1. Remove the bench front plate, front support arm and cover
As shown below:
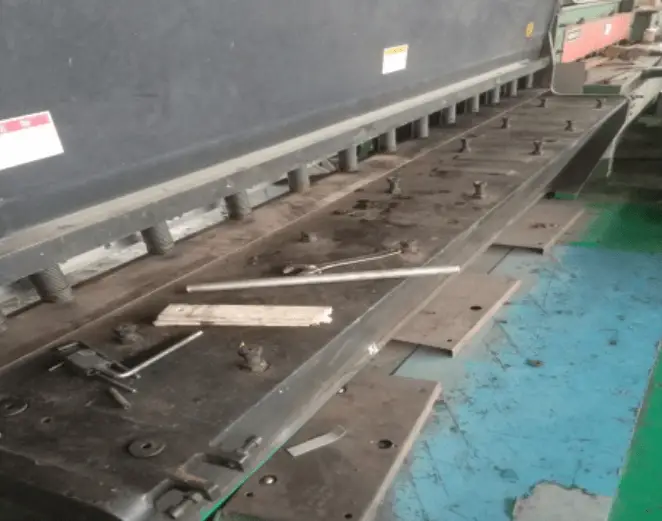
2. Blade removal
(1) When disassembling, first remove the blade, leaving a screw in the center of the blade to loosen it. Do not remove this screw to prevent the blade from falling and causing injury to people.
After removing all other screws, two people should work together to remove the lower blade. The blade has two screws that can be used by two people to lift it.
② Before proceeding, set the operation panel to “Manual shift mode”, which can only be performed when the machine is in stop mode. This is shown in the attached figure.
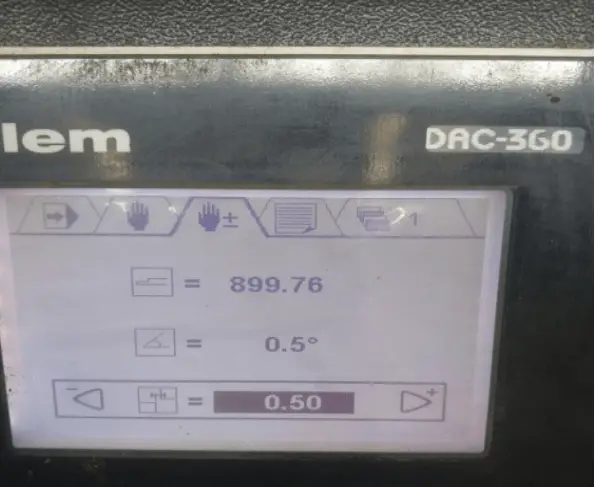
- The backgauge distance must be set to more than 900.
- To adjust the upper blade shear angle, change it to 0.5°. Note that a greater angle will result in a greater tilt of the upper blade.
- To prevent the upper and lower blades from colliding, change the upper and lower blade gap to 0.5 or more. This will ensure that charging both blades does not cause them to collide with each other.
3. Removing the upper blade
When removing the drive, first loosen the center screw, but do not remove it. Then loosen the pressure reducing valve inside the unit by turning it counterclockwise as shown below.
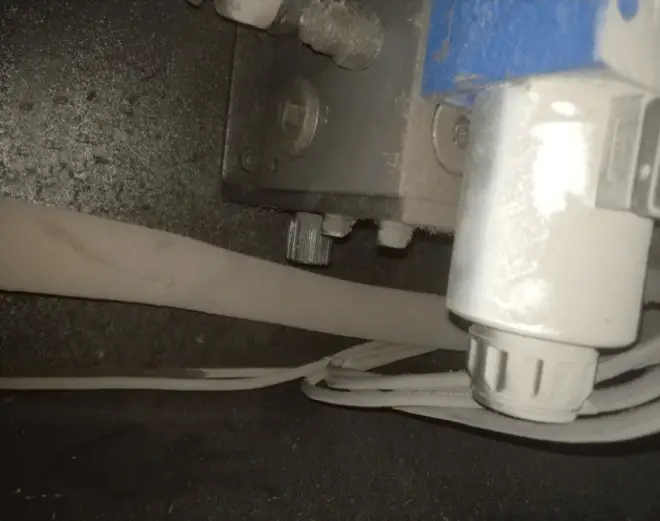
The greater the counterclockwise rotation of the pressure reducing valve, the faster the upper blade will fall.
Once the top blade has been lowered enough to reveal the two hidden screws, close the pressure reducing valve by turning it fully clockwise. Then you can remove the two hidden screws on the top blade.
After removing these screws, activate the unit's oil pump and the upper blade will return to its initial position, facilitating its removal. To remove the top blade, it can be tilted at a greater angle.
When disassembling the unit, it is important to have several people working together to avoid injury. Use a wooden board in the center to provide additional support and stability.
4. Clean oil, dust and dirt from the upper and lower blades
Before installation, inspect the tool for damage and mark the available surface. Prepare the surface for installation by cleaning it and making any necessary repairs or adjustments.
5. Blade Installation
The installation process is the reverse of the removal process.
Install the blade first, using two screws to lightly secure it and make it easier for two people to carry. Then place the screw into the device and install the lower blade by screwing it into place. The hidden screws on both sides of the upper blade do not need to be installed first.
Finally, on the operation panel, adjust the settings for “Manual Shift Mode” with the following values:
Backgauge distance: above 900, Shear angle: 1.7° (greater than 1.5°) and Clearance: 0.5 or more. These configurations are designed to prevent the upper and lower blades from colliding with each other during installation.
6. Fixing the upper and lower blade
When installing the blade, one person must always be in control of the pressure reducing valve.
Lower the upper blade slowly and close the pressure reducing valve when the upper and lower blades overlap. Use a feeler gauge to check the gap between the blades, it should be 0.5 mm. If the gap is too small (e.g. 0.1 or 0.2), adjust it again in “Manual Shift Mode”.
If the clearance is appropriate and the blades are not touching, continue to release the pressure reducing valve. Close the pressure reducing valve again (clockwise) when the upper blade touches the lower blade on the right side. Use the feeler gauge to check the gap again and ensure the blades are not touching.
Activate the oil pump to return the upper blade ram to the home position. Use a wooden plank to hold the blade in place and slowly release the pressure reducing valve.
Tighten the nearby screws one by one, from left to right, using the same method. After all screws have been tightened, release the top blade and tighten the last two hidden screws (which are shorter).
7. Gap correction
Use a plug gauge to check the gap in the top and bottom blades and make sure it matches the readings on the machine. If there are discrepancies, follow these steps to make adjustments:
(1) Two people are required to adjust the gap using a wrench. One person should hold the hexagonal bar in place while the other person loosens the nuts on both ends of the bar, as shown in the figure below.
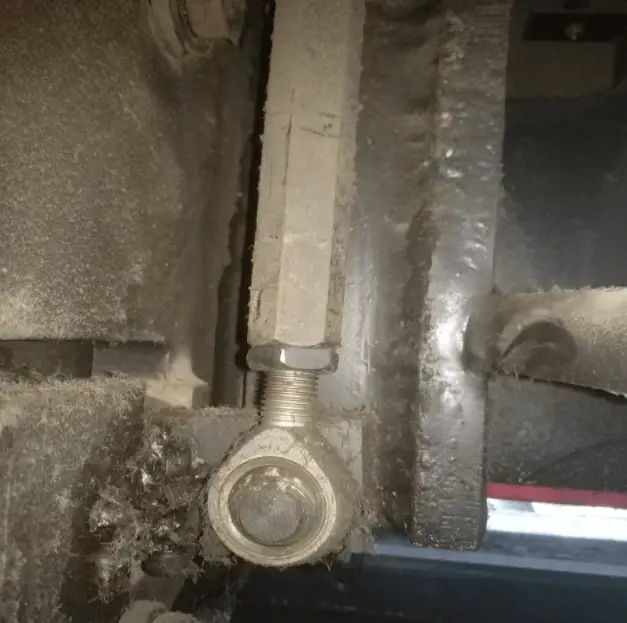
Send the nuts on each end up, then use a wrench to turn the hex bar (adjustment lever). Turn the screw clockwise to reduce the gap and counterclockwise to increase it (depending on location).
(2) Use this method to adjust the gap on both sides, ensuring that the gap matches the machine's display. The top and bottom sides of the tool must be matched before tightening the nuts on both ends of the bolt.
8. Once the gap has been adjusted, it is necessary to check the correct distance from the back gauge
If an error requires adjustment, adjust as follows.
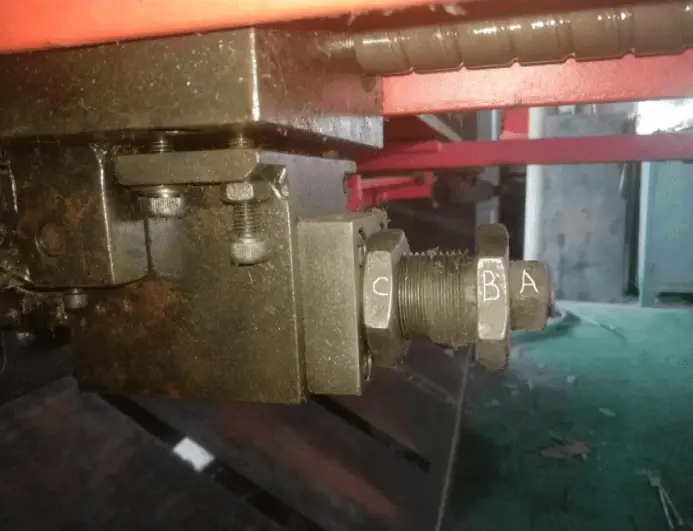
① To adjust the stop, move it to the rear position where the machine displays 900 mm. Loosen nut “A” and then nut “C”. Use a wrench to turn adjusting screw “B”. Each turn of the screw is approximately 2.3 mm and turning it clockwise reduces the size, while turning it counterclockwise increases it.
② Once the backstop has been adjusted, first tighten nut “A” and then nut “C”. Check the accuracy of the fit using the shear plate until the test piece passes.