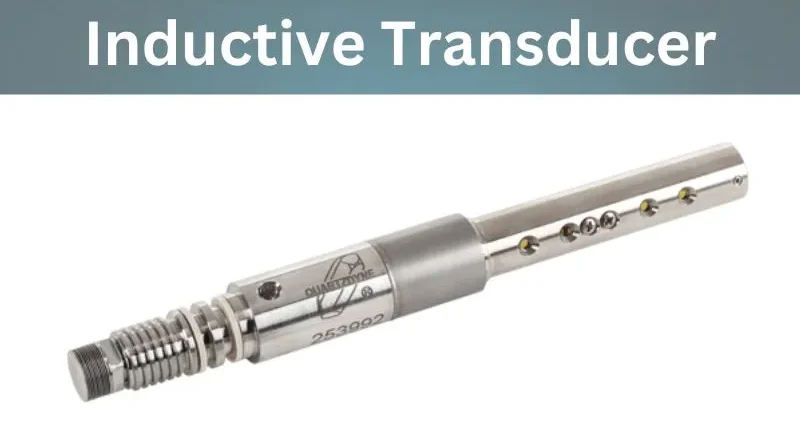
The inductive transducer is an instrument that uses electromagnetic principles to convert physical movements into changes in inductance. They respond to changes such as the rotation of a coil, the size of magnetic material, and adjustments in flow permeability. Far from just any device, these transducers perform important tasks, including motion detection and metal detection in devices like touchpads and proximity sensors. Dive deeper into their many uses and learn how they work to turn imperceptible movements into valuable data.
An inductive transducer works by inducing magnetic materials. Changes in factors such as coil twists, magnetic material size, and flux permeability affect the inductance of the circuit, allowing you to convert physical motion into a change in inductance.
Basics of Inductive Converters
Inductive transducers are widely used in various fields because of their ability to convert physical movements into changes in inductance. Their operation is based on the principle of electromagnetic induction, that is, they generate electrical voltage when the magnetic field changes.
This change occurs due to the twists in the coil, the size of the magnetic material, and the permeability of the flux. These factors directly affect the inductance of the circuit, allowing inductive transducers to detect and respond to physical changes. For example, when a metallic object approaches the transducer, the magnetic field around it changes, resulting in a change in inductance. This change can be accurately measured and converted into useful data.
Imagine a proximity sensor at the entrance to a parking lot. When a car approaches, it triggers the sensor causing a change in the magnetic field, which is then converted into an electrical signal that triggers a gate opening mechanism. The inductive transducer allows accurate detection without direct contact and is therefore ideal for such applications.
Furthermore, these transducers play a crucial role in touchpad devices that detect capacitance fluctuations due to the proximity and touch of human fingers. They are also used in dynamic motion measurement systems to accurately track movement and speed.
Inductive transducers have remarkable versatility that goes far beyond what we generally know. Now let's explore some specific applications where these devices are indispensable.
Inductive converters power countless critical applications and demonstrate their adaptability and precision. In the next section we will look at specific types and examples of inductive transducers.
Types and examples of inductive transducers
Inductive transducers come in different types, each suited to specific applications and industries.
Simple Inductance Converter
Let's start by exploring the Simple Inductance Converter . This type directly converts the measured mechanical quantity into a change in inductance and is widely used in various sensing systems such as proximity sensors, accelerometers, and vibration sensors.
The Single Inductance Converter is versatile because it can record several mechanical quantities, such as displacement, position and pressure. For example, it is often used in the automotive industry to measure tire pressure and fuel levels in tanks. This makes it an integral part of modern vehicles and contributes to efficient performance and safety measures.
Counterinductive transducer with two coils
Now let's take a look at those Counterinductive transducer with two coils . This type detects the change in mutual inductance between the primary and secondary coils. A well-known example of this category is the linear variable differential transformer (LVDT), which is widely used for accurate position measurement in aerospace, manufacturing and robotics. Its ability to provide accurate and reliable measurements has made it indispensable for critical applications where accuracy is of utmost importance.
In medical devices such as MRI machines, inductive transducers are crucial for detecting changes in magnetic fields. The phenomenon of nuclear magnetic resonance in the tissues of the human body creates these fluctuations. By accurately measuring these changes, medical professionals can create detailed images for diagnostic purposes.
The versatility of inductive transducers goes beyond traditional industrial applications; they also play a crucial role in scientific research and exploration. For example, search coil magnetometers use inductive sensors to measure magnetic fields in geophysical surveys, space exploration missions, and environmental studies.
By understanding the different types of inductive transducers and their practical applications, we can recognize their far-reaching impact on a wide range of areas – from automotive engineering to medical diagnosis – and demonstrate their indispensable value in modern technology.
Now that we have familiarized ourselves with the wide range of possible uses of inductive transducers in different industries and environments, let's take a closer look at how these transducers work in specific measurement situations.
How inductive converters work
Let's explore electromagnetic induction to understand how inductive transducers work. When a magnetic material moves in the magnetic field of an inductor, it causes changes in the circuit's inductance.
Let's break this down further : Imagine a coil and a core. The position of the core changes in response to the measured physical quantity, causing a change in the inductance of the coil. This movement is directly related to the measured physical quantity, such as: B. Displacement, coupling distance or changes in the magnetic field.
This process results in a corresponding change in the electrical output signal, which has applications in diverse areas such as proximity sensors, touchpads, dynamic motion measurement, metal detection, and motion detection in devices such as belt conveyors and bucket elevators.
An example of this is the linear variable differential transformer (LVDT), which uses the principle of mutual inductance and is widely used to accurately measure displacement and position due to its accuracy and reliability.
Mathematical models
Theoretical data for inductive transducers often include mathematical models or equations that describe the relationship between the measured physical quantity and the output electrical signal. These models are crucial for understanding and predicting the behavior of inductive transducers in various scenarios.
An LVDT, for example, is characterized by a special transfer function that relates its input (displacement) to its output (voltage). This transfer function allows engineers to accurately calibrate LVDTs and use them safely in a variety of applications.
Understanding the complex functionality and practical application of inductive transducers provides valuable insights into their use across various industries and technologies. If you want more detailed insights and practical examples of how they work, mytech-info. com is your point of contact!
Would you like to know more about the strengths and weaknesses of inductive transducers? In the following, we will examine these aspects in more detail to fully understand their implications for practical applications.
Advantages and limitations
Inductive transducers offer several advantages that make them valuable tools in a variety of applications.
High responsiveness
Their high responsiveness allows them to detect even the smallest changes in physical properties, making them incredibly accurate measuring devices.
Reduced load effects
This high accuracy is further enhanced by the reduced load effects, ensuring that the measurements obtained are accurate and not influenced by external factors.
Robustness in demanding environments
Furthermore, inductive transducers are robust against environmental influences. Whether exposed to moisture, dust or temperature fluctuations, these transducers maintain their functionality and accuracy, making them reliable components in critical industrial and scientific environments.
Restrictions to Consider
Despite their many strengths, inductive transducers have limitations that must be considered when determining their suitability for specific applications.
Limitations in operating range
A common limitation is reduced operating range due to side effects. While they are excellent at making accurate measurements within a certain range, they can have difficulty maintaining accuracy outside of these parameters. For example, an inductive transducer designed for highly accurate measurement of small displacements may not be suitable for applications that require measurements over a wide range, compromising its versatility and applicability.
Sensitivity to magnetic fields
Furthermore, sensitivity to magnetic fields can be a challenge for inductive transducers in environments with prevalent magnetic interference. Although they can detect changes in magnetic materials, excessive external magnetic fields can cause inaccuracies in measurements.
Temperature restrictions
Additionally, temperature limitations can affect the performance of inductive transducers. Extremely high or low temperatures can affect the properties of the materials used in these transducers, causing variations in their responsiveness and accuracy.
Understanding the notable advantages and limitations of inductive transducers provides valuable information about their optimal use and the precautions necessary to maximize their effectiveness.
In the following course we will examine how these properties can be transferred to different applications in different areas.
Applications in various areas
Inductive transducers are incredibly versatile and are used in a variety of industries due to their ability to convert physical quantities into electrical signals. Let us now explore some fascinating applications that highlight the importance of inductive transducers in modern technology.
Proximity sensors in robotics
Inductive transducers play a crucial role in robotics because they enable proximity sensors. In robotics, accurate detection of objects or obstacles is crucial for safe and efficient operations. Inductive transducers enable reliable, contactless detection of metallic objects so robots can efficiently navigate their environment. This technology is critical for industrial robotics, automated material handling systems, and even advanced prosthetics, where object detection and obstacle avoidance are key.
A notable example of this application is assembly line robots, which use inductive transducers to locate components and perform complicated tasks with high precision. These robots can work efficiently in complex environments with minimal human intervention.
Touchpad technology in consumer electronics
Have you ever wondered how the touchpad on your smartphone or laptop works? Inductive transducers form the heart of touchpad technology and enable the detection of touch and finger movements. These transducers convert the user's touch into electrical signals, allowing intuitive interaction with electronic devices. This app has revolutionized the way we interact with consumer electronics by providing responsive and accurate touch controls for multiple devices.
The sensitivity and precision of inductive transducers have paved the way for innovative touch-sensitive interfaces that improve the user experience. From smartphones and tablets to laptops and smart home devices, the seamless integration of inductive transducer-based touchpad technology has become an integral part of modern consumer electronics.
Metal detection in security systems
Metal detection is crucial in security systems to ensure security and prevent unauthorized access to restricted areas. They use inductive transducers that allow reliable detection of metallic objects, such as weapons or prohibited items. These transducers allow security personnel to conduct thorough inspections while maintaining operational efficiency.
Take airport security checkpoints, for example. Metal detectors have sophisticated inductive transducers that can distinguish between harmless everyday objects and potentially dangerous metal objects. This level of accuracy is essential to ensure public safety without unduly disrupting normal operations.
Elevator motion detection
Elevators have precise motion detection systems to ensure smooth operation and passenger safety. Inductive transducers detect elevator positions, speed fluctuations and door movements. By accurately capturing these parameters, inductive transducers contribute to the safe and efficient operation of elevators in residential, commercial and industrial environments.
The integration of inductive transducers improves the performance and reliability of vertical transportation through real-time monitoring and control mechanisms.
The diverse possible uses of inductive converters highlight their indispensable role in a wide variety of industries. They influence technological progress and contribute to improving functionality and security in several areas.
Selection of suitable inductive displacement transducers
Choosing the correct inductive transducer is crucial for the optimal performance of electrical systems. There are several factors to consider when making this decision, and it involves more than just randomly selecting a sensor.
One of the most important points to consider is the specific application requirements. For example, if you need a sensor for a harsh environment with a lot of dust, humidity, or extreme temperatures, you want a sensor that can easily handle those conditions.
Environmental conditions
Environmental factors such as temperature range, presence of water/moisture, exposure to dirt and chemicals, and potential electromagnetic interference can significantly affect the performance and lifespan of an inductive proximity sensor. In heavy machinery and equipment scenarios where sensors may be exposed to high levels of electromagnetic noise, it is essential to select sensors designed to operate reliably under these conditions.
It's similar to choosing a coat – you wouldn't choose a thin raincoat if you were going mountain climbing! You would need something much tougher and warmer to withstand harsh conditions.
Compatibility with existing systems is another important aspect. When selecting an inductive proximity sensor, it is important to ensure compatibility with your existing control system and wiring. This includes evaluating the initial sensor configuration (two-wire or three-wire) and determining whether additional devices or modifications are needed for seamless integration into the system.
System operating voltage
The operating voltage of the system is also crucial. Different systems operate at different voltages, so it's important to make sure your sensor adapts to this. For example, your phone's charger doesn't work with all devices, so the sensors must meet the system's voltage requirements.
Understanding these selection criteria is critical to optimizing the performance of electrical systems. These considerations ensure that the selected inductive proximity sensor is suitable for specific application requirements, can withstand environmental stresses and can be seamlessly integrated into existing systems. For a complete guide on how to select suitable inductive transducers for various applications, see mytech-info. with .
Knowing how to select appropriate inductive transducers will help you make an informed decision and configure your electrical systems for improved performance and longevity.