Arc welding of galvanized steel
The zinc coating on galvanized steel can present challenges during welding. The main difficulties include:
- Greater sensitivity to cracks and porosity in welding
- Zinc evaporation and soot generation
- Melting and destruction of zinc coating and oxide slag
Of these problems, welding cracks, porosity and slag are the main concerns.
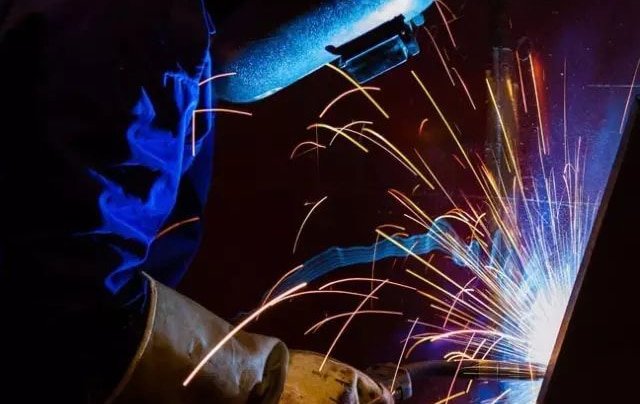
Weldability
(1) The crack
During the welding process, molten zinc can accumulate on the surface of the weld pool or at the base of the weld. The lower melting point of zinc compared to iron causes the iron in the molten pool to solidify first, allowing liquid zinc to penetrate it along the grain boundaries of the steel, leading to a decrease in intercrystalline bond strength .
Furthermore, the formation of brittle metallic compounds, such as Fe3Zn10 and FeZn10, between zinc and iron further reduces the plasticity of the weld metal. This makes it prone to cracking along the crystal boundaries due to welding residual stress.
1) Factors that affect sensitivity to crack
① Zinc coating thickness: The thickness of the zinc coating on galvanized steel affects its sensitivity to cracking. A thin zinc coating results in less crack sensitivity, while a thicker coating on hot-dip galvanized steel leads to greater crack sensitivity.
② Part thickness: Part thickness also influences crack sensitivity, with thicker parts having higher welding restraint stress and greater crack sensitivity.
③ Groove clearance: Larger groove clearance increases crack sensitivity.
④ Welding method: Different welding methods can also affect crack sensitivity. Manual arc welding results in less crack sensitivity, while using CO2 gas for welding can cause greater crack sensitivity.
2) Methods to prevent cracking
① Preparation for welding: Before welding, it is necessary to create a V, Y or X-shaped groove at the welding location on the galvanized sheet. The zinc coating can be removed near the groove with oxyacetylene or sandblasting. It is important not to have too much clearance, with the general recommendation being 1.5mm.
② Selection of soldering materials: To reduce the likelihood of cracking, it is important to choose soldering materials with low silicon content. For gas shielded welding, a welding wire with a low silicon content must be used. Manual welding can be performed using a titanium-type electrode or a titanium-calcium electrode.
(2) Stoma
The zinc layer close to the groove can undergo oxidation (ZnO) and vaporization due to the heat generated during arc welding, leading to the emission of white smoke and vapor. This can easily result in porosity in the weld. The higher the welding current, the more severe the zinc evaporation and the greater the likelihood of porosity.
Welding with titanium and calcium-titanium electrodes tends to result in lower porosity in the medium current range. On the other hand, both low and high currents during welding with cellulose-type and low-hydrogen welding electrodes can cause porosity.
It is important to control the electrode angle so that it is in the range of 30-70° to reduce the risk of porosity.
(3) Zinc evaporation and soot
The zinc layer near the molten pool during welding oxidizes to ZnO and vaporizes due to the heat of the arc, creating a significant amount of dust. The main component of this dust is ZnO, which can have harmful effects on workers' respiratory systems.
It is important to ensure good ventilation during welding to reduce the risk to workers.
Under the same welding specifications, welding with a titanium oxide electrode generates less dust compared to using a low hydrogen welding electrode, which tends to produce a greater amount of dust.
(4) Oxide slag
When using a low welding current, the ZnO formed during the heating process may become trapped and form ZnO slag. ZnO is stable and has a high melting point of 1800°C. The presence of large ZnO slag blocks can have a significant negative impact on weld plasticity.
However, when using a titanium oxide type electrode, the distribution of ZnO is small and uniform, which has little effect on the plasticity and tensile strength of the weld. On the other hand, when using cellulose or hydrogen electrode, the ZnO in the welding seam is larger and more abundant, resulting in poor welding performance.
Galvanized Steel Welding Process
Galvanized steel can be welded using several techniques, including manual electric arc welding, gas shielded fusion electrode welding, argon arc welding, and resistance welding.
(1) Manual arc welding
1) Weld preparation
To reduce the amount of welding dust and prevent the formation of cracks and porosity during welding, it is necessary to prepare the appropriate slope before welding and remove the zinc layer close to the groove. This removal can be achieved by flame or sandblasting.
It is important to control the groove gap so that it is in the range of 1.5 to 2 mm, and for thicker parts the gap can be increased to 2.5 to 3 mm.
2) Electrode selection
The principle for selecting a welding rod is to ensure that the mechanical properties of the weld metal are as similar as possible to those of the original material. Furthermore, it is important to control the amount of silicon in the welding electrode so that it remains below 0.2%.
Related Reading: How to Choose the Right Welding Rod?
Joints produced with ilmenite, titanium oxide, cellulose, titanium-calcium and low hydrogen welding electrodes can present satisfactory resistance. However, low hydrogen and cellulose electrodes tend to result in slag and porosity in welds, so they are not commonly used.
For mild steel galvanized steel sheets, J421/J422 or J423 welding rods are preferred. For galvanized steel sheets with a resistance level above 500MPa, E5001 or E5003 welding rods must be used. For galvanized steel sheets with strength greater than 600MPa, the recommended welding rods are E6013, E5503 or E5513.
When welding, it is recommended to use a short arc and avoid arc oscillation to minimize the expansion of the fusion zone of the galvanized layer, guarantee the corrosion resistance of the part and reduce the amount of soot generated.
(2) Gas shielded welding with melting electrode
Gas shielded welding, such as welding with CO2 gas or an Ar+CO2 or Ar+O2 mixture, is recommended for welding galvanized steel. The type of shielding gas used can have a significant impact on the Zn content in the weld. The use of pure CO2 or CO2+O2 results in a higher Zn content in the welding seam, while the use of Ar+CO2 or Ar+O2 leads to a lower Zn content. Welding current has minimal effect on the Zn content in the weld, with a slight decrease as the current increases.
Gas shielded welding produces more welding dust compared to manual arc welding, so it is important to pay special attention to exhaust. The size and composition of soot are mainly influenced by current and shielding gas, with a higher current or a greater amount of CO2 or O2 in the gas leading to more soot. The ZnO content in soot also increases, with a maximum content of around 70%.
The molten depth of galvanized steel is greater than that of ungalvanized steel under the same welding specifications. T-joints, lap joints and down welding are more prone to porosity, and welding speed has a significant impact, especially for galvanized steel alloys. In multi-line welding, subsequent welding lines are more sensitive to porosity than previous lines.
The composition of the shielding gas has little effect on the mechanical properties of joints, and pure CO2 is commonly used for welding. The welding parameters for I-shaped butt joints, lap joints and T-joints of galvanized steel plates using CO2 welding are listed in tables 1-3.
Table 1 Specification parameters for CO2 welding of I-shaped galvanized steel plate butt joint
Thickness/mm | Clearance/mm | Welding position | Wire feed speed/mm*s-1 | Arc voltage/V | Welding current/A | Welding speed/mm*s-1 | Observation |
---|---|---|---|---|---|---|---|
1.6 | 0 | Flat welding | 59.2~80.4 | 17~20 | 70~90 | 5.1~7.2 | ER705-3 Welding Wire
Dia. 0.9mm Dry extension 6.4 mm |
Vertical downward welding | 82.5 | 17 | 90 | 5.9 | |||
Horizontal Welding | 50.8 | 18 | 100 | 8.5 | |||
Aerial welding | 50.8~55 | 18~19 | 100~110 | - | |||
3.2 | 0.8~1.5 | Flat welding | 71.9 | 20 | 135 | 5.5 | |
Vertical welding | 71.9 | 20 | 135 | 7.6 | |||
Horizontal Welding | 71.9 | 20 | 135 | 6.8 | |||
Aerial welding | 71.9 | 20 | 135 | 5.5 |
Table 2 Specification parameters for CO2 welding of galvanized steel plate lap joint
Thickness/mm | Welding position | Wire feed speed/mm*s-1 | Arc voltage/V | Welding current/A | Welding speed/mm*s-1 | Observation |
---|---|---|---|---|---|---|
1.6 | Flat welding | 50.8 | 19 | 110 | 5.1~6.8 | ER705-3 welding wire
Dia. 0.9mm Dry extension 6.4 mm |
Horizontal Welding | 50.8 | 19~20 | 100~110 | 5.5~6.8 | ||
Aerial welding | 50.8 | 19~20 | 100~110 | 4.2~5.1 | ||
Vertical welding | 50.8 | 18 | 100 | 5.5~6.8 | ||
3.2 | Flat welding | 67.2 | 19 | 135 | 3.8~4.2 | |
Horizontal Welding | 67.2 | 19 | 135 | 3.8~4.2 | ||
Vertical downward welding | 67.7 | 19 | 135 | 5.1 | ||
Aerial welding | 59.2 | 19 | 135 | 3.4~3.8 |
Table 3 Specification parameters for CO2 welding of T-shaped galvanized steel plate butt joint (angle joint)
Thickness/mm | Welding position | Wire feed speed/mm*s-1 | Arc voltage/V | Welding current/A | Welding speed/mm*s-1 | Observation |
---|---|---|---|---|---|---|
1.6 | Flat welding | 50.8~55 | 18 | 100~110 | - | ER705-3 welding wire
Dia. 0.9mm Dry extension 6.4 mm |
Vertical welding | 55~65.6 | 19 | 110~120 | - | ||
Aerial welding | 55 | 19~20 | 110 | 5.9 | ||
Horizontal Welding | 59.2 | 20 | 120 | 5.1 | ||
3.2 | Flat welding | 71.9 | 20 | 135 | 4.7 | |
Vertical Welding | 71.9 | 20 | 135 | 5.9 | ||
Horizontal Welding | 71.9 | 20 | 135 | 4.2 | ||
Aerial welding | 71.9 | 20 | 135 | 5.1 |