1. Principales causas de error dimensional de piezas provocado por oxicorte
Las principales causas de errores en el corte y corte NC incluyen la deformación térmica de la lámina de acero, la técnica del operador, la planitud de la plataforma de soporte, la precisión del equipo y el grado de corrosión en la superficie de la lámina de acero.
2. Análisis de errores dimensionales de piezas producidas por oxicorte y mediciones específicas.
El oxicorte de chapas de acero siempre implica una deformación en caliente. Sin embargo, los errores dimensionales en piezas deformadas en caliente se pueden reducir significativamente. La velocidad de corte y la calidad de las piezas se ven afectadas por las habilidades del operador.
La nivelación de la plataforma de soporte y la precisión del equipo tienen el mayor impacto en el tamaño de las piezas. Las imprecisiones a menudo pueden provocar que las piezas se descarten directamente. Además, la corrosión superficial de la placa de acero puede afectar tanto a la calidad como a la velocidad de corte.
2.1 Error dimensional de piezas causado por deformación térmica de placa de acero
La deformación térmica en chapas de acero se nota principalmente en piezas delgadas. Con base en años de práctica y análisis de corte, se ha determinado que los errores dimensionales en las piezas causados por la deformación térmica se pueden minimizar centrándose en los tres aspectos siguientes:
2.1.1 Dibujar gráficos de piezas
Al crear gráficos para piezas, asegúrese de incluir una cantidad adecuada de compensación de expansión térmica en la dirección longitudinal de la pieza. El monto de la compensación debe seleccionarse en función de las características específicas de cada parte individual.
Ventajas : compensa directamente el error dimensional de las piezas provocado por la expansión térmica;
Desventajas : Sólo es aplicable a piezas cuadradas y otras formas no son fáciles de compensar.
2.1.2 D proceso de alta detallado
A partir del aspecto de descarga, refine el proceso de descarga y formule un proceso de descarga especial para piezas volátiles.
2.1.2 se obtiene del borde común
El uso de un borde común puede reducir el tiempo de corte, minimizar el aporte de calor a través de la placa de acero, reducir la expansión de la placa de acero y en consecuencia reducir los errores dimensionales de las piezas.
Como se ilustra en la Figura 1, cuando no se crea un borde común, AB y CD en dos lados adyacentes de dos partes deben cortarse por separado.
Por otro lado, después de utilizar un borde común, sólo es necesario cortar el borde AB y no es necesario cortar el borde CD.
Esto no sólo reduce los errores en las piezas, sino que también aumenta la eficiencia del corte y la utilización de la chapa.
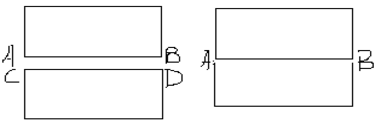
2.1.2 R dirección de corte razonable
Determine la dirección de corte razonable de la pieza de acuerdo con la situación real, primero corte el orificio, luego corte la forma y primero corte el borde cerca del borde de la placa de acero.
Intente asegurarse de que haya suficiente rigidez de conexión entre la pieza de trabajo y la placa de acero antes de cortar la pieza de trabajo cerca del punto de finalización, para garantizar el tamaño de corte y la precisión de la pieza de trabajo.
Por ejemplo, en la Fig. 2, primero corte el orificio interior (1-6) y luego corte el contorno exterior en el orden A, B, C, D y A.
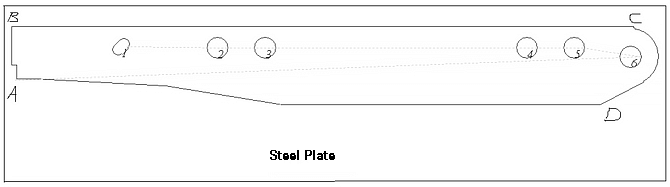
2.1.3 Diseño de piezas y ruta de corte sencillos
El error causado por la deformación de la placa de acero se puede minimizar mediante la disposición adecuada de las piezas y el ajuste de la trayectoria de corte.
Como se ilustra en la Figura 3, las piezas en forma de T que son susceptibles a deformarse deben combinarse con piezas más pequeñas que tienen menos probabilidades de deformarse. Esto ayuda a reducir el calentamiento excesivo en áreas localizadas, minimiza la deformación térmica y garantiza dimensiones precisas de las piezas.
Para minimizar la deformación en piezas delgadas, se debe utilizar corte desplazado al descargarlas.
Como se muestra en la Figura 4, después de cortar la parte 2, se debe usar la segunda columna para cortar la parte 3. Después de que la parte 2 se enfríe durante un tiempo determinado, se debe girar para cortar la parte 4.
Se deben hacer esfuerzos para evitar un calentamiento excesivo localizado de la chapa de acero, minimizar la deformación térmica y garantizar al máximo la precisión de las dimensiones de la pieza.
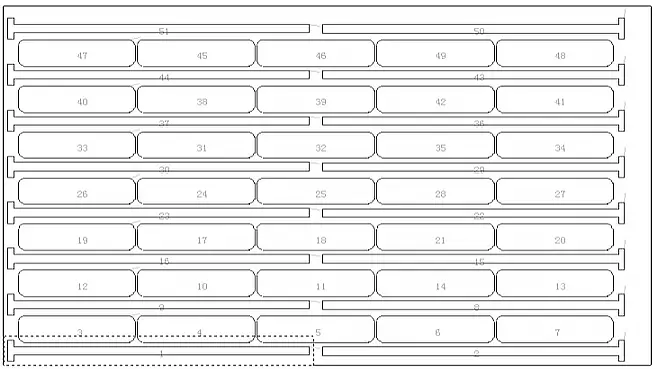

2.1.2S intervalo de configuración
Para reducir el error causado por la deformación de la placa de acero (como se muestra en la Fig. 5), se recomienda establecer intervalos. Tenga en cuenta que las secciones A, B, C y D no deben cortarse temporalmente, sino durante la limpieza de la plataforma.
Ventajas : reduce directa y eficazmente la deformación de la pieza;
Desventajas : La configuración de intervalos aumenta el número de perforaciones de corte, aumenta el tiempo de corte y aumenta el consumo de la boquilla de corte.
Cortar el espacio (como se muestra en la Fig. 6) puede provocar cicatrices que deje el personal de limpieza de la plataforma.
Se requerirán reparaciones, soldaduras y esmerilados posteriores.
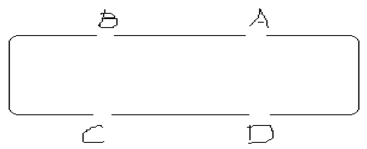
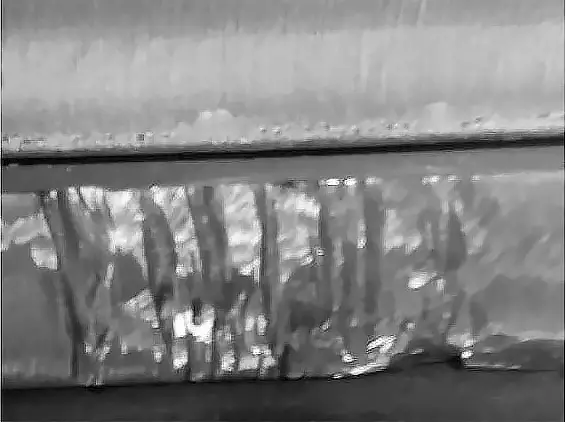
Según las diferentes situaciones, la elección y el uso de métodos adecuados o una combinación de varios métodos para controlar la deformación de la placa de acero pueden desempeñar un papel obvio.
2.2. Error dimensional de piezas causado por la tecnología del operador NC
En teoría, al utilizar el mismo equipo y programa NC, las piezas a cortar deberían ser idénticas. Sin embargo, en realidad, este no es siempre el caso.
Incluso con el procedimiento correcto, las piezas cortadas por diferentes operadores pueden presentar variaciones de tamaño y errores, e incluso algunas pueden necesitar ser desguazadas.
Para garantizar que las piezas se corten correctamente, se debe elegir la boquilla de corte adecuada en función del espesor de la placa de acero. Se debe ajustar correctamente la llama y establecer la compensación de espacio correspondiente para garantizar que las piezas sean de alta calidad.
Como referencia, consulte la siguiente tabla que proporciona los parámetros del proceso de corte con gas.
Parámetros del proceso de corte |
|||||||
Número de boquilla de corte |
Cortar el diámetro del orificio de oxígeno/mm |
Espesor de corte /mm |
Velocidad de corte mm/min |
Tiempo/s de precalentamiento |
Presión de oxígeno MPa |
Presión de gas MPa |
Valor de compensación de grietas /mm |
1 |
1.0 |
5-10 |
700-500 |
5-12 |
0,6-0,7 |
>0.03 |
dos |
dos |
1.2 |
10-20 |
600-380 |
15-25 |
0,6-0,7 |
>0.03 |
2.5 |
3 |
1.4 |
20-40 |
500-350 |
25-30 |
0,6 ~ 0,7 |
>0.03 |
3 |
4 |
1.6 |
40~60 |
420-300 |
35-50 |
0,6-0,7 |
>0.03 |
3.5 |
5 |
1.8 |
60-100 |
320-200 |
50-80 |
0,6-0,7 |
>0.03 |
3.5 |
6 |
2.0 |
100-150 |
260~140 |
80-120 |
0,7-0,8 |
>0,04 |
3.5 |
Nota: La pureza del oxígeno es superior al 99,5%.
2.3. Error dimensional de piezas causado por la plataforma de soporte.
La razón principal de los errores dimensionales en las piezas causados por la plataforma de soporte se debe a que el plano de la plataforma de soporte no es paralelo a la superficie del riel guía de la máquina de corte NC.
La plataforma de trabajo de placa de acero de soporte a menudo sufre impactos y golpes en la plataforma de carga y descarga, lo que hace que su plano se vuelva desigual y no paralelo a la superficie del riel guía de la máquina de corte NC.
Si el desnivel es significativo, puede provocar que el soplete de corte de la máquina cortadora no sea perpendicular a la placa de acero, lo que provocará que la dirección del espesor de toda la pieza se incline.
Debido al corte con llama de larga duración, la placa de inserción de la plataforma de soporte puede sufrir daños por corte y adherencia de escoria, lo que provoca irregularidades locales en la plataforma de soporte.
Durante el proceso de corte de la pieza, la pieza puede quedar parcialmente suspendida, lo que da como resultado una inclinación parcial de la dirección del espesor de la pieza.
Cuando el espesor de la placa de acero es relativamente grande, el tamaño de la pieza tendrá un error significativo.
2.4. Error dimensional de piezas causado por la precisión del equipo.
La precisión del riel guía del equipo tiene un impacto directo en la precisión de las piezas cortadas. Para minimizar los errores causados por la precisión del riel guía, es esencial mantener y verificar periódicamente el paralelismo y la planitud del riel guía.
Proteger los parámetros del equipo es crucial. Cualquier cambio realizado en los parámetros verticales y horizontales del equipo puede provocar el desguace de un número importante de piezas.
Los operadores deben realizar una autoinspección minuciosa de las piezas, especialmente las grandes, e informar inmediatamente de cualquier problema encontrado. Este enfoque ayudará eficazmente a identificar tales problemas.
3. Conclusión
Se pueden combinar varios métodos para reducir eficazmente los errores y mejorar la calidad del producto en función de las causas de los errores en diferentes partes.