The strength of metals is one of the most important mechanical properties required for classifying the applications and uses of metals. Some metals may be suitable for use in the construction industry, but not in the aerospace industry. This is a crucial factor used by scientists, manufacturers and engineers to ensure the functionality and practicality of metal in all their projects.
In the materials industry, strength is defined by the ability of a material to withstand an applied load without suffering failure or plastic deformation.
Types of Strengths
Materials have different resistances depending on the load. These resistances are used as parameters to be considered when selecting a material for specific applications. Below are the different types of resistance of metals:
Stretch limit- This is the maximum strength a metal can withstand before showing permanent plastic deformation in a tensile test. Engineers use this value to determine the maximum load a component can support. This is used in many technical regulations as a criterion for defining failure.
Tensile strength or simply called tensile strength- This is defined by the maximum stress that the material can withstand in a tensile test. In simpler terms, this is the maximum load a metal can withstand before breaking or being torn apart.
compressive strength- This is the maximum strength at which a material can resist failure during a compression test. In this type of resistance, the load is applied to the top and bottom of the sample.
Impact Resistance- This is the ability of a metal to withstand sudden and severe stress without failing. It is the maximum energy a metal can absorb before cracking or breaking.
Why do we need to learn about the resistance of metals?
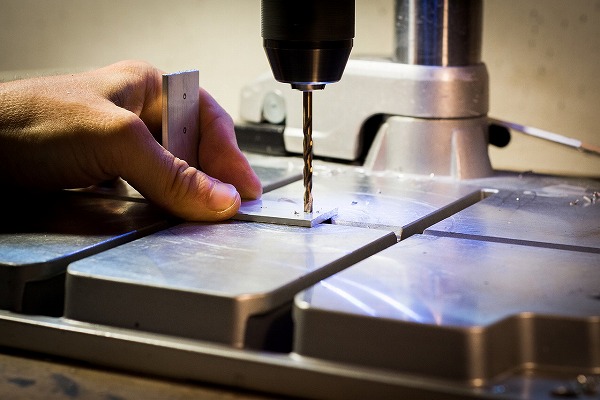
Now that you've learned about the basic types of mental toughness, you probably understand a little about the importance of learning about mental toughness. To explain this further, below is a comprehensive discussion on why metal strength is important across various industries:
Mechanical/structural design
When it comes to mechanical and structural elements, engineers need to know the strength of the parts they are designing. They use them to identify where a material might break or fail. This allows them to set limits and define necessary constraints for specific pieces they design.
Material selection
The resistance of metals is a very important criterion in the selection of materials that can withstand the demands of various industrial applications. Different metals have different resistance values. There are certain metals that are suitable for heavy-duty applications and also some that are more suitable for light-duty applications. For example, a metal with high tensile strength is preferred for manufacturing parts required for lifting or pulling.
Security
It all comes down to security. The resistance of metals establishes several limits to avoid failures in any application. Knowing the resistance class of the metal, it is possible to design parts in a safe and infallible way that can withstand the intended loads without causing harm to users.
The strongest metals used in metallurgy
In industry there are stronger metals that can be preferred depending on the application and design requirements. Below are the strongest metals commonly used in various industries:
1. Titanium
This natural metal has high tensile strength because its structure is less dense than that of common metals. Titanium is popular due to its low strength-to-weight ratio and high corrosion resistance, making it perfect for aerospace, automotive and medical applications. In addition to its pure state, titanium is often alloyed with other metals to further increase its strength. An example is titanium aluminide, in which the alloying elements are aluminum and vanadium.
2. Chrome
Chromium made it to the list of the strongest metals because it is considered the hardest metal on the planet. Although chromium is not often used alone, it has surprising effects when alloyed with other metals. One popular application is chromium as a main ingredient in the production of stainless steel, one of the most sought after metals in all industries.
3. Tungsten
It is considered the strongest and hardest natural metal as it has a tensile strength of 250,000 psi or 1,725 MPa. To compensate for its fragility, this metal is often alloyed with other elements. The most popular alloy is tungsten carbide. The strength of tungsten is very useful for various applications in the military, aerospace, mining and other metallurgical industries.
4. Steel
Steel is generally one of the strongest metals and the most important building material. This metal is made from alloys of iron, carbon and some other elements, depending on the type of steel. The breaking strength of steel depends on its other alloying components. Below are some common types of steel:
- Stainless steel – an alloy of steel, chromium and manganese. This metal is known for its excellent corrosion resistance properties. It has a yield strength of 1560 MPa and a tensile strength of up to 1600 MPa.
- Steel-iron-nickel alloys – Generally, alloying carbon steel with nickel increases its tensile strength by up to 1450 MPa. Different manufacturers have produced their own variants of this alloy.
- Tool Steel – This type of steel alloy is made by mixing the correct proportions of cobalt and tungsten. Its strength and hardness make it a perfect material for making CNC cutting tools and even shafts.
5. Inconel
Another league that made the list is Inconel. This is an alloy of austenitic nickel and chromium. These superalloys are extremely strong and resistant to corrosion, making them perfect for applications in extreme environments and conditions. They are commonly used to manufacture turbines, turbocharger rotors, heat exchangers, pressure vessels, and more.
Processes to improve metal strength
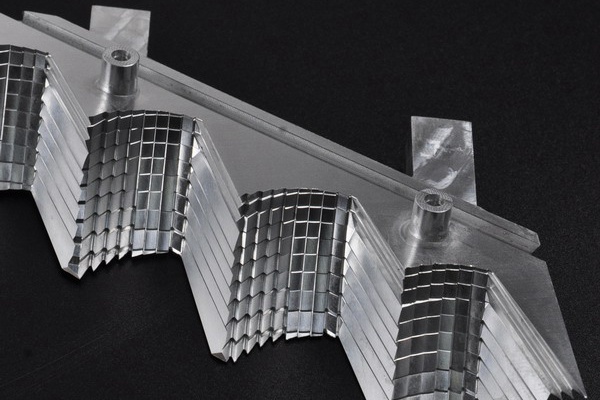
1. Solid solution solidification and alloy formation
This is the method used for the previously mentioned metal alloys to improve the strength of the pure metal. Solid solution hardening involves the formation of a “solid solution” by adding atoms of an alloying element to the crystal lattice of the base metal.
2. Heat treatment
This specific process can be carried out at any point in the production of a metal part to improve its properties. During the heating process, the microstructure of the metal is changed, making the metal or alloy stronger, more resistant and more durable. Below are the common heat treatment methods:
- Brightness- Metals such as copper, silver, aluminum, steel and brass are heated to reduce the risk of breakage during processing. Three phenomena occur during annealing: recovery, recrystallization and grain growth.
- Quenching Tempering involves heating the metal to a temperature just below its hardening temperature and holding it at that temperature for a specific period of time. This process is done to reduce the fragility of the metal, maintaining its hardness and resistance.
- Normalization- This process is done to make the steel stronger and more ductile.
- hardening In this process, the metal is heated to a temperature high enough to dissolve solvent-rich precipitates. This process then increases the hardness and strength of the metal. The disadvantage, however, is that the metal has already lost its ductility, making it brittle.
3. Work hardening
In this method, the metal is reinforced through plastic deformation to increase its hardness, yield strength and tensile strength. The displacements that occur during this process lead to entanglements in the grain displacements. This interlacing prevents further deformation of the affected grains and thus increases mental strength. Solidification often occurs in cold working and forming processes such as crushing, shearing and bending.
The difference between strength and hardness
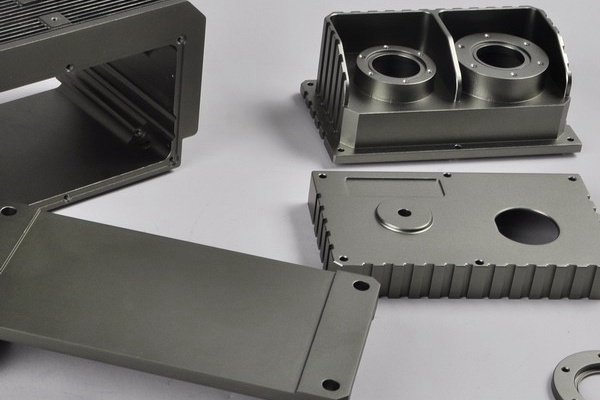
Although strength and hardness are closely related, it is important to note that these properties are measured differently. Strength is defined as the ability of a material to resist deformation caused by an external load, while hardness is the ability of a material to resist penetration or scratching.
As already mentioned, there are completely different testing methods for these two. The strength of metals is determined by a tensile or compression test on a universal testing machine, while hardness tests can be performed using several methods, including Rockwell hardness test, Brinell hardness test, Vickers hardness test, and Shore stereoscope. .
These two are important in the design and engineering industry as they represent one of the most important parameters to consider. Resistance establishes the limits for the maximum load allowed on the parts to be manufactured. This is crucial to avoid errors in structures and machines. On the other hand, hardness is a very good indicator of a metal's resistance to mechanical wear. Harder metals are preferred for making parts that need to have excellent wear resistance.
Metal Strength Chart
If your project requires metal parts, there are some important parameters you need to know about common metals. For example, the yield strength of steel, tensile strength of steel, density, hardness, etc. There is a metal table. You can compare and reference the properties of different metals.
Types of metals | Tensile Strength (PSI) | Yield Strength (PSI) | Rockwell hardness (scale B) | Density (Kg/m³) |
304 stainless steel | 90,000 | 40,000 | 88 | 8,000 |
6061-T6 Aluminum | 45,000 | 40,000 | 60 | 2720 |
Aluminum 5052-H32 | 33,000 | 28,000 | 2680 | |
Aluminum 3003 | 22,000 | 21,000 | 20 to 25 | 2730 |
A36 steel | 58-80,000 | 36,000 | 7800 | |
Steel Grade 50 | 65,000 | 50,000 | 7800 | |
Yellow brass | 40,000 | 55 | 8470 | |
bronze metal | 49,000 | 65 | 8746 | |
copper | 28,000 | 10 | 8940 | |
Phosphor bronze | 55,000 | 78 | 8900 | |
aluminum bronze | 27,000 | 77 | 7700-8700 | |
titanium | 63,000 | 37,000 | 80 | 4500 |
University Degree
It is very important to choose the right metal for your projects. You can refer to the metal strength table and choose a suitable metal material according to the characteristics, functions and application of your projects. Of course, if you think this is complicated, you can contact WayKen, who have extensive experience in metallurgy and can always give you professional suggestions for your project.