1. Laser drilling technology
1. Physical mechanism of laser drilling
When a metallic material is irradiated by a laser with a power density of 10 6 -10 9 C/cm 2 due to the high power density of the laser, the surface temperature of the material will exceed the boiling point, resulting in melting or vaporization, and the oxidized mixture split on the surface will be ejected.
At the end of the laser pulse, the laser power density decreases and the split jet weakens.
With the injection of fission products, vaporization occurs at a certain speed.
The grade moves toward the inside of the material, the material is vaporized and removed, and the hole is gradually deepened.
As the diameter and depth of the hole increase, the fission products are successively removed by steam pressure and finally a deep hole is formed.
Laser drilling classification
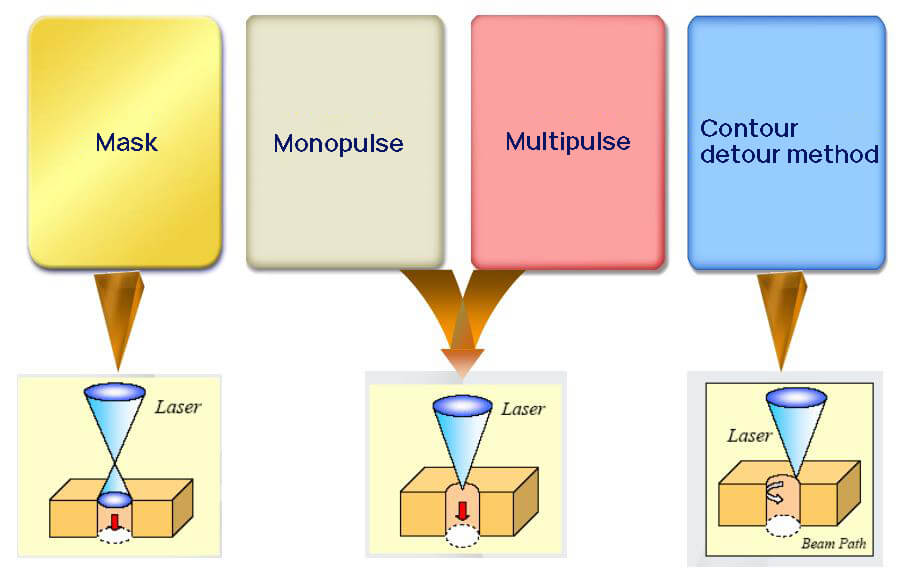
2. Influencing factors of laser drilling
(1) Pulse energy
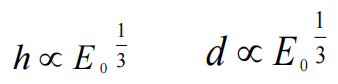
Primary gasification depth:
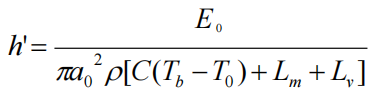
L i and l v are the latent heat of fusion and vaporization of materials, respectively.
At this time, the mass of material removal is πa 0 2 d'ρ.
C: Specific heat capacity
T b : Melting point temperature
T 0 : Room temperature
E 0 : Pulse energy
Ignore heat conduction and surface emission.
(2) Pulse width
Energy/J | Pulse width/ms | Hole depth/mm | Opening/mm | Depth diameter ratio |
5.4 5.1 5.9 5.7 5.4 5.0 |
0.25 0.35 0.55 0.75 0.85 1.15 |
1.2 1.3 1.5 1.6 1.8 1.6 |
0.42 0.39 0.38 0.36 0:30 0.26 |
2.9 3.3 3.9 4.4 6.0 6.1 |
Pulse width selection depends on hole requirements:
- Long pulses should be used to drill deep and small holes;
- When drilling large, shallow holes, shorter pulses should be used;
- Short pulses should be used for high-quality holes;
- For materials with low thermal conductivity, shorter pulses should be used.
With increasing pulse width, more heat is used for non-destructive heating of materials, resulting in large deformation of materials, large thermal stress and easy cracking.
Generally, pulse width of 0.3-0.7 ms is used.
(3) Pulse waveform
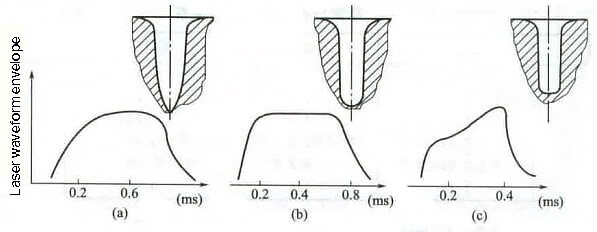
The waveform with steep front and back edges and gradually increasing laser light intensity should be selected as far as possible.
Generally, the front edge of the laser should be controlled within 8~10us to obtain better input, and the trailing edge less than 8us can obtain high inner wall quality.
Especially for small holes less than 50us, the trailing edge gradient is increased to prevent the hole from being blocked by liquid substances.
(4) Laser mode
The laser divergence angle mainly affects the aperture difference and taper at the inlet and outlet.
Generally, with the increase of the divergence angle, the taper of the hole increases and the diameter of the laser beam focused spot also increases.
Approximate focus radius formula:
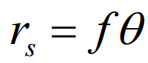
Approximate depth of focus formula:
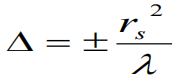
The lower the mode, the smaller the divergence angle.
The divergence angle of the base matrix is the smallest.
The taper of the base die drilling should be small.
(5) Focusing conditions (focus and defocus amount)
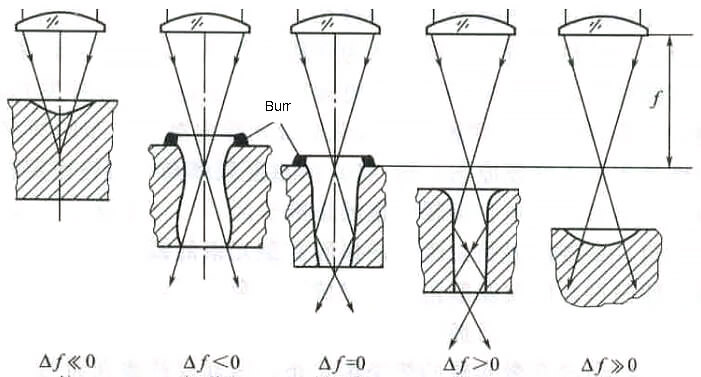
The influence of the amount of defocus △∫ on the shape of the hole wall
- If the focus is on the surface of the part, the taper is large;
- If the focus is in the middle of the part, the drilling quality is good or bad;
- If it is a certain positive blur, the punching effect is good.
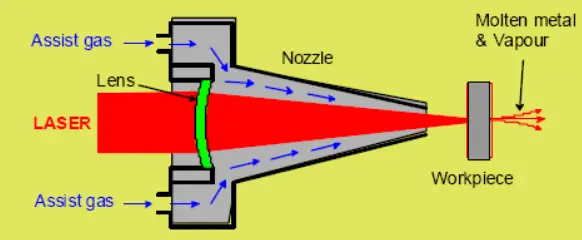
(6) Material characteristics (physical characteristics, overall dimensions)
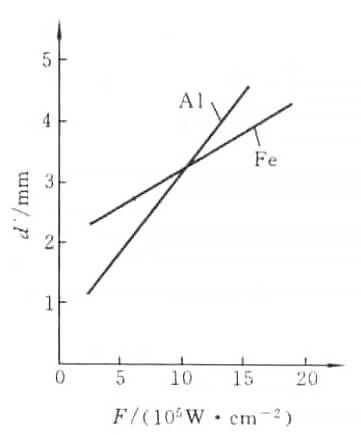
When the laser power density F is low, the thermal diffusion loss of aluminum is greater than that of iron, and the hole depth of aluminum is smaller than that of iron.
With the increase of F, the material will quickly reach the boiling point and the heating rate will be fast.
At this time, heat conduction loss can be ignored.
Because aluminum has latent heat of vaporization, the vaporization removal amount of aluminum is greater than that of iron, therefore the hole depth of aluminum is deeper than that of iron.
The laser pulse with high power density should be used for drilling.
(7) Multipulse drilling
The hole depth of single pulse drilling is limited, only 3 to 4 times the hole diameter, and the accuracy and repeatability are difficult to control.
Generally, multipulse drilling is used.
Multi-pulse drilling can control unstable factors such as hole shape distortion, heat-affected zone expansion, and surface cracks.
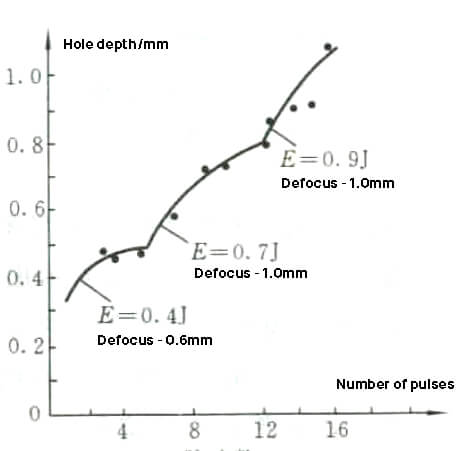
(8) Laser drilling auxiliary technology
Improve hole shape:
(a) Liquid film with low surface tension is coated to reduce deposit and hole taper.
(b) Cover the shielding layer so that the taper of the laser drilling is on the shielding layer.
(c) Blow compressed air to improve surface quality.
(d) A reflector is installed under the workpiece.
(e) Multipulse drilling, periodically focusing the laser beam at a certain position at the bottom of the hole.
(f) After laser drilling, auxiliary correction.
3. Features and application of laser drilling
Quality advantage | Technical characteristics | P practical application |
1. The laser can make small, deep holes | The laser focusing diameter can reach 0.3mm | Special nozzles and cooling channels |
2. Drill oblique holes and special-shaped holes on the inclined plane | Aerial laser transmission | Turbine Engine Blade Drilling |
3. Drill extremely hard ceramic parts | No technical difficulties in laser drilling of ceramic holes | High temperature resistant flame nozzle for steel industry |
4. High drilling precision and reliable performance | No tool wear during laser drilling | Gas engine nozzle drilling |
5. Laser drilling of high-density small holes | Laser can be used for drilling with high speed flying method | Precision chemical industry, pharmaceutical sieve plate |
Laser drilling application examples:
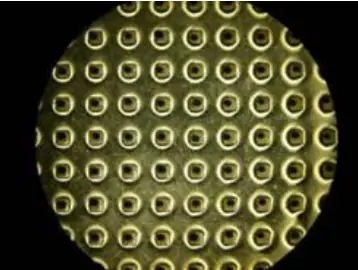
Ceramic Φ 0.5mm hole
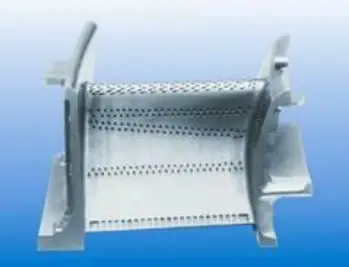
Motor blade Φ 0.5mm small hole
Laser drilling of aircraft components :
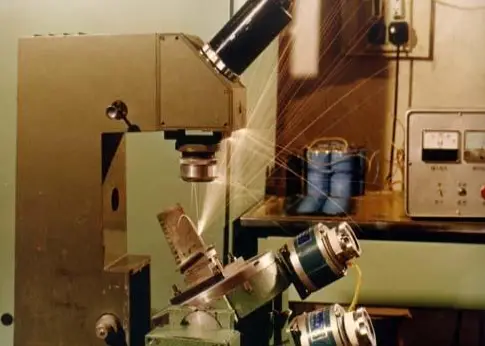
2. Laser cutting technology
1. Principle and classification of laser cutting
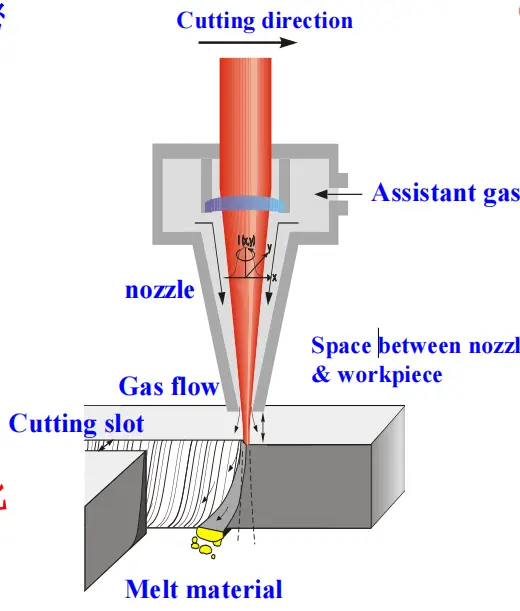
Laser cutting consists of irradiating the workpiece with a focused laser beam of high power density.
On the premise that the laser power density exceeds the laser limit, the laser beam energy and the thermal energy of the chemical reaction added in the active gas-assisted cutting process are all absorbed by the material, which causes the temperature of the laser operating point increases sharply.
After reaching the boiling point, the material begins to vaporize and form holes.
With the relative movement of the beam and the workpiece, the material finally forms a crack, and the slag in the crack is expelled by a certain amount of auxiliary gas.
Laser cutting can be divided into vaporization cutting, fusion cutting and oxygen combustion cutting.
Oxygen combustion support cutting is the most widely used.
From laser cutting of different materials, it can be divided into metal laser cutting and non-metal laser cutting.
Related Reading: Laser Cutting Basics
(1) Steam cutting
Vaporization cutting refers to the laser beam heating the part to a temperature above the boiling point.
Some materials escape as vapor and some materials are expelled from the cutting bottom as jets.
The laser cutting energy required is 10 times that of fusion cutting.
The mechanism is as follows:
① The laser heats the material, partially reflecting and partially absorbing, and the material's reflectivity decreases with increasing temperature.
② The temperature rise in the laser action zone is fast enough to prevent melting caused by heat conduction.
③ Steam quickly escapes from the surface of the workpiece at approximately the speed of sound.
Vapor cutting is only applied to materials such as wood, plastic and carbon that cannot be melted.
Femtosecond laser cutting belongs to gasification cutting.
(2) Fusion cutting
Fusion cutting occurs when the power density of the laser beam exceeds a certain value, the inner part of the workpiece evaporates to form a hole, and then blows auxiliary inert gas with the optical axis to push the molten materials away around the hole.
The merging and cutting mechanism is:
① When the laser beam irradiates the workpiece, the remaining energy except reflection heats the material and evaporates into holes.
② Once the hole is formed, it absorbs all the light energy with a black body, and the hole is surrounded by a wall of molten metal. The cast wall is kept relatively stable by the high-velocity steam flow.
③ The fusion isotherm passes through the workpiece and the molten material is expelled by auxiliary blowing.
④ With the movement of the workpiece, the small hole moves horizontally through a slot.
(3) Oxygen combustion supporting cutting
The oxygen-assisted melting and cutting mechanism is:
① Under laser irradiation, the material reaches temperature Tm and comes into contact with oxygen, which causes violent combustion reaction and emits a lot of heat.
Under the combined action of the laser and this heat, a small hole filled with vapor is formed in the material, and the surrounding of the hole is surrounded by molten gas;
② The steam flow causes the surrounding molten metal wall to move forward, and heat and material transfer occurs;
③ The combustion speed of oxygen and metal is limited by the conversion of combustion materials into slag.
The rate of diffusion of oxygen through the slag to the ignition front. The greater the oxygen flow rate, the faster the chemical combustion reaction will be;
④ In the area that does not reach the combustion temperature, the oxygen flow acts as cooling to narrow the zone affected by cutting heat.
⑤ There are two heat sources, laser radiation and chemical reaction heat, in oxygen-assisted cutting.
Related Reading: Types of Laser Cutting Methods
2. Factors influencing laser cutting
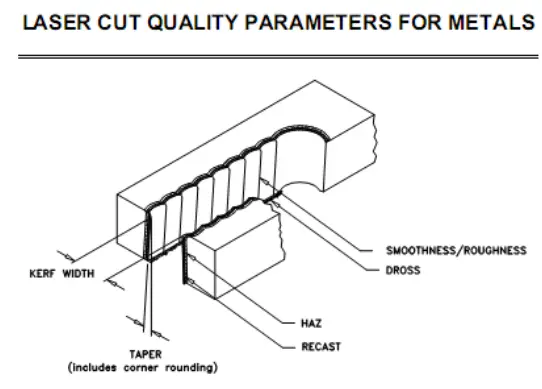
(1) Material properties
PROCESSING CAPACITY SUMMARY
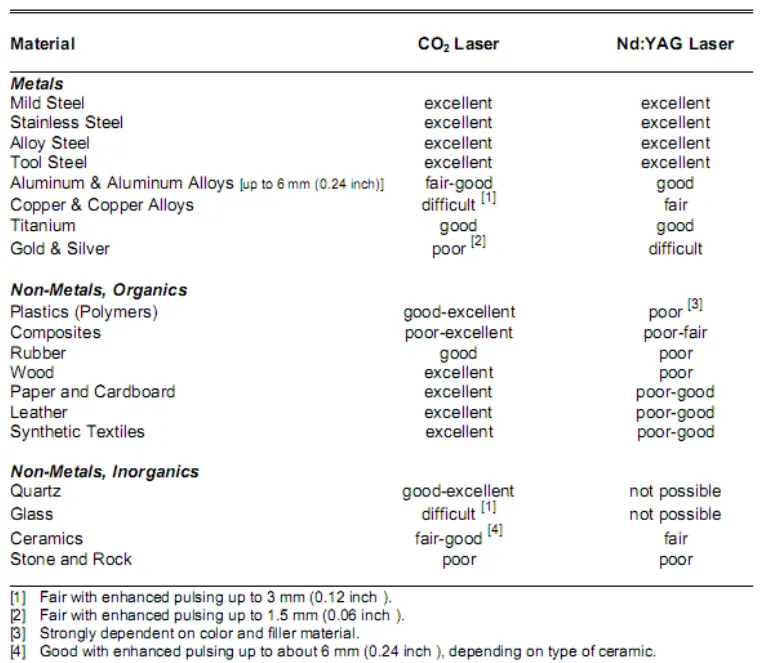
(2) Laser mode
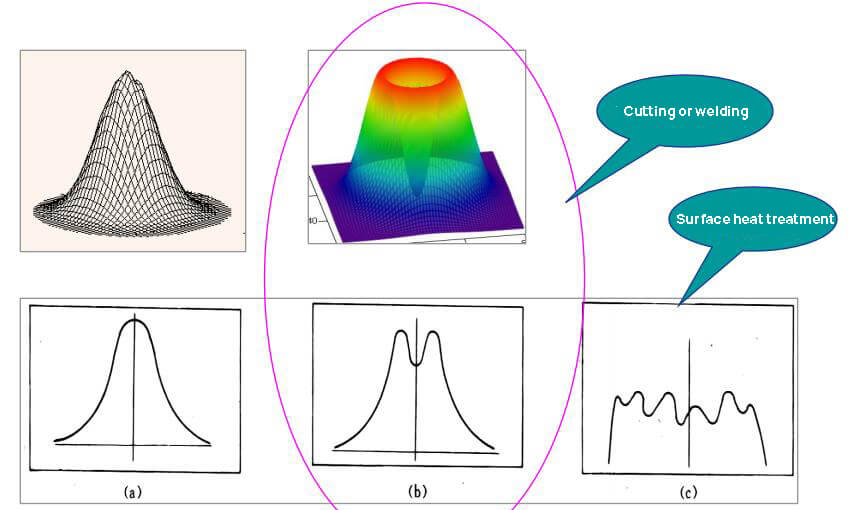
(a) Gaussian mode (b) Lower order mode (c) Multimodal
(3) Laser power and cutting speed
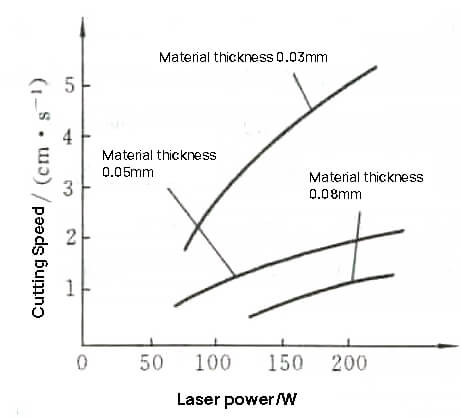
Relationship between cutting speed and laser power, sheet thickness
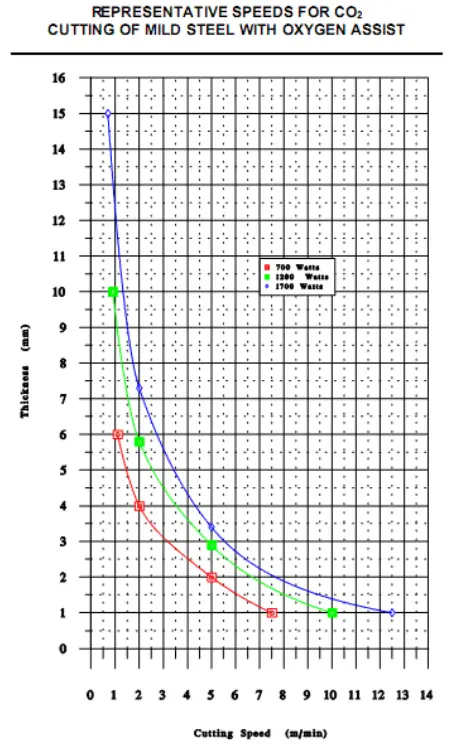
For a given sheet thickness, laser cutting speed generally increases linearly with laser power.
(4) Notch and roughness
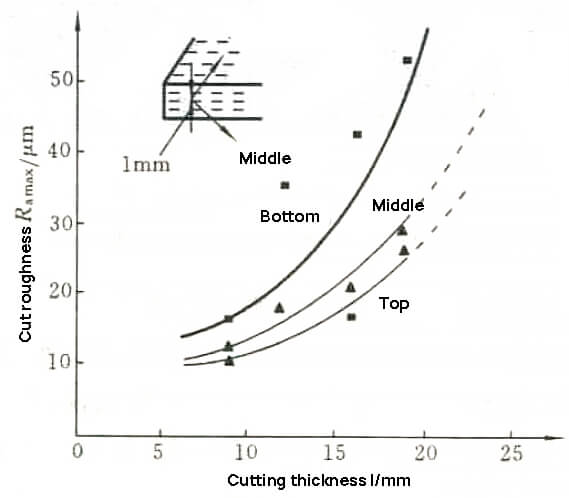
Relationship between notch roughness and cutting thickness
For incision roughness in metal laser cutting, the upper half is generally the best, the middle section is second, and the lower section is poor.
The roughness of the notch is related to the notch cut.
(5) Focus position
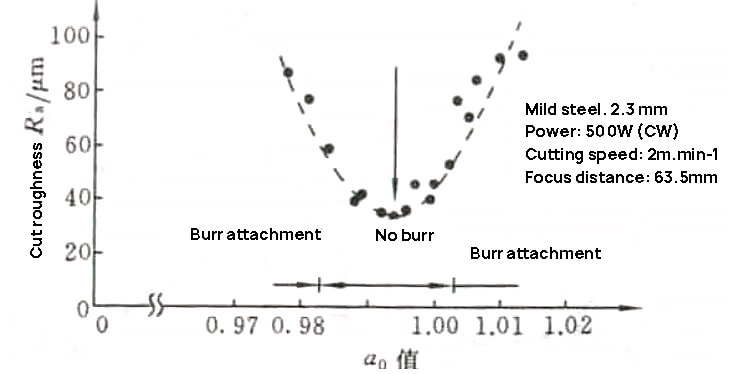
The relationship a0 between the distance from the workpiece to the focusing lens and the focal length is 0.988
For example, when laser cutting a 2.3mm low carbon steel plate, it is best to use negative defocus of 0.3 to 0.7mm.
(6) Focusing mirror
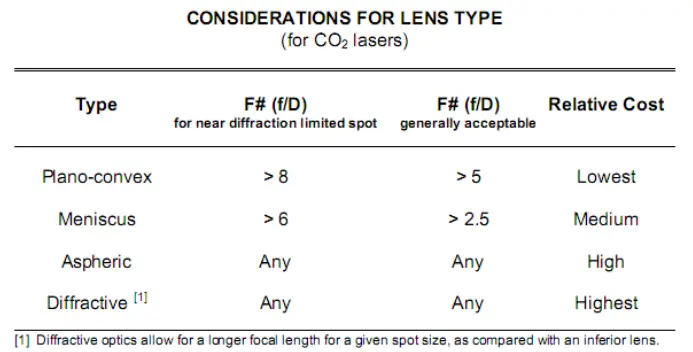

(7) Nozzle diameter
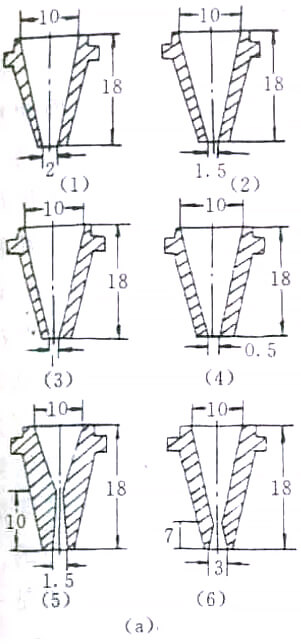
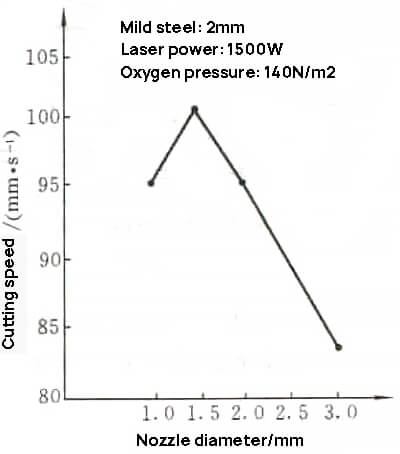
The oxygen flow must be a supersonic convergent air flow to prevent expansion of the lower section of the incision.
There is an ideal nozzle diameter for a specific laser cut. In the figure, 1.5 mm is the best nozzle diameter.
(8) Oxygen blow pressure
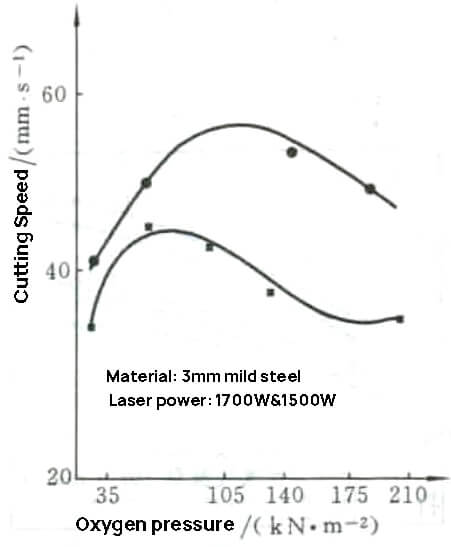
Relationship between oxygen blowing pressure and cutting speed
At different laser powers and thicknesses, there is an optimal value of oxygen blowing pressure.
(9) Laser polarization
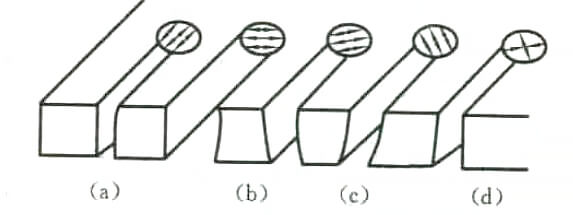
The state of the incision obtained by different polarized lights
(a) Linear polarized light;
(b) Linear polarized light;
(c) Linear polarized light;
(d) Circularly polarized light.
As can be seen in the figure, circular polarized light is used and the incision is straight, regardless of the cutting direction.
The cutting system is generally equipped with a circular polarizer with a 45-degree reflection.
Related Reading: Factors Affecting Laser Cutting Quality
3. Features of laser cutting
Quality advantage | Technical characteristics | Practical application |
1. The heat affected zone at the edge of the cutting joint is small | Less total energy required for laser cutting | Silicon Steel Core Cutting for Large Motor |
2. The laser cutting slit is narrow | High energy concentration in laser cutting | Cutting the oil pipe filter gasket |
3. High cutting precision and small deformation of the workpiece | The diameter of the laser focusing spot is small | Cylinder gasket cutting and shaping |
4. Good cutting repeatability and small error | CNC precision cutting | Cutting complex shaped parts |
5. The laser cutting surface is clean and free of slag | Perfection of the physical metallurgical cutting process | Cutting with a diamond saw blade for decoration |