La resistencia de los metales es una de las propiedades mecánicas más importantes requeridas para clasificar las aplicaciones y usos de los metales. Algunos metales pueden ser adecuados para su uso en la industria de la construcción, pero no en la industria aeroespacial. Este es un factor crucial utilizado por científicos, fabricantes e ingenieros para garantizar la funcionalidad y practicidad del metal en todos sus proyectos.
En la industria de materiales, la resistencia se define como la capacidad de un material para soportar una carga aplicada sin sufrir fallas o deformaciones plásticas.
Tipos de fortalezas
Los materiales tienen diferentes resistencias según la carga. Estas resistencias se utilizan como parámetros a considerar al seleccionar un material para aplicaciones específicas. A continuación se detallan los diferentes tipos de resistencia de los metales:
Límite de estiramiento: esta es la resistencia máxima que un metal puede soportar antes de mostrar una deformación plástica permanente en una prueba de tracción. Los ingenieros utilizan este valor para determinar la carga máxima que puede soportar un componente. Esto se utiliza en muchos reglamentos técnicos como criterio para definir el fallo.
Resistencia a la tracción o simplemente llamada resistencia a la tracción. Esta se define como la tensión máxima que el material puede soportar en un ensayo de tracción. En términos más simples, esta es la carga máxima que un metal puede soportar antes de romperse o desgarrarse.
Resistencia a la compresión: esta es la resistencia máxima a la que un material puede resistir la falla durante una prueba de compresión. En este tipo de resistencia, la carga se aplica a la parte superior e inferior de la muestra.
Resistencia al impacto: es la capacidad de un metal para resistir tensiones repentinas y severas sin fallar. Es la energía máxima que un metal puede absorber antes de agrietarse o romperse.
¿Por qué necesitamos aprender sobre la resistencia de los metales?
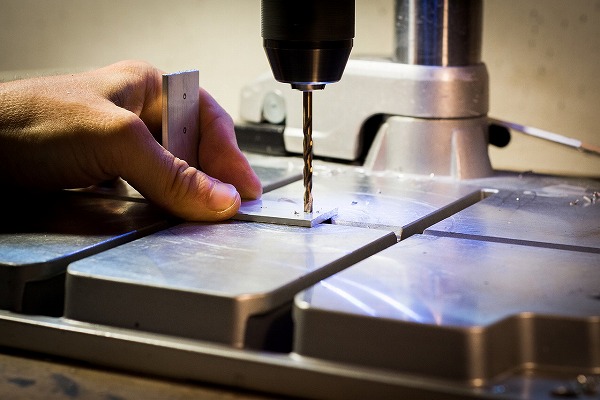
Ahora que ha aprendido acerca de los tipos básicos de fortaleza mental, probablemente comprenda un poco la importancia de aprender sobre la fortaleza mental. Para explicar esto con más detalle, a continuación se ofrece una discusión exhaustiva sobre por qué la resistencia del metal es importante en varias industrias:
Diseño mecánico/estructural.
Cuando se trata de elementos mecánicos y estructurales, los ingenieros necesitan conocer la resistencia de las piezas que están diseñando. Los utilizan para identificar dónde un material podría romperse o fallar. Esto les permite establecer límites y definir las restricciones necesarias para las piezas específicas que diseñan.
Selección de materiales
La resistencia de los metales es un criterio muy importante en la selección de materiales que puedan soportar las exigencias de diversas aplicaciones industriales. Diferentes metales tienen diferentes valores de resistencia. Hay ciertos metales que son adecuados para aplicaciones de trabajo pesado y también algunos que son más adecuados para aplicaciones de trabajo liviano. Por ejemplo, se prefiere un metal con alta resistencia a la tracción para fabricar piezas necesarias para levantar o tirar.
Seguridad
Todo se reduce a la seguridad. La resistencia de los metales establece varios límites para evitar fallos en cualquier aplicación. Conociendo la clase de resistencia del metal, es posible diseñar piezas de forma segura e infalible que puedan soportar las cargas previstas sin causar daños a los usuarios.
Los metales más fuertes utilizados en metalurgia.
En la industria existen metales más resistentes que pueden preferirse según la aplicación y los requisitos de diseño. A continuación se muestran los metales más fuertes que se utilizan comúnmente en diversas industrias:
1. Titanio
Este metal natural tiene una alta resistencia a la tracción porque su estructura es menos densa que la de los metales comunes. El titanio es popular debido a su baja relación resistencia-peso y su alta resistencia a la corrosión, lo que lo hace perfecto para aplicaciones aeroespaciales, automotrices y médicas. Además de su estado puro, el titanio a menudo se alea con otros metales para aumentar aún más su resistencia. Un ejemplo es el aluminuro de titanio, en el que los elementos de aleación son aluminio y vanadio.
2. Cromo
El cromo llegó a la lista de los metales más fuertes porque se considera el metal más duro del planeta. Aunque el cromo no se suele utilizar solo, tiene efectos sorprendentes cuando se alea con otros metales. Una aplicación popular es el cromo como ingrediente principal en la producción de acero inoxidable, uno de los metales más buscados en todas las industrias.
3. tungsteno
Se considera el metal natural más fuerte y duro ya que tiene una resistencia a la tracción de 250.000 psi o 1.725 MPa. Para compensar su fragilidad, este metal suele estar aleado con otros elementos. La aleación más popular es el carburo de tungsteno. La resistencia del tungsteno es muy útil para diversas aplicaciones en las industrias militar, aeroespacial, minera y otras industrias metalúrgicas.
4. Acero
El acero es generalmente uno de los metales más resistentes y el material de construcción más importante. Este metal se fabrica a partir de aleaciones de hierro, carbono y algunos otros elementos, según el tipo de acero. La resistencia a la rotura del acero depende de sus otros componentes de aleación. A continuación se muestran algunos tipos comunes de acero:
- Acero inoxidable: una aleación de acero, cromo y manganeso. Este metal es conocido por sus excelentes propiedades de resistencia a la corrosión. Tiene un límite elástico de 1560 MPa y una resistencia a la tracción de hasta 1600 MPa.
- Aleaciones de acero, hierro y níquel: generalmente, la aleación de acero al carbono con níquel aumenta su resistencia a la tracción hasta en 1450 MPa. Diferentes fabricantes han producido sus propias variantes de esta aleación.
- Acero para herramientas: este tipo de aleación de acero se fabrica mezclando las proporciones correctas de cobalto y tungsteno. Su resistencia y dureza lo convierten en un material perfecto para fabricar herramientas de corte CNC e incluso ejes.
5. Inconel
Otra liga que entró en la lista es el Inconel. Esta es una aleación de níquel austenítico y cromo. Estas superaleaciones son extremadamente fuertes y resistentes a la corrosión, lo que las hace perfectas para aplicaciones en entornos y condiciones extremas. Se utilizan comúnmente para fabricar turbinas, rotores de turbocompresores, intercambiadores de calor, recipientes a presión y más.
Procesos para mejorar la resistencia del metal.
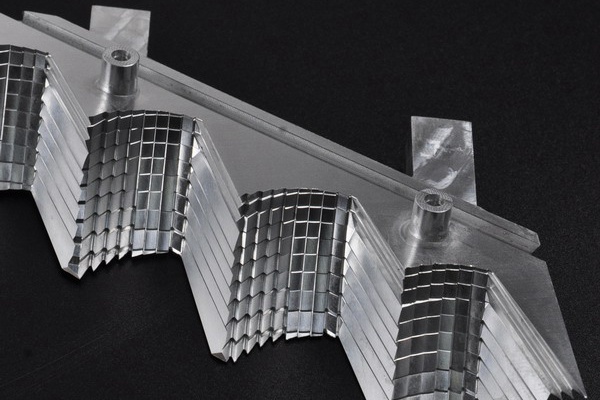
1. Solidificación de soluciones sólidas y formación de aleaciones.
Este es el método utilizado por las aleaciones metálicas mencionadas anteriormente para mejorar la resistencia del metal puro. El endurecimiento en solución sólida implica la formación de una "solución sólida" mediante la adición de átomos de un elemento de aleación a la red cristalina del metal base.
2. Tratamiento térmico
Este proceso específico se puede llevar a cabo en cualquier punto de la producción de una pieza metálica para mejorar sus propiedades. Durante el proceso de calentamiento, la microestructura del metal cambia, haciendo que el metal o la aleación sea más fuerte, resistente y duradero. A continuación se detallan los métodos comunes de tratamiento térmico:
- Brillo: metales como cobre, plata, aluminio, acero y latón se calientan para reducir el riesgo de rotura durante el procesamiento. Durante el recocido ocurren tres fenómenos: recuperación, recristalización y crecimiento del grano.
- Templado El templado implica calentar el metal a una temperatura justo por debajo de su temperatura de endurecimiento y mantenerlo a esa temperatura durante un período de tiempo específico. Este proceso se realiza para reducir la fragilidad del metal, manteniendo su dureza y resistencia.
- Normalización: este proceso se realiza para hacer que el acero sea más fuerte y más dúctil.
- endurecimiento En este proceso, el metal se calienta a una temperatura lo suficientemente alta como para disolver los precipitados ricos en disolventes. Este proceso luego aumenta la dureza y resistencia del metal. La desventaja, sin embargo, es que el metal ya ha perdido su ductilidad, lo que lo vuelve quebradizo.
3. Endurecimiento por trabajo
En este método, el metal se refuerza mediante deformación plástica para aumentar su dureza, límite elástico y resistencia a la tracción. Los desplazamientos que se producen durante este proceso provocan enredos en los desplazamientos de grano. Este entrelazado evita una mayor deformación de los granos afectados y, por tanto, aumenta la fuerza mental. La solidificación ocurre a menudo en procesos de trabajo y conformado en frío, como trituración, corte y doblado.
La diferencia entre fuerza y dureza.
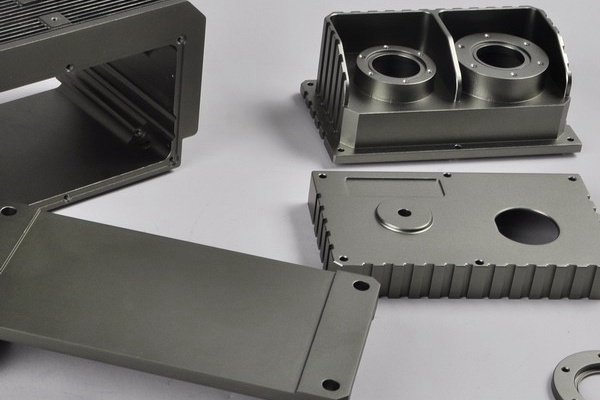
Aunque la resistencia y la dureza están estrechamente relacionadas, es importante señalar que estas propiedades se miden de manera diferente. La resistencia se define como la capacidad de un material para resistir la deformación causada por una carga externa, mientras que la dureza es la capacidad de un material para resistir la penetración o el rayado.
Como ya se mencionó, existen métodos de prueba completamente diferentes para estos dos. La resistencia de los metales se determina mediante una prueba de tracción o compresión en una máquina de prueba universal, mientras que las pruebas de dureza se pueden realizar utilizando varios métodos, incluida la prueba de dureza Rockwell, la prueba de dureza Brinell, la prueba de dureza Vickers y el estereoscopio Shore.
Estos dos son importantes en la industria del diseño y la ingeniería, ya que representan uno de los parámetros más importantes a considerar. La resistencia establece los límites de carga máxima permitida sobre las piezas a fabricar. Esto es crucial para evitar errores en estructuras y máquinas. Por otra parte, la dureza es un muy buen indicador de la resistencia de un metal al desgaste mecánico. Se prefieren los metales más duros para fabricar piezas que deben tener una excelente resistencia al desgaste.
Tabla de resistencia del metal
Si su proyecto requiere piezas metálicas, existen algunos parámetros importantes que debe conocer sobre los metales comunes. Por ejemplo, el límite elástico del acero, la resistencia a la tracción del acero, la densidad, la dureza, etc. Hay una mesa de metal. Puede comparar y hacer referencia a las propiedades de diferentes metales.
tipos de metales | Resistencia a la tracción (PSI) | Límite elástico (PSI) | Dureza Rockwell (escala B) | Densidad (Kg/m³) |
acero inoxidable 304 | 90.000 | 40.000 | 88 | 8.000 |
Aluminio 6061-T6 | 45.000 | 40.000 | 60 | 2720 |
Aluminio 5052-H32 | 33.000 | 28.000 | 2680 | |
Aluminio 3003 | 22.000 | 21.000 | 20 a 25 | 2730 |
acero A36 | 58-80.000 | 36.000 | 7800 | |
Acero Grado 50 | 65.000 | 50.000 | 7800 | |
Latón amarillo | 40.000 | 55 | 8470 | |
metal bronce | 49.000 | sesenta y cinco | 8746 | |
cobre | 28.000 | 10 | 8940 | |
Bronce fosforado | 55.000 | 78 | 8900 | |
bronce de aluminio | 27.000 | 77 | 7700-8700 | |
titanio | 63.000 | 37.000 | 80 | 4500 |
Titulación Universitaria
Es muy importante elegir el metal adecuado para tus proyectos. Puede consultar la tabla de resistencia del metal y elegir un material metálico adecuado según las características, funciones y aplicación de sus proyectos. Por supuesto, si crees que esto es complicado, puedes contactar con WayKen, quienes tienen una amplia experiencia en metalurgia y siempre podrán darte sugerencias profesionales para tu proyecto.