1. What is welding voltage
Welding voltage refers to the voltage generated during the welding process in welded components. This stress is caused by the thermal process of welding and the resulting internal stress and changes in the shape and size of the weldment.
The root cause of welding stress and deformation is the uneven temperature field during welding and the resulting local plastic deformation and differences in microstructure with varying specific volumes.
Transient welding stress and strain occur when the welding temperature field has not yet dissipated. On the other hand, welding residual stress and strain refers to the stress and strain that remain after the welding temperature field dissipates.
In the absence of external forces, the welding stress is balanced within the weldment. However, under certain conditions, welding stress and deformation can affect the functionality and appearance of the weldment.
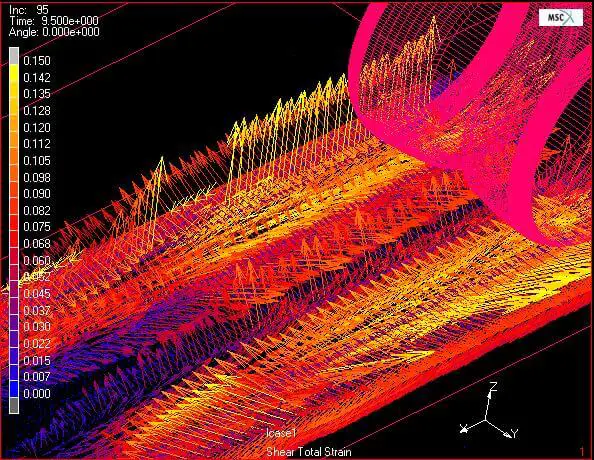
2. Welding stress hazards
Welding residual stress has six effects on welds:
① Effect on strength:
Severe defects in areas with high residual tensile stress can negatively impact the static load resistance of the weldment if it operates below the brittle transition temperature. The presence of residual tensile stress at stress concentration points under cyclic stress will reduce the fatigue strength of the weld.
The fatigue resistance of welds depends not only on the magnitude of the residual stress, but also on factors such as the stress concentration factor, the characteristic coefficient of the stress cycle and the maximum value of the cyclic stress. The influence of residual stress decreases as the stress concentration factor decreases and intensifies as the characteristic stress cycle coefficient decreases, but decreases as the cyclic stress increases.
When the cyclic stress approaches the yield point, the effect of residual stress gradually decreases.
② Effect on stiffness:
The combination of residual stress from welding and stress from external loads can result in premature yielding and plastic deformation in specific areas of the weld. This will result in a reduction in welding stiffness.
③ Influence on pressure welding stability:
When a welded rod is subjected to pressure, residual stress from welding combines with stress from external loads, potentially causing yielding or local instability and reducing the overall stability of the rod.
The impact of residual stress on stability depends on the geometry and distribution of internal stress in the member. The influence of residual stress on unclosed sections such as I-sections is greater than its influence on closed sections such as box sections.
④ Influence on machining accuracy:
The presence of welding residual stress can affect the machining accuracy of weldments to varying degrees. The lower the welding stiffness, the greater the amount of machining and the greater its impact on accuracy.
⑤ Influence on dimensional stability:
Weld residual stress and weld size change over time and this can affect the dimensional stability of the weld. Residual stress stability also influences the dimensional stability of the weld.
⑥ Effect on corrosion resistance:
The combination of welding residual stress and loading stress can result in stress corrosion cracking.
Influence of welding residual stress on the structure and bar:
Welding residual stress is the initial stress in a member before it supports any load. During use of the bar, the residual stress superimposes on the working stress caused by other loads, leading to secondary deformation and a redistribution of the residual stress.
This not only decreases the stiffness and stability of the structure, but also significantly impacts its fatigue resistance, resistance to brittle fracture, stress corrosion cracking and high temperature creep cracking under the combined effects of temperature and environment.
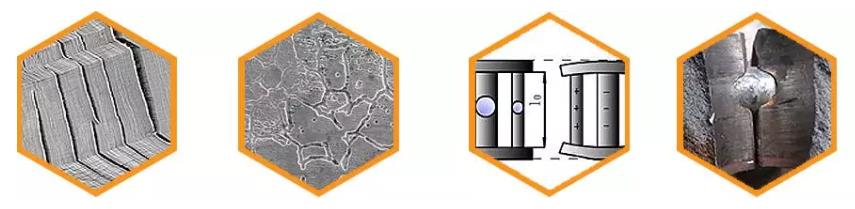
3. Measures to reduce and eliminate welding stress
Welding stress can be minimized through comprehensive design and process consideration. When designing a welding structure, welding joints with lower rigidity should be adopted, the quantity and cross-sectional size of welds should be minimized, and excessive concentration of welds should be avoided. The following measures can be taken in terms of the process:
1) Reasonable selection of welding sequence and direction.
Determining the welding sequence should allow the weld to contract freely as much as possible to reduce stress. The welding stress generated by the sequence shown in Figure 4-10a is small, while in Figure 4-10b, weld bead 1 first increases the restraint on weld bead 2, thereby increasing the residual stress.
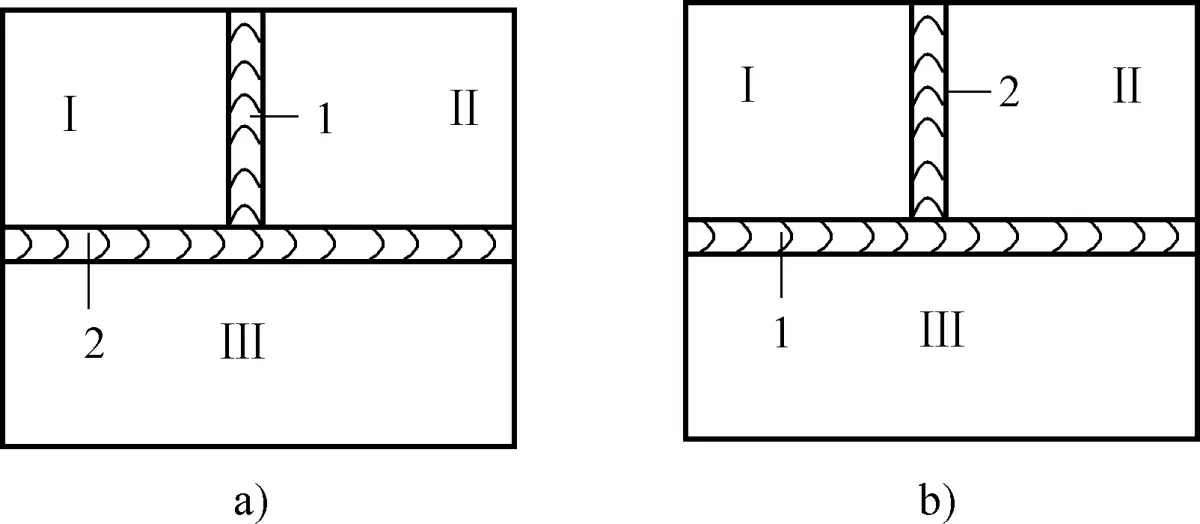
a) Minimum welding voltage, b) Substantial welding voltage.
2) Hammer the weld.
During the weld cooling process, use a round-head hammer to strike the weld evenly and quickly, causing local plastic elongation deformation of the weld metal, compensating for part of the welding shrinkage deformation, thereby reducing the residual stress of welding.
3) Warming up the “stress reduction zone”.
Before welding, heat an appropriate part of the part (known as the stress reduction zone) to lengthen it (Figure 4-11). After welding, during cooling, the stress reduction zone and the weld shrink in the same direction, reducing the stress and deformation of the weld.
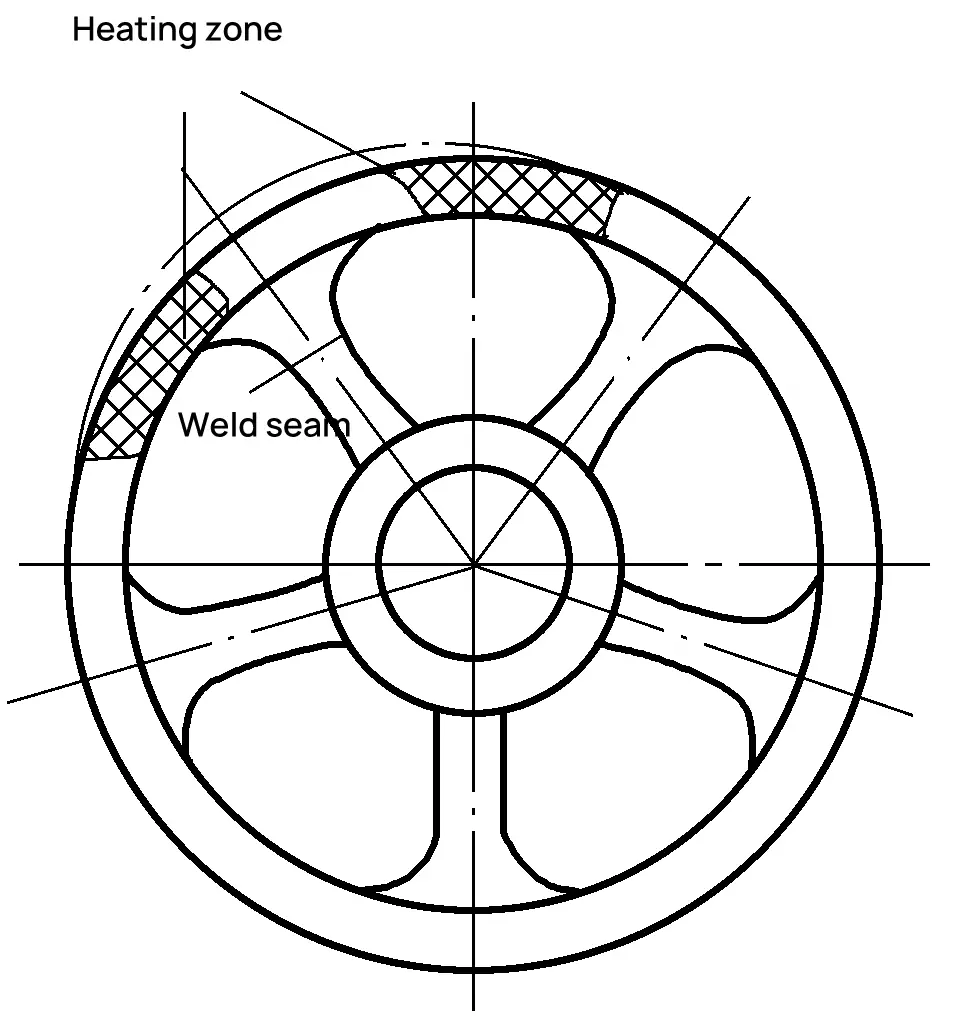
4) Preheating before welding and slow cooling after welding.
The purpose of preheating before welding is to reduce the temperature difference between the welding zone and the surrounding metal, slow down the cooling rate of the welding zone, and reduce uneven expansion and contraction during welding heating and cooling, reducing thus the welding stress. Slow cooling after welding can have the same effect.
However, this method complicates the process and is only suitable for materials with low plasticity and prone to cracking, such as high and medium carbon steel, cast iron and alloy steel.
5) Post-welding stress relief annealing.
In order to eliminate welding residual stress in the welding structure, stress relief annealing is commonly used in production. For carbon steel and low to medium alloy steel structures, the entire component or part of the welding joint can be heated to 600-800°C after welding and slowly cooled after being kept at this temperature for a certain period of time. Generally, more than 80% of the welding residual stress can be eliminated.
4. Measures to control and reduce welding deformation
To control welding deformation, the size and shape of welding seams should be reasonably selected during the design of the welding structure, the number of welding seams should be minimized as much as possible, and the arrangement of welding seams should be symmetrical . In the production of welded structures, the following techniques can normally be applied:
Addition of subsidy method :
Based on theoretical calculations and empirical values, the shrinkage tolerance is considered in advance during the preparation and processing of welded parts, so that the part can reach the required shape and size after welding.
Counterdeformation method :
Based on experience or measurement, the size and direction of welding structural deformation are estimated in advance. During assembly of the welding structure, an intentional deformation is created in the opposite direction but of equal magnitude to compensate for the deformation produced after welding (see Figure 4-12).
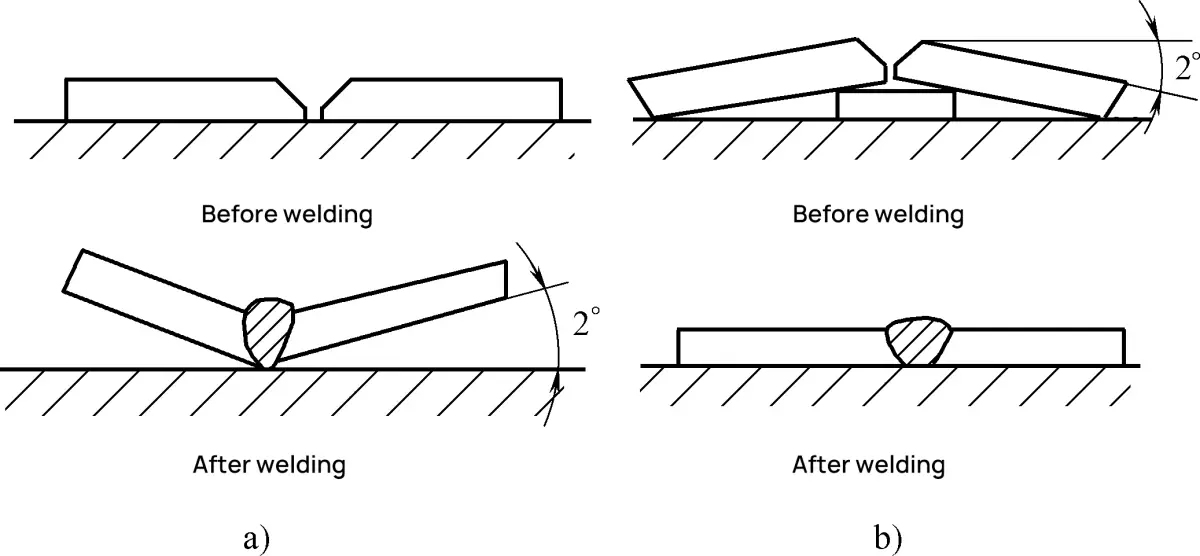
a) Creation of angular deformation
b) Neutralization of angular deformation
Rigid fixing method :
The welded parts are clamped during welding, and the rigid fixation is removed after the welded parts cool to room temperature. This can effectively prevent angular deformation and wavy deformation, but increases welding stress.
This method is only suitable for low-carbon steel structures with good plasticity and should not be used for cast iron and steel materials with a high tendency to harden to avoid post-welding fractures. Figure 4-13 shows the use of the rigid clamping method to prevent angular deformation of the flange face.
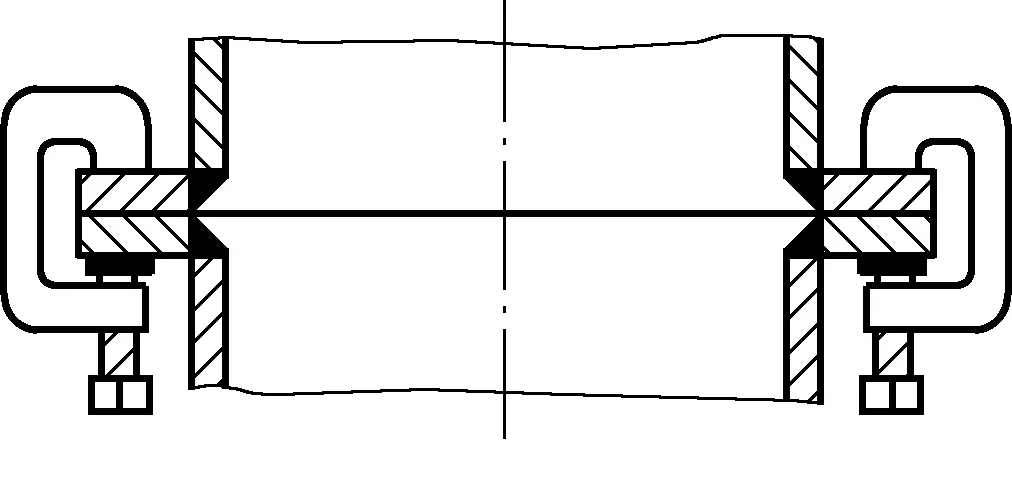
4) Choose an appropriate welding sequence.
Selecting a reasonable welding sequence is essential to control welding deformation. For welding of symmetrical section beams, the welding sequence shown in Figure 4-14 can effectively reduce welding deformation.
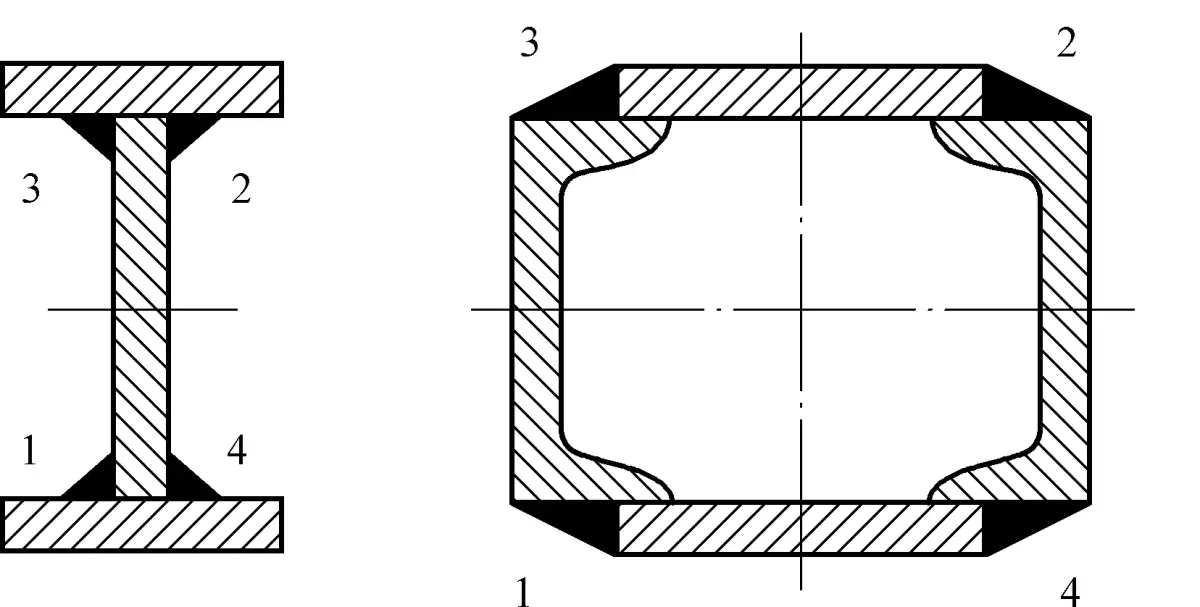
For workpieces with an uneven distribution of welds, such as the overhead crane main beam shown in Figure 4-15, a sensible welding sequence is to have two workers simultaneously and symmetrically weld the 1-1′ seams first, followed by the 2- 2′ seams and finally the 3-3′ seams. In this way, the upward deflection caused by welding 1-1' can be essentially compensated by the downward deflection caused by welding 2-2 and 3-3.
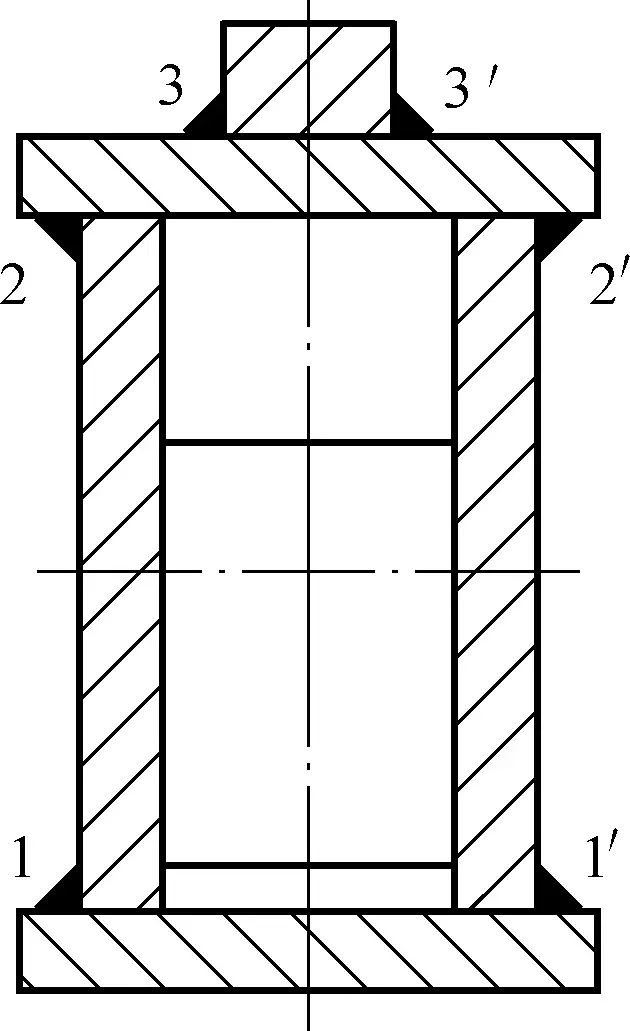
5. Welding Deformation Correction
During the welding process, even when the measures mentioned above are taken, deformations that exceed the permissible value may sometimes occur. Commonly adopted methods to correct welding deformation include:
1) Mechanical correction.
Mechanical correction involves the use of external force to induce plastic deformation in the component in the opposite direction to the welding deformation, thus canceling out each other's deformations (Figure 4-16). This method is normally only suitable for low-carbon steels and common low-alloy steels that have relatively low stiffness and good plasticity.
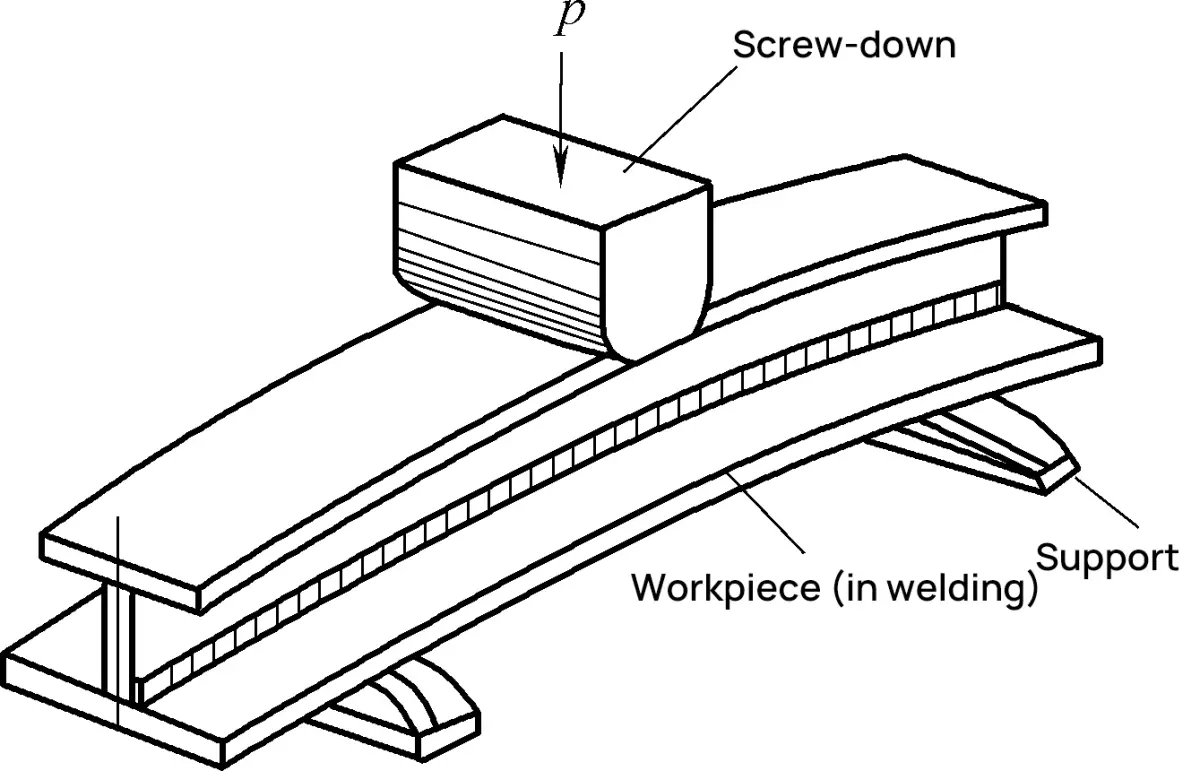
2) Flame correction.
Flame correction uses cooling contraction after local heating of the metal to correct existing welding deformation. Figure 4-17 shows an upward deformation of a T beam after welding, which can be corrected by heating the web position with a flame. The heating zone is triangular and the heating temperature is 600-800°C.
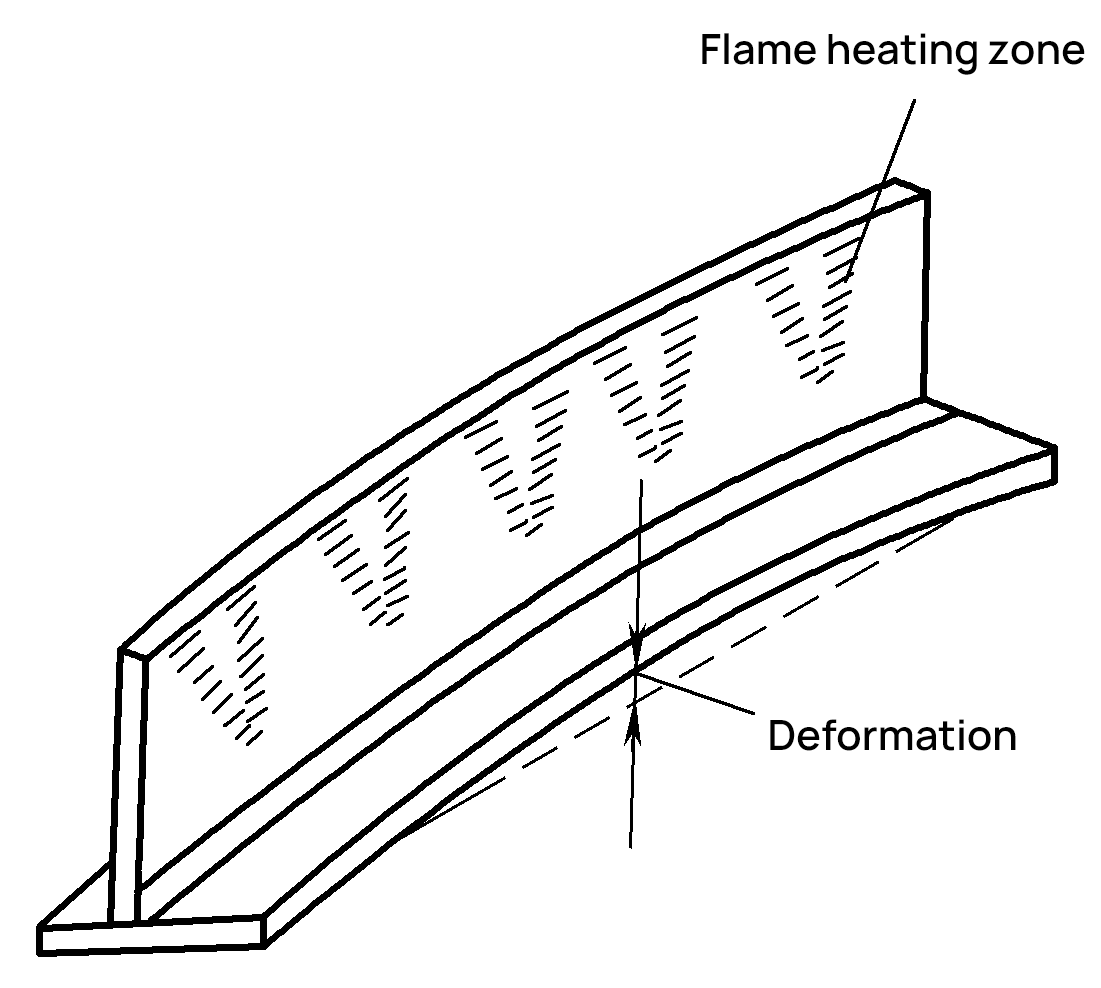
After cooling, the core shrinks, causing reverse deformation and straightening the welded component. This method is mainly suitable for materials with good plasticity and no tendency to harden.
6. Others and welding stress elimination method
(1) Vibrational aging
Vibration aging treatment is a common method for reducing internal residual stress in engineering materials. The process involves subjecting the material to vibration, which causes a small plastic deformation in the material when the combined residual stress and additional vibration stress exceed the yield strength of the material, thereby reducing internal stress.
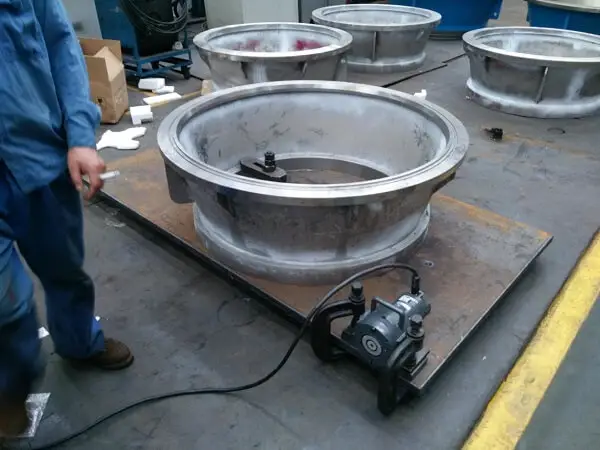
(2) Thermal aging
Thermal aging is a process of reducing the residual stress in a part by heating it to its elastic-plastic transition temperature, holding it at that temperature for a specified period of time, and then slowly cooling it. This process causes the part to be in a low stress state after cooling.
However, if the process parameters for heating, insulation and cooling are not properly selected or if the operating procedures are not strictly followed, the stress elimination process may not be effective and the stress on the workpiece may even increase. This has been demonstrated through production experience.