1. Analysis and Risk Prevention Measures in Welding Operations
Welding, also known as arc welding, is a process that uses the thermal effect of welding equipment to heat and melt the cross-section of welded metal so that the originally separated metals are joined together to form a strong, non-removable joint . .
According to different welding processes, arc welding can be divided into automatic welding, semi-automatic welding and manual welding. Automatic and semi-automatic welding is mainly used in the manufacture of large machinery and equipment, with equipment installed in factories and relatively fixed work spaces.
Manual welding, on the other hand, is more flexible and can be used in external construction. Due to differences in work spaces, welding operations involve multiple hazards, including electrical, optical, thermal, and open flame hazards.
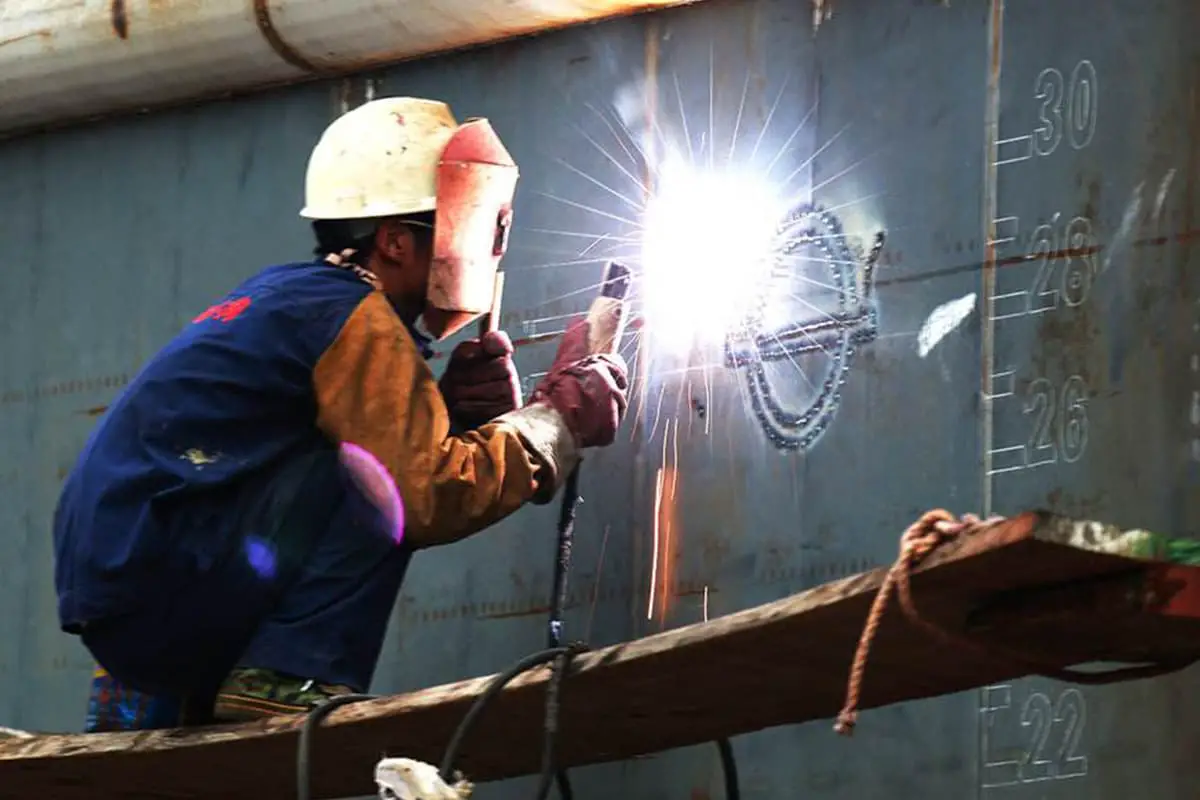
1.3 Burn risks
During the welding process, arcs and molten metal slag are generated. If welders do not wear specialized protective clothing, gloves and shoes, especially when welding at heights where welding sparks can fly, it can cause burns to the welder or workers below the work surface.
1.4 Risks of sudden burns when welding
Intense visible light and invisible ultraviolet rays are generated during welding, which can cause severe irritation and damage to the eyes.
Prolonged direct exposure can cause eye pain, photophobia, tearing and wind sensitivity, causing conjunctivitis and keratitis (commonly known as welding burns).
1.5 Risks of light radiation
Welding arcs emit infrared, ultraviolet and visible light, which can have a radiant effect on the human body.
Infrared radiation has a thermal radiation effect and can cause heatstroke in high temperature environments during welding.
Ultraviolet radiation has a photochemical effect and can cause damage to the skin. Prolonged exposure to visible light can cause decreased vision.
1.6 Hazards from harmful gases and smoke dust
The arc temperature during welding can reach more than 4,200℃, causing the core, flux and welding rod metal to undergo gasification, evaporation and condensation, resulting in the production of a large amount of manganese oxide, chromium and harmful smoke dust.
Furthermore, the high temperature and intense radiation of the arc light can cause the surrounding air to produce toxic gases such as ozone and nitrogen oxides.
Engaging in welding operations for a long time in poorly ventilated conditions can lead to inhalation of these toxic gases and smoke dust, which can have an impact on human health.
1.7 Risks of Falls from Height
Due to construction requirements, welders often need to perform welding operations at height.
If fall protection measures are not implemented properly, scaffolding is not properly erected and inspected before use, or personal protective equipment such as helmets and safety harnesses are not used during high-level operations, it can Accidents such as falls from height occur.
1.8 Poisoning and Choking Risks
Welders often need to enter enclosed or semi-enclosed locations such as metal containers, equipment, pipes, towers and tanks for welding.
If toxic and harmful substances or inert gases are stored or produced during transportation, poor work management and inadequate protective measures can easily lead to the poisoning or asphyxiation of workers, especially in oil refineries and chemical enterprises.
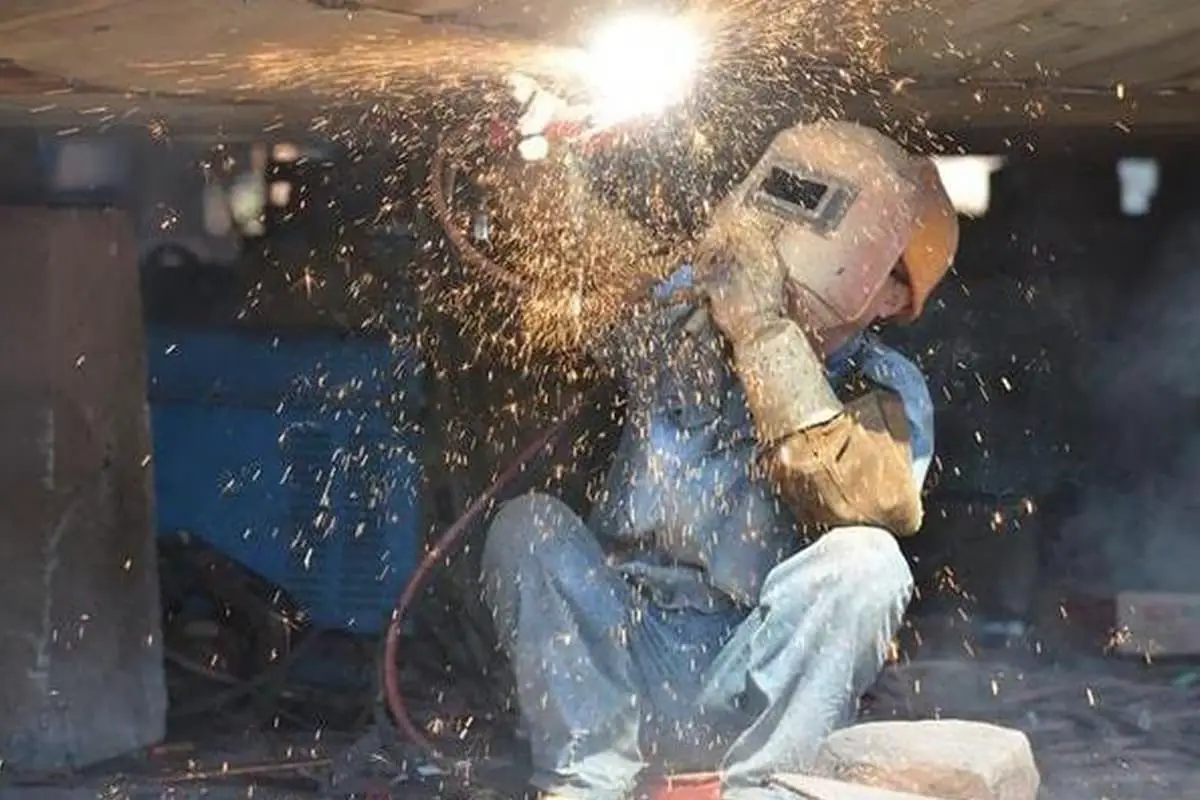
2. Risk Analysis in Welding Operations and Preventive Measures
2.1 Electrical Safety Measures
To prevent electrical accidents, insulation, shielding, insulation, leakage protection and personal protective measures must be taken to avoid direct contact with energized parts. Specific methods include:
a) Improve the insulation performance of welding equipment and circuits. The welding equipment and power cables used must be qualified products, and their electrical insulation performance must be suitable for the voltage level, surrounding environment and operating conditions. Welding machines must be regularly maintained and protected from exposure to sunlight and rain to prevent degradation of their electrical insulation performance.
b) When a welding machine malfunctions, needs to be repaired, the working location needs to be changed, or joints need to be replaced or fuses need to be replaced, the power supply must be turned off before operation.
c) When installing the power supply of the welding machine, be sure to install a residual current device to ensure that the power will be automatically cut off if a person comes into contact with energized parts. When welding on wet or metallic containers, equipment or components, a residual current device with a rated operating current not exceeding 15 mA and a rated operating time of less than 0.1 second must be used.
d) Good protective grounding or zero grounding measures must be taken for the welding machine housing and secondary winding cables. When the power supply is a three-phase three-wire system or a single-phase system, a protective grounding wire with a resistance value of not more than 4Ω must be installed. When the power supply is a three-phase four-wire system with a grounded neutral point, a protective neutral wire must be installed.
e) Strengthen workers' education on electrical safety knowledge and self-protection awareness. Welders must wear insulated shoes and special insulated gloves while working. Welding in the rain is prohibited. When welding in particularly humid environments, workers should stand on dry wooden boards or rubber insulating pads.
f) The use of metallic structures, pipes, rails and other metallic connections as conductors is prohibited. When welding in metal containers or particularly humid locations, the luminaires' power supply must use a safe voltage lower than 12V.
2.2 Fire and Explosion Prevention Measures
a) When welding in flammable and explosive places, a hot work permit must be obtained in accordance with regulations before welding. Approval from relevant departments is required before work begins, and the “no fire” principle must be strictly followed.
b) Before welding, check for flammable and explosive substances below and around the work area and properly handle flammable paints or anti-corrosive substances if present. For welding operations close to operating production units and oil tank areas, fire barriers must be constructed. If welding is carried out at height, asbestos plates or iron plates must be used for insulation to prevent sparks from being emitted.
c) When welding on containers, equipment or pipelines used for the production and transportation of flammable and explosive substances, it is necessary to check whether the connected equipment and pipelines are closed or blocked with blanking plates, and carry out blowing, cleaning, replacement and sampling to analysis in accordance with regulations. Welding can only be carried out after qualifying the analysis results.
2.3 Burn Prevention Measures
a) Welders must wear suitable protective clothing, insulated gloves and insulated shoes when welding. When using high currents for welding, welding tongs must be equipped with protective covers.
b) Newly welded areas must be covered with asbestos sheets or other materials in a timely manner to avoid direct contact and burns to feet and body.
c) Welding electrode heads replaced during high level welding must be centrally stacked to avoid burns to workers below.
d) Protective glasses must be worn when cleaning welding slag. When carrying out suspended or horizontal welding at height, isolation measures must be taken due to excessive sparks.
2.4 Prevention measures for sudden welding burns
Depending on the intensity of the welding current, suitable visors with special protective lenses and colored protective glasses must be used.
Other employees involved in assisting with welding and those near the welding site must also take protective measures and wear suitable protective glasses.
2.5 Measures to prevent radiation
Welders and adjacent workers must wear appropriate personal protective equipment. It is prohibited to directly observe the arc light without wearing welding masks and sunglasses.
Skin exposure should be minimized and, in summer, welding operations should not be carried out in shorts and short-sleeved shirts. If possible, UV protection cream should be applied to exposed skin.
2.6 Measures to prevent harmful gases and dust
a) Design the welding process reasonably and try to use single-side welding and double-side forming process to reduce the amount of welding inside metal containers.
b) For welding operations in small or closed spaces, forced ventilation measures must be taken to reduce the concentration of harmful gases and dust in the work area.
c) Whenever possible, automatic or semi-automatic welding should be used instead of manual welding to reduce exposure of welding personnel to harmful gases and dust.
d) Use low-dust, low-toxicity welding electrodes to reduce the content of harmful smoke and dust in the work area.
e) During welding, welders and other people in the vicinity must wear masks against dust and toxic gases to minimize inhalation of smoke and dust.
2.7 Measures to prevent falls
Welders must undergo regular medical examinations. Individuals with a history of hypertension, heart disease, epilepsy, etc. are prohibited from carrying out welding at high altitudes. When working at height, welders must properly fasten their seat belts and wear safety helmets.
Before welding, the work area and its surroundings must be inspected to ensure the stability and integrity of footrests, as well as the compliance of scaffolding and other safety protective installations with safety requirements.
If necessary, safety nets must be installed below and around the work area. Isolation measures must be taken for operations involving upward and downward movements.
2.8 Measures to prevent poisoning and suffocation
a) Before welding in closed or semi-closed areas, such as containers, equipment, pipes, towers and tanks containing toxic or hazardous substances, all connected process equipment must be disconnected.
Cleaning, purging and replacement must be carried out, and a work permit to enter the equipment must be obtained in accordance with regulations. Sampling and analysis must be carried out, and only after passing the inspection can work begin.
b) Under normal circumstances, sampling and analysis should be carried out every 4 hours, and if conditions change, sampling and analysis should be carried out immediately. Adequate quantities of respiratory equipment (oxygen) must also be available on site for emergency use.
c) Safety monitoring by designated personnel must be carried out during operation, and welders must rotate their work regularly.
For equipment with strong tightness and prone to oxygen deficiency, oxygen replacement must be done through forced ventilation (direct oxygen supply is prohibited) to avoid asphyxiation due to oxygen deficiency.
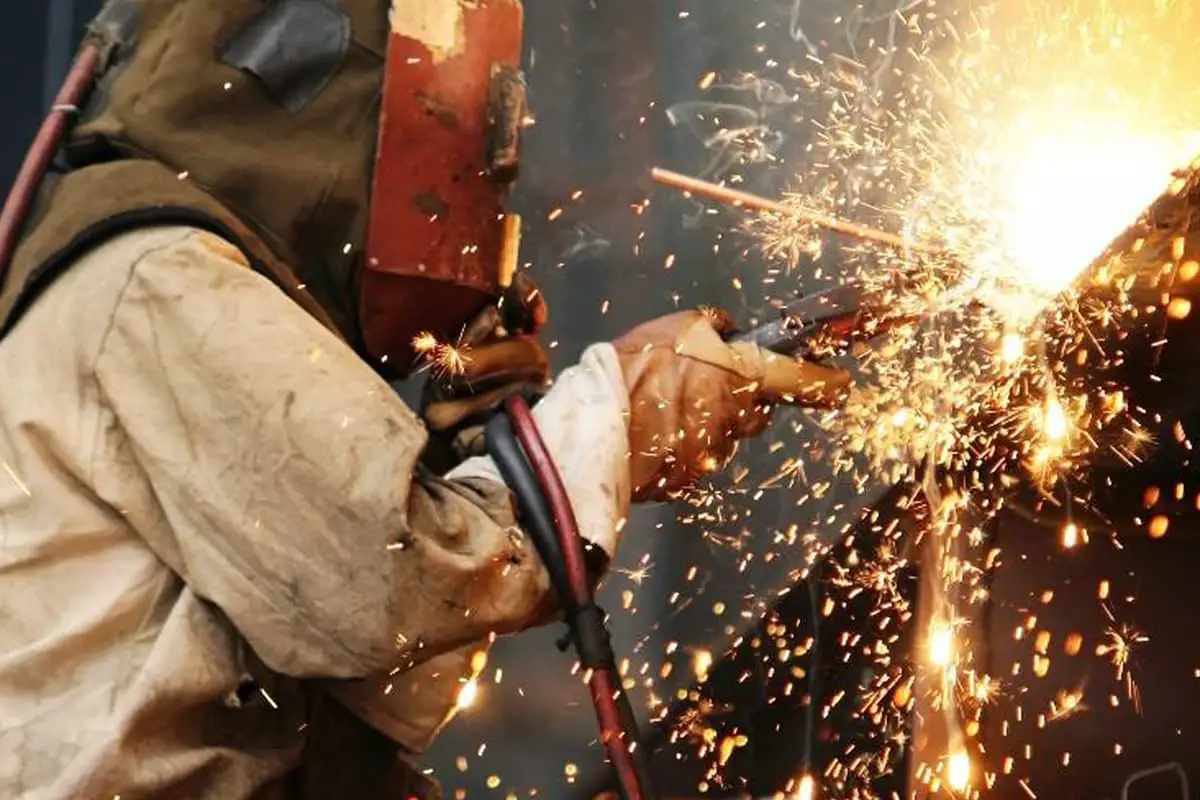
Occupational risks and protection for welders
Welding, a specialized operation, involves significant occupational hazards, including dust, toxic gases, high temperatures, arc light and high-frequency electromagnetic fields. As society rapidly advances, welding is increasingly becoming an integral part of almost every industrial sector.
The increase in the number of welders has led to an increase in occupational hazards associated with welding.
Main hazards in welding operations
- Metal dust hazard: The composition of welding dust varies depending on the welding rod used, which consists of a welding core and flux. The core contains iron, carbon, manganese, silicon, chromium, nickel, sulfur and phosphorus; the flux is mainly composed of marble, fluorite, rutile, pure salt, water glass and ferromanganese. The arc discharge produced during welding generates a high temperature of 4000-6000°C, resulting in large amounts of dust from the melting of the welding rod and workpiece. The dust, composed mainly of iron oxide, manganese oxide, silica and silicate, is easily inhaled and can cause fibrosis in the lung tissue over time, known as welder's pneumoconiosis. This condition is often accompanied by manganese poisoning, fluorosis, and metal fume fever. Symptoms include chest tightness, chest pain, shortness of breath, cough, headache and general weakness. Lung function can also be significantly impaired.
- Danger from toxic gases: High temperatures and intense ultraviolet rays from welding arcs produce large amounts of toxic gases, such as carbon monoxide and nitrogen oxides. (1) Ozone is a colorless, highly irritating gas that strongly affects the respiratory tract and lungs. Short-term exposure to low-concentration ozone (0.4 mg/m3) can cause coughing, dry throat, chest tightness, decreased appetite, fatigue, and other symptoms, while long-term exposure can cause bronchitis, emphysema, and pulmonary fibrosis. (2) Carbon monoxide, a colorless, odorless and non-irritating gas, easily binds to hemoglobin and prevents oxygen from doing so, which leads to tissue necrosis due to lack of oxygen. (3) Nitrogen oxides are toxic gases with a strong odor, the most common being nitrogen dioxide. This reddish-brown gas with a distinct odor can cause intense irritation and corrosion of lung tissue, leading to pulmonary edema.
- Arc Light Radiation Hazard: Arc light produced by welding consists mainly of infrared, visible and ultraviolet light. Ultraviolet light, which can damage the eyes and exposed skin, causing keratoconjunctivitis (eye arch) and erythema. Symptoms include eye pain, photophobia, tearing, swollen eyelids, and clear borders of edema and erythema on the skin after exposure to ultraviolet light. Severe cases may present with blisters, oozing, edema, and a distinct burning sensation.
Protection against occupational risks in welding operations
Given the variety and magnitude of hazards in welding operations, a range of effective protective measures must be implemented to reduce occupational risks for welders.
Improve welding technology, processes and materials:
Improving welding technology to mechanize and automate operations can fundamentally eliminate the risks of welding to human health.
Improving welding processes, such as reasonable design of welding vessels and adopting new techniques such as single-side welding and double-sided forming, can prevent welders from operating in poorly ventilated vessels, significantly improving their conditions. of work.
Choosing non-toxic or low toxicity welding rods by improving the material of welding rods is also an effective way to reduce welding risks.
Improve ventilation conditions in workplaces:
Ventilation can be natural or mechanical, with the latter relying on fans to provide air exchange, dust removal and detoxification. In closed spaces with little natural ventilation, mechanical ventilation measures are necessary.
Strengthen individual protection measures:
Personal protective measures can prevent damage caused by toxic gases and dust produced during welding. Workers must wear appropriate protective glasses, face shields, masks, gloves and wear white protective clothing and insulated shoes.
Bare arms are not allowed. If working in a closed, poorly ventilated container, a ventilated protective helmet must be worn.
Intensify publicity, education and on-site monitoring on labor protection:
Workers must receive the necessary education on occupational health and safety knowledge to increase their awareness of self-protection and reduce the incidence of occupational diseases.
Furthermore, it is crucial to reinforce monitoring of dust and toxic hazards at welding sites and perform regular physical examinations of welders to detect and resolve problems quickly.
Personal protective measures for welding operations
Personal protective measures for welding operations mainly involve protecting the head, face, eyes, ears, respiratory tract, hands and body.
These measures mainly include dust protection, poison prevention, noise reduction, high temperature radiation protection, radioactivity protection, mechanical injury prevention and general cleanliness.
In addition to using standard protective equipment (such as work clothes, gloves, goggles, masks), an air respirator may be used in specific operating environments, such as when welding in closed containers or in situations where ventilation is difficult, to prevent damage. of smoke and dust.
In emergency welding repairs in highly toxic environments, an insulated oxygen respirator can be used to prevent acute occupational poisoning.
To protect welders' eyes from damage caused by arc light, a face shield with special protective lenses must be worn during welding. Lenses must be selected based on the intensity of the welding current, but the welder's vision and the brightness of the work environment must also be considered.
To avoid skin damage from the electric arc, welders should wear light-colored or white canvas work clothes. The sleeves must be closed tightly, the collar buttoned and no skin must be exposed.
For welding assistants and other people near the welding site, they must cooperate with each other to avoid damage caused by arc light. Assistants must wear appropriately tinted filter glasses.
In operations with multiple people or crossing work areas, protective measures must be taken, such as installing protective screens, to prevent arc light from injuring the eyes of welders and other workers.
In addition, after handling thorium-tungsten rods, hands should be washed with running water and soap, and attention should be paid to regularly cleaning clothing and work gloves. Wearing noise-canceling earmuffs or earplugs can protect against noise hazards. These are all effective personal protection measures.