The lower protective lens is an essential consumable accessory for laser equipment, with a very high replacement frequency. It acts as a “double-sided fence” on the laser’s outer light path.
Its main functions are to resist the harsh external processing environment, prevent the invasion of dust and splashes, and resist the high-power laser transmitted in the direct internal direction.
Due to its crucial role, it is often the first component to be affected even when there is a problem in the gas path, leading to huge consumption.
Customers often ask about selecting the right protective lenses. To answer these questions, we interviewed Raycus R&D and after-sales engineers to provide answers to your concerns.
1. Is there a big difference between lower protection lenses from different manufacturers?
There is a significant difference between lower protection lenses. These lenses not only protect the cleanliness of the internal light path of the cutting head, but also require high-power laser support capacity and high laser transmission.
To meet these demanding conditions, the substrate, processing, coating and packaging requirements for lower protection lenses are stringent.

Generally speaking, the original cutting head bottom protection lenses are expensive, which has made third-party bottom protection lenses quite popular. However, not every third-party manufacturer has the production capacity to manufacture this type of consumable.
In recent years, as the fiber laser price war has heated up, the price of laser accessories has decreased significantly. However, blindly looking for lower prices and ignoring quality will not lead to positive results.
2. What will be the consequences if the selection is inappropriate?
The unqualified lower protective lens absorbs light and heats up quickly, causing significant focus drift and resulting in poor cropping.
Furthermore, excessive heating may cause the lower protective lens to break and even lead to reverse breakage of the focus and alignment of the cutting head.
Damage to high-value components can result in maintenance costs of up to 20% to 50% of the price of a new cutting head, resulting in significant losses.
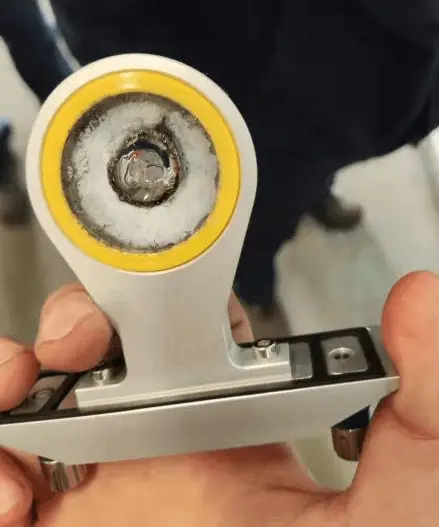
Breakage of the lower protective lens
Coating that does not meet the required standards has low light transmittance. As a result, there is insufficient transmission and strong reflection, causing the return light from the lower protective lens to reverse through the collimating lens and the focusing lens of the cutting head. This light then converges near the end cover of the output head, leading to burnout of the output head's protective window.
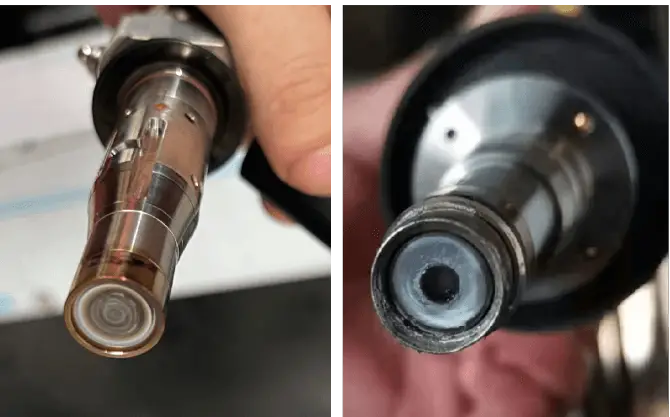
The window protective cover and shaving head protective cover are burnt out
The situation becomes more serious when the output head cover is burned. The direct laser cannot be transmitted and gets stuck in the output head, leading to the destruction of the metal structure of the output head. This, in turn, causes water leakage, slag spraying and other related problems.
In these cases, irreversible damage to the cutting head is likely to occur.
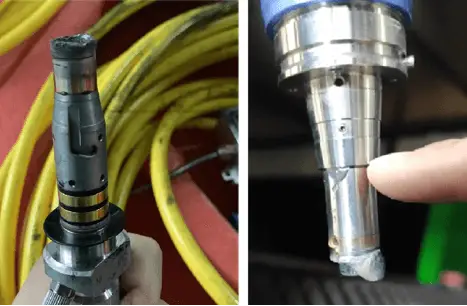
Burnt cutting head shell
3. How to choose protective lenses?
In general, small and medium-sized end customers have relatively low demand for consumables and weak bargaining power. They can purchase consumables through equipment suppliers. However, caution should be exercised when purchasing through informal channels or when prices are significantly different.
Large terminal customers or integrators, on the other hand, have high demand and strong bargaining power and quality inspection capabilities. They can buy from integrators, consumable manufacturers or first-class agents.
When purchasing protective lenses, it is important to consider the following points:
- Base material: Choose mature materials from established industrial suppliers.
- Manufacturers: Look for cold optical processing manufacturers with high-power laser windows, lenses and other optical parts production qualifications.
- Coating: Select an anti-reflective film customized for the laser output wavelength.
- Test report: Make sure the protective lens comes with transmission wavelength report, qualified finish report, material model, weak absorption report (if applicable), coating adhesion report, size report and format, among other necessary documents.
4. What type of protective lenses should not be used?
There are four types of protective lenses that should not be used.
The first type is the protective lens with film coating and exposed quartz substrate. This type of protective lens can be recognized with the naked eye.
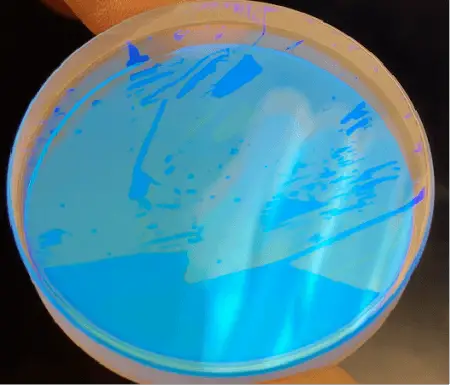
Removing the lower protective coating from the lens
The second type is protective lenses with a low-quality coating. Although the appearance of this protective lens may look good, tests show that some areas of the coating have low transmittance and high reflection.
This type of protective lens cannot be detected by the naked eye or under a microscope and can only be accurately measured with professional instruments.
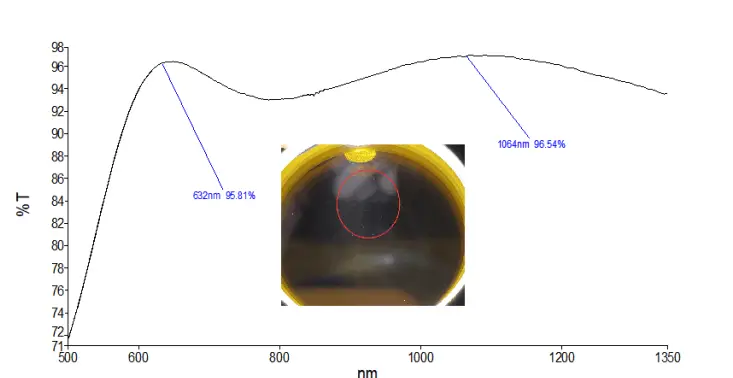
Poor quality of the lower protective lens coating
The third type is a protective lens with foreign bodies or bubbles between the film and the substrate. This type of protective lens is intended for high-power use, but has a short lifespan and is prone to burnout.
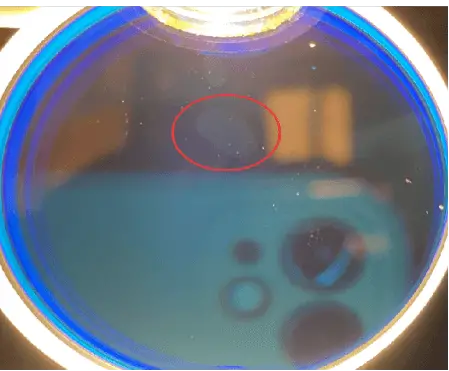
Bubbles or foreign bodies at the bottom of the film
The fourth type is the protective lens with poor finish, which has a short lifespan.
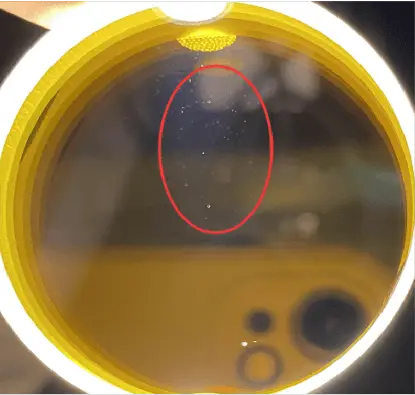
Poor finish of the lower protective lens
5. How to judge whether the lower protective lens is abnormal?
Identifying system instability and risks resulting from abnormal protection is an urgent requirement in today's competitive market. Although most high-power cutting heads currently have protective lens temperature and stray light monitoring, some cutting head monitoring indirectly deduces the current temperature, resulting in low accuracy and low sensitivity response.
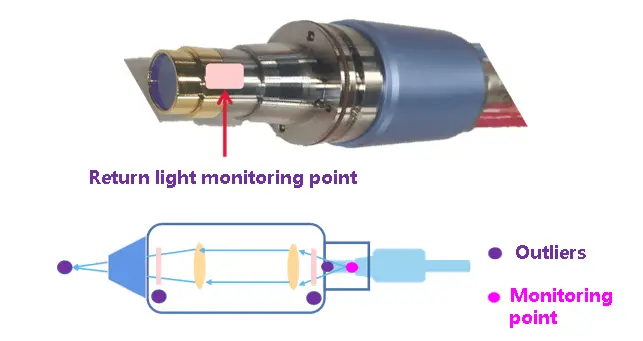
Sensor packaging position and abnormal points that can be monitored
Based on the situation mentioned above, Raycus has recently implemented a new return light monitoring system on its medium and high power lasers.
The primary return light monitoring sensor is placed near the end of the output optical cable, creating a nearly coaxial monitoring arrangement. This allows immediate detection of any return light generated due to damage to the cutting head's optical components.
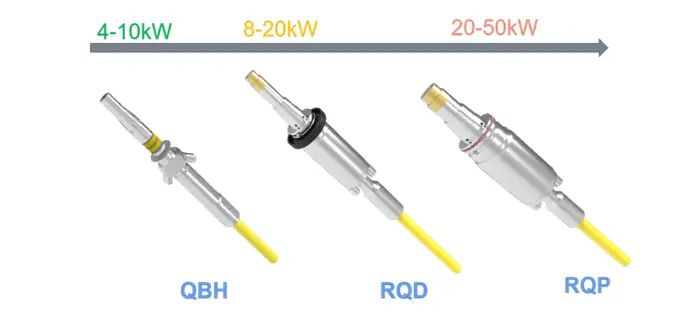
Model of laser power section and output optical cable with return light monitoring
Assuming the water cooling system is operating normally, the Raycus optical laser return visit monitoring system will quickly trigger an alarm signal if it detects any of the following three conditions:
- Abnormal lower protective lens.
- Abnormal upper protective lens.
- Processing highly reflective materials.
For example, the Raycus 20kW model has been equipped with backlight monitoring since 2019, successfully avoiding the following problems:
- Improper use by customers which may cause damage to the output head.
- Faulty design from the cutting head manufacturer.
- Poor condition of the customer's cutting head.
- High reverse cut by the customer.
Currently, the quality of protective lenses available on the market varies greatly. We recommend carefully reviewing the above information and purchasing protective lenses through legitimate channels.