With rapid advances in modern science, technology and the industrial sector, tubular components play an increasingly crucial role in various sectors, including construction machinery, transportation, agricultural machinery, kitchen appliances and fitness.
At the same time, the emergence and rapid development of CNC laser tube cutting machines have accentuated the benefits of laser tube cutting.
Laser cutting, with its unique attributes of narrow cutting width, minimal thermal effects, fast cutting speeds, perfect cuts, excellent flexibility and no apparent restrictions on the shape, type or thickness of the tube to be cut, stands out when compared to the traditional cut. tube processing methods.
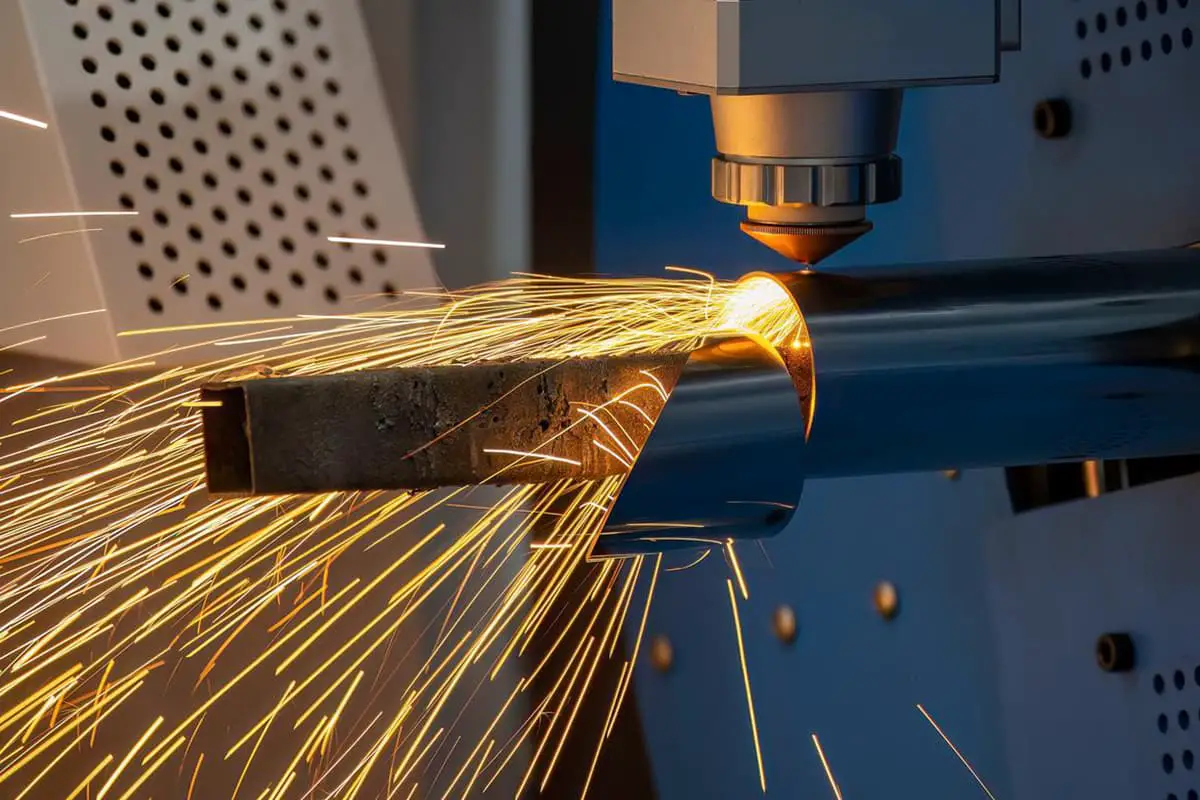
Laser tube cutting technology improves cutting quality, ensures processing efficiency, simplifies workflow, and significantly increases economic benefits for a large number of laser tube cutting users.
However, laser tube cutting is a complex process, with several factors influencing the cutting result. It is vital to analyze problems that arise during the process and develop methods to resolve them.
Incomplete or rough cuts
There are basically four reasons for incomplete or rough cuts during the laser cutting process:
1. Cutting at excessive speeds
Especially when working with special or thick tubes such as profiles or irregularly shaped tubes.
When the cutting head reaches a corner, where the thickness increases, cutting too quickly can lead to incomplete or rough cuts, as shown in Figure 1.
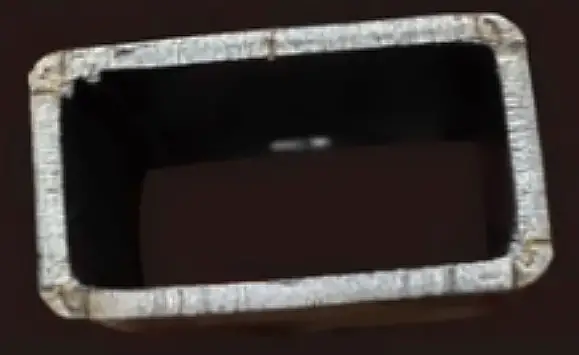
In these scenarios, it is common practice to reduce cutting speed at corners and increase auxiliary gas pressure.
2. Incorrectly adjusted cutting head focal length or incorrectly aligned laser path.
The focal length can significantly affect the quality of the tube cut.
The cutting head's default focal settings include negative, zero, and positive focus.
Positive focus is suitable for oxygen cutting of carbon steel, zero focus is suitable for cutting thin sheets, and negative focus is ideal for materials such as stainless steel, galvanized carbon steel, aluminum, copper, etc., which require oxygen cutting. nitrogen/air.
Therefore, it is essential to choose the correct focal position for various tubes. An incorrectly aligned laser path also significantly affects tube cutting.
Therefore, during test cuts, it is vital to continually adjust the beam position to obtain a perfectly circular spot on the test material.
Contaminated protective lenses, as shown in Figure 2.
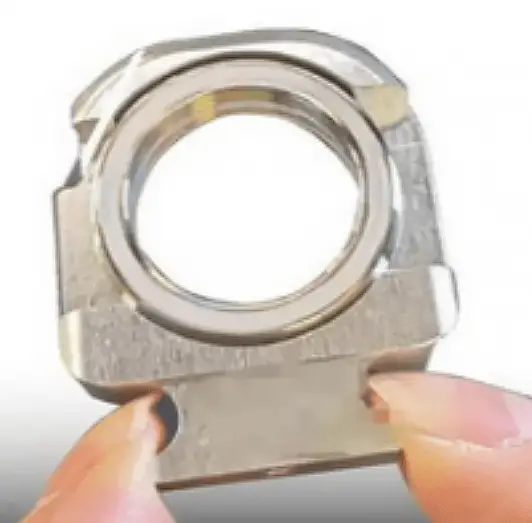
3. The cutting head protective lens and focusing lens are contaminated and the water source for the cooling system is dirty.
Although the normal cutting procedure continuously cools and removes slag with the auxiliary gas, the protective and focusing lenses can be easily contaminated due to the high temperatures during cutting. If these lenses are polluted, it may cause incomplete cuts or failed cutting of the tube.
Furthermore, the use of impure water in the laser cutting system, at best, can affect its cooling efficiency, leading to clogging of the cutting head and generator water channels, impacting the tube cutting quality.
In the worst case scenario, it could damage the generator and cutting head, resulting in significant economic losses.
Therefore, it is essential to use purified water, preferably distilled, to avoid blockages and refrigeration problems.
4. Excessive laser output power or improper nozzle selection for the cutting head.
When laser cutting symmetrical tubes, such as round or square tubes, excess power can cause fused edges.
These molten residues can accumulate on the inner side of the opposite face, effectively increasing the thickness. This buildup can clog subsequent cutting passes, making a complete cut difficult and leaving a rough finish.
Therefore, it is essential to perform preliminary drilling and trial cutting tests to determine the optimal laser output power and auxiliary gas pressure.
Nozzle selection also affects cut quality.
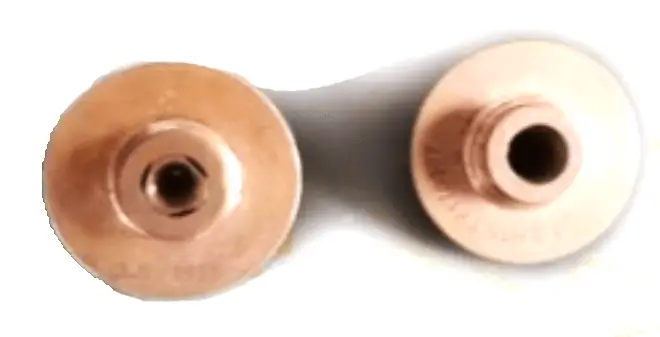
Typically, double nozzle configurations are suitable for precise cutting grooves on pipes, mainly used for thin, high-precision and fast pipe cutting, while single nozzle configurations are suitable for pipes of thicker and varied materials, with requirements less accurate.
Test cuts help you choose the right nozzle for your pipe, ensuring overall cut quality and efficiency.
Misalignment of start and end points or discrepancies in the cutting pattern
Inaccurate parameter settings for machine axes.
Generally, a laser tube cutter comprises control axes such as X-axis rack and pinion drive, Y-axis lead screw drive, Z-axis cutting head and W-axis rotary feed chuck.
If parameters such as gear pitch circle diameter, lead screw pitch or gear ratios are set incorrectly, it will profoundly affect the final cutting result. Some errors can even affect the proper functioning of the machine.
Before operating the machine, it is essential to ensure that the axis parameters are correctly configured.
Misalignment of the X and Y axes or Z and X axes.
If the X and Y axes are not perpendicular, the circular patterns cut into the pipe surface may be distorted, as shown in Figure 4.
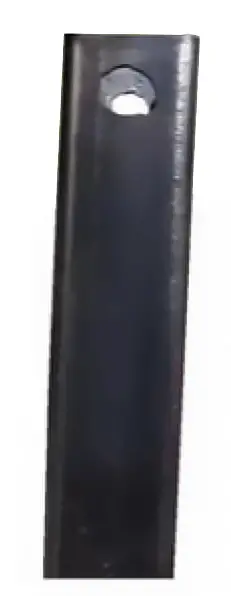
A square pattern can become a parallelogram. If the Z and X axes are not aligned, the cutting head path deviates, causing discrepancies between the simulated and actual cutting paths, leading to misalignment between the start and end points, as seen in Figure 5.
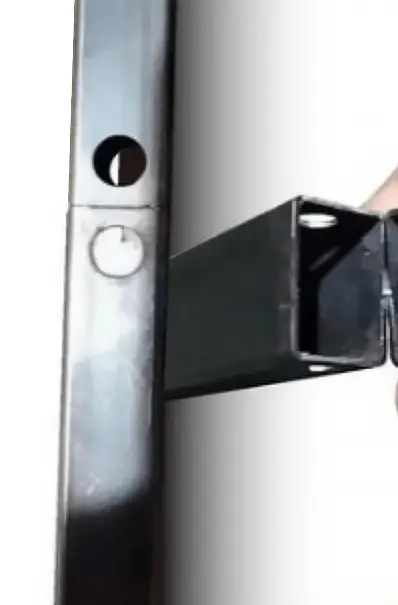
This misalignment is one of the reasons for incomplete pipe cuts. If such problems arise, immediate calibration using a micrometer is necessary, along with checking for loose bolts or wear on racks, lead screws, or gears.
To complete
Laser tube cutting has gained a significant position in the laser cutting industry.
Especially as laser tube cutters have evolved through manual, semi-automatic and fully automatic phases, more people are recognizing their potential in production and processing.
This growing confidence underscores the need to identify and resolve various challenges encountered during laser tube cutting, continually refine cutting systems and techniques, and promote the development of high-speed, precision, automated, flexible, and multifunctional laser tube cutting. . This is critical to the rapid advancement of the entire laser cutting industry.