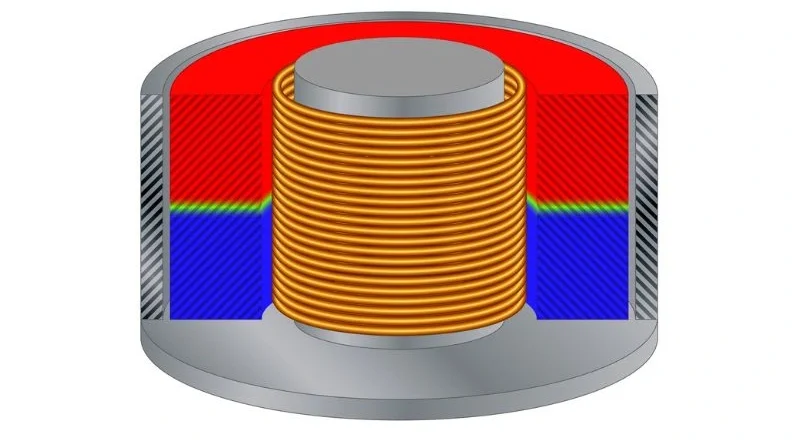
PMMC, short for Permanent Magnet Moving Coil, is an indispensable instrument in electrical engineering. They reliably measure direct current or direct current in various applications, ensuring maximum efficiency and safety. What's amazing about these tools is that they translate scientific principles into practical applications – the force on a moving coil in the field of a permanent magnet provides information about the flow of electricity. Now let's explore this complex science made simple yet useful.
The PMMC (Permanent Magnet Moving Coil Instrument) instrument is known for its accuracy in measuring direct current. Its main components include moving coil, permanent magnet, control springs, damping system, pointer and scale, providing accurate readings and low power consumption.
The role of the PMMC instrument
Imagine having to measure water flow in a river without a reliable flow meter. That would be very difficult, right? Accurate measurement of direct current (DC) is crucial for many electrical engineering applications. This is where the PMMC instruments come into action. These instruments are like reliable measuring devices that provide accurate voltage and current measurements. Its importance cannot be underestimated, especially when it comes to maintaining safety and efficiency in electrical systems.
PMMC instruments are carefully designed to ensure accurate measurements. They consist of essential components such as a moving coil, a permanent magnet, control springs, a damping system, a pointer and a scale. These elements work seamlessly together to provide reliable readings, allowing engineers and technicians to safely monitor and troubleshoot electrical circuits.
Accuracy and reliability
One of the most important aspects that make PMMC instruments indispensable is their accuracy. With an accuracy of +/- 1%, these instruments provide consistent and reliable measurements, ensuring systems function optimally and safely.
For example, in automotive applications where electrical currents must be accurately monitored to ensure the proper functioning of critical systems such as engine control units or safety functions, PMMC instruments play a crucial role in providing accurate measurements.
Flexibility in measuring range
Another notable feature of PMMC instruments is their ability to effectively measure a wide range of voltages and currents. This flexibility allows these instruments to be used in different environments and applications without the need for recalibration or constant adjustment.
In laboratory environments where experiments may use different voltage and current levels, PMMC instruments can adapt to these changing requirements, giving researchers confidence that their measurements are accurate across multiple parameters.
The ability of PMMC instruments to provide accurate measurements with high reliability and flexibility demonstrates their central role in supporting the diverse needs of electrical engineers across a wide range of applications.
Let's now delve deeper into the complex mechanisms that allow PMMC instruments to make such precise measurements.
How the PMMC instrument works
A PMMC instrument may appear simple on the surface, but its operation is based on fascinating physical principles. The core of a PMMC meter is the interaction between a permanent magnet and a moving coil. When an electric current flows through the coil, it experiences a force due to the magnetic field created by the permanent magnet. This force causes the coil to move in direct proportion to the current flowing through it.
The key to understanding this interaction lies in the fundamental concept of electromagnetism. As current flows through the coil, it creates a magnetic field that interacts with the magnetic field of the permanent magnet. This interaction results in mechanical movement of the coil, which is then translated into a measurement of current flow. This direct relationship between current and coil movement makes PMMC instruments extremely accurate in measuring direct currents.
Importance of magnetic field strength
For a PMMC instrument to function correctly, the magnetic field strength must be within a certain range, typically 0.1 to 0.2 Tesla. This ensures that the force applied to the moving coil remains constant, allowing for accurate measurements.
For context, think of it this way: just like you need water pressure in your home for a faucet to work properly, a PMMC instrument requires a certain magnetic field strength to work accurately.
Understanding this interaction between electrical current and magnetic fields highlights why PMMC instruments are ideal for measuring direct currents with remarkable accuracy. This reliable and consistent ratio has made these instruments indispensable in electrical measurements, especially for applications where accurate readings are required.
Now let's examine the critical role that construction materials and design elements play in ensuring the accuracy and reliability of PMMC instruments.
Accurate DC measurement and PMMC methodology
PMMC instruments play a crucial role in accurately measuring direct currents. Imagine this: the movement of a coil in a magnetic field serves as a measure of precision. The unique design of PMMC instruments allows for accurate measurement of direct currents, making them an indispensable tool in electrical engineering.
The methodology used in PMMC instruments revolves around keeping the deflection torque in direct proportion to the current flowing through the coil. This proportional relationship is critical to ensuring accurate DC measurement. In other words, as the current flowing through the coil changes, the deflection torque also changes, allowing for accurate readings that reflect the actual value of the measured DC current.
To put this into perspective, imagine a well-tuned instrument sensitive to current fluctuations. A small change in current results in an immediate response from the instrument pointer. This sensitivity allows for accurate and reliable measurements and provides electrical engineers with valuable data for their work.
But what makes PMMC instruments so suitable for accurate DC measurements? It's about its design and operational functions. The moving coil in combination with a permanent magnet and control springs results in an instrument that impresses with its precision and reliability.
Device feature | To use |
moving coil | Sensitive reaction to current changes |
Permanent magnet | Provides a constant magnetic field for smooth operation |
control springs | Ensure adequate movement and stability for accurate measurements |
Damping system | Minimizes vibrations for stable measured values |
Understanding these special components shows why PMMC instruments are valued for their unparalleled accuracy in measuring DC currents.
Now that we've looked at how PMMC instruments ensure accurate DC measurements, it's time to look at their capabilities in more detail.
Advantages and Disadvantages of PMMC Instrument
With their unique design, PMMC instruments offer several advantages that make them an indispensable tool for accurate DC measurements and electrical engineering applications. First, let's look at the benefits of PMMC instruments.
Advantages of the PMMC instrument
The correctly divided scale of PMMC instruments allows for accurate readings, essential for accurate measurements in electrical engineering. This feature ensures that the instrument provides detailed and reliable data for analysis, making it a preferred choice in diverse areas such as power systems, electronic circuit design, and industrial automation.
Furthermore, PMMC instruments are characterized by low power consumption in terms of energy efficiency. With the growing importance of sustainable energy practices, making accurate measurements while saving energy is a significant advantage in modern electrical systems and laboratories.
The high precision of PMMC instruments contributes to their reliability in measuring diverse voltage and current ranges. In applications where accuracy is of utmost importance, such as: When testing electrical components or calibrating equipment, the ability to trust the accuracy of PMMC instruments is invaluable.
Another important advantage of PMMC instruments is their adaptability to measure different voltage and current ranges. This versatility enables diverse applications, from testing low-voltage circuits to monitoring high-current systems, providing engineers with a comprehensive tool for different electrical measurement needs.
Although PMMC instruments offer several advantages that make them indispensable in diverse electrical engineering scenarios, it is important to consider their limitations.
Disadvantages of the PMMC instrument
A major limitation of PMMC instruments is their limitation to DC measurements. This limitation limits its use in applications that require AC measurements or a combination of AC and DC analyses. Although they excel at accurate DC measurements, alternative instruments are needed for comprehensive electrical analysis using AC circuits.
In addition to their limited application to DC measurements, the higher cost of PMMC instruments compared to other types of instruments can be a challenge, especially for projects with limited budgets or educational institutions. The initial investment required to purchase PMMC instruments may discourage some users from using this technology in certain scenarios.
We cannot underestimate the importance of understanding these drawbacks when considering the application of PMMC instruments in various electrical engineering contexts.
Imagine having a toolbox with different tools for specific tasks. Just as a wrench does not need to be suitable for all screw types, PMMC instruments have strengths and weaknesses that must be carefully examined before use in electrical measurement operations.
By weighing the pros and cons of PMMC instruments, engineers and professionals can make informed decisions about using accurate electrical measurements and instruments.
Now let's examine the potential errors that can affect the performance of PMMC instruments in electrical measurements.
PMMC instrument errors and their most common causes
PMMC instruments are known for their accuracy in measuring direct current. However, as with any instrument, errors may occur that affect accuracy. Understanding these common causes of error is critical to ensuring accurate measurements and maintaining the reliability of PMMC instruments.
A common cause of failure in PMMC instruments is aging. As with any other mechanical device, the components of a PMMC instrument can wear out over time, affecting its accuracy. For example, the strength of the permanent magnet may decrease or the control springs may lose their elasticity. These changes can result in measurement discrepancies, which is why regular maintenance is essential to ensure optimal performance.
Temperature effects can also significantly affect the accuracy of PMMC instruments. Temperature fluctuations can cause the materials used in the instrument to expand or contract, which in turn leads to changes in the tension of control springs or deterioration of the magnetism of the permanent magnet. Such fluctuations can lead to measurement errors, highlighting the need for temperature-controlled environments when using PMMC instruments for accurate measurements.
Weak magnets and springs are other factors that contribute to errors in PMMC instruments. If the strength of the permanent magnet weakens or the control springs lose elasticity, the deflection torque may be affected, resulting in inaccurate readings. These components are essential for proper moving coil deflection, which is why regular checks and replacements are important to maintain measurement accuracy.
Expanded moving coil area is another common cause of failure in PMMC instruments that should not be overlooked. Let's look at this in more detail.
PMMC instrument calibration and maintenance
Proper calibration and regular maintenance are essential for optimal performance and accuracy of PMMC instruments. Calibration involves comparing the readings of one device or system with those of another calibrated and referenced to a known set of parameters. This guarantees accurate and reliable measurements. On the other hand, maintenance practices help prevent errors and ensure the longevity of these instruments.
Calibration frequency is critical to maintaining the accuracy of PMMC instruments and typically occurs every 6 months. This frequency may vary depending on usage, environmental conditions and industry standards. Regular calibration ensures accurate readings and helps identify underlying issues before they become serious problems.
Importance of calibration
Calibration ensures the accuracy and functionality of PMMC instruments by adjusting their performance to international or industry standards. Regular calibration ensures they achieve required levels of accuracy and meet regulatory standards. Proper and timely calibration can improve accuracy by +/- 0.5%, significantly increasing the reliability of measurements made with PMMC instruments.
To put this into perspective, imagine a scenario in which an electrical engineer uses an uncalibrated PMMC instrument to measure current in a circuit. Due to inaccuracies, variations in actual current values may occur, resulting in erroneous assessments and potentially affecting the safety and efficiency of the entire electrical system.
Maintenance Vitality
In addition to calibration, regular maintenance is critical to the longevity and efficient operation of PMMC instruments. Typical maintenance tasks may include cleaning, lubricating, checking for mechanical wear, and ensuring that all components are functioning optimally.
Regular maintenance can prevent errors and extend the life of PMMC instruments by up to 20%. This simple yet effective approach can significantly help PMMC instruments provide accurate measurements over time.
When maintaining PMMC instruments, proactive measures such as cleaning and lubrication reduce common causes of failure such as aging, temperature effects, weak magnets, weak springs and mechanical wear – factors that significantly impact accuracy and performance if not proactively addressed through regular maintenance protocols.
In conclusion, proper calibration at regular intervals and effective maintenance practices are the cornerstones to ensuring accurate functionality and longevity of PMMC instruments. mytech-info. com We provide detailed guidance with comprehensive calibration procedures and maintenance best practices tailored to maintain the accuracy and reliability of PMMC instruments for a variety of electrical engineering applications.
For more guidance on calibrating and maintaining your PMMC instruments, see our complete guide to magnets at mytech-info.com/category/magnet/ .