To reduce the cost of loader products, we aim to reduce cutting and molding expenses by improving the utilization rate of essential materials such as cooling water tubes, electrodes, vortex rings, nozzles, nozzle covers, protective caps and Vortex gas caps during plasma cutting. and erasure.
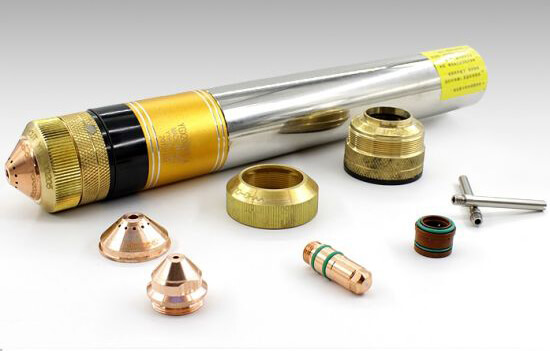
With increasing competition in the market, cost-effective products have become customers' first choice. However, the cost of producing a product, which includes the cost of raw materials, energy consumption, employee salaries, equipment depreciation and production cost, is also increasing. As a result, there is less and less room for the company's profits to increase.
Figure 1 illustrates the composition of the product cost.
To respond to the company's call to “strengthen cost control” and increase profits, it is urgent to reduce the cost of equipment consumables.
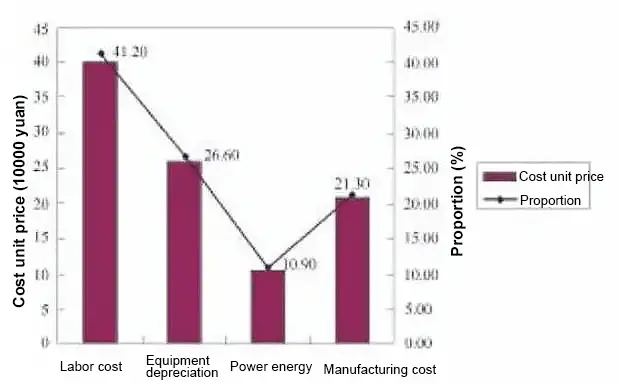
Figure 1 Product cost breakdown
As low-value consumables make up a significant part of the production cost, increasing their utilization rate is one way to increase profit margins.
In plasma cutting, cooling water tubes, electrodes, vortex rings, nozzles, nozzle caps, protective caps and vortex gas caps are essential materials.
Optimizing the use of these materials can lead to a certain degree of product profit improvement.
Plasma cutting head loss classification
After analyzing the consumption of low-value plasma consumables in June, it was concluded that the consumption of electrodes and nozzles is the highest.
To understand the reasons for the high consumption of these two consumables, measures will be taken to improve their use and reduce their consumption.
The main form of electrode damage is depression, as shown in Figure 2a.
The main forms of damage to the nozzle cover and vortex gas cover are burns, round holes and increase in hole diameter, as shown in Figure 2b.
The main forms of nozzle damage are round hole, burnout and increase in hole diameter, as shown in Figure 2c.
The main forms of protective cover damage are deformation, scratches and overdenture, as shown in Figure 2d.
The vortex ring is mainly broken, while the main damage of the cooling water pipe is burned with the weapon.

Fig. 2 Damage to plasma cutting head components
Causes of damage and improvement measures of plasma cutting head
First, let's consider the number of holes required for blanking programming.
During the stamping process, each part must be punched before the material can be arranged according to the shape of the part.
If you want to increase the electrode life, the number of perforations and the cutting length must be reduced. However, the cutting length is directly related to the product design and cannot be changed arbitrarily. Therefore, our focus will be on reducing the number of drillings.
The conventional cutting procedure requires the gun to be started once for each closed contour. Therefore, studying how to combine multiple contours for cutting can significantly reduce the number of perforations.
The improved cutting and cutting procedure is shown in Fig. 3.

Fig.3 Blanking and cutting after improvement
Secondly, the pressure in the plasma pipeline is insufficient. This directly affects the quality of the plasma cutting torch and limits the distance the cutting head can cut. As a result, there is an increased risk of collision damage to the cutting head.
To remedy insufficient pressure, the pump can be set to increase internal piping pressure, which in turn reduces cutting nozzle loss.
By implementing the above measures, the cutting nozzle loss can be significantly reduced, as shown in Figure 4.
After two months of implementing these improvements, plasma cutting head consumable consumption continued to decline.
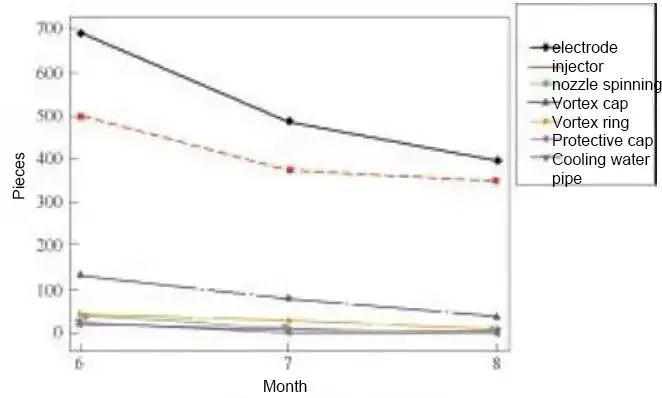
Fig. 4 Plasma cutting head loss trend
During the drilling and hole cutting process, debris often falls into the grid and can cause the cutting gun to fall and damage the motherboard or cutting nozzle. To improve this situation, we have implemented the following measures:
Firstly, when drilling a hole, a flat drop probe automatically adjusts the height. However, this can cause problems when drilling small holes as it is easy to knock the probe.
To solve this problem, we established a small hole database that allows the automatic height adjustment command to be disabled during hole cutting. By doing this, the probe will not fall, reducing the risk of damaging the cutting gun.
In short
After analyzing the causes of loss of plasma cutting head parts, the main factors that influence it were identified: number of perforations, closed contour, piping pressure and cut size.
By implementing appropriate and effective measures, the loss of plasma cutting head parts can be significantly reduced.