La aleación de aluminio tiene muy baja densidad y es ligera; sin embargo, tiene una alta resistencia, comparable o incluso superior a la del acero de alta calidad. Es maleable, fácil de procesar en diferentes perfiles y tiene una excelente conductividad eléctrica y térmica y resistencia a la corrosión.
La aleación de aluminio se usa ampliamente en industrias como la automotriz, aeroespacial, de fabricación mecánica y de construcción naval, lo que la convierte en uno de los materiales de aleación más utilizados. Las aleaciones duras de aluminio pertenecen al sistema Al-Cu-Mg y generalmente contienen una pequeña cantidad de Mn.
Pueden tratarse térmicamente como refuerzo, caracterizándose por su alta dureza pero baja plasticidad. El aluminio superduro pertenece al sistema Al-Cu-Mg-Zn, también puede tratarse térmicamente para fortalecerlo y tiene la mayor resistencia entre las aleaciones de aluminio a temperatura ambiente.

Sin embargo, tiene baja resistencia a la corrosión y se ablanda rápidamente a altas temperaturas. Las aleaciones forjadas de aluminio son principalmente aleaciones de Al-Zn-Mg-Si. Aunque contienen muchos tipos de elementos, las cantidades son pequeñas, por lo que tienen una termoplasticidad excelente y son aptos para la forja.
Con el rápido desarrollo de los niveles industriales, la demanda de estructuras soldadas de aleaciones de aluminio está aumentando, lo que promueve una investigación en profundidad sobre el rendimiento de la soldadura de las aleaciones de aluminio.
I. Introducción y ventajas de la soldadura MIG de aleaciones de aluminio”
Los principales procesos de soldadura para aleaciones de aluminio incluyen la soldadura con gas inerte de tungsteno (TIG), la soldadura con gas inerte de metal (MIG), la soldadura por fricción y agitación y la soldadura por resistencia.
La soldadura MIG es un proceso de soldadura por arco que utiliza protección mediante gas argón o una mezcla de gases inertes y activos. La diferencia fundamental entre la soldadura MIG y TIG es la sustitución del electrodo de tungsteno del soplete por un alambre metálico.
En la soldadura MIG, el alambre se funde mediante el arco y se introduce en la zona de soldadura, impulsado por rodillos motorizados que alimentan el alambre desde la bobina hasta el soplete según las necesidades de soldadura. Los gases protectores utilizados en ambos procesos son diferentes; Se añade un 1% de oxígeno al gas argón para mejorar la estabilidad del arco.
También existen diferencias en la transferencia por aspersión, pulverización pulsada, transferencia globular y transferencia por cortocircuito.
La energía CC, no la CA, es la fuente de calor para la soldadura MIG. Esto se debe a los efectos sobre la estabilidad y consistencia del arco durante el proceso de soldadura si no se utiliza energía CC. Para situaciones en las que no se utiliza soldadura de CA, la polaridad de CC positiva y la polaridad de CC inversa son dos opciones de selección diferentes, y la soldadura MIG generalmente usa polaridad de CC inversa.
Esto se debe a que el arco es estable cuando se elige la polaridad inversa de CC y produce un mejor efecto que previene eficazmente la formación de una película de óxido metálico durante la soldadura, lo cual es muy beneficioso para el magnesio, el aluminio y sus aleaciones.
Por último, cuando se utiliza CC con polaridad inversa, la velocidad de fusión del alambre es más rápida y la eficiencia de producción es mayor. La soldadura MIG es confiable y produce resultados consistentemente de alta calidad, lo que la hace más adecuada para soldar placas de aluminio y aleaciones de espesor medio.
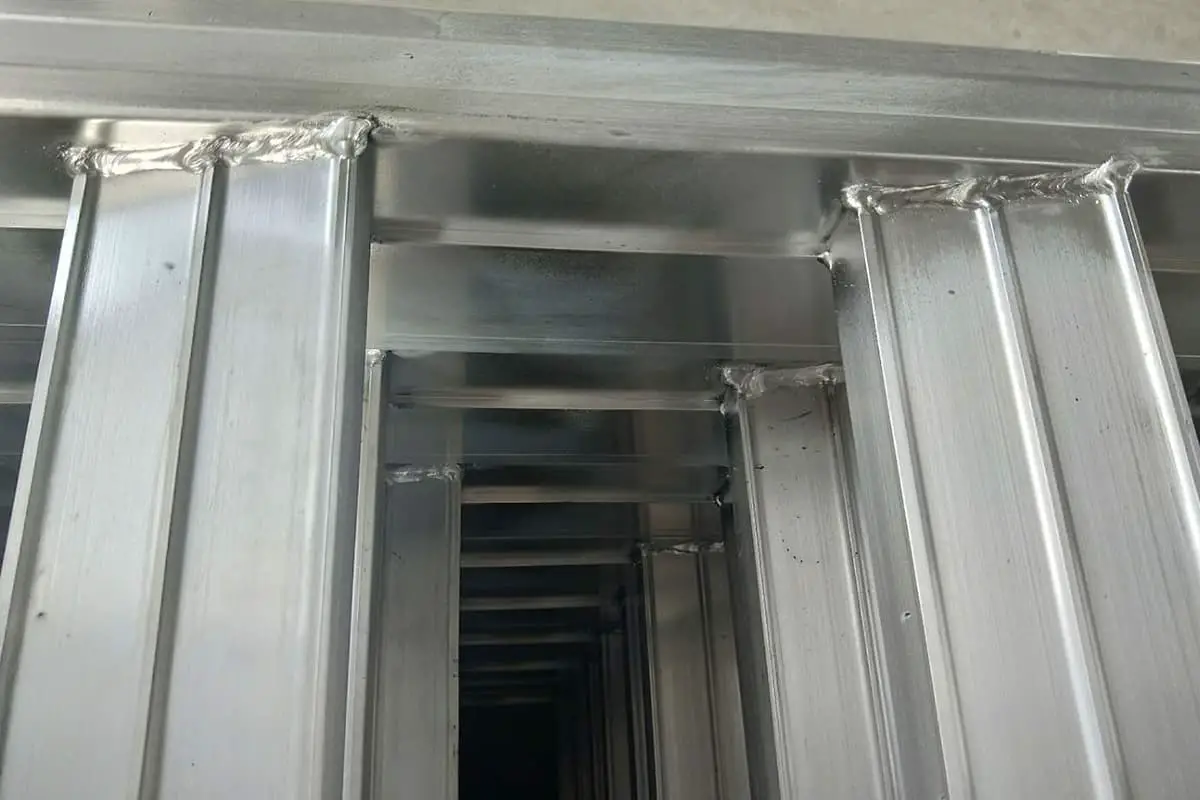
II. Puntos clave a considerar en la soldadura MIG
Pueden ocurrir problemas como desalineación y deformación durante el proceso de soldadura MIG. Por lo tanto, las siguientes cuestiones deben abordarse cuidadosamente durante las operaciones.
1. Desalineación entre componentes de soldadura
En la soldadura MIG, la desalineación entre componentes puede ocurrir fácilmente debido a un diseño defectuoso de los accesorios de la herramienta o a operaciones no estándar. Esto requiere una fijación cuidadosa y una atención meticulosa durante el montaje.
2. Problemas de deformación de la hoja
Incluso con las herramientas ideales, las láminas de aleación de aluminio aún pueden deformarse debido al calor excesivo producido en el proceso de soldadura MIG, lo que provoca que toda la lámina se deforme. Las pequeñas deformaciones se pueden corregir martillando uniformemente con un mazo de madera.
Sin embargo, la deformación severa requiere calentamiento con llama, ajustando la temperatura y el tiempo de la llama para lograr la forma deseada.
3 . Óxido negro en soldadura MIG de aleación de aluminio.
El residuo negro que se produce durante la soldadura MIG de aluminio se compone principalmente de óxidos como el óxido de magnesio y el óxido de manganeso. La presencia excesiva de óxido negro durante la soldadura de una sola capa suele indicar un blindaje insuficiente.
Durante la soldadura multicapa, la aparición de óxido negro en la pasada de raíz indica una buena penetración, ya que el metal fundido se oxida en el aire debajo de la soldadura y sube a la superficie.
Si aparece óxido negro en el paso del recubrimiento, esto sugiere un blindaje inadecuado. Con suficiente blindaje, deberían aparecer dos bandas blancas brillantes a cada lado de la soldadura.
III. Peligros del polvo de soldadura MIG de aleación de aluminio
La aleación de aluminio tiene un punto de fusión bajo y genera cantidades sustanciales de polvo de óxido de aluminio bajo la formación de arcos a alta temperatura, lo que representa un riesgo significativo para los sistemas respiratorios de los trabajadores.
Además, los elementos de aleación de la aleación de aluminio pueden crear partículas de óxido nocivas durante el funcionamiento. A pesar de su baja concentración, estos óxidos de elementos de aleación aún pueden dañar la salud humana.
El polvo de soldadura MIG de aleación de aluminio puede provocar enfermedades como neumoconiosis, demencia, osteomalacia y anemia, por lo que es necesaria una protección eficaz contra ella.
4. Medidas de protección contra el polvo de la soldadura MIG de aleación de aluminio.
El objetivo fundamental de la protección contra el polvo de soldadura MIG de aleación de aluminio es evitar la inhalación de polvo nocivo. La experiencia demuestra que si las operaciones de soldadura de aleaciones de aluminio son poco frecuentes en el entorno de producción, un respirador con filtro a menudo puede ser suficiente para evitar que los trabajadores inhalen polvo nocivo.
Sin embargo, si las operaciones de soldadura de aleaciones de aluminio son frecuentes, depender únicamente de la filtración es insuficiente. Se requiere el uso integral de respiradores filtrantes y sistemas de ventilación efectivos.
Además, para la soldadura MIG de aleaciones de aluminio, el uso de una fuente de energía pulsada no sólo puede mejorar la calidad de la soldadura sino también disminuir la generación de polvo de óxido de aluminio. En entornos laborales donde se realiza soldadura MIG de aleaciones de aluminio, la piel y la ropa de los trabajadores están sujetas a la acumulación de polvo.
Una vez que el polvo de soldadura se deposita en estas áreas, puede dañar la salud de los trabajadores y es necesario limpiarse las manos y la ropa con regularidad para garantizar la seguridad.
En general, aunque el polvo procedente de la soldadura MIG de aleaciones de aluminio supone un riesgo importante para la salud humana, este riesgo puede controlarse eficazmente reforzando la gestión de la producción y concienciando a los trabajadores sobre la protección en el propio proceso de fabricación.