Element 1: H(Hydrogen)
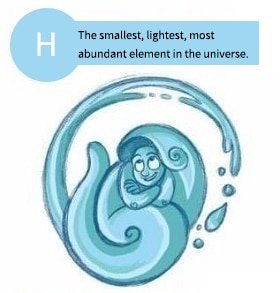
Hydrogen is the most harmful element in steel, and hydrogen solution in steel can cause hydrogen embrittlement and white spots on steel.
Similar to oxygen and nitrogen, the solubility of hydrogen in solid steel is very low. When hydrogen is mixed with liquid steel at high temperatures, it cannot escape in time before cooling and accumulates in the organization, forming high-pressure fine pores. This can cause the plasticity, toughness and fatigue resistance of steel to drastically reduce or even lead to serious cracking and brittle fractures.
Hydrogen embrittlement occurs mainly in martensitic steel, but is not very prominent in ferrite steel. It generally increases along with the hardness and carbon content.
On the other hand, hydrogen can improve the magnetic conductivity of steel, but it also increases coercivity and iron loss. The coercivity can be increased by 0.5 to 2 times after adding hydrogen.
Element 2:(Boron)
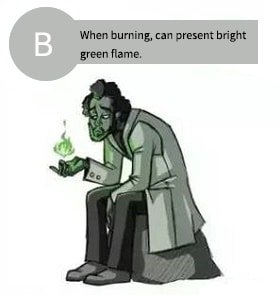
The main function of boron in steel is to increase the hardenability of the steel, thus saving other relatively rare metals such as nickel, chromium, molybdenum, etc. To this end, its content is generally stipulated in the range of 0.001% to 0.005%. It can replace 1.6% nickel, 0.3% chromium or 0.2% molybdenum.
When boron is used to replace molybdenum, it should be noted that although molybdenum can prevent or reduce quench brittleness, boron has a slight tendency to promote it. As such, molybdenum cannot be completely replaced by boron.
Adding boron to carbon steel can improve hardenability, which can greatly improve the performance of steel thicker than 20mm. Therefore, 40B and 40MnB steel can replace 40Cr, and 20Mn2TiB steel can replace 20CrMnTi carburizing steel.
However, due to the weakened or disappeared effect of boron with the increase of carbon content in steel, when choosing steel for boron carburizing, it should be noted that after carburizing the parts, the hardenability of the carburized layer will be lower than that of the core.
Generally, spring steel is required to be fully hardened, and boron steel would be a good choice due to its small spring area. However, the effect of boron on high silicon spring steel is volatile, so it should not be used.
Boron, nitrogen and oxygen have a strong affinity. Adding 0.007% boron into edge steel can eliminate steel aging.
Element 3: C(Carbon)
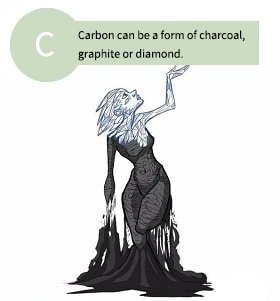
Carbon is the main element after iron and directly affects the strength, plasticity, toughness and welding properties of steel.
When the carbon content in steel is below 0.8%, the strength and hardness of the steel increase with the addition of carbon content, while the plasticity and toughness decrease.
However, when the carbon content is above 1.0%, the strength of the steel decreases as the carbon content increases.
As the carbon content increases, the welding performance of steel decreases (when the carbon content in steel is greater than 0.3%, its weldability decreases significantly). Furthermore, cold brittleness and aging sensitivity increase and resistance to atmospheric corrosion decreases.
Element 4: N(Nitrogen)
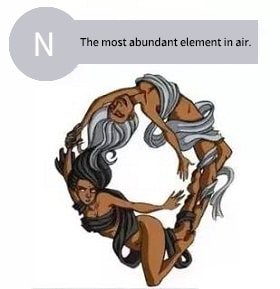
The effect of nitrogen (N) on steel performance is similar to that of carbon and phosphorus. With an increase in nitrogen content, it can significantly improve the strength of steel, reducing its plasticity, especially toughness and weldability, and increasing its cold brittleness.
In addition, the aging tendency, cold brittleness and hot brittleness increase, and the welding and cold bending properties of steel are damaged. Therefore, the nitrogen content in steel must be minimized and restricted.
The nitrogen content should not be more than 0.018%. When combined with aluminum, niobium, vanadium and other elements, nitrogen can reduce their adverse effects and improve the performance of steel. Nitrogen can also be used as an alloying element for low alloy steels.
In some stainless steels, adequate nitrogen content can reduce Cr usage and effectively reduce costs.
Element 5: O (Oxygen)
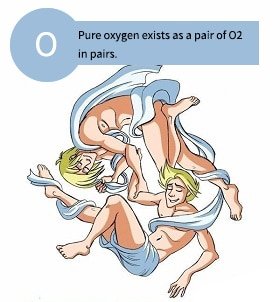
Oxygen is a harmful element for steel. It is naturally present in steel during the steel manufacturing process, making it impossible to completely remove it, even with the addition of manganese, silicon, iron and aluminum at the end of the process.
During the solidification of molten steel, the reactions of oxygen and carbon in the solution produce carbon monoxide, which can cause bubbles.
In steel, oxygen mainly exists in the form of FeO, MnO, SiO2 and Al2O3, which reduces the strength and plasticity of steel. In particular, fatigue resistance and toughness will be seriously affected.
Oxygen will increase the loss of iron in silicon steel, weaken the magnetic conductivity and intensity of magnetic induction, and enhance the effect of magnetic aging.
Element 6: Mg(Magnesium)
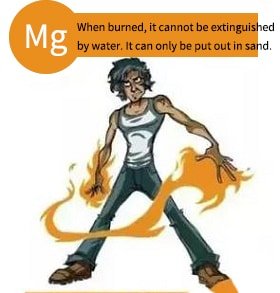
Magnesium (Mg) can reduce the number of inclusions in steel, decrease its size, create an even distribution and improve its shape.
In bearing steel, trace amounts of magnesium can improve the size and distribution of carbides.
When the magnesium content is between 0.002% and 0.003%, the tensile strength and yield strength of the steel increase by more than 5%, while the plasticity remains essentially unchanged.
Element 7: Al(Aluminum)
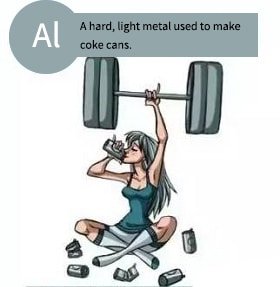
Aluminum, added to steel as a deoxidizer or alloying element, is much stronger than silicon and manganese in terms of deoxidation.
The main function of aluminum in steel is to refine the grains and stabilize the nitrogen, which significantly improves the impact resistance of the steel and reduces the tendencies towards cold brittleness and aging.
For grade D carbon structural steel, the acid-soluble aluminum content in the steel should not be less than 0.015%. For deep drawing with 08AL cold-rolled sheet, the acid-soluble aluminum content in the steel should be 0.015% to 0.065%.
Aluminum can also improve the corrosion resistance of steel, especially when combined with molybdenum, copper, silicon, chromium and other elements.
Aluminum is added to chrome molybdenum steel and chrome steel to increase their wear resistance.
The presence of aluminum in high-carbon tool steel can make the hardening process brittle.
The disadvantage of aluminum is that it can affect the thermal processing properties, welding performance and cutting performance of steel.
Element 8: Si(Silicon)
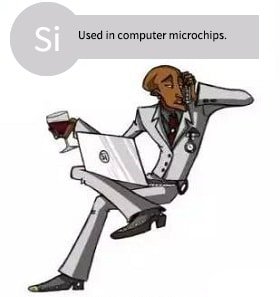
Si is an essential reducing and deoxidizing agent in the steel manufacturing process.
Many carbon materials contain less than 0.5% Si, and this Si is typically introduced during the steelmaking process as a reducing and deoxidizing agent.
Silicon can be dissolved in ferrite and austenite to increase the hardness and strength of steel, which is second only to phosphorus and is stronger than manganese, nickel, chromium, tungsten, molybdenum and vanadium.
However, when the silicon content exceeds 3%, the plasticity and toughness of the steel will be significantly reduced.
Silicon can improve the yield strength, yield strength, yield rate of steel (Os/Ob), as well as fatigue strength and fatigue rate (σ-1/σb), which is why silicon or Silicon manganese steel can be used as spring steel.
Silicon can reduce the density, thermal conductivity and conductivity of steel. It can promote the thickening of ferrite grains and reduce the coercive force.
Silicon can also reduce the anisotropy of the crystal, facilitating magnetization and reducing magnetic resistance, which can be used to produce electrical steel, so the magnetic block loss of silicon steel sheet is low.
Silicon can improve the magnetic permeability of ferrite, so that the steel sheet has a higher magnetic intensity under a weaker magnetic field. But in a strong magnetic field, silicon reduces the magnetic intensity of steel. Silicon has a strong deoxidizing force that reduces the magnetic aging effect of iron.
When heated in an oxidizing atmosphere, silicon steel forms a layer of SiO2 film that improves the steel's oxidation resistance at high temperatures.
Silicon can promote the growth of columnar crystals in molten steel and reduce plasticity.
If silicon steel cools quickly when heated, due to low thermal conductivity, the internal and external temperature difference of the steel is large, which can easily cause the steel to break.
Silicon can reduce the welding performance of steel because it is easier to oxidize than iron. It is easy to generate silicate with a low melting point during welding, which can increase the fluidity of slag and molten metal, cause spatter and affect the welding quality.
Silicon is a good deoxidizer. When aluminum is deoxidized, a certain amount of silicon can be added to significantly improve the deoxidation rate.
Silicon has a certain residue in steel, which is introduced into steel as a raw material. In rim steel, silicon is limited to < 0.07% and, when necessary, silicon-iron alloy is added to steel production.
Element 9: (Phosphorus)
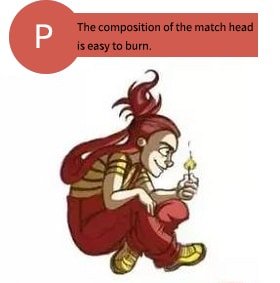
OP is introduced into steel by ore, which is generally considered a harmful element. Although phosphorus can increase the strength and hardness of steel, it significantly decreases plasticity and impact resistance.
Especially at low temperatures, it makes the steel significantly brittle, which is called “cold brittleness”.
Cold brittleness weakens the cold processing and weldability of steel.
The higher the phosphorus content, the greater the cold brittleness, so the phosphorus content in steel is strictly controlled.
High quality steel: P < 0.025%; Quality steel: P < 0.04%; Common steel: P < 0.085%.
P is strong in solid solution strengthening and quench hardening.
When combined with copper, it can improve the atmospheric corrosion resistance of high-strength low-alloy steel while reducing its cold stamping performance;
When combined with sulfur and manganese, P can improve steel machinability, temper brittleness, and cold brittle sensitivity.
Phosphorus can improve ratio resistance and can reduce coercive force and eddy current loss due to coarse grain.
For magnetic induction, the magnetic induction of steel with higher P content will be improved in weak magnetic field.
Hot working of P-containing silicon steel is not difficult, but because P can make silicon steel brittle, its content must be ≯ 0.15% (such as in cold-rolled electrical silicon steel, the P content is 0. 07 ~ 0.10%) .
Phosphorus is the most powerful element in ferrite. (The effect of P on silicon steel recrystallization temperature and grain growth is 4 ~ 5 times that of silicon with the same content.)
Element 10: S (Sulphur)
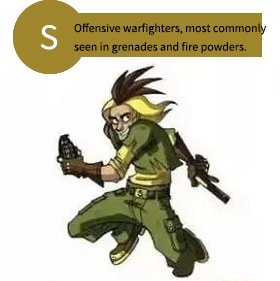
Sulfur is derived from ore and coke fuel used in steelmaking. It is a harmful element to steel.
Sulfur exists in steel in the form of FeS. FeS and Fe form a compound with a low melting point of 985℃. The hot working temperature of steel is generally higher than 1150 ℃. Therefore, during hot working, FeS compounds may melt prematurely, causing the part to break. This phenomenon is called “hot brittleness”. Reduces the ductility and toughness of the steel, causing cracks during forging and rolling.
Sulfur is also detrimental to welding performance and reduces the corrosion resistance of steel. The sulfur content in high-quality steel should be less than 0.02% to 0.03%, in low-quality steel less than 0.03% to 0.045%, and in ordinary steel less than 0.055% to 0.7%.
Sulfur can be used in the production of steel parts that require low capacity and greater surface brightness, known as fast-cutting steels, such as Cr14 with a small amount of sulfur intentionally added (0.2% to 0.4%). Some high speed steels and tool steels use S to process the surface.
Element 11 and 12: K/Na(Kalium / Natrium)
K/Na can be used as a modifier to spheroidize the carbides in white iron, improving its toughness by up to two times while maintaining its hardness.
They can also refine the structure of ductile iron and stabilize the production process of vermicular iron.
Furthermore, K/Na are effective elements to promote austenitization. For example, they can reduce the manganese/carbon ratio of austenitic manganese steel from 10:1-13:1 to 4:1-5:1.
Element 13: Ca(Calcium)
Adding calcium to steel can refine its grain, partially desulfurize it, and change the composition, quantity, and shape of nonmetallic inclusions, similar to adding rare earths to steel.
This can improve the corrosion resistance, wear resistance, high and low temperature performance of steel, as well as its impact resistance, fatigue resistance, plasticity and welding properties.
Furthermore, the addition of calcium can improve the cold heading, shock resistance, hardness and contact resistance of steel. In cast steel, the addition of calcium increases the mobility of the cast steel, improves the surface of the casting, and eliminates the anisotropy of organizations in the casting. Its casting performance, thermal crack resistance, mechanical properties and machining performance increase.
Furthermore, adding calcium to steel can improve its performance against hydrogen cracking and lamellar rupture, in addition to extending the useful life of equipment and tools. Calcium is added to the mother alloy as a deoxidizer, inoculant and microbinding agent.
Element 14: Ti(Titanium)
Titanium has a strong affinity for nitrogen, oxygen and carbon and a stronger affinity for S than iron, making it an effective element for nitrogen and carbon deoxidation and fixation.
Although titanium is a strong carbide-forming element, it does not combine with other elements to form compounds.
Titanium carbide has strong bonding strength, is stable and difficult to decompose. It can only dissolve slowly in steel at temperatures above 1000℃.
Before isolation, titanium carbide particles can prevent grain growth.
Due to titanium's greater affinity for carbon than for chromium, it is commonly used in stainless steel to fix carbon, remove chromium dilution at the grain boundary, and eliminate or reduce intergranular corrosion in steel.
Titanium is also a strong ferrite-forming element that greatly increases the A1 and A3 temperatures of steel.
In common low-alloy steel, titanium can improve plasticity and toughness, while increasing the strength of steel by fixing nitrogen and sulfur and forming titanium carbide.
The grain refinement formed by normalizing and precipitation carbides can greatly improve the plasticity and impact resistance of steel.
Titanium-containing alloy structural steel has good mechanical properties and process performance, but its main disadvantage is poor hardenability.
In high chromium stainless steel, the titanium content is generally five times that of carbon, which can improve the corrosion resistance (mainly anti-intergranular corrosion) and toughness of the steel, promote grain growth at high temperatures and improve the welding performance of steel.
Element 15: V(Vanadium)
Vanadium has a strong affinity for carbon, nitrogen and oxygen, forming stable compounds with them. In steel, vanadium is mainly present in the form of carbides.
Vanadium works to refine the structure and grain of steel and can increase hardenability when dissolved in solid solution at high temperatures. However, when present in the form of carbides, it can reduce hardenability. Vanadium also increases the tempering stability of hardened steel and produces a secondary hardening effect.
The amount of vanadium in steel is generally limited to 0.5%, except in high-speed tool steel. In common low-carbon alloy steel, vanadium can refine the grains and improve the strength, yield rate, low-temperature properties and welding properties of the steel. In structural steel alloys, it can reduce hardenability under normal heat treatment when used in combination with manganese, chromium, molybdenum and tungsten.
Vanadium can improve the strength and yield ratio in spring steel and bearing steel, especially the yield strength and yield strength, and reduce the sensitivity to carbon during heat treatment, thereby improving the surface quality. When added to tool steels, it refines the grain, reduces sensitivity to overheating, and increases tempering stability and wear resistance, extending tool life.
In steel carburizing, vanadium allows the steel to be quenched directly after carburizing, without the need for secondary quenching. Bearing steel containing vanadium and chromium has high dispersion and good performance.
Element 16: Cr(Chromium)
Chromium can increase the hardenability of steel and has the effect of secondary hardening, and can improve the hardness and wear resistance of carbon steel without making it brittle.
When the Cr content is greater than 12%, it makes the steel have good resistance to oxidation at high temperatures and corrosion, as well as increasing its hot resistance.
Chromium is the main alloying element in stainless steel, acid-resistant steel and heat-resistant steel.
Chromium can improve the strength and hardness of carbon steel under rolling, reduce cross-sectional elongation and shrinkage.
When the chromium content exceeds 15%, the strength and hardness will decrease, and the cross-sectional elongation and shrinkage will increase correspondingly. When grinding, parts made of chrome steel are easy to obtain high surface quality.
The main function of chromium in tempering structure is to improve hardenability, make the steel have good comprehensive mechanical performance after quenching and tempering, produce chromium carbide in carburizing steel to improve the wear resistance of the material surface.
Chromium spring steel is not easy to decarburize during heat treatment.
Chromium can improve the wear resistance, hardness and red hardness of tool steel and make it have good tempering stability.
In electrothermal alloys, chromium can improve the oxidation resistance, strength and toughness of the alloy.
Element 17 :Mn(Manganese)
Mn can improve the strength of steel. Because Mn is relatively cheap and can be alloyed with Fe, it has little effect on the plasticity and improves the strength of the steel. Therefore, Mn is widely used to reinforce steel.
It can be said that almost all carbon steel contains Mn. Mild stamping steel, two-phase steel (DP steel), steel with transformation-induced plasticity (TR steel), and martensitic steel (MS steel) contain manganese.
Generally, the Mn content in mild steel will not exceed 0.5%. The Mn content in high-strength steel increases with increasing strength level, such as in martensitic steel, the Mn content can reach up to 3%.
Mn improves the hardenability of steel and improves the thermal processing performance of steel. A typical example is 40Mn and #40 steel.
Mn can eliminate the influence of S (sulfur). Mn can form MnS with a high melting point in steel casting, weakening and eliminating the adverse effects of S.
However, Mn content is also a double-edged sword. Increasing Mn content will reduce the plasticity and welding properties of steel.
Element 18 :Co(Cobalt)
Cobalt (Co) is used in special steels and alloys. Co-containing high-speed steel has strong hardness at high temperatures.
When added to martensitic aged steel along with molybdenum, Co can increase the steel's hardness and overall mechanical properties.
Furthermore, Co is an important alloying element in hot steel and magnetic materials.
However, Co can reduce the hardenability of steel and thus decrease its comprehensive mechanical properties, especially in carbon steel.
Furthermore, Co can strengthen ferrite, and when added to carbon steel during annealing or normalizing, it can improve the hardness, yield strength and tensile strength of the steel, but it has a negative effect on its elongation and shrinkage. transversal section.
Furthermore, increasing the Co content in steel reduces its impact resistance.
Lastly, due to its antioxidant properties, Co is used in heat-resistant steels and alloys, particularly in Co-based alloy gas turbines.
Element 19 :Ni(Nickel)
The beneficial effects of nickel include high strength, high toughness, good hardenability, high strength and high corrosion resistance.
Nickel can significantly increase the strength of steel while maintaining high toughness. Furthermore, its brittle temperature is exceptionally low (below -100°C when nickel <0.3%, and can drop to -180°C when the Co content is increased to about 4-5%), which which can improve the strength and plasticity of hardened steel. .
A steel with Ni=3.5% cannot be quenched, but adding Ni=8% to Cr steel can turn it into M-type at a very low cooling rate.
Nickel has a similar lattice constant to γ-Fe, which makes it conducive to improving steel hardening by forming a continuous solid solution.
Nickel can reduce the critical point and increase the stability of austenite, which leads to the reduction of quenching temperature and good quenching.
Ni steel is generally used for heavy parts of large sections. When combined with Cr, W or Cr and Mo, hardenability can be increased. Nickel-molybdenum steel has a high fatigue limit and Ni steel has good thermal fatigue resistance, capable of working in hot and cold conditions.
In stainless steel, Ni is used to create a uniform A-body to improve corrosion resistance.
Ni steel does not overheat easily, which can prevent grain growth at high temperatures and maintain a fine grain structure.
Element 20 :Cu(cuprum)
The prominent role of copper (Cu) in steel is to improve the atmospheric corrosion resistance of common low-alloy steel. When mixed with phosphorus, Cu can also improve the strength and yield ratio of steel without any adverse effect on its welding performance.
Steel rail (U-Cu) containing 0.20% to 0.50% Cu has a corrosion resistance period 2 to 5 times that of normal carbon steel.
When the Cu content exceeds 0.75%, an aging effect may occur after solid solution treatment and aging.
With a low Cu content, its effect is similar to that of nickel, but weaker. With high Cu content, it is not suitable for thermal deformation processing, which may lead to copper brittleness.
Adding 2-3% copper to austenitic stainless steel can increase the corrosion resistance of sulfuric acid, phosphoric acid and hydrochloric acid, as well as the stability of stress corrosion cracking.
Element 21 :Ga(Gallium)
Gallium (Ga) is an element located in the closed γ section. Microgallium is soluble in ferrite and forms a solid solution substitute. It is not a carbide-forming element, but it also does not form oxides, nitrides and sulfides.
In the γ+a two-phase regions, microgallium is easily diffused from austenite to ferrite, where its concentration is high. The effect of microgallium on the mechanical properties of steel is mainly solid solution strengthening.
Ga has a minor effect on the corrosion resistance of steel.
Element 22 :As(arsenic)
Arsenic (As) from the ore can only be partially removed in the sintering process, but can be removed with chloridization roasting. How it will be mixed with pig iron during the blast furnace smelting process.
When the As content in steel exceeds 0.1%, it can increase the brittleness of the steel and weaken its welding performance. Therefore, the As content in the ore should be controlled, and the amount of As in the ore should not exceed 0.07%.
Arsenic has a tendency to increase the yield point σs and tensile strength σb of low-carbon round steel while reducing its elongation. Furthermore, its effect on reducing the impact strength Akv of round carbon steel at normal temperature is significant.
Element 23 :Se(selenium)
Selenium (Se) can improve the machining properties of carbon steel, stainless steel and copper and make the surface of parts shiny and clean.
High magnetic induction oriented silicon steel generally uses MnSe2 as the inhibitor. Its good inclusion, compared with that of MnS, is stronger in restraining the growth of the initial recrystallization grain and is more conducive to promoting the growth of the selected secondary recrystallization grain. This can achieve a high-orientation (110)(001) texture.
Element 24 :Zr(zirconium)
Zirconium (Zr) is a strong carbide-forming element and its role in steel is similar to that of niobium, tantalum and vanadium.
Adding a small amount of Zr has the effects of degassing, purifying and refining the grain, which is advantageous for improving the low temperature performance and stamping performance of steel.
Zr is often used in the manufacture of gas engines and ultra-high-strength steel and high-temperature Ni-based alloys that are needed for missile structures.
Element 25 :Nb(niobium)
Niobium (Nb) is often associated with tantalum and their roles in steel are similar. Nb and tantalum can partially dissolve in solid solution and strengthen it.
Steel tempering is significantly improved when the austenitic body is dissolved. However, in the form of carbides and oxide particles, Nb can refine the grain and reduce the hardenability of the steel. It can increase the tempering stability of steel and has a secondary hardening effect.
Microniobium can improve the strength of steel without affecting its plasticity or toughness. Furthermore, it can refine the grain, improve impact resistance and reduce the brittle transition temperature of steel. When the Nb content is more than 8 times that of carbon, almost all of the carbon in the steel can be fixed, making the steel have good hydrogen resistance.
In austenitic steels, Nb can prevent oxidizing media from causing intergranular corrosion of the steel. It can also improve the high temperature performance of hot steel such as creep resistance due to its fixed carbon and precipitation hardening effect.
Nb can improve the yield strength and impact resistance of common low-alloy steel and reduce its brittle transition temperature, which is beneficial for welding. In carburizing and tempering structural steel alloys, it can increase hardenability and at the same time improve toughness and low temperature performance. In addition, Nb can reduce the air hardening of low-carbon martensitic stainless steel, prevent hardening quench brittleness, and increase creep resistance.
Element 26 :Mo(molybdenum)
Molybdenum (Mo) can improve the hardenability and thermal intensity of steel, prevent quench brittleness, increase residual magnetism, coercivity and corrosion resistance in some media.
In quenched and tempered steel, Mo can strengthen the quenching depth, hardening of large cross-sectional parts, and improve the drawing strength or tempering stability of steel. This can make parts more effectively eliminate (or reduce) residual stresses and improve their plasticity under high temperatures.
In the carburizing of steel, Mo can reduce the tendency of carbide to form into a continuous mesh at the grain boundary during the carburizing layer, reduce the residual austenite in the carburizing layer, and relatively increase the surface wear resistance.
In steel forging, Mo can maintain a stable hardness of steel and increase its resistance to deformation, cracking and abrasion.
In acid-resistant stainless steel, Mo can further improve its corrosion resistance to organic acids such as formic acid, acetic acid, oxalic acid, hydrogen peroxide, sulfuric acid, sulfurous acid, sulfate, acid dyes, bleaching powder or fluid . In particular, the addition of Mo can prevent the corrosion tendency of chlorine ion.
W12Cr4V4Mo high speed steel with about 1% Mo has excellent wear resistance, tempering hardness and red hardness.
Element 27 :Sn(Estanum)
Tin (Sn) has been considered a harmful impurity element in steel. It can affect the quality of steel, especially the quality of continuous casting billet. Sn can cause steel to produce hot brittleness, tempering brittleness, cracks and fractures, affecting the welding performance of steel, and is one of the 'five evils' of steel.
However, Sn plays an important role in electrical steel, cast iron and easy-cutting steel. The grain size of silicon steel is related to the segregation of Sn, and the segregation of Sn can impede grain growth. The higher the Sn content, the greater the grain precipitation and the more effective it will be in preventing grain growth. The smaller the grain size, the less iron loss.
Sn can change the magnetic properties of silicon steel and improve the strength of the favorable {100} texture in the finished oriented silicon steel product. This can lead to an obvious increase in the intensity of magnetic induction. When a small amount of Sn is contained in cast iron, it can improve the wear resistance of steel and affect the fluidity of cast iron. Pearlitic malleable cast iron has high strength and high wear resistance. To obtain molten pearlite, Sn is added to the alloy solution during melting. Since Sn is an element that blocks the spherification of graphite, it is necessary to control the amount of Sn addition, which is generally less than 0.1%.
Easy-cutting steel can be divided into sulfur, calcium, lead and easy-cutting composite steel. Sn has an obvious tendency to accumulate around inclusions and defects. Sn does not change the shape of sulfide inclusions in steel, but it can improve the brittleness and cutting performance of steel by grain boundary and phase boundary segregation. When the Sn content is >0.05%, the steel has good cutting capacity.
Element 28 :Sb(Stibium)
After adding antimony (Sb) to high magnetic orientation silicon steel, the grain size of the first and secondary recrystallization can be refined, leading to more perfect second recrystallization and improved magnetism.
After cold rolling and decarbonization of Sb steel, the texture composition components {110}<115> or {110}<001> favorable to the development of secondary recrystallization will be enhanced and the number of secondary crystal nuclei will increase .
In the construction of Sb-containing welding steel, under austenitic temperature, Sb precipitates around MnS inclusions and along the original austenite grain boundary. Precipitation enriched with MnS inclusions can refine the organization of steel and improve its toughness.
Element 29 :W(tungsten)
In steel, tungsten (W) is partially dissolved in iron forming a solid solution, in addition to producing carbide.
Its effect is similar to that of Mo, and the overall effect is not as significant as that of Mo if calculated by quantity.
The main role of W in steel is to increase tempering stability, red hardness, heat intensity and wear resistance due to carbide formation.
Therefore, it is mainly used for tool steel such as high-speed steel and hot forged steel.
W is a high-quality spring steel refractory carbide, which can reduce the carbide concentration process and maintain high temperature resistance at higher temperatures.
W can also reduce the overheating sensitivity of steel, increase its hardenability and hardness.
Air cooling makes 65SiMnWA spring steel has high hardness after hot rolling.
A spring steel with a cross section of 50 mm2 can be hardened in oil and withstand a heavy load, be heat resistant (not exceeding 350 ℃).
The high-strength, heat-resistant and high-quality 30W4Cr2VA spring steel has great hardenability, and its tensile strength can be 1470 ~ 1666 pa after quenching at 1050 ~ 1100 ℃ and quenching at 550 ~ 650 ℃.
It is mainly used in manufacturing springs used under high temperatures (500℃).
Due to the addition of W, it can significantly improve the abrasion and cutting properties of steel, so W is the main element of tool steel alloy.
Element 30 :Pb(Plumbum)
Pb can improve the machinability of steel. Steel containing Pb has good mechanical properties and can be heat treated. However, due to its environmental pollution and harmful effects in the steel waste recycling process, Pb has been gradually replaced.
Pb is difficult to form a solid solution or compounds with Fe. Instead, it tends to accumulate at the grain boundary in a globular form, which can cause brittleness in steel at temperatures between 200-480°C and result in cracking. during welding.
Element 31 :Bi(Bismuth)
The cutting performance of steel can be improved by adding 0.1-0.4% Bi to the free cutting steel.
When Bi is evenly distributed in the steel, the Bi particles melt after coming into contact with the cutting tool, acting as a lubricant, causing the cutting tool to break to prevent overheating and increase the cutting speed.
Recently, Bi has been added to many stainless steels to improve their cutting performance.
Bi exists in three types of free-cutting steels: independently in the steel matrix, surrounded by sulfide, and between the steel matrix and the sulfide.
The strain rate of MnS inclusions decreases with increasing Bi content in S-Bi free-cutting steel ingots.
The bimetal in steel can contain the deformation of sulfide in the steel ingot forging process.
Adding 0.002-0.005% Bi to cast iron can improve the casting performance of malleable cast iron, increase the whitening tendency, reduce annealing time, and optimize the extension performance of parts.
Adding 0.005% Bi to nodular cast iron can improve its anti-seismicity and tensile strength.
It is difficult to add Bi to steel because Bi largely volatilizes at 1500℃ and is therefore difficult to be evenly infiltrated into the steel.
At present, abroad, Bi is replaced by Bi-Mn alloy plates with a melting point of 1050 ℃ as an additive, but the utilization rate of Bi is still about 20%.
Nippon Steel & Sumitomo Metal, Posco, TYO and other companies have proposed that the addition of Bi can significantly improve the B8 value of oriented silicon steel.
According to statistics, Nippon Steel & Sumitomo Metal and JFE have more than a hundred high magnetic orientation silicon steel inventions, having added Bi.
After adding Bi, the magnetic induction reaches 1.90T and the maximum is 1.99T.
Other Element 32-48 :Re (Rare Earths)
Rare earth elements commonly refer to the lanthanides with atomic numbers ranging from 57 to 71 (lanthanum, cerium, praseodymium, neodymium, promethium, samarium, europium, gadolinium, terbium, dysprosium, holmium, erbium, thulium, ytterbium and lutetium), more scandium (No. 21) and yttrium (No. 39), for a total of 17 elements. Their properties are similar, making them difficult to separate. Mixed rare earths, which are cheaper, refer to those that have not been separated.
Rare earths can be used for deoxidation, desulfurization and microbonding, and can also change the deformability of rare earth inclusions. They can affect the brittleness of Al2O3 to a certain extent and improve the fatigue performance of most types of steel.
Rare earth elements, along with Ca, Ti, Zr, Mg and Be, are the most effective deforming agents for sulfide. By adding the appropriate amount of rare earths to steel, oxide and sulfide inclusions can be transformed into small, dispersed globular inclusions, which eliminate the harmful effects of MnS and other inclusions.
In steel production practice, sulfur is normally present as FeS and MnS. When the Mn content is high in steel, MnS is more likely to form. Although MnS has a high melting point and can avoid thermal brittleness, during machining deformation, it can stretch in the processing direction and form strips. This can significantly reduce the plasticity, toughness and fatigue resistance of steel, making it necessary to add RE to steel for deformation processing.
Rare earth elements can also increase the oxidation and corrosion resistance of steel. Its effect on oxidation resistance is greater than that of silicon, aluminum and titanium. They can improve the flow of steel, reduce non-metallic inclusion, and make the steel structure dense and pure. The role of rare earths in steel is mainly purification, metamorphism and alloying.
With the gradual control of oxygen sulfur content, traditional molten steel purification and metamorphism are gradually weakening, while new purification technologies and alloying effects are being improved. Rare earth elements increase the antioxidant capacity of ferrochrome aluminum alloy and maintain the fine grain of the steel at high temperatures, significantly increasing its high temperature strength and the service life of the electrothermal alloy.