
This article examines the conditions necessary to achieve maximum efficiency in DC machines. We will examine the fundamental principles and factors that influence the efficiency of these machines and discuss various techniques and strategies used to achieve maximum efficiency. By understanding these important considerations, engineers and designers can make informed decisions and take steps to optimize the performance of DC machines in their specific applications. The importance of maximum efficiency in DC machines is understood.
Factors affecting efficiency
The main factors that affect the efficiency of a DC machine, including copper and iron losses, are as follows:
Copper losses
Copper losses arise from the resistance of the copper windings in the armature and field coils. These losses lead to the dissipation of electrical energy in the form of heat. Minimizing copper losses can be achieved by using low resistance materials and ensuring proper winding design and construction.
Iron losses
Iron losses, also known as core losses, arise from the magnetization and demagnetization of the machine's iron core. These losses consist of hysteresis and eddy current losses. Reducing iron losses can be achieved by using high-quality laminated iron cores and optimizing the core design.
Mechanical losses
Mechanical losses in DC machines are associated with friction and air losses. Friction losses arise from the movement of mechanical parts such as bearings, brushes and gears. Air losses, on the other hand, arise from the resistance to which the rotating parts are exposed in the surrounding air. Reducing mechanical losses includes using efficient bearings, minimizing brush friction, and using aerodynamic designs.
Voltage and current levels
The voltage and current at which a DC machine operates directly affect its efficiency. Using the machine at the voltage and current ratings specified by the manufacturer can help ensure optimal efficiency. Deviations from these values can lead to increased losses and reduced efficiency.
Temperature and cooling
Temperature has a significant impact on the efficiency of DC machines. Excessive heat can increase resistance and lead to greater losses, negatively impacting efficiency. Implementing effective cooling mechanisms, such as fans, heat sinks, or liquid cooling, can help maintain optimal operating temperatures and improve efficiency.
load and speed
The load and speed of a DC machine also affect its efficiency. Different constraints and speeds require different levels of electrical and mechanical energy, which affects the overall efficiency of the machine. Through appropriate load management, speed control mechanisms, and system design considerations, you can optimize efficiency under a variety of operating conditions.
Compensation for losses of copper and iron
It is important to find the right balance between copper losses due to resistance in the winding wires and iron losses due to hysteresis and eddy currents in the core material. Balancing copper and iron losses requires a comprehensive approach that takes into account the electrical, magnetic and thermal aspects of the DC machine. Engineers can minimize and compensate for copper and iron losses by selecting appropriate materials, optimizing winding and core designs, and implementing efficient cooling mechanisms. This balance is key to maximizing the efficiency and overall performance of DC machines, ensuring optimal power conversion and reduced operating costs.
Optimal operating point
It highlights the importance of selecting the ideal operating point with maximum efficiency, taking into account parameters such as load torque, speed and armature resistance.
The ideal operating point of a DC machine refers to the specific load, voltage, and current conditions under which it achieves maximum efficiency and performance. Operating a DC machine at its sweet spot ensures optimal power conversion, lower losses, and greater overall system efficiency. This section examines key considerations for determining and achieving the optimal operating point of DC machines.
Efficiency-load ratio
The efficiency of a DC machine depends on the load under which it is operated. In general, efficiency increases as the load approaches the rated load and reaches a maximum at a certain point. Operating the machine at this point minimizes electrical and mechanical losses, resulting in the highest efficiency.
Voltage and current levels
The voltage and current at which a DC machine operates have a significant impact on its efficiency. Deviations from manufacturer-specified voltage and current ratings may result in increased losses and reduced efficiency. Operating the machine within the recommended voltage and current ranges ensures optimal performance and efficiency.
Load management
Efficient load management is essential for optimal operation of a DC machine. Matching the load to machine capabilities and design specifications can prevent excessive losses and ensure equipment operates within its efficiency range. Appropriate load balancing and control techniques, such as: B. the use of appropriate gears or control algorithms optimizes load distribution and improves overall system efficiency.
System design and control
DC machine system design and control must take into consideration factors such as intended application, operating conditions, and desired performance. Proper system design, including component selection, conductor sizing, and implementation of control algorithms, ensures that the machine performs optimally in various operating scenarios.
Thermal management
Effective thermal management is critical to maintaining optimal operating point. Appropriate cooling mechanisms, such as fans, heat sinks or liquid cooling, help dissipate heat generated during operation, prevent excessive temperature rise and ensure optimal machine performance and efficiency.
Benefits of maximum efficiency
Discuss the benefits of operating a DC machine at maximum efficiency, including less wasted energy, lower operating costs, longer life, and minimized risk of overheating or damage.
Maximizing the efficiency of DC machines offers several important benefits, from improved performance and cost savings to environmental sustainability. By operating DC machines at maximum efficiency, several benefits can be achieved. This section examines two main benefits of achieving maximum efficiency in DC machines.
Better power conversion and performance
Efficient operation of a direct current machine ensures optimal conversion of electrical to mechanical energy. This means that a higher percentage of the electrical energy supplied is used effectively to perform useful work, such as driving a load or operating a system.
Cost savings and economic benefits
Maximum efficiency in DC machines can result in significant cost savings and economic benefits for users and operators. These benefits include:
Reduced operating costs
Operating a DC machine at maximum efficiency means lower energy consumption and therefore lower operating costs over the life of the machine. This is particularly important for applications with high energy requirements, such as: B. industrial processes and large infrastructures.
Better return on investment (ROI)
Through maximum efficiency, DC machines offer a greater return on investment. Lower energy consumption and reduced operating costs result in a shorter payback period, allowing users to more quickly recover their initial investment in the machine.
Environmental sustainability
Achieving maximum efficiency with DC machines is consistent with the goals of ecological sustainability and resource conservation. Lower energy consumption reduces greenhouse gas emissions, creates a cleaner environment and helps combat climate change. Additionally, it supports regulatory compliance and sustainability initiatives.
Competitive advantage
Companies that use DC machines with maximum efficiency gain a competitive advantage in the market. Energy-efficient technologies are increasingly sought after by customers, regulators and investors, improving the company's reputation and market position.
Analyze and optimize operating conditions
Emphasis is placed on the importance of careful analysis and optimization of operating conditions to ensure that the DC machine operates as efficiently as possible.
This summarized the importance of achieving maximum efficiency in DC machines and the associated benefits in terms of performance, energy savings and cost reduction.
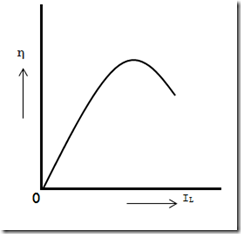
Now;
Efficiency η = output/input