With the development of society, environmental protection has received more and more attention, especially for industries with serious pollution. In recent years, numerous factories have been forced to close due to environmental protection regulations.
Today, we will present some operating principles of dust collectors. In the future we will also present practical cases of using PLC to control various dust collectors in factories. Don't miss out on this valuable information if you need it.
Dust collector classification and dedusting process
1. Dust collector classification
According to the mechanism of action, dust collectors can be divided into four categories: mechanical dust collectors, electrical dust collectors, filter dust collectors and washing dust collectors.
Mechanical dust collectors also include gravity dust collectors, inertial force dust collectors and centrifugal force dust collectors.
According to different installation ways, dust collectors can be divided into vertical and horizontal types.
Depending on the involvement of liquid in the dust removal process, dust collectors can be divided into dry dust collectors without liquid involvement and wet dust collectors with liquid involvement.
2. Main components of dust collector
The components of a dust collector include an inlet for introducing dusty gas, a dust removal space for solid gas separation or a dust removal room, and a dust outlet for removing the separated dust and a relatively gas outlet. clean after dust removal.
3. Dust removal process
(1) Capture separation process
① Capture and transition stage: in essence, it is the dust concentration stage.
The dust, which is evenly mixed or suspended in the conveying medium, enters the dust removal space of the dust collector. Due to the action of external forces, the powder is moved to the separation interface. As the dust moves to the separation interface, its concentration increases, preparing it for solid-gas separation.
② Separation phase:
When high concentration dust flows into the separation interface, there are two mechanisms of action:
First, the capacity of the conveying medium to transport dust gradually reached its limit. In the tendency of dust suspension and sedimentation, sedimentation is mainly used, and the dust is separated from the conveying medium through dust sedimentation.
Secondly, in the high-concentration dust flow, the diffusion and agglomeration tendency of dust particles is mainly agglomeration. The particles may agglomerate among themselves or agglomerate and adsorb at the media interface.
(2) Dust removal process
After passing through the separation interface, the separated powder is discharged through the powder outlet.
(3) Exhaustion process
The relatively purified air stream after dust removal is discharged through the exhaust port.
Common dust collectors and their principles
1. Bag filter
A bag filter is a type of dust removal equipment based on the principle of filtration. It uses organic or inorganic fiber filter cloth to filter gas dust.
The structure of a bag filter for pulsed jet dust cleaning is composed of an upper box, an intermediate box, a lower box and a control valve. The dust-containing gas enters the middle box of the bag-type dust collector through the air inlet and enters the fabric bag from the outside of the bag.
The dust is blocked on the outer surface of the filter bag, and the purified air enters the bag, then enters the upper box through the top of the fabric bag, and finally is discharged through the exhaust pipe.
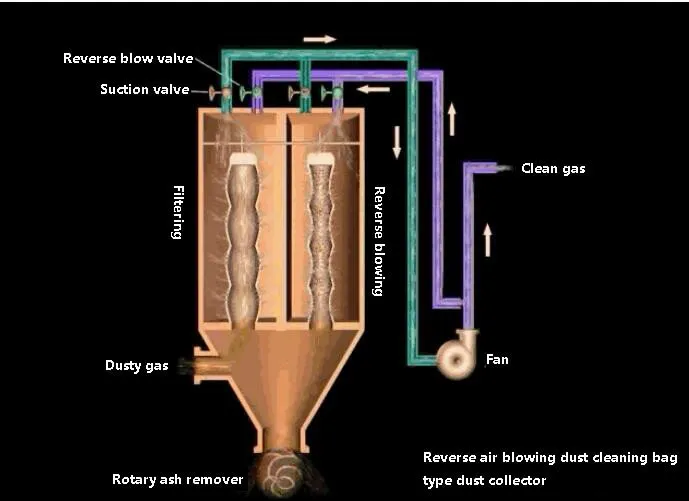
To prevent the filter bag from being sucked in and emptied during filtration, a support structure is placed on the filter bag. The pulse valve controls the pulse to eject high-speed, high-pressure airflow into the filter bag, causing the filter bag to expand and contract sharply, creating shock and vibration.
Part of the dust trapped outside the bag falls into the lower ash bag by gravity, and part of it is blown by the instantaneous airflow from inside to outside and enters the ash hopper. Finally, it is discharged through the dust discharge valve.
This type of dust collector can clean ash without disrupting the air.
It is mainly used to separate particles and fine dust from industrial waste gases and is widely used in industries such as metallurgy, mining, cement, thermal power plants, building materials, smelting, chemical industry, tobacco, asphalt mixers, grain, machining and removal of boiler dust.
2. Electrostatic precipitator
The working principle of an electrostatic precipitator air purifier involves using a high voltage DC electric field to ionize gas molecules in the air, producing a large number of electrons and ions that move to the two poles under the action of electric field strength.
As these charged particles move, they encounter dust particles and bacteria in the air stream and carry them away. The charged particles move to the polar plate with opposite charges under the action of the electric field force. Under the action of the electric field, free ions in the air also move to the two poles.
The greater the voltage and intensity of the electric field, the faster the speed of movement of the ions.
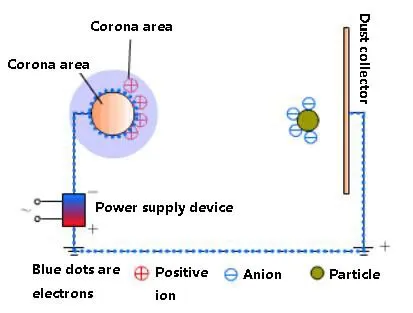
Advantages of electrostatic precipitator:
① High separation efficiency, which can effectively remove particles;
② Large amount of treated gas and low resistance;
③ Suitable for corrosive and high temperature gases;
④ Low operation cost.
Disadvantages:
① High investment cost, huge equipment and large usable area;
② High requirements for equipment manufacturing, installation and maintenance;
③ It is sensitive to the characteristics of dust.
1) Basic types of electrostatic precipitators
An electrostatic precipitator consists of a precipitating body and a feeding device.
The dust collector body includes a discharge electrode, a dust collection electrode, an airflow distribution device, an ash cleaning mechanism, an isolation device, a housing and other parts.
① Single-zone (stage) electrostatic precipitator
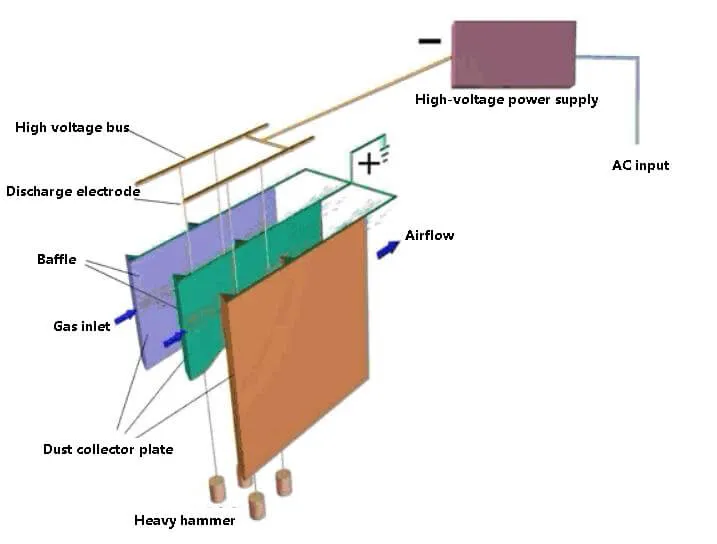
In a single-zone dust collector, the particle charging and dust collection processes are carried out in the same area, which means that the corona electrode and the dust collector are in the same area.
② Dual-zone (stage) electrostatic precipitator
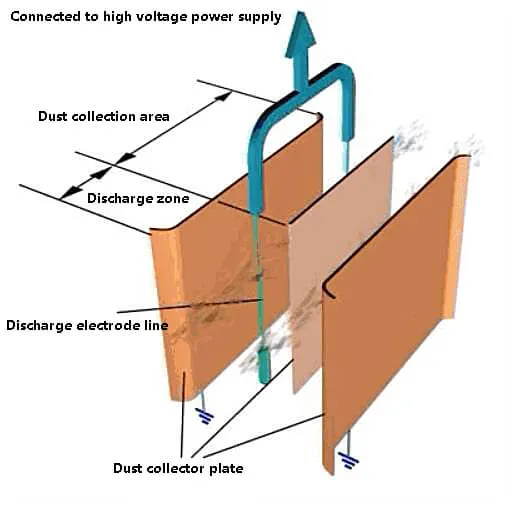
In a dual-zone electrostatic precipitator, particle loading and settled dust collection are carried out in two separate areas.
A group of electrodes is installed in the first area to charge the dust particles, and another group of electrodes is installed in the second area to settle and collect the dust particles.
It is mainly used in air conditioning systems.
3. Mechanical dust collector
Mechanical precipitator is a device that uses mechanical force, including gravity, inertial force and centrifugal force, to separate dust particles from gas.
This type of dust collector mainly includes gravity dust collector, inertial dust collector and cyclone dust collector.
The mechanical dust removal device is characterized by its simple structure, low cost, convenient use and maintenance, and the ability to handle gases with high particle concentration and large gas volume. It can also adapt to high temperature flue gas treatment.
However, it is generally used for multi-stage dust removal or applications where high dust removal efficiency is not required.
1. Gravity dedusting chamber
It is also known as a gravity sedimentation chamber.
It is a dust removal equipment that uses the difference in density between dust particles and gas to allow dust particles to settle and separate naturally from the air flow by the action of gravity.
This is the simplest type of dust removal equipment.
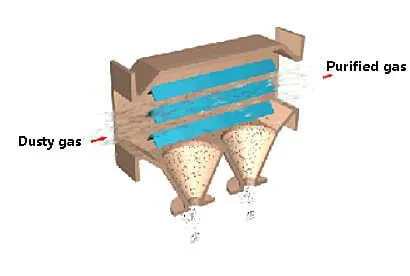
2. Inertial precipitator
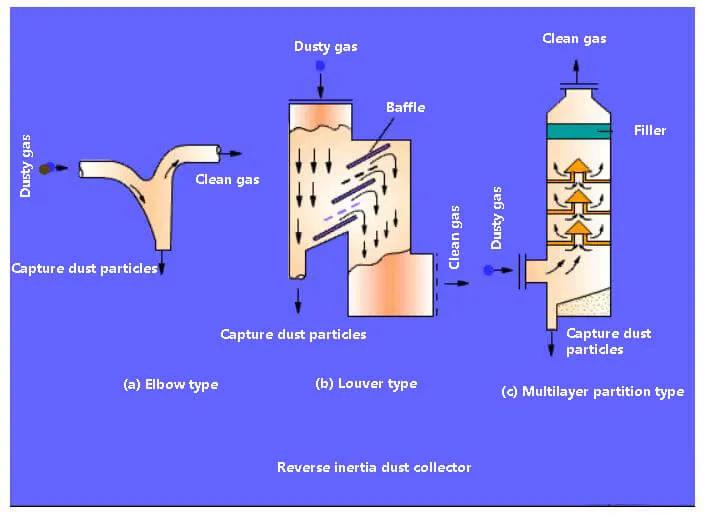
Main features:
The device has a simple structure and low resistance.
Compared to a gravity sedimentation chamber, its dust removal efficiency is higher, but it still falls into the low-efficiency dust collector category. It is generally used for primary dust removal or as dust removal from the front stage of a high-efficiency dust collector.
This equipment is suitable for capturing metallic or mineral dust with particle size greater than 10~20µm. However, it is not suitable for cohesive and fibrous dust as it is prone to clogging.
4. Wet dust collector
Due to the explosive nature of dust, there has been an increasing focus on the potential dangers it poses.
As a result, the use of wet dust collectors has also become more prevalent.
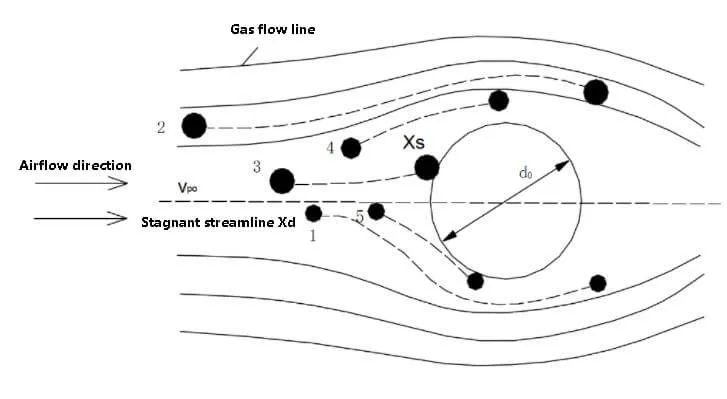
The fundamental principle behind all wet dust collectors is to facilitate contact and combination of droplets with relatively small dust particles, thus producing larger particles that are easier to capture.
During this process, dust particles increase in size using several methods, including combining larger droplets with dust particles, absorbing water to increase mass or density, and forming and growing condensable particles at lower temperatures. in the dust collector.
Wet dust collectors can be categorized based on their structure as follows:
1. Gravity Spray Wet Dust Remover
Gravity spray washers are known for their simple structure, low resistance and easy operation. However, they have high water consumption, require large equipment and area and have low dust removal efficiency.
Gravity spray wet dust collectors, such as spray washers, fall into this category.
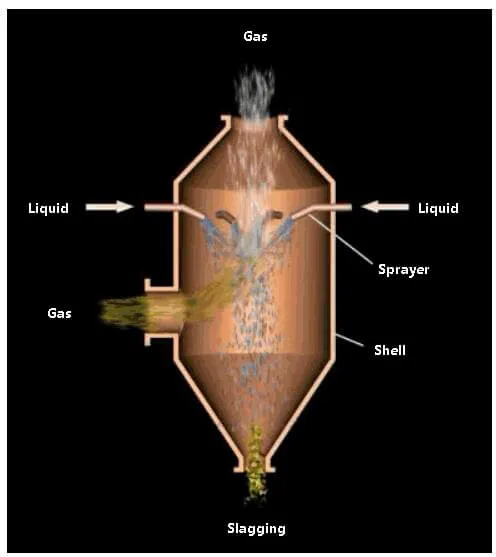
Spray Type Washing Dust Collector
2. Cyclone wet dust collector
The cyclone purifier is suitable for removing dust particles larger than 5μm. For submicron dust purification, it is often connected in series behind a Venturi scrubber to function as a condensed water droplet dehydrator. The cyclone can also be used to absorb certain gaseous pollutants.
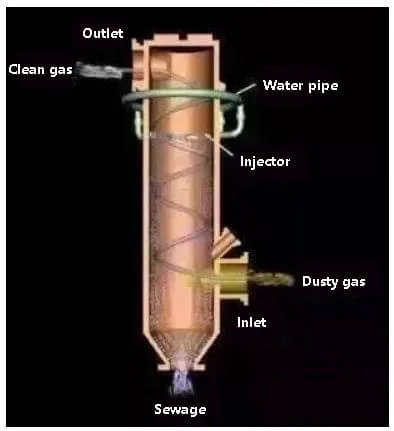
Vertical Cyclone Water Film Dust Collector
3. Self-excited wet dust collector
Self-excited dust collectors have the advantages of compact structure, small size, ease of construction and installation, good load adaptability and low water consumption.
However, they are relatively expensive and can have high pressure losses.
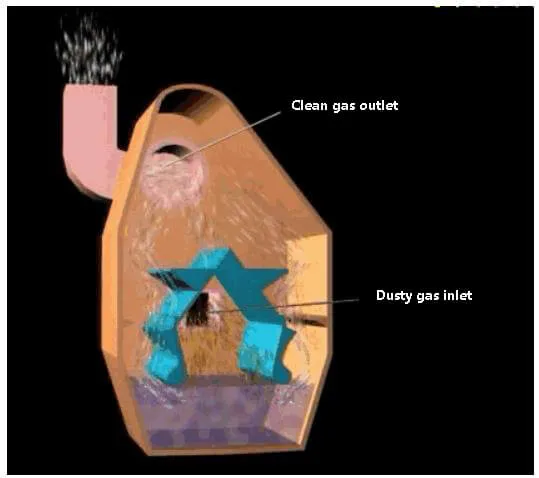
Self-excited wet dust collector
4. Packaging type wet dust collector
Compacted wet dust collector such as compacted tower and turbulent ball tower.
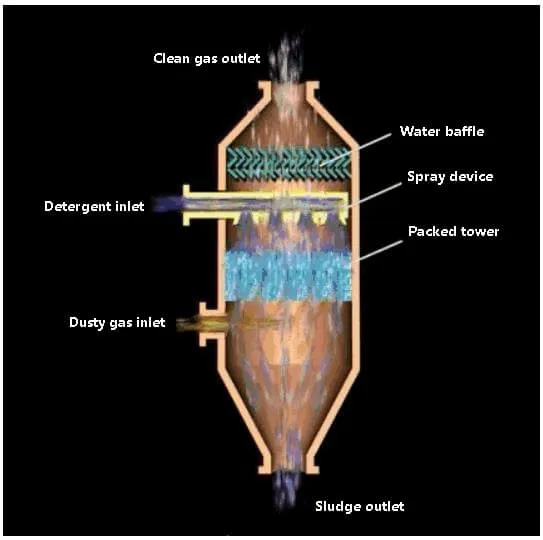
packed tower
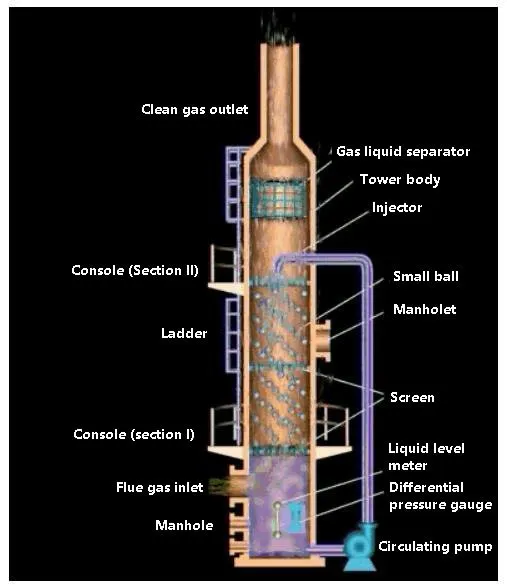
Turbulent Ball Tower
5. Foam Wet Dust Remover
Foam wet dust remover such as foam precipitator and cyclone dust collector.
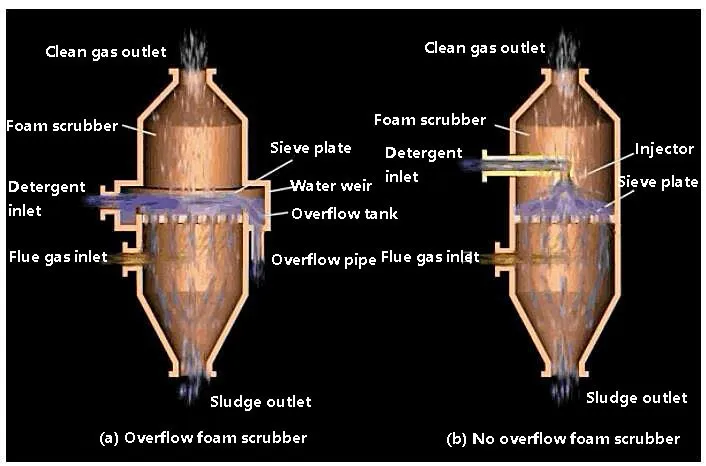
Foam Washing Dust Remover
6. Venturi wet dust collector
Venturi purifier is known for its high fine dust removal efficiency and its ability to cool gases at high temperature.
As a result, it is often employed for cooling and dust removal from high-temperature flue gases, such as those generated by iron-producing blast furnaces and steel-producing electric furnaces. It is also used for the purification of various furnace combustion gases in non-ferrous smelting and chemical production.
Venturi purifier has the advantages of simple structure, small size, flexible layout, low investment cost, but may result in large pressure loss.

Venturi Purifier