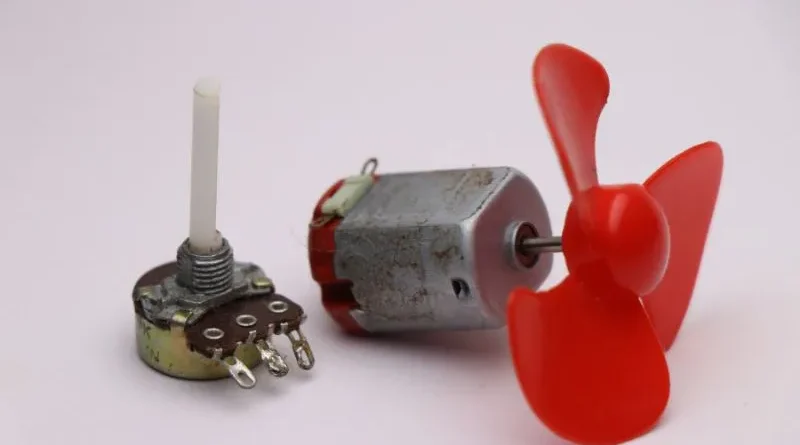
In electrical engineering, DC shunt motors have long been known for their versatile applications and robust performance – a crucial aspect of exploiting their full potential lies in effectively controlling their speed. The ability to regulate the speed of a DC shunt motor opens up a wide range of possibilities in diverse industries, from industrial machinery to electric vehicles.
This article discusses speed control methods for DC shunt motors and examines traditional and innovative techniques that maximize efficiency, accuracy, and overall motor performance. By understanding these methods, engineers can optimize the operation of DC shunt motors and unlock their full potential in numerous technological advances.Speed control methods
-
Flow Control Method
-
anchor control method and
-
Voltage regulation method
Flow Control Method
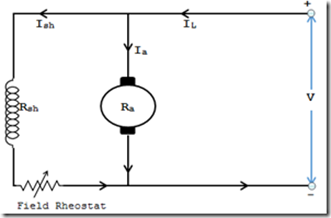
This method is widely used because it is very simple and cheap. In this method, speed control can be achieved by varying the flow Φ because the speed of the motor is N ∝ (1/ Φ), so it is called flow control method. An adjustable resistor is connected in series with the shunt field winding as shown in the figure. This adjustable resistance is also called a shunt field rheostat. This shunt field rheostat moderates the shunt current and flow. Therefore, we can only increase the speed beyond the rated engine speed. Typically allows thrust to build at a 3:1 ratio. Different speed choices tend to produce instability and poor switching.

Anchor Control Method
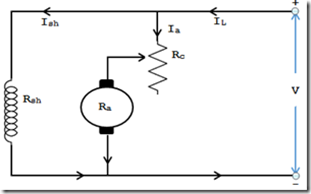
In this method, speed control can be achieved by varying the voltage across the armature and back emf. This is achieved by connecting an adjustable resistor in series with the armature shown in the figure. This adjustable resistance is also called the regulator resistance Rc.
N∝ {v-Ia(Ra+Rc)}
Anchor React on DC Motor
Armature response is a significant phenomenon in DC motors that affects their overall performance and operation. When current flows through the armature winding, a magnetic field is created that interacts with the main magnetic field produced by the field winding. This interaction, known as the anchoring reaction, leads to several effects. First, it distorts the main magnetic field and changes the flux density distribution in the motor. This distortion results in a displacement in the neutral plane in which the commutation occurs, which can lead to possible problems such as sparks and brush wear.
Voltage regulation method
In this method, the supply voltage that feeds the field current is different from that that feeds the armature. This technique can avoid the disadvantages of poor speed control and efficiency that occur with the armature control method. However, this method is quite expensive. Therefore, this method is used for larger engines where efficiency is a priority.
DC shunt motor speed control using voltage control method can be done in two ways. They are:
- Multiple Voltage Control
- Ward-Leonard system.
Multiple Voltage Control Method
Ward-Leonard System
DC shunt motor characteristics
DC shunt motors have unique properties that make them usable in many different applications. One of its notable features is relatively constant speed control over a wide load range. The speed of a shunt motor is determined by the back electromotive force (EMF) generated in the armature winding. As the motor load increases, the armature current increases, which leads to a drop in the armature voltage and therefore a reduction in the back emf force. This reduction in counter-electromotive force leads to a slight reduction in speed and ensures stable speed control.
Additionally, DC shunt motors have excellent starting torque, allowing them to start efficiently even under high loads. This is due to the high torque generated by connecting the armature and field windings in parallel. Additionally, these motors offer a wide range of speed control, allowing precise adjustments to specific application requirements. Overall, the distinctive features of DC shunt motors, including their stable speed control, high starting torque, and versatile speed control, make them the preferred choice for numerous industrial and commercial applications.