I. Performance requirements of aluminum profiles
A. Aluminum materials
1. The following combinations of alloy types and hardness can be used to make aluminum profiles if they meet the requirements of production processing, surface treatment and performance: 6063-T5, 6063-T6, 6105-T5, 6061-T6.
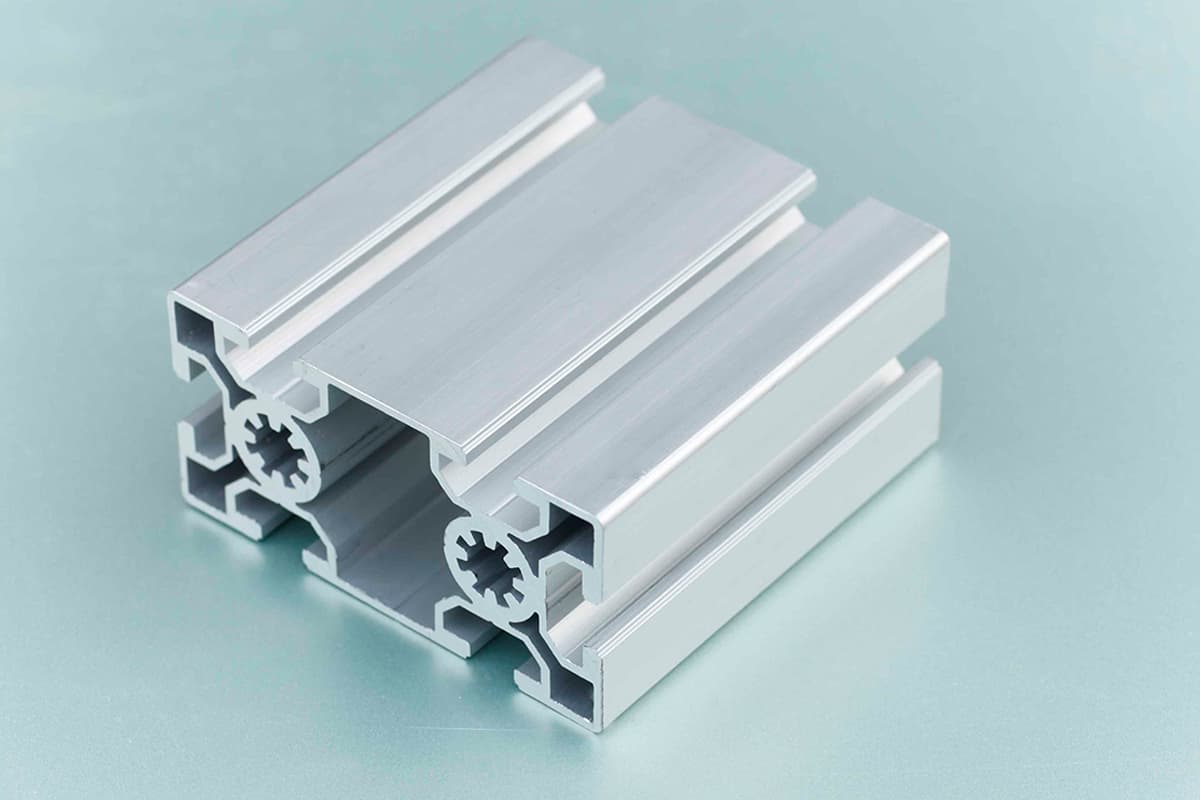
Other 6xxx series alloys can also be submitted for approval if they meet the technical requirements.
The thickness of aluminum profiles should not be less than the following requirements based on performance needs:
The. Aluminum main profiles: 3.0mm.
B. Cover plates and non-structural decorative strips around the glass: 1.5mm.
w. All aluminum profiles must be high-quality construction products, and their permitted processing errors must meet “GB/T 5237 – Regulations for Aluminum Alloy Construction Profiles”. The material must meet the requirements of “GB/T 3190 – Chemical Composition of Deformed Aluminum and Aluminum Alloys.
d. All aluminum profiles submitted must be accompanied by mold drawings showing that the material thickness requirements are met, and these must be archived.
2. The following combinations of alloy types and hardnesses can be used to make aluminum plates or sheets if they meet the processing, surface treatment and performance requirements: 3003-H14, 5005-H14.
Other alloys from the 3xxx, 5xxx or 6xxx series can also be submitted for approval if they meet the technical requirements.
Boards must meet the requirements of “GB/T 5237”.
The thickness of the boards shall not be less than the following requirements based on performance needs:
The. Components formed from aluminum plate: 3.0 mm.
B. Unless specifically required by architectural drawings, the thickness of aluminum plate is 3mm. Reinforcement measures shall be taken as necessary to ensure that the external flatness of the aluminum plate does not exceed 0.1% or 1.5 mm (within 1.5 meters), whichever is less. The thickness of aluminum plates used in roofs and ceilings must be 5 mm.
w. The minimum thickness of the cover plate must be 3.0 mm.
B. Surface Treatment – Aluminum Materials
The color and surface treatment method of the aluminum material must be consistent with the approved submitted samples within the standard color range of the aluminum material manufacturer.
The color and surface treatment of the aluminum must be consistent with samples approved for shipment within the aluminum manufacturer's standard color range.
1. Fluorocarbon spraying or other equivalent practices must be approved by the architect.
2. Exterior Exposed Aluminum
The. All visible exterior aluminum surfaces must have a factory-applied Duranar XL coating, and the fluorocarbon paint used must be based on Kynar 500 fluoropolymer resin supplied by PPG or other authorized formula suppliers. The facade subcontractor must provide written proof of authorization to the owner and architect for review prior to spraying, demonstrating that the paint formula and spraying operations meet the requirements.
B. Duranar XL coating includes three coats and three bakes. The average dry film thickness of PPG primer is 5 to 8 micrometers. The average dry film thickness of Duranar color paint is 25 micrometers. The average dry film thickness of XL Sun Storm clear paint is 10 to 20 micrometers. The total thickness of the dry film must be at least 40 micrometers.
w. Indentations or invisible parts such as internal corners and grooves should also be sprayed as much as possible.
d. Aluminum is usually a certain length before cutting and processing. The facade subcontractor must use appropriate processing equipment to ensure good cutting condition. If the cutting edge is exposed to the external environment, it will need to be treated or sealed to prevent damage to the edge in the coating.
It is. Surface treatment
1) A1-Duranar XL (3 layers) or equivalent product, light silver, consistent with the sample reviewed by the architect.
2) A2-Duranar XL (3 coats) or equivalent product, dark gray, consistent with the sample reviewed by the architect.
3) A3-Duranar XL (3 coats) or equivalent product, grayish blue, consistent with the sample reviewed by the architect.
4) AR1- Roofing system with vertical seam, anodized and embossed treatment. Consistent with architect-reviewed sample.
5) AR1P- 32% perforation rate, 3mm standing seam roof system hole diameter, anodized and embossed treatment. Consistent with architect-reviewed sample.
6) AR4-Duranar XL (3 coats) or equivalent product, color and texture consistent with AR1.
3. Internal and external exposed aluminum materials
The. The aluminum surface is treated with factory-baked PPG fluorocarbon paint.
B. The thickness of the dry film must be at least 60 to 80 micrometers.
w. Recessed or invisible parts, such as internal corners and grooves, should also be sprayed as much as possible.
d. The baking operation must be carried out by a bakery authorized by the formula manufacturer, and the operation must strictly follow the technical requirements for cleaning, priming, coating and quality control. The exterior curtain wall subcontractor must submit written proof of authorization to the owner and architect for review prior to spraying, proving that the paint formula and spray operation meet the requirements.
It is. Surface treatment
1) A4-Duranar (2 coats) or equivalent product, dark gray, according to the sample reviewed by the architect.
2) A5-Duranar (2 coats) or equivalent product, light silver, consistent with sample reviewed by the architect.
4. Surface baking must meet at least the requirements of “AAMA 2605” – Voluntary Specification, Performance Requirements and Test Procedures for High Performance Organic Coatings on Aluminum Extrusions and Panels.
5. Surface baking must meet at least the requirements of “AAMA 2603” – Voluntary Specification, Performance Requirements and Test Procedures for Pigmented Organic Coatings on Aluminum Extrusions and Panels.
6. Surface baking must meet at least the requirements of “AAMA 2604” – Voluntary Specification, Performance Requirements and Test Procedures for High Performance Pigmented Organic Coatings on Aluminum Extrusions and Panels.
7. The color difference of adjacent components treated with the same surface treatment method under normal sunlight should be imperceptible to the naked eye. The exterior curtain wall subcontractor must submit samples that reflect the maximum range of color differences for review by the owner, architect, and design consultant.
8. The external curtain wall subcontractor must establish and present a complete quality control system to ensure compliance with technical requirements. The quality control system must include recorded procedures, steps, tests, etc. The exterior curtain wall subcontractor must maintain complete records of inspections, tests and procedures, and these records must be submitted regularly to the owner, architect and design consultant. Surface treatment should not be performed until this quality control system is reviewed and approved by the owner and architect.
9. Materials that have not been tested and tested in accordance with standards, or whose color difference exceeds the standard color difference range, or materials rejected by the owner or architect, shall not be submitted for review.
10. On-site refinishing of aluminum materials must be authorized in writing by the owner. On-site retouching can only use the “natural air drying” method, as follows:
The. Materials and procedures for on-site touch-up must strictly follow the manufacturer's written instructions.
B. Damaged materials identified by the owner or architect must be replaced.
w. The exterior curtain wall subcontractor should test the entire refinishing process on the sample and send it to the homeowner and architect for review. On-site touch-ups should not be performed until the sample is approved by the owner and architect.
II. Aluminum Profile Production Process

The aluminum profile production process mainly includes three steps: casting, extrusion and coloring (coloring in this project mainly involves anodizing and fluorocarbon spraying).
1. Smelting is the first step in aluminum production.
The process includes:
(1) Mixture of ingredients:
Based on the specific grade of the alloy to be produced, the quantity of each alloy component is calculated and the raw materials are reasonably matched.
(2) Melting:
The prepared raw materials are melted in a furnace according to the process requirements. Impurities and gases in the melt are effectively removed through degassing and slag refining.
(3) Casting:
Molten aluminum is cooled and cast into round rods of various specifications under certain casting conditions through a deep pit casting system.
2. Extrusion is the means of shaping profiles.
The process involves designing and manufacturing molds according to the cross-sectional drawing of the profiled product. Heated round casting rods are then extruded from the mold using an extrusion machine.
The commonly used 6063 alloy undergoes a cooling quenching process and subsequent artificial aging to complete heat treatment strengthening.
Different grades of heat treatable reinforcing alloys have different heat treatment regimes.
3. Coloring
Anodizing: Extruded aluminum alloy profiles have poor surface corrosion resistance and require anodizing for surface treatment to increase the corrosion resistance, wear resistance and aesthetics of the material. The main process includes:
(1) Surface pretreatment:
The surface of the profile is cleaned by chemical or physical methods to reveal a pure base, facilitating the acquisition of a complete and dense artificial oxidation film. A mirror or matte (semi-matte) surface can also be obtained by mechanical means.
(2) Anodizing:
The profile with pre-treated surface undergoes anodization under certain process conditions, forming a dense, porous and strong adsorption AL2O3 film layer.
(3) Sealing:
The pores of the porous oxidation film generated after anodizing are sealed, increasing the anti-pollution, corrosion resistance and wear resistance of the oxidation film. The oxidation film is colorless and transparent.
The strong adsorption of the film before sealing may attract and deposit some metal salts in the pores, allowing the profile surface to display many colors other than natural silvery white, such as black, bronze, gold, stainless steel, etc.
4. Fluorocarbon spraying
Spraying process: spray primer → finishing → varnish → baking (180-250 ℃) → quality inspection.
The multi-layer spraying process generally includes three sprays (also known as tri-coating), including primer, topcoat and varnish, and a two-layer process (primer and topcoat).
1. The purpose of pre-treatment:
Before spraying aluminum alloy profiles and plates, the surface of the part needs to undergo degreasing, decontamination and chemical treatment to form a chromate film, increasing the adhesion of the coating to the metal surface and its antioxidant capacity, which is beneficial to prolong the service life of the paint film.
2. Primer coating:
As a primer layer that seals the substrate, its function is to increase the anti-permeability of the coating, strengthen the protection of the substrate, stabilize the metal surface layer, strengthen the adhesion between the finish and the metal surface, and ensure the uniformity of the finish color. The layer thickness is usually 5 to 10 microns.
3. Finishing layer:
The top coat is the crucial layer in the spray coating process. Provides the decorative color required by aluminum, ensuring the exterior meets design specifications.
Furthermore, it protects the metal surface from external atmospheric conditions, acid rain and pollution. It also prevents the penetration of UV rays, significantly increasing its anti-aging capabilities. The top coat is the thickest layer in the spray coating process, with a typical thickness of 23 to 30 micrometers.
4. Clear Coat Layer:
The varnish layer, also known as the glossy layer, mainly increases the paint's resistance to external erosion. Preserves the finish layer, intensifies the metallic shine of paint colors and makes the appearance more vibrant and attractive.
The coating thickness is typically 5 to 10 micrometers. The total thickness of the three spray layers is generally 40 to 60 micrometers, which can be increased upon special requirements.
5. Healing Process:
The three spray layers generally require secondary curing, where the aluminum enters a curing oven. The curing temperature normally ranges from 180°C to 250°C, and the curing time is 15 to 25 minutes.
Different fluorocarbon paint manufacturers will provide ideal temperatures and times based on their specific paints. Some chlorofluorocarbon spray plants (also known as foundry oil plants) modify the two curing steps in the three-spray process to one, based on their experience.
6. Quality inspection:
Quality inspection must be carried out in accordance with AAMA-605.02.90. Only strict quality checks can guarantee high-quality spray products.