1. Introduction
When a press brake bends a workpiece, the ram and worktable deform under the force of the bend. At this point, the depth of the upper die entering the lower die opening does not align with the entire length of the part, causing a significant decrease in part accuracy.
To address this issue, several strain compensation devices have been developed and can be classified into two categories.
The first category involves the work table designed with a convex shape that rises in the middle, forming a symmetrical curve. This is known as “lower matrix convex compensation”.
The second category involves the upper die or ram being elevated with a symmetrical curve dipping down the middle. This is called “upper matrix convex compensation”.
2. The influence of two types of crowning devices on part accuracy
2.1 Deformation of ram and worktable during bending after convex compensation device
For simplicity of description and expression, the ram and worktable are represented as thin rectangles.
Without any compensation, the ram and worktable deform under the bending force. At this time, the value of the compensation convexity (f) is equal to zero, being the deformation of the ram (f1) and the deformation of the work table (f2).
To correct this, the compensation device is triggered, setting the value of the compensation convexity (f) equal to (f1 + f2).
In an ideal scenario, the depth of the upper die entering the lower die opening remains consistent along the entire length of the die, resulting in a uniform bend angle of the sheet metal. Although achieving this ideal scenario is challenging, people continually strive to get as close as possible.
From the above analysis, it can be concluded that both compensation devices can effectively reduce the angular error of bent parts. However, its impact on righteousness is different.
2.2 Natural deflection of bent parts
After bending, the edge of the bent part will flex naturally, with its maximum deflection being described by δ.
During the bending process, the metal in the deformation area undergoes high levels of plastic deformation. In this zone, the inner layer of the circular arc experiences longitudinal compressive stress parallel to the OX direction, while the outer layer experiences longitudinal tensile stress.
These opposing tensile and compressive stresses create a longitudinal moment (My) rotating about the OY axis, which is necessary to keep the longitudinal direction (OX direction) of the bent part in alignment with the corresponding longitudinal line of the die during bending.
Once the ram returns and the bending force and longitudinal moment are removed, the metal layers in the deformation area recover quickly. As a result, natural bending occurs in the opposite direction to the longitudinal moment in the longitudinal direction.
For ease of expression, the flexural deformation zone is considered a plane. Under the influence of bending force, the upper (inner circular) layer of the metal undergoes longitudinal compression and the lower (outer circular) layer undergoes longitudinal tension.
2.3 Influence of two different convex compensation methods on the straightness of bent parts
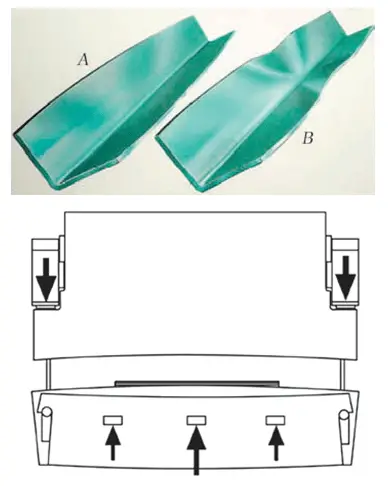
When a lower die is equipped with convex compensation, the compensation convexity curve rises. On the other hand, when a top die is equipped with convex compensation, the compensation convexity curve descends.
The natural deflection curve of the bent part is an upward bulge. The value of compensation convexity is determined by the deformation of the ram and worktable during bending and is relatively small.
Due to the compensation convexity, the deflection caused by springback will be reduced. As a result, the deflection caused by the compensation convexity is normally less than the natural deflection (δ) of the bent part.
3. Comparative analysis of common strain compensation devices
3.1 Convex compensation of the lower cross member hydraulic cylinder
Once the hydraulic cylinder is filled with pressurized oil, the cross beam will rise and form a set of controllable convex curves. This design is widely used in CNC press brakes and has the following characteristics:
- The cylinder is evenly distributed along the cross beam, and the convex curve closely resembles the deformation curve of the ram and work table along the entire length of the work table.
- It is easy to operate with the hydraulic system pressure control.
- It can improve the bending angle accuracy.
- Its structure is complex and the cost is high.
3.2 Convex module compensation on the work table
The work table is equipped with several groups of wedges located below it. The angle of each group is designed to meet specific requirements. The horizontal position of the upper wedge in each wedge group is fixed, while the lower wedge moves to the left simultaneously.
As the worktable rises to meet design requirements, this design has become widely used in various types of press brakes.
Following are the features of this design:
- The wedges are evenly distributed along the worktable, and the convex curve after compensation is designed to match the deformation curve of the ram and worktable, resulting in relatively accurate compensation.
- The amount of compensation can be controlled by adjusting the movable length of the lower wedge, allowing manual or flexible operation.
- It can improve the bending angle accuracy.
3.3 Convex compensation of the upper die wedge
Several modules are positioned between the ram and the upper die, with each group of wedges having the same specifications. The connecting plate and the lower wedge wedge are fixed as a unit. By moving the upper wedge, a downward convex curve can be achieved. Finally, the modules are fixed between the ram and the upper die by a pressing plate.
Following are the features of this design:
- The wedge blocks are evenly distributed under the ram.
- By adjusting each wedge, the ideal convex curve can be obtained.
- The structure is simple, the cost is low, but the operation is less convenient.
- It is widely used in small and medium-sized conventional press brakes.
- With precise adjustment, the bending angle accuracy can be significantly improved and the parts have good straightness.
3.4 Convex compensation of the ram hydraulic cylinder
A group of hydraulic cylinders is installed in the center of the ram. Once the cylinders are filled with pressurized oil, the center portion of the ram will descend, creating a controllable local convex curve.
However, due to structural limitations, the two sides of the ram cannot be compensated effectively, making this method of compensation less commonly used.
Following are its characteristics:
- The convex offset is concentrated at the center of the ram and a consistent convex curve cannot be formed along the entire length of the upper die.
- Angle and straightness accuracy can be improved to a certain extent.
4. Conclusion
During the operation of the press brake, the compensation convexity must correspond to the deformation of the ram and the work table. This requires the ability to quickly and easily adjust convexity compensation over the entire length of the die.
However, the current design of the punch's convex compensation makes it difficult to meet this requirement, limiting its use.
To increase the operation accuracy of the press brake and fully utilize the benefits of upper die convex compensation, the development of a new structure for rapid control of the upper die crown is a promising direction for the future development of press brakes.
Currently, some organizations have made positive attempts in this field and achieved promising results.