Ball screws play a crucial role in the power system of machine tools. As the manufacturing industry evolves, the market demands increasingly stringent product quality, pushing companies towards higher precision requirements for machine tools.
Consequently, the reliability and performance of ball screws have become essential standards. In the feeding system, ball screw wear can lead to decreased preload, which is a common problem.
Proper preload can prevent axial impacts and excessive heat, improving the precision and service life of the ball screw. This article will briefly review the problems associated with ball screws and discuss viable predictive maintenance strategies to mitigate wear.
A ball screw is a linear actuator that converts rotary motion into linear motion, widely used in machine tool feed systems. Its main advantage is precise positioning at high speeds, with high mechanical efficiency.
Due to its low friction, its transmission efficiency can reach up to 90%, which also extends the service life of the ball screw and reduces maintenance downtime. Friction and linear impacts between the ball screw and nut make it difficult to achieve an accurate feeding system.
Typically, the right amount of preload is applied to eliminate linear impacts and increase ball screw rigidity. However, excessive preload can increase friction. Preload also plays a significant role in ball screw stiffness, noise and positional accuracy.
When a machine starts or stops, the acceleration or deceleration of the ball screw can lead to loss of lubricating oil at the mating surfaces. This loss can worsen heat dissipation and accelerate ball screw wear. As wear deepens, preload decreases, marking a primary concern for ball screws.
Friction-induced wear in ball screws involves analysis of surface wear. The surface roughness of the ball is smoother than that of the track, so its relative motion can be compared to the interaction between a smooth surface and a rough surface.
If a harder, rougher surface repeatedly strikes in the same direction across a softer surface, unidirectional plastic deformation accumulates with each cycle. This process of “ratchet failure” or “progressive collapse” suggests that wear occurs through a ductile fracture mechanism, producing very fine, plate-like debris, as shown in Figure 1.
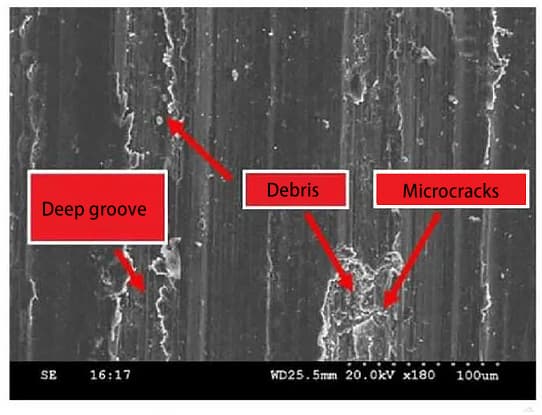
Dynamic testing of ball screws shows that torque initially increases to a high value before starting to decrease. This is because the lubrication film that protects the contact surfaces needs time to form, increasing friction between the ball and track and requiring more torque to drive the ball screw system shaft. As shown in Table 1, with higher speeds requiring more acceleration time, torque increases with speed.
Table 1 Acceleration as a function of rotational speed
Rotation speed (rad/s) | 31.4 | 62.8 | 94.2 | 125.6 | 219.9 | 314.2 |
Acceleration time(s) | 0.036 | 0.055 | 0.076 | 0.099 | 0.16 | 0.215 |
Acceleration (m/s) ²) | 2.78 | 3.63 | 3.95 | 4.04 | 3.75 | 4.65 |
When decelerating, the behavior differs from acceleration, but it also requires greater torque for deceleration. When the speed stabilizes, the torque gradually increases with speed. The difference in torque is relative to similar stable speeds in instantaneous steps, showing that the lubrication regimes during acceleration, deceleration and constant speed are distinct.
Thus, the contact surfaces support significant loads and low relative speeds, leading to critical lubrication problems during acceleration and deceleration.
Predictive maintenance involves using sensors to monitor the operational status of equipment, combining sensor data with lifecycle parameters to determine maintenance timing. This maximizes maintenance intervals and reduces downtime costs.
Predictive maintenance can reduce unexpected mechanical failures and prevent problems from worsening. Early detection and repair of mechanical problems can mitigate most problems, thereby improving product quality and the efficiency of factories and production lines.
Detection methods can be direct or indirect. Direct methods involve directly measuring the operational accuracy and positional status of the component. Indirect methods collect signals and information related to the component to infer its status.
This article focuses on direct methods, where detection signal selection is crucial. Detection signals include acoustic emission signals, laser detection, electrical signal detection, vibration signal detection and machine tool internal signals.
For maintenance of ball screws based on electric motor current, time domain analysis methods are typically used. Wavelet theory represents a new method of analysis in the time domain.
Electrical signals contain many error messages and a significant amount of noise. Wavelet signals can effectively separate signals into different time and frequency bands, eliminating noise signals and reconstructing a clearer signal image.
The collection of current signals uses Hall current sensors, based on the Hall principle of magnetic balance and the closed loop principle, as shown in Figure 2.
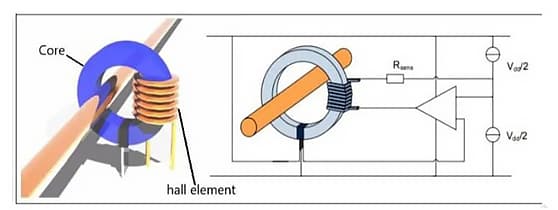
The input current generates a magnetic field that passes through a high-quality magnetic core, forming a magnetic flux loop. The Hall element is fixed in a small air gap. A coil wound around the magnetic core produces a compensating current in the opposite direction.
This compensatory current compensates the magnetic flux generated by the input current, maintaining zero magnetic flux in the circuit. After special circuit processing, the output potential of the Hall element accurately reflects changes in current.
Thus, Hall current sensors can monitor changes in ball screw drive motor current. Processing the collected data can accurately determine the operating status of the ball screw.