The theoretical weight of bolts, including those with and without nuts, can be calculated using a segmented approach.
Theoretical Screw Weight Table
Specification (Diameter × Length) |
Weight per Thousand Screws (Kg) | Specification (Diameter × Length) | Weight per thousand screws (kilograms) | ||
Nut Free | With Walnut | Nut Free | With Walnut | ||
M10×30 | 29 | 40 | M14×80 | 117 | 142 |
M10×40 | 35 | 46 | M14×90 | 129 | 154 |
M10×50 | 41 | 52 | M16×40 | 92 | 126 |
M10×60 | 47 | 58 | M16×50 | 106 | 140 |
M12×30 | 41 | 57 | M16×60 | 122 | 156 |
M12×40 | 49 | 65 | M16×70 | 138 | 172 |
M12×50 | 58 | 74 | M16×80 | 154 | 188 |
M12×60 | 67 | 83 | M16×90 | 170 | 204 |
M12×70 | 76 | 92 | M16×100 | 185 | 219 |
M12×80 | 85 | 101 | M20×50 | 183 | 245 |
M14×40 | 69 | 94 | M20×60 | 205 | 267 |
M14×50 | 81 | 106 | M20×70 | 230 | 292 |
M14×60 | 93 | 118 | M20×80 | 255 | 317 |
M14×70 | 105 | 130 | M20×90 | 279 | 341 |
M20×100 | 304 | 366 | M22×160 | 548 | 624 |
M20×110 | 329 | 391 | M24×80 | 388 | 500 |
M20×120 | 354 | 416 | M24×90 | 424 | 536 |
M20×130 | 378 | 440 | M24×100 | 459 | 571 |
M22×60 | 250 | 326 | M24×110 | 495 | 607 |
M22×70 | 280 | 356 | M24×120 | 531 | 643 |
M22×80 | 310 | 386 | M24×130 | 566 | 678 |
M22×90 | 339 | 415 | M24×140 | 602 | 714 |
M22×100 | 369 | 445 | M24×150 | 637 | 749 |
M22×110 | 399 | 475 | M24×160 | 673 | 785 |
M22×120 | 429 | 505 | M27×80 | 519 | 687 |
M22×130 | 459 | 535 | M27×90 | 564 | 732 |
M22×140 | 489 | 565 | M27×100 | 609 | 777 |
M22×150 | 519 | 595 | M27×110 | 654 | 822 |
M27×120 | 699 | 867 | M30×170 | 1154 | 1388 |
M27×130 | 744 | 912 | M30×180 | 1210 | 1444 |
M27×140 | 789 | 957 | M30×190 | 1266 | 1500 |
M27×150 | 834 | 1002 | M30×200 | 1322 | 1556 |
M27×160 | 879 | 1047 | M30×210 | 1378 | 1612 |
M27×170 | 924 | 1092 | M30×220 | 1434 | 1868 |
M27×180 | 969 | 1137 | M36×110 | 1246 | 1617 |
M30×100 | 765 | 999 | M36×120 | 1326 | 1697 |
M30×110 | 820 | 1054 | M36×130 | 1406 | 1777 |
M30×120 | 875 | 1109 | M36×140 | 1486 | 1857 |
M30×130 | 931 | 1165 | M36×150 | 1566 | 1937 |
M30×140 | 986 | 1220 | M36×160 | 1646 | 2017 |
M30×150 | 1042 | 1276 | M36×170 | 1726 | 2097 |
M30×160 | 1098 | 1332 | M36×180 | 1806 | 2177 |
M36×190 | 1886 | 2257 | M42×230 | 3095 | 3694 |
M36×200 | 1966 | 2337 | M42×240 | 3204 | 3803 |
M36×210 | 2046 | 2417 | M42×250 | 3313 | 3912 |
M36×220 | 2126 | 2497 | M48×150 | 3005 | 3962 |
M36×230 | 2206 | 2577 | M48×160 | 3147 | 4104 |
M36×240 | 2286 | 2657 | M48×170 | 3289 | 4246 |
M42×150 | 2223 | 2822 | M48×180 | 3431 | 4388 |
M42×160 | 2332 | 2931 | M48×190 | 3573 | 4530 |
M42×170 | 2441 | 3040 | M48×200 | 3715 | 4672 |
M42×180 | 2550 | 3149 | M48×210 | 3857 | 4814 |
M42×190 | 2659 | 3258 | M48×220 | 3999 | 4956 |
M42×200 | 2768 | 3367 | M48×230 | 4141 | 5098 |
M42×210 | 2877 | 3476 | M48×240 | 4283 | 5240 |
M42×220 | 2986 | 3585 | M48×250 | 4432 | 5389 |
M48×260 | 4574 | 5531 | M48×280 | 4858 | 5815 |
M48×300 | 5142 | 6099 |
How to determine the strength grades of screws
Common screws are divided into Grade A, Grade B (refined screws) and Grade C (raw screws).
Grade A and B screws use grade 5.6 and 8.8 steel, while grade C screws use grade 4.6 and 4.8 steel. High strength screws are made from grade 8.8 and 10.9 steel. In Grade 10.9, for example, 10 indicates that the tensile strength of the steel material is fu=1000N/mm² and 0.9 indicates that the yield strength of the steel material is fy=0.9fu. Other models follow this convention. Anchor bolts use Q235 or Q345 steel.
Grade A and B screws (refined screws) are made from shaped billets. The surface of the screw shank is smooth, the dimensions are accurate, and the screw holes are drilled using a die or first drilled into individual parts with a smaller hole and then drilled again to the designed diameter on the assembled components (known as Class I holes). The gap between the screw diameter and the hole is very small, only allowing about 0.3mm, requiring gentle hammering during installation for shear and tensile strength.
However, manufacturing and installing grade A and B screws (refined screws) are labor-intensive and expensive. In steel structures, they are only used at important installation nodes or in bolted connections that support shear and tensile loads from dynamic forces.
Grade C screws (raw screws) are made by pressing round steel. Its surface is rougher and the dimensions are less precise. Screw holes are drilled in one go or without a die (Class II holes), and the hole diameter is 1-2 mm larger than the screw diameter. This results in significant shear deformation under shear forces, and individual bolts can contact the hole wall and experience excessive internal forces, leading to early failure.
Due to the simplicity and lower manufacturing cost of Grade C bolts (raw bolts), they are commonly used in various steel structure projects, especially suitable for connections that bear tensile forces along the bolt axis, detachable connections and temporary fixing components.
In connections with significant shear forces, brackets or other structural measures are used to support the shear forces, allowing the bolt to utilize its tensile strength advantages.
Grade C bolts can also be used in secondary connections subject to static or indirect dynamic loads such as shear connections.
High strength stainless steel screws
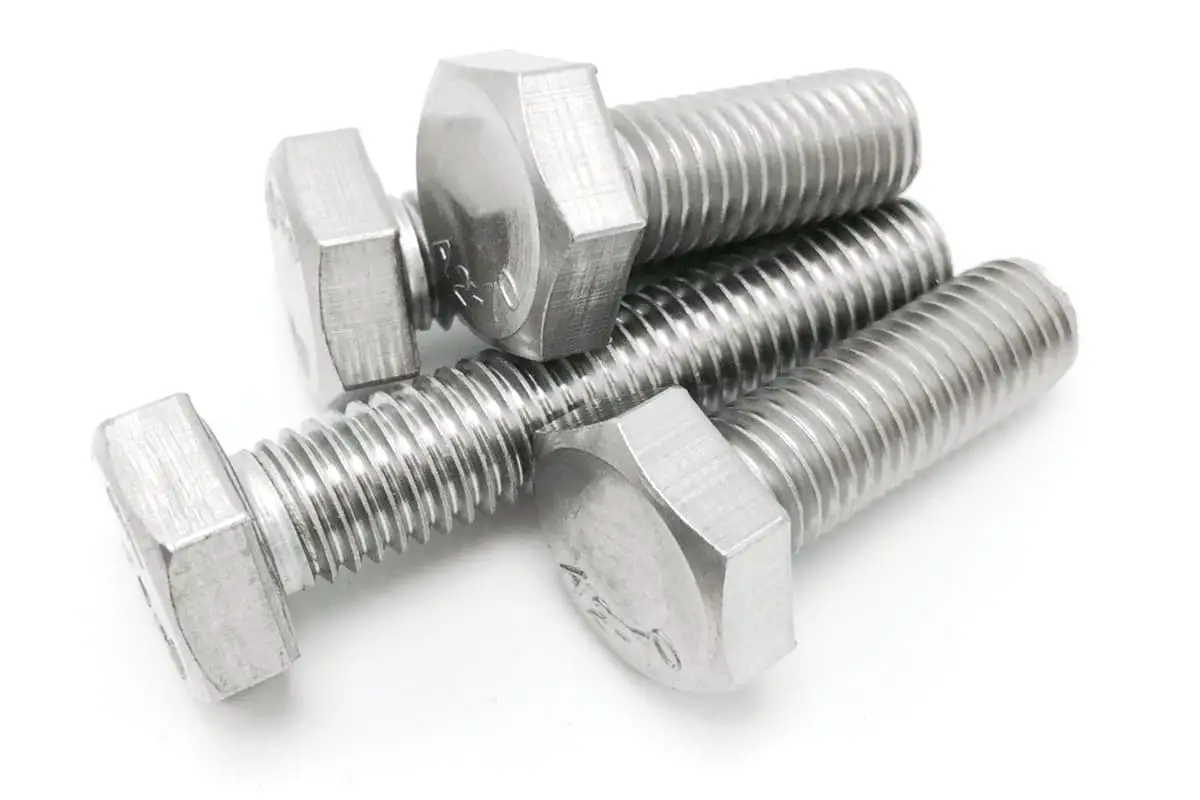
High-strength stainless steel screws have high strength and resistance to corrosion by air, steam, water and other weak corrosive media, as well as acids, alkalis and salts. They do not corrode, corrode, rust or wear.
Stainless steel is also among the strongest materials used in construction. Due to its excellent corrosion resistance, it guarantees the permanent integrity of structural components in engineering projects.
The performance grades of steel structure connecting bolts are divided into more than ten grades, including 3.6, 4.6, 4.8, 5.6, 6.8, 8.8, 9.8, 10 .9, 12.9.
Screws of grade 8.8 and above are made of low-carbon alloy steel or medium-carbon steel and undergo heat treatment (quenching, tempering), commonly known as high-strength screws, while the rest are known as common screws.
Bolt performance grade markings consist of two numbers, indicating the nominal tensile strength and yield strength ratio of the bolt material.
High-strength bolts are made from high-strength steel or bolts that require significant pre-tensioning force. They are widely used in bridges, railways, high and ultra-high pressure equipment connections. These screws often fail due to brittle fractures.
High-strength bolts used in ultra-high-pressure equipment need to apply significant pre-tension to ensure the container is sealed.
Some concepts about high strength screws: 1. Screws with performance grades above 8.8 are known as high strength screws. The current national standard only lists up to M39, and for larger sizes, especially lengths greater than 10~15% times the diameter, national production is still limited.
Difference between high strength screws and common screws
High-strength screws differ from ordinary screws in that they can withstand greater loads than standard screws of the same specification. Common screws are made of Q235 (A3) steel. High-strength screws are made of 35# steel or other high-quality materials and undergo heat treatment to increase their strength. The main difference is in the resistance of the material.
From a raw material perspective, high-strength screws are made of high-strength materials. The bolt, nut and washer of a high strength bolt are all made of high strength steel, commonly using 45# steel, 40 boron steel, 20 manganese titanium boron steel, 35CrMoA, etc. Common screws are generally made from Q235 (equivalent to the old A3 steel).
In terms of strength grade, the increasingly used high-strength screws typically come in grades 8.8s and 10.9s, with 10.9 being the most common. Common screws have lower strength grades, generally 4.4, 4.8, 5.6 and 8.8.
Regarding force-bearing characteristics, high-strength bolts apply pretension and transmit external forces through friction. Common screw connections rely on the shear strength of the screw shank and hole wall pressure to transmit shear forces. The pretension generated when tightening the nut is minimal and can be considered negligible.
In contrast, high-strength screws, in addition to the material's high strength, are applied with significant pretension, creating a compressive force between the connected components. This produces substantial friction perpendicular to the screw axis. Pretension, slip resistance coefficient and type of steel material directly affect the load capacity of high strength bolts.
Based on force-bearing characteristics, they are divided into bearing type and friction type. Both types have different calculation methods. The smallest standard for high-strength screws is M12, commonly used sizes range from M16 to M30, and the performance of super-large screws is unstable, requiring careful consideration in design.
The difference between friction type and bearing type connections in high strength bolts:
High-strength bolt connections firmly hold the connected plates through a significant pre-tension force within the bolt shaft, generating substantial friction, thereby improving the overall integrity and rigidity of the connection. When subjected to shear forces, they can be divided into friction-type and bearing-type high-strength bolted connections, differing fundamentally in their limit states.
Although they are the same type of screw, their calculation methods, requirements and application scopes vary significantly. In shear-resistant design, the limit state for friction-type high-strength bolt connections is the maximum possible frictional force provided by the clamping force of the bolts between the contact surfaces of the plates, ensuring that the external shear force does not exceed this maximum friction force during the entire service period.
The plates do not suffer relative deformation due to sliding (maintaining the original gap between the screw axis and the hole), and the connected plates are subject to elastic forces as a whole. In bearing-type high-strength bolt connections, the external shear force may exceed the maximum friction force, causing relative sliding deformation between the connected plates until the bolt shaft contacts the hole wall.
Subsequently, the connection transfers forces through bolt shaft shear, hole wall pressure, and friction between the plate surfaces, with the final shear failure of the connection being bolt shaft shear or bolt wall pressure. hole.
In summary, friction-type and bearing-type high-strength screws are essentially the same screws, differing only in the fact that slip is considered in the design. Friction-type high-strength screws must not slip; they cannot withstand shear forces and any slippage is considered a design flaw, a technically mature approach. High-strength bearing-type bolts can slip and also withstand shear forces, with ultimate failure similar to that of ordinary bolts (either bolt shear or steel plate compression).
In terms of use: For the bolted connections of the main structural components of buildings, high-strength bolts are generally used. Ordinary screws can be reused, while high-strength screws cannot and are typically used for permanent connections.
High strength bolts are prestressed bolts. In friction type applications, a specific pre-tension is applied using a torque wrench, while in rolling type applications, the spline is cut. Common screws, with lower shear resistance, can be used in less critical structural areas and only need to be tightened. Common screws are generally grades 4.4, 4.8, 5.6 and 8.8. High strength screws are generally grades 8.8 and 10.9, with 10.9 being the most prevalent.
Grades 8.8 and 8.8S are equivalent. The strength performance and calculation methods of ordinary bolts differ from those of high-strength bolts. High-strength bolts bear force mainly through the internal pretension force P, creating frictional resistance on the contact surfaces of connected components to support external loads, while ordinary bolts directly support external loads.
More specifically: High-strength bolt connections offer advantages such as simple construction, good force-bearing performance, replaceability, fatigue resistance, and resistance to loosening under dynamic loads, making them a promising connection method.
The high-strength screws are tightened with a special wrench, generating a large and controlled pre-tension. This pretension, transmitted through the nut and washer, creates an equivalent precompression force on the connected components. Under this pre-compressive force, significant friction is generated along the surfaces of the connected components.
As long as the axial force is less than this friction force, the components will not slip and the connection will remain intact. This is the principle behind high strength bolted connections.
High-strength screw connections rely on friction between the mating surfaces of connected components to prevent slippage. To ensure sufficient friction, it is necessary to increase the clamping force between the components and increase the friction coefficient of the contacting surfaces.
The clamping force between the components is obtained by applying pre-tension to the screws, requiring the use of high-strength steel for the screws, hence the term “high-strength screw connections”.
In high-strength bolted connections, the friction coefficient significantly influences the load capacity. Experiments show that the coefficient of friction is mainly affected by the nature of the contact surfaces and the material of the components.
To increase the coefficient of friction of the mating surfaces, construction often involves methods such as sandblasting or metal brushing to treat the mating surfaces within the connection area.
In fact, high-strength screws come in two types: friction type and bearing type. The design criterion for friction-type high-strength bolts is that the shear force induced by the design load does not exceed the friction force. For bearing-type high-strength screws, the criterion is that the screw axis is not sheared or the plates are not crushed.
Corrosion resistance of high strength stainless steel screws
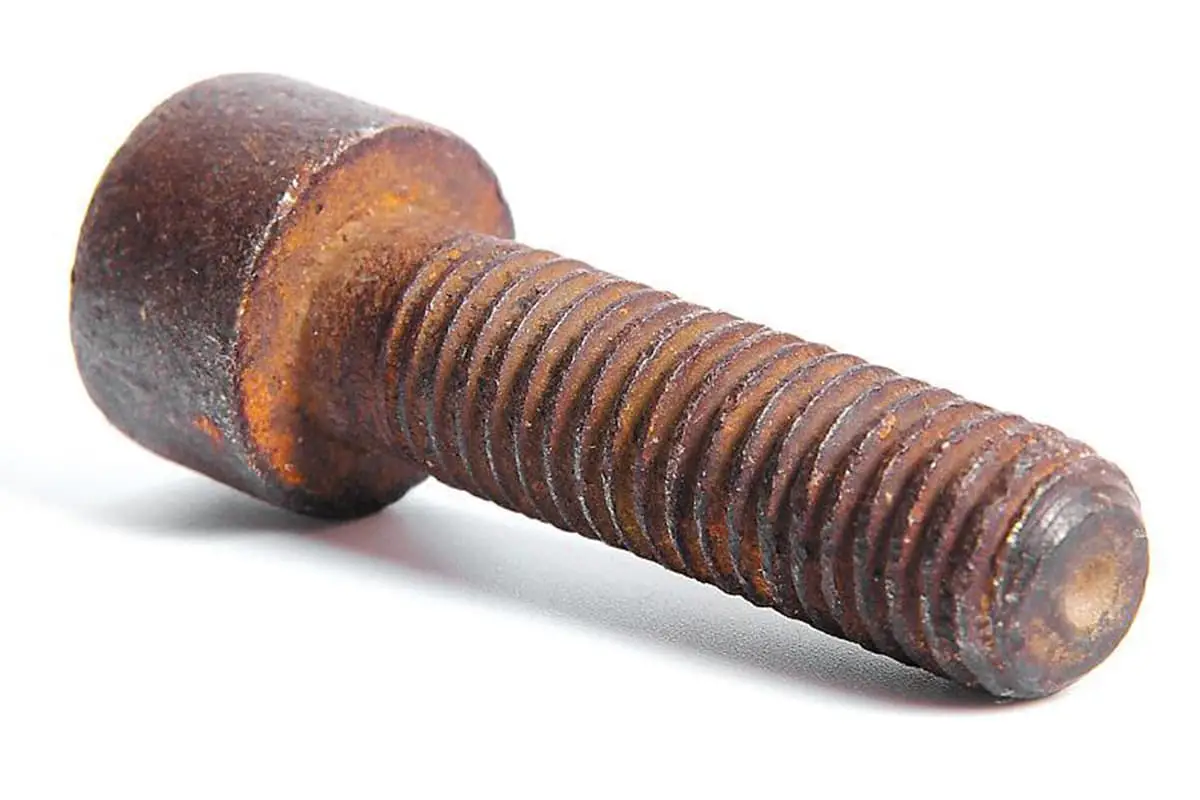
High strength stainless steel screws are known for their corrosion resistance characteristics.
All metals react with oxygen in the atmosphere, forming an oxide film on their surface. Unfortunately, the iron oxide formed in regular carbon steel continues to oxidize, causing the rust to expand and eventually create holes. Carbon steel surfaces can be protected with paint or oxidation-resistant metals (such as zinc, nickel and chromium) through electroplating. However, as is commonly known, this protective layer is just a thin film. If the protective layer is damaged, the underlying steel begins to rust.
The corrosion resistance of stainless steel depends on chromium. However, as chromium is a component of steel, the protection method is different. When the chromium content exceeds 11.7%, the steel's resistance to atmospheric corrosion increases significantly.
Although a higher chromium content can still improve corrosion resistance, the effect is less pronounced. This occurs because alloying steel with chromium changes the type of surface oxide, similar to the oxide formed in pure metallic chromium. This firmly adhering chromium-rich oxide protects the surface from future oxidation. This oxide layer is extremely thin, allowing the steel's natural luster to shine through, giving stainless steel its distinctive appearance.
Furthermore, if the surface layer is damaged, the exposed steel surface will react with the atmosphere to repair itself, reforming this “passive” oxide film and continuing its protective role. Therefore, all stainless steel elements share a common characteristic: their chromium content is greater than 10.5%.
The meaning of bolt and nut performance classes
The performance grades of bolts and nuts for steel structure connections are divided into more than ten levels, including 3.6, 4.6, 4.8, 5.6, 6.8, 8.8, 9.8 , 10.9, 12.9.
Grade 8.8 and higher bolts are made of low-carbon alloy steel or medium-carbon steel and undergo heat treatment (quenching and tempering), commonly known as high-strength bolts. The rest are generally called common screws.
The performance grade of a bolt is indicated by two numbers, indicating the nominal tensile strength and the yield strength ratio of the bolt material. For example:
For a grade 4.6 screw:
- The nominal tensile strength of the screw material is 400 MPa;
- The yield strength ratio of the screw material is 0.6;
- The nominal yield strength of the screw material is 400 × 0.6 = 240 MPa.
For a grade 10.9 high strength screw, after heat treatment, it can achieve:
- Nominal tensile strength of 1000 MPa;
- A yield strength ratio of 0.9;
- A nominal yield strength of 1000 × 0.9 = 900 MPa.
The importance of the screw's performance grade is an internationally standardized criterion. Screws of the same performance grade, regardless of their material and origin, have the same performance and in design it is sufficient to select solely based on the performance grade.
Strength grades, such as 8.8 and 10.9, refer to the bolt's resistance to shear stress, measured at 8.8 GPa and 10.9 GPa, respectively.
- Grade 8.8 has a nominal tensile strength of 800 N/mm² and a nominal yield strength of 640 N/mm².
- Generally, screws are indicated by “XY”, where X 100 is equal to the tensile strength of the screw in MPa and X 100*(Y/10) is equal to the yield strength of the screw (since by designation: yield /tensile strength = Y/10).
For example, a grade 4.8 screw:
- It has a tensile strength of 400 MPa;
- And a yield strength of 400*8/10 = 320 MPa.
In addition, stainless steel screws are often marked as A4-70, A2-70, etc. with a different meaning.
Regarding units of measurement: The world mainly uses two systems to measure length. One of them is the metric system, which uses meters (m), centimeters (cm), millimeters (mm), etc., widely used in Europe, China, Japan and other regions of Southeast Asia. The other is the imperial system, which uses inches, equivalent to the old Chinese market inch, used predominantly in the United States, the United Kingdom and other Western countries.
- Metric measurement: (decimal system) 1 meter = 100 centimeters = 1000 millimeters
- Imperial measurement: (octal system) 1 inch = 8 fractions of an inch; 1 inch = 25.4mm; 3/8 inch × 25.4 = 9.52 mm
- For products below 1/4 inch, sizes are indicated by measurement numbers, such as: #4, #5, #6, #7, #8, #10, #12.
Thread types and characteristics
Topic types
Threads are a form of helical structure found on the outer or inner surface of a solid, characterized by a uniform helical ridge. Based on their structural characteristics and applications, they are categorized into three main types:
- Common threads : They have a triangular tooth shape and are used to connect or fix components. Common threads are divided into coarse and fine threads, with fine threads offering greater connection strength.
- Transmission Threads : These threads have various tooth shapes including trapezoidal, rectangular, sawtooth and triangular.
- Sealing threads : Used to seal connections, main types include pipe threads, tapered threads and tapered pipe threads.
Line Fit Classes
Thread fit refers to how loosely or tightly the threads fit together. The degree of fit is determined by the combination of deviations and tolerances applied to the internal and external threads.
(1) Unified thread pattern:
External threads have three grades: 1A, 2A and 3A. Internal threads have three grades: 1B, 2B and 3B. These are all loose fits, with higher note numbers indicating tighter fits.
On unified threads, runouts are specified only for grades 1A and 2A. Grade 3A has zero deviation and the deviations of grades 1A and 2A are equal. The higher the note number, the lower the tolerance.
- Classes 1A and 1B represent very weak tolerance levels suitable for loose fits on internal and external threads.
- Classes 2A and 2B are the most commonly used thread tolerance levels for Unified series mechanical fasteners.
- Classes 3A and 3B provide the tightest fit suitable for fasteners with tight tolerances used in safety critical projects.
- For external threads, classes 1A and 2A have a fit tolerance, while 3A does not. The tolerance of 1A is 50% greater than 2A and 75% greater than 3A. For internal threads, the tolerance of 2B is 30% greater than 2A, 1B is 50% greater than 2B, and 75% greater than 3B.
(2) Metric Threads:
The external threads have three grades: 4h, 6h and 6g. Internal threads have three grades: 5H, 6H and 7H. (Japanese standard thread accuracy grades are divided into levels I, II and III, with II being the most common). In metric threads, the basic deviation for H and h is zero. The basic deviation for G is positive and for e, f and g is negative.
- H is the commonly used tolerance position for internal threads, typically used without surface coating or with an extremely thin phosphating layer. The basic deviation from G is for special occasions, such as thicker coatings, and is rarely used.
- g is often used for 6-9um thin coatings. For example, if a product drawing specifies a 6h bolt, the pre-coat thread would use a 6g tolerance band.
- The best thread settings are typically combinations of H/g, H/h or G/h. For precision fasteners such as screws and nuts, a setting of 6H/6g is recommended as standard.
(3) Line marking
- Main geometric parameters of self-tapping and self-drilling threads:
- Major Diameter/Outer Diameter (d1): The diameter of an imaginary cylinder where the crests of the threads coincide. It essentially represents the nominal diameter of the thread.
- Minor Diameter/Root Diameter (d2): The diameter of an imaginary cylinder where the roots of the wires coincide.
- Pitch (p): The axial distance between corresponding points on adjacent threads along the pitch line. In the imperial system, this is indicated by the number of threads per inch (25.4 mm).
Below are common specifications for pitch (metric) and thread count (imperial):
- Metric self-tapping threads:
Specifications: ST 1.5, ST 1.9, ST 2.2, ST 2.6, ST 2.9, ST 3.3, ST 3.5, ST 3.9, ST 4.2, ST 4.8, ST 5.5, ST 6.3, ST 8.0, ST 9.5
Steps: 0.5, 0.6, 0.8, 0.9, 1.1, 1.3, 1.3, 1.3, 1.4, 1.6, 1.8, 1.8, 2.1, 2.1
- Imperial self-tapping threads:
Specifications: #4, #5, #6, #7, #8, #10, #12, #14
Yarn Counts: AB 24, 20, 20, 19, 18, 16, 14, 14 yarns; One thread 24, 20, 18, 16, 15, 12, 11, 10