faster than nitrogen cutting, but the difference is not significant.
Summary
Experiments were conducted to compare the performance and efficiency of cutting with air and nitrogen/oxygen on plates of various materials and thicknesses.
Based on a comprehensive assessment, for relatively flexible requirements, air cutting is a cost-effective option. Using air as a cutting auxiliary gas can also significantly reduce production costs.
But it should be noted that:
When using compressed air for cutting, it is crucial to ensure the air is treated by a cold dryer to reach a pressure dew point of 3-8°C and undergo multi-stage degreasing. The air must have a liquid oil content of 0.003 ppm and a vapor oil content of 0.003 ppm, requiring the use of a filter specifically designed to remove gaseous oil.
Regular maintenance of the air compressor, cold dryer and filter is necessary to maintain the dryness of low oil compressed air. Contaminants such as water and oil in the air can quickly pollute the pipeline and cause haze on the protective lenses, affecting the quality of the cut. Neglecting to replace the protective mirror in a timely manner may also cause damage to the internal mirror group, as the high-power beam may cause the internal temperature of the cutting head to increase.
To find the most economical cutting solution that best meets current cutting needs, cutting efficiency, cost and effect must be taken into consideration in the production process, leading to a higher quality production result.