Although aluminum and its alloys are widely used in welding important products, they present difficulties in actual welding production. Some of the main problems include porosity in the weld, hot cracking during welding and achieving equal strength in the joint.
One of the reasons for these problems is the strong chemical activity of aluminum and its alloys, which makes the surface very prone to the formation of oxide films, often refractory. For example, the melting point of Al2O3 is 2050 ℃ and the melting point of MgO is 2500 ℃. Furthermore, aluminum and its alloys have high thermal conductivity, making it easier to avoid melting during welding.
The oxide film, which has a similar density to aluminum, can form inclusions in the weld metal. Additionally, the less dense oxide film with MgO can absorb more water and is often a significant cause of weld porosity. Furthermore, aluminum and its alloys have a large coefficient of linear expansion and high thermal conductivity, making them prone to deformation during welding.
Finally, the article analyzes the relatively serious cracks that occur during testing.
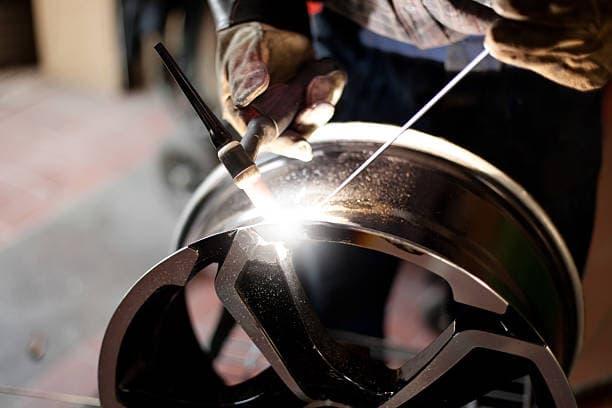
1. Cracks in aluminum alloy welded joints and their characteristics
During the aluminum alloy welding process, various cracks may appear at the welded joints due to differences in the types, properties and welding structures of materials.
The shape and distribution of these cracks can be quite complex.
Based on their location, these cracks can be divided into two types:
(1) Cracks in the weld metal: longitudinal cracks, transverse cracks, crater cracks, hair-shaped or arc cracks, root cracks and micro-cracks (especially in multilayer welding).
(2) Cracks in the heat-affected zone: weld cracks, lamellar cracks and micro thermal cracks close to the fusion line.
Cracks generated during welding can be categorized into hot cracks and cold cracks, based on the temperature range in which they occur.
Hot cracks occur at high temperatures during welding and are mainly caused by the segregation of alloying elements at the grain boundary or by the presence of low melting point materials.
The shape, temperature range and main causes of hot cracking vary depending on the welded metal materials.
Hot cracks can be divided into three types: crystallization cracks, liquefaction cracks and polygonization cracks.
Crystallization cracks occur mainly during the welding process at high temperatures. Near the solidus, the solidified metal shrinks, causing insufficient residual liquid metal that cannot fill over time, leading to the generation of cracks.
Intergranular cracking occurs due to solidification contraction stress or external force, mainly in carbon steel, low alloy steel welds and some aluminum alloys with more impurities.
Liquefaction cracks occur due to shrinkage stress during solidification of grain boundaries heated to high temperatures in the heat-affected zone.
In testing, it was found that insufficient surface cleaning of the filler material resulted in the presence of inclusions and pores in the weld after welding. In the three group number test, because the welding filler material is a molten structure and the inclusion is a high melting point material, it remains in the weld after welding.
The casting structure is relatively sparse, with many holes, facilitating the absorption of components containing crystal clear water and quality oil. These factors can cause porosity during welding, and inclusions and pores become key parts that induce microcracks when the weld is under tensile stress.
Additional microscope observations revealed an interaction between these inclusions and pore-induced microcracks. However, it is challenging to determine whether inclusions act primarily as a source of stress concentration to induce cracking or as a brittle phase to induce cracking.
Furthermore, it is widely believed that porosity in aluminum-magnesium alloy welds does not significantly affect the tensile strength of the weld. However, this study found inclusion-induced microcracks and porosity in the weld tensile samples simultaneously.
Whether pore-induced microcracks are an associated secondary phenomenon or one of the main factors causing a significant decline in the tensile strength of welds requires further study.
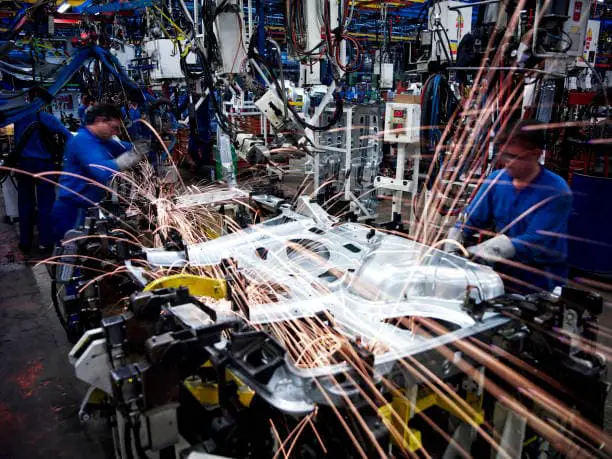
2. Hot crack generation process
Currently, the theory of hot crack welding, proposed by Prokhorov both nationally and internationally, is considered highly refined.
To summarize, theory suggests that the generation of cracks in the crystal mainly depends on the following three factors:
- The size of the brittle temperature range
- The ductility of the alloy within this temperature range
- The rate of deformation of the metal when in the brittle temperature range
The size of the brittle temperature range and the ductility value within this range are commonly called metallurgical factors that can produce hot cracks in welding, while the metal deformation rate within the brittle temperature range is known as the mechanical factor.
The welding process involves a series of unbalanced technological procedures. This characteristic is closely linked to metallurgical and mechanical factors of metallic fracture in welded joints, such as physical, chemical and organizational heterogeneity, slags and inclusions, gaseous elements and vacancies with supersaturated concentrations of the products of technological and metallurgical welding processes. .
All of these factors are closely related to the initiation and development of cracks in metallurgy.
In terms of mechanical factors, the specific temperature gradient and cooling rate of the welding thermal cycle can cause the welded joint to be in a complex stress-strain state under certain constraint conditions, which provides the necessary conditions for the initiation and development of cracks.
During the welding process, the combined effect of metallurgical and mechanical factors can strengthen or weaken the metallic bond in two ways.
If a strong bond is established in the metal of the welded joint during cooling, the deformation can remain obedient under certain rigid restraint conditions. When the weld and metal near the seam can withstand external restraint stresses and internal residual stresses, cracking is less likely to occur and the sensitivity of the metal to cracking is low.
On the other hand, if the stress cannot be withstood, the strength bond in the metal is more likely to be broken, resulting in cracks. In this case, the sensitivity to cracking of the weld joint metal is high.
The solder joint metal is cooled to room temperature at a certain rate from the crystallization solidification temperature. Its sensitivity to cracking depends on the comparison of the deformation capacity and the applied strain, as well as the comparison of the resistance to deformation and the applied stress.
However, during the cooling process, different temperature stages can result in different intergranular strength and grain strength growth, different strain distributions between and within grains, different strain-induced diffusion behaviors, different stress concentration conditions and factors that lead to metal embrittlement. These can cause different specific weak links in welded joints, and the degree to which they weaken can also vary.
The occurrence of cracks in the metal of the welded joint is closely related to metallurgical and mechanical factors.
The stress gradient in mechanical factors is related to the temperature gradient, which is determined by the characteristics of the thermal cycle. The thermal conductivity of the metal determines the characteristics of the thermal cycle, which are considered metallurgical factors. These include the metal's thermoplastic change characteristics, thermal expansion, and structural transformation.
The stress-strain state of the welded joint metal is greatly influenced by metallurgical and mechanical factors. Furthermore, these factors change as the temperature decreases and the cooling rate changes.
Different temperature ranges affect the strength of the welded joint metal differently. For example, the large crystallization temperature range and low solidus temperature are likely to cause stress concentration in the low-melting residual liquid metal between the grains, leading to cracks in the solid metal. Similarly, if the shrinkage is large, especially under the condition of rapid cooling, cracking is likely to occur when the shrinkage strain rate is high and the stress-strain state is severe.
During the later phase of solidification and crystallization of the weld metal during aluminum alloy welding, the eutectic is compressed at the center of the crystal intersection to form a “liquid film”. At this point, due to large shrinkage during cooling, free shrinkage is not available to generate large tensile stresses. As a result, the liquid film forms a weak link, which may crack in the weak zone under the effect of tensile stress.
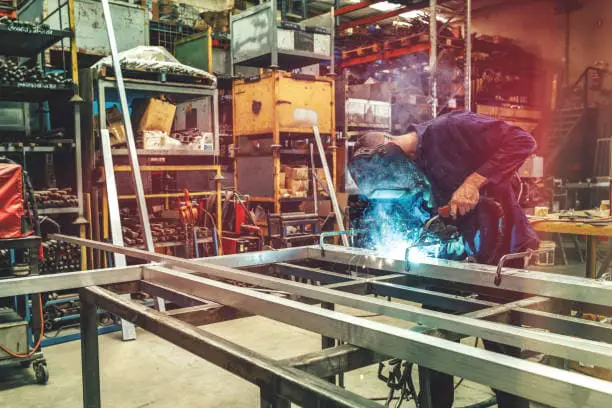
3. Hot cracking mechanism
To investigate the occurrence of hot cracks when welding aluminum alloys, the welding pool crystallization process is classified into three stages.
The first stage is the liquid-solid stage, during which there are a small number of crystal nuclei as the welding molten pool begins to cool due to the high temperature. As the temperature drops and the cooling time increases, the crystalline nuclei gradually grow and new ones emerge.
However, the liquid phase still predominates and there is no contact between adjacent grains, which allows the free flow of the liquid aluminum alloy that has not yet solidified. Thus, even under tensile stress, any open gaps can be readily filled by the flowing liquid metal, making the likelihood of cracking at this stage very small.
The second stage is the solid-liquid stage. Here, the solid phase in the molten pool continues to increase as crystallization progresses, and the previously formed crystalline nuclei continue to grow.
When the temperature drops to a certain point, the solidified aluminum alloy metal crystals come into contact with each other and continuously roll together. At this stage, the flow of liquid aluminum alloy is blocked and the crystallization of the molten pool enters the solid-liquid phase.
Due to the small amount of liquid aluminum alloy metal, the deformation of the crystal itself can be strongly developed at this stage, and the residual liquid phase between the crystals is not easy to flow.
The small gaps generated under tensile stress cannot be filled, and even a small tensile stress can lead to the possibility of cracking. This stage is known as the “brittle temperature zone”.
The third stage is the complete solidification stage. When the weld formed after complete solidification of the molten pool metal is subjected to tensile stress, it has good strength and plasticity, and the probability of cracking at this stage is relatively low.
Therefore, when the temperature is higher or lower than the brittle temperature zone between ab, the weld metal has greater resistance to crystalline cracking and less tendency to crack. In general, for metals with fewer impurities (including base metals and welding materials), the brittle temperature range is narrow.
Tensile stress operates in this range for a short period of time, so the total weld stress is relatively small, resulting in a lower tendency for cracks to develop during welding.
However, if there are many impurities in the weld, the brittle temperature range is relatively wide, and the tensile stress action time in this range is relatively long, leading to a greater tendency to produce cracks.
4. Prevention measures for welding cracks in aluminum alloys
To reduce the probability of hot cracks when welding aluminum alloys, improvement can be made through two aspects: metallurgical factors and technological factors.
Regarding metallurgical factors, the prevention of intergranular hot cracks during welding involves adjusting the weld alloy system or adding modifiers to the filler metal.
To control an appropriate amount of fusible eutectic and narrow the crystallization temperature range from the perspective of crack resistance, the focus of the solder alloy system needs adjustment.
Because aluminum alloy is a typical eutectic alloy, the “maximum” solidification temperature range of the alloy corresponds to the maximum cracking tendency.
The presence of a small amount of fusible eutectic always increases the tendency for solidification cracks. To counter this, the content of the major alloy elements is normally increased beyond the alloy component with the maximum cracking tendency to produce a “healing” effect.
Furthermore, trace elements such as Ti, Zr, V and B are added to the filler metal as modifiers in an attempt to improve plasticity and toughness, refining the grains and preventing hot cracking during welding. This attempt has been ongoing for some time and has produced positive results.
Figure 3 shows the results of the crack resistance test of Al-4.5% Mg welding wire with a modifier under the condition of a rigid overlapping fillet weld. The test included the addition of 0.15% Zr and 0.1% Ti+B. The results indicate that the simultaneous addition of Ti and B significantly improved the cracking resistance.
Ti, Zr, V, B and Ta share a common characteristic: they can react with aluminum to form a series of peritectic reactions, resulting in the formation of refractory metal compounds such as Al3Ti, Al3Zr, Al7V, AlB2, Al3Ta, etc. .
These small refractory particles can act as non-spontaneous solidifying crystal nuclei during the liquid metal solidification process, thus facilitating grain refinement.
Process factors such as welding specifications, preheat, joint shape and welding sequence are crucial in resolving welding cracks, which are based on welding stress. The parameters of the welding process impact the imbalance of the solidification process and the state of the solidification structure, as well as the rate of strain growth during solidification, thus influencing the formation of cracks.
Welding methods that employ concentrated thermal energy facilitate rapid welding and can prevent the formation of thick columnar crystals with strong directivity, thereby improving crack resistance.
Reducing the welding speed and employing a small welding current can decrease the superheating of the molten pool and improve crack resistance. Increasing the welding speed, however, increases the deformation rate of the welded joints and the tendency for hot cracking. Therefore, it is evident that increasing welding speed and current increases the tendency to crack.
During the assembly and welding of aluminum structures, the weld does not have much rigidity. As such, measures such as sectional welding, preheating or reducing the welding speed can be taken.
Preheating can reduce the relative expansion of the sample and consequently decrease the welding stress, which reduces the stress in the brittle temperature range. Butt welding with slots and small gaps should be employed as much as possible, while cross joints and inappropriate positioning and welding sequences should be avoided. When welding is completed or stopped, the crater must be filled immediately and the heat source removed, otherwise cracks may easily occur in the crater.
During welding of multilayer welded joints of 5000 series alloys, microcracks often occur due to local intergranular melting, necessitating control of the welding heat input from the next layer of the weld bead.
Based on the findings in this article, cleaning the surface of the base metal and filler material is crucial for welding aluminum alloys. The inclusion of materials becomes the source of weld cracks and the main reason for the decline in weld performance.