Most pneumatic and hydraulic systems use a flow-controlled valve to control the direction, speed and pressure of air and hydraulic lines.
There are many different types of valves that can be used for this type of control, and each valve has its own specific purpose.
Based on their design or installation, valves are divided into:
- directly through
- square
- triple
Some types of valves can regulate flow while allowing it to flow through another section, while other types are designed to simply allow, stop, or change the direction of flow.
A traditional flow control valve has a variable orifice that can be closed to decrease flow or open to increase flow.
The flow control valve has technically advanced functionality compared to conventional control valves, but both allow pressure and flow regulation.
Flow control valve – what exactly is it used for?
Flow control valves are used in pneumatics mainly to regulate pressure or flow, for example of oil in hydraulics. As part of a pneumatic circuit, the function of flow control valves is to reduce the flow rate in a given section, which results in a slower drive speed: actuator, spool, etc.
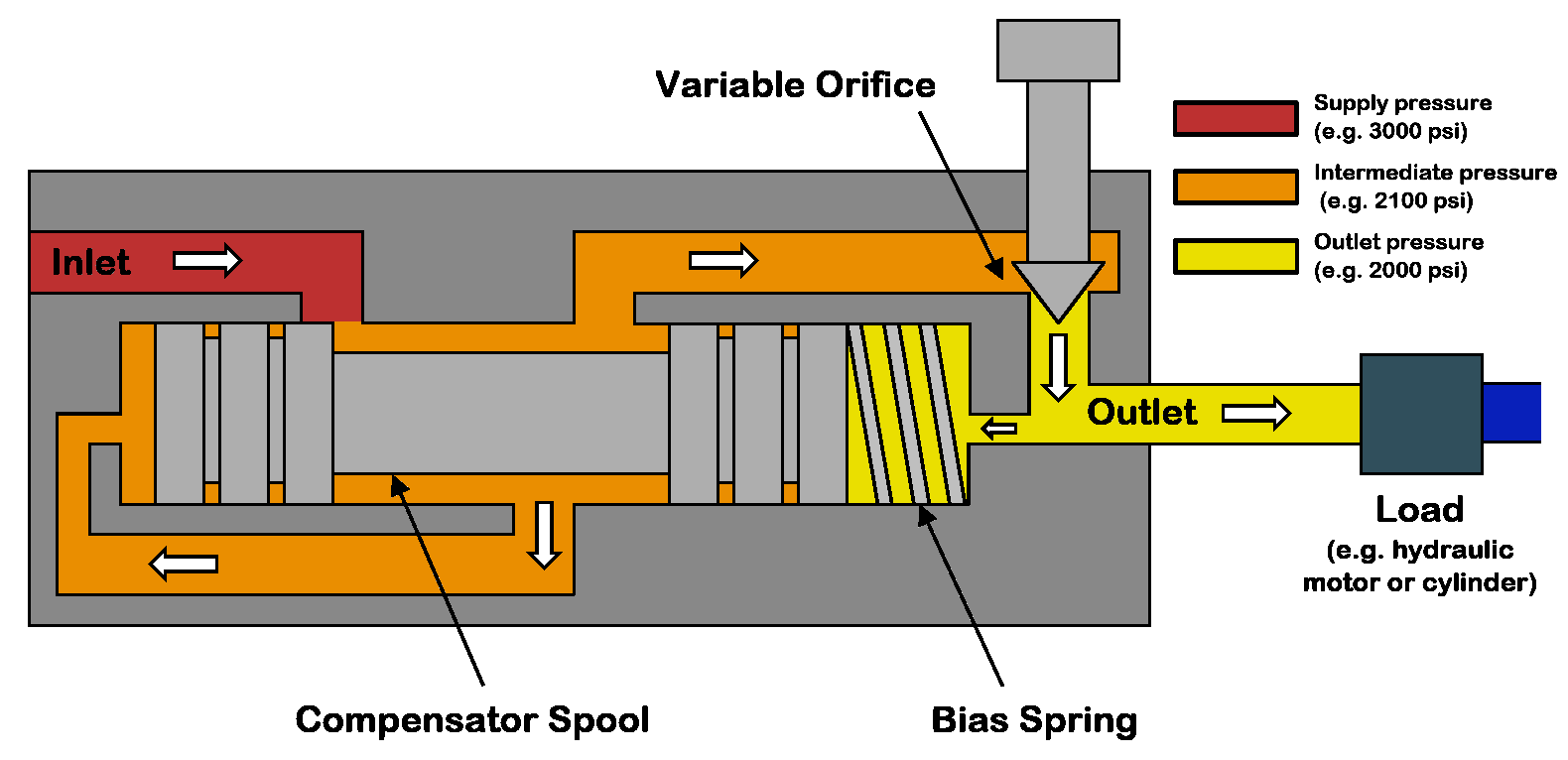
It is designed to allow air to flow in one direction, which in turn allows it to flow freely in the opposite direction.
However, there are different types of flow control valves, each of which can serve different purposes depending on the purpose of the machine or system.
How does a flow control valve work?
Flow in valves is directly proportional to speed and pressure is directly proportional to force. By increasing the flow to the actuator, you increase its speed.
By increasing the available pressure, you increase the available force.
Flow changes the speed or power of the actuator, pressure changes its force, and the position of the valve changes the direction of action.
In short, flow control valves change the flow before and after them.
The flow control valve can be installed as a single element of the system or can work in conjunction with another control valve that drives the flow cycle, such as a 2/2,5/2 solenoid valve or similar manual valve.
If you have a flow control valve, you will find that it smoothly and arbitrarily regulates the amount of fluid flowing out and the filling rate of the drive chamber, piping, etc. is regulated as expected.
This is practical when using such valves and represents one of the most economical forms of control in systems.
Flow regulating valve – Various versions
As mentioned earlier, there are different types of flow control valves that have different applications. Depending on whether the flow needs to be regulated, accelerated, reduced, or changed in some way, a different type of control valve is required.
Let's look at a few different types of flow control valves.
Valve with flow regulation – Traditional
Control valves are valves used to regulate conditions such as flow, pressure, temperature, or level of a liquid by fully or partially opening or closing.
Conventional control valves represent the most basic type of valve, and control valve flow control is limited to the “fully open,” “fully closed,” or “fully switched” flow path.
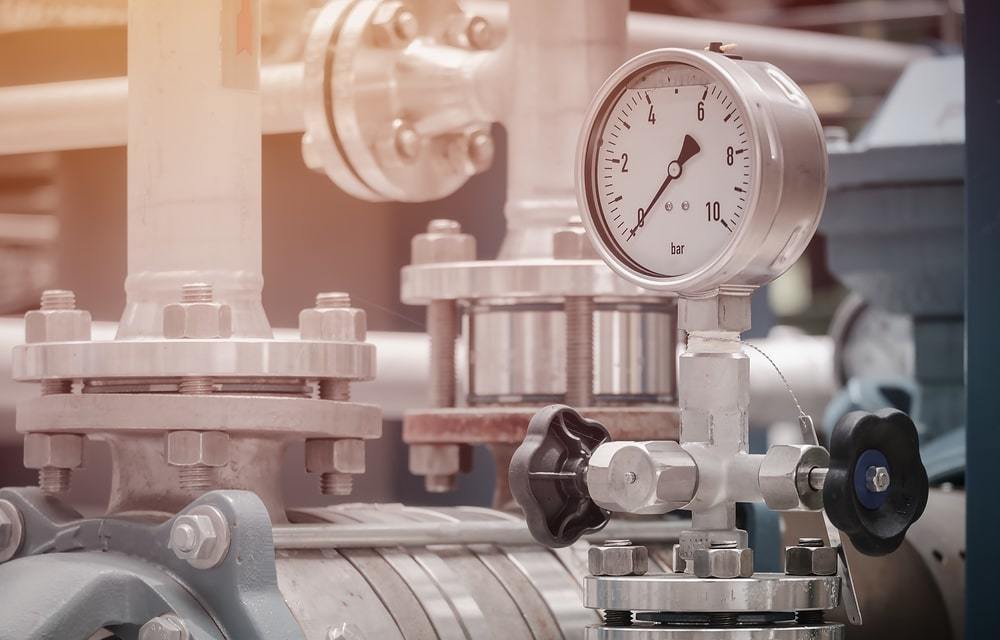
Any desired direction, flow or pressure would require an individual conventional valve to control it.
Directional valves would be an advancement over traditional control valves and would allow media to flow in a variety of ways from one or more sources.
Conventional control valves have a simple design and simple functions.
Needle Control Valves
A flow regulating needle valve is used to regulate the amount of medium flowing into the system by changing the cross section of the through hole until it is completely closed.
They are mainly intended for air installations. Needle valves have a brass needle (cone), hence the name, whose displacement allows continuous adjustment from the maximum open position to the closed position.
The flow direction is marked with an arrow on the valve body. Constant maximum working pressure throughout the entire operating temperature range.
It is possible to work with such valves with non-flammable and non-toxic gases (nitrogen, carbon dioxide, helium, argon, etc.).
One of the biggest disadvantages of the needle valve is that it restricts flow in both directions. When you use a needle valve to regulate the speed of a pneumatic piston in the forward stroke, it also limits the stroke in the reverse stroke.
Ball valves
These valves have a perforated, hollow, rotating ball, which is one of the main components of the valve for flow control.
The ball valve opens when the hole in the ball communicates with the body's flow port and closes when rotated 90 degrees by the valve handle or lever.
These types of control valves are very reliable and durable. They are used in practically all sectors or even in all homes (water, gas installations, etc.). Its advantage is also its low price and easy accessibility.
The name goes back to the previously typical spherical shape of the body, which consists of two body halves separated by an internal partition. They are often used in plumbing.
These types of valves are used in applications that require frequent actuation and throttling.
Ball valves can be flanged, screwed for mounting (large DN diameters) or threaded. Ball valves for welding are a separate group.
Butterfly valves
Butterfly valves are used to regulate, isolate or block flow. Its operating principle is similar to that of a ball valve, in the sense that it was designed to open or close quickly when necessary using an actuator. Large flow diameters = high operating resistance or lever for smaller diameters = low resistance.
Inside the tube is a disc and a rod connected to an actuator that passes through the disc. In butterfly valves, the disc is made of stainless steel and rotates.
There are rubber or plastic seals on the case. In difficult working conditions, the use of rigid seals (e.g. metal) is necessary.