Metal laser cutting machines are a crucial tool in the mechanical metal processing and manufacturing industry and are commonly used to replace traditional cutting equipment. However, improper operation or lack of maintenance can lead to various problems with this precision equipment.
A common problem during the cutting process is the phenomenon of not cutting.
To solve this problem, it is important to understand the causes and find appropriate solutions.
Below I will present the causes and solutions for the problem of not cutting with a laser.
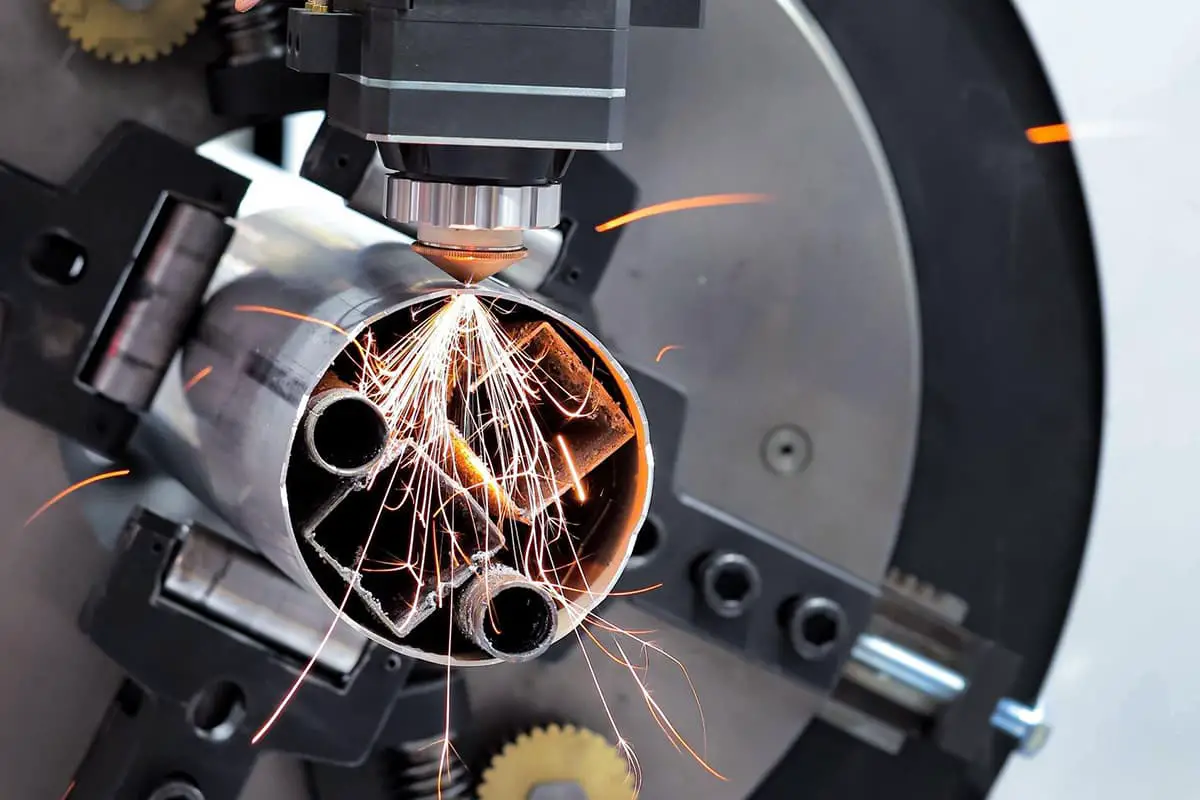
I. Causes for the laser not cutting
Laser cutting is a complex process and can often result in rough incisions or incomplete cuts. There are several reasons why this can occur, including reduced laser power or an aging lamp tube, which leads to insufficient laser beam energy.
Other reasons may include cutting at too fast a speed, damage to the focusing lens, poor focus, incorrect light path, and unstable voltage.
Other factors that can cause rough incisions or incomplete cuts include the material itself, insufficient auxiliary gas pressure, dirty water from the cooling system, and poor heat dissipation.
It is important to take the issue of incomplete laser cuts seriously and work to identify and address the root causes in order to improve production efficiency and ensure high-quality laser cutting.
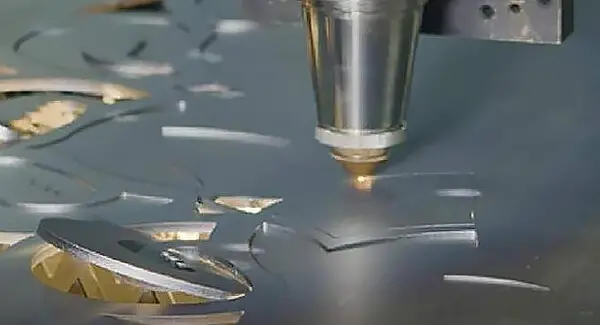
The following is a list of six reasons for laser cutting failure.
- Decreased laser power: Over time, the laser power of a fiber laser cutting machine can gradually decrease, causing a decline in cutting capacity and leading to incomplete cuts.
- Optical element pollution: Optical elements such as focusing lenses and reflectors are susceptible to residue accumulation due to prolonged exposure to poor working conditions, which can reduce laser power and lead to incomplete cuts.
- Poor light spot clearance: The light spot of a fiber laser cutting machine is crucial to the quality of the cut and, if not properly cleared, can result in a lack of clean cuts.
- Excessive cutting speed: If the cutting speed is too fast, it may cause missed cuts and result in incomplete cuts.
- Insufficient Auxiliary Gas Pressure: Auxiliary gas helps remove debris during cutting, and if the air pressure is not sufficient, it can result in clogged cuts.
- Exceeding board thickness limits: Different fiber laser cutting machines have different cutting thickness ranges, and if the thickness of the processed board exceeds the range, it may result in a lack of ideal cutting, including incomplete cuts.
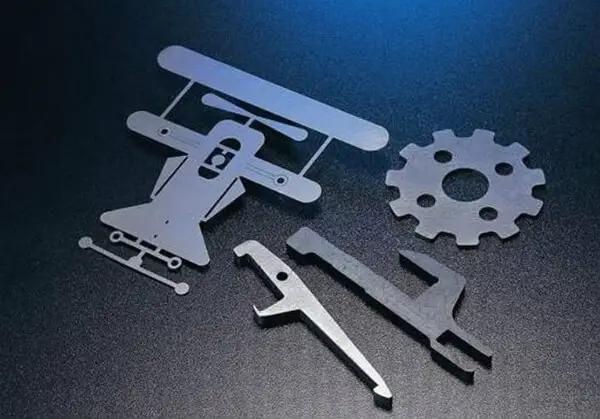
II. Solutions for lasers that don't cut
To solve the problem of laser power decline and low current, it is recommended to replace the laser tube and use a larger voltage regulator to increase the laser current output and increase the output power.
To avoid incomplete cuts, it is important to reduce the cutting speed appropriately and keep optical elements such as mirrors and focusing lenses clean and free from contamination. This may involve timely cleaning or replacement of the lenses.
If there is a problem with the light path, readjust it and adjust the focal length until the laser beam creates a circular spot on the paper.
For cutting materials such as copper and aluminum, which have a high reflection rate, it may be beneficial to polish the surface or apply a light-absorbing material beforehand.
Regular maintenance, such as cleaning the nozzle of foreign matter and increasing auxiliary gas pressure, as well as timely replacement of distilled water in the cooling system, can also help improve cut quality and reduce the risk of incomplete cuts . polite.
These measures can effectively solve the problem of the sample not being cut, and we hope they will help you. If you encounter problems that cannot be resolved alone, it is important to inform your supplier immediately so that professional after-sales personnel can carry out further investigation, examination and maintenance.
III. Fiber laser cutting machine maintenance
Use a vacuum cleaner to remove dust and dirt from the machine once a week, and be sure to keep all electrical cabinets closed to prevent dust accumulation.
Regularly check the steel belt tension of the fiber laser cutting machine. Loose belts can cause operational problems and even pose a safety risk. While it may seem like a small detail, it's still important to keep your belt tight.
Inspect the straightness of the laser cutting machine track and the verticality of the machine every six months, and carry out timely maintenance and debugging if any problems arise. Neglecting these checks can result in poor cut quality and increased errors, which affects the overall cut quality.
The dual focal length laser cutting head is a vulnerable component that can be damaged over time with prolonged use.
Regularly clean the guide rails of the fiber optic laser cutting machine to remove any dust or debris and ensure normal operation. Clean the rack frequently and add lubricating oil to keep it free of debris. Regularly clean and lubricate the guide rail and motor to improve machine movement and cutting accuracy, resulting in better quality of the cut product.