Con respecto a los elementos de aleación como Si, Mn, S, P, Cr, AI, Ti, Mo y V contenidos en el alambre de soldadura, ¿cuál es el impacto de estos elementos de aleación en el rendimiento de la soldadura? Las siguientes son explicaciones para cada elemento:
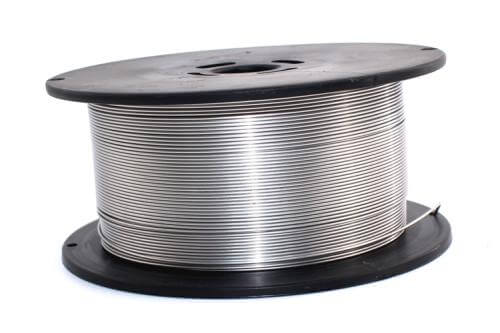
Silicio (S i )
El silicio es el elemento desoxidante más utilizado en los alambres de soldadura. Puede evitar que el hierro se combine con el oxígeno y puede reducir el FeO en el charco fundido.
Sin embargo, cuando se utiliza silicio solo para la desoxidación, el SiO2 resultante tiene un alto punto de fusión (aproximadamente 1710 ℃) y las partículas producidas son pequeñas y difíciles de flotar fuera del baño de soldadura. Esto puede provocar que la escoria quede atrapada en el metal de soldadura.
Manganeso (Mn)
La función del manganeso es similar a la del silicio, pero su capacidad de desoxidación es ligeramente menor que la del silicio. Cuando se usa manganeso solo para la desoxidación, el MnO resultante tiene una densidad más alta (15,11 g/cm 3 ) y también es difícil que flote fuera del baño de soldadura.
Además de su función desoxidante, el manganeso en el alambre de soldadura también puede combinarse con azufre para formar sulfuro de manganeso (MnS), que puede eliminarse (desulfurarse), reduciendo así la tendencia al craqueo en caliente causado por el azufre.
Debido a que es difícil eliminar los productos de desoxidación cuando se usan silicio o manganeso solos para la desoxidación, comúnmente se usa una combinación de silicio y manganeso para formar un compuesto de silicato (MnO · SiO 2 ) durante la desoxidación.
MnO·SiO 2 tiene un punto de fusión más bajo (aproximadamente 1270 °C) y una densidad más baja (aproximadamente 3,6 g/cm 3 ). Puede coagularse en grandes bloques de escoria y flotar fuera del baño fundido, logrando un buen efecto de desoxidación.
El manganeso también es un importante elemento de aleación en el acero y un importante elemento de templabilidad. Tiene un impacto significativo en la tenacidad del metal de soldadura.
Cuando el contenido de Mn es inferior al 0,05%, el metal de soldadura tiene una alta tenacidad. Cuando el contenido de Mn es superior al 3%, el metal de soldadura se vuelve quebradizo. Cuando el contenido de Mn está entre 0,6% y 1,8%, el metal de soldadura tiene alta resistencia y tenacidad.
Azufre (S)
El azufre en el acero suele estar presente en forma de sulfuro de hierro, que se distribuye en forma de malla a lo largo de los límites de los granos y reduce significativamente la tenacidad del acero. La temperatura eutéctica del hierro y del sulfuro de hierro es relativamente baja (985°C).
Por lo tanto, durante el trabajo en caliente, dado que la temperatura de trabajo inicial generalmente está entre 1150 y 1200 ℃, el hierro eutéctico y el sulfuro de hierro ya se han derretido, provocando grietas durante el proceso de trabajo.
Este fenómeno se conoce como “fragilidad por calor de azufre”. La propiedad del azufre hace que el acero sea propenso a agrietarse en caliente durante la soldadura.
Por tanto, el contenido de azufre en el acero está estrictamente controlado. La principal diferencia entre el acero al carbono ordinario, el acero al carbono de alta calidad y el acero avanzado de alta calidad es la cantidad de azufre y fósforo.
Como se mencionó anteriormente, el manganeso tiene un efecto desulfurante porque puede formar sulfuro de manganeso (MnS) de alto punto de fusión (1600 ℃) con azufre, que se distribuye en forma granular dentro de los granos.
Durante el trabajo en caliente, el sulfuro de manganeso tiene suficiente plasticidad para eliminar los efectos nocivos del azufre. Por tanto, es beneficioso mantener una cierta cantidad de contenido de manganeso en el acero.
Fósforo (P)
El fósforo se puede disolver completamente en ferrita del acero. Su efecto fortalecedor sobre el acero es superado solo por el carbono y aumenta la resistencia y dureza del acero.
El fósforo también puede mejorar la resistencia a la corrosión del acero, pero disminuye significativamente su ductilidad y tenacidad. Este efecto es especialmente grave a bajas temperaturas, lo que se conoce como fenómeno del “fósforo quebradizo en frío”.
Por tanto, es perjudicial para la soldadura y aumenta la susceptibilidad del acero a agrietarse. Como impureza, también se debe limitar el contenido de fósforo en el acero.
Cromo (Cr)
El cromo puede aumentar la resistencia y dureza del acero, al tiempo que disminuye en menor medida su ductilidad y tenacidad. El cromo tiene una gran capacidad de resistencia a la corrosión y a los ácidos, por lo que los aceros inoxidables austeníticos generalmente contienen más del 13% de cromo.
El cromo también tiene fuertes propiedades antioxidantes y resistentes al calor. Por lo tanto, el cromo también se utiliza mucho en aceros resistentes al calor como 12CrMo, 15CrMo y 5CrMo. El cromo está presente en el acero en determinadas cantidades.
El cromo es un componente importante del acero austenítico y un componente de la ferrita. Puede mejorar la resistencia a la oxidación y las propiedades mecánicas del acero aleado a altas temperaturas. En el acero inoxidable austenítico, cuando la cantidad total de cromo y níquel es del 40% y la relación Cr/Ni es 1, hay tendencia al agrietamiento en caliente.
Sin embargo, cuando la relación Cr/Ni es 2,7, no hay tendencia al agrietamiento en caliente.
Por lo tanto, en general, cuando la relación Cr/Ni es de alrededor de 2,2-2,3 en acero tipo 18-8, el cromo puede formar fácilmente carburos en aleaciones de acero, reducir la conductividad térmica y causar dificultades en la soldadura debido a la formación de óxido de cromo.
Aluminio (IA)
El aluminio es uno de los elementos desoxidantes fuertes. Por lo tanto, el uso de aluminio como desoxidante no solo puede reducir la producción de FeO, sino que también facilita la reducción de FeO, suprimiendo efectivamente la reacción química del gas CO producido en el baño fundido y mejorando la capacidad de resistir la porosidad del CO.
Además, el aluminio también puede combinarse con nitrógeno para formar un efecto de fijación de nitrógeno, reduciendo la porosidad del nitrógeno.
Sin embargo, el uso de aluminio para la desoxidación da como resultado la formación de AI 2 Ó 3 de alto punto de fusión (aproximadamente 2050 ℃), que existe en estado sólido en el baño de soldadura y es fácil de provocar que la escoria quede atrapada en el metal de soldadura.
Al mismo tiempo, el alambre de soldadura que contiene aluminio es propenso a salpicar y un contenido excesivo de aluminio puede reducir la resistencia del metal de soldadura al agrietamiento en caliente.
Por lo tanto, el contenido de aluminio en el alambre de soldadura debe controlarse estrictamente y no debe ser demasiado alto. Si el contenido de aluminio en el alambre de soldadura se controla adecuadamente, la dureza, el límite elástico y la resistencia a la tracción del metal de soldadura mejorarán ligeramente.
Titanio (TI)
El titanio también es un fuerte elemento desoxidante y también puede combinarse con nitrógeno para formar TiN, desempeñando un papel en la fijación de nitrógeno y mejorando la capacidad del metal de soldadura para resistir la porosidad del nitrógeno.
Si están presentes cantidades apropiadas de titanio y boro (B) en la estructura de metal de soldadura, la estructura de metal de soldadura se puede refinar.
Molibdeno (Mo)
El molibdeno puede aumentar la resistencia y dureza del acero aleado, refinar el tamaño del grano, prevenir la fragilidad y la tendencia al sobrecalentamiento y mejorar la resistencia a altas temperaturas, la resistencia a la fluencia y la durabilidad.
Cuando el contenido de molibdeno es inferior al 0,6%, puede mejorar la ductilidad, reducir la tendencia a agrietarse y aumentar la resistencia al impacto. El molibdeno también tiene tendencia a promover la grafitización.
Por tanto, el contenido de molibdeno en aceros resistentes al calor como 16Mo, 12CrMo, 15CrMo, etc. suele rondar el 0,5%.
Cuando el contenido de molibdeno en el acero aleado está entre 0,6% y 1,0%, el molibdeno puede reducir la plasticidad y tenacidad del acero aleado y aumentar su tendencia al templado.
Vanadio (V)
El vanadio puede aumentar la resistencia del acero, refinar el tamaño del grano, reducir la tendencia al crecimiento del grano y mejorar la templabilidad.
El vanadio es un elemento formador de carburos relativamente fuerte y los carburos que forma son estables por debajo de 650°C.
También tiene efectos endurecedores de la edad. Los carburos de vanadio tienen estabilidad a altas temperaturas y pueden mejorar la dureza del acero a altas temperaturas. El vanadio también puede alterar la distribución de los carburos en el acero, pero es propenso a formar óxidos refractarios, lo que dificulta la soldadura y el corte.
Generalmente, cuando el contenido de vanadio en el metal de soldadura es de alrededor del 0,11%, puede desempeñar un papel en la fijación de nitrógeno, convirtiendo una situación desfavorable en favorable.