- Aluminum installation: light and durable, but more expensive
Aluminum compressed air systems are used in many industries to generate, store and distribute compressed air. These systems typically consist of a compressor, storage tanks, and distribution lines.
One of the main advantages of using aluminum in compressed air systems is its lightness and resistance to corrosion. Aluminum is much lighter than other materials such as steel, making it easier to transport and handle. Additionally, it is resistant to corrosion caused by contact with salt water, chemicals and other corrosive substances, making it suitable for use in a variety of industries.
In addition to its corrosion-resistant properties, aluminum also has good thermal conductivity, making it suitable for use in applications where temperature control is important.
When considering installing a compressed air system, it is important to carefully consider the benefits and costs of different materials. For example, an aluminum air system may be more expensive initially than a polypropylene or bolt-on system, but it may last longer and require less maintenance over time. In the long term, this can bring savings to the company.
So why would a company choose aluminum installation over polypropylene or screw installation?
There are several reasons to choose aluminum over these other materials. First, aluminum systems are more resistant to corrosion and have a longer lifespan, which can result in savings over time by requiring less maintenance and repairs. Additionally, aluminum systems are light and easy to handle, which can be important in some industries or applications where weight is a critical factor.
In general, the choice of material for a compressed air system depends on the specific requirements of the application and the industry in which it will be used. It is important to carefully consider the benefits and limitations of different materials to select the best option for your application.
Although aluminum has many advantages as a material for compressed air systems, there are also some potential disadvantages that must be considered.
One potential disadvantage of aluminum is that it may not be as strong as other materials, such as steel. This may make it unsuitable for high pressure or heavy load applications. Aluminum systems may also be more susceptible to damage from impact or mechanical wear than systems made from other materials.
Another potential disadvantage of aluminum is that it can be more expensive initially than other materials such as polypropylene or bolted systems. This can make installation more expensive initially, although long-term savings from reduced maintenance and repair costs can offset these initial costs.
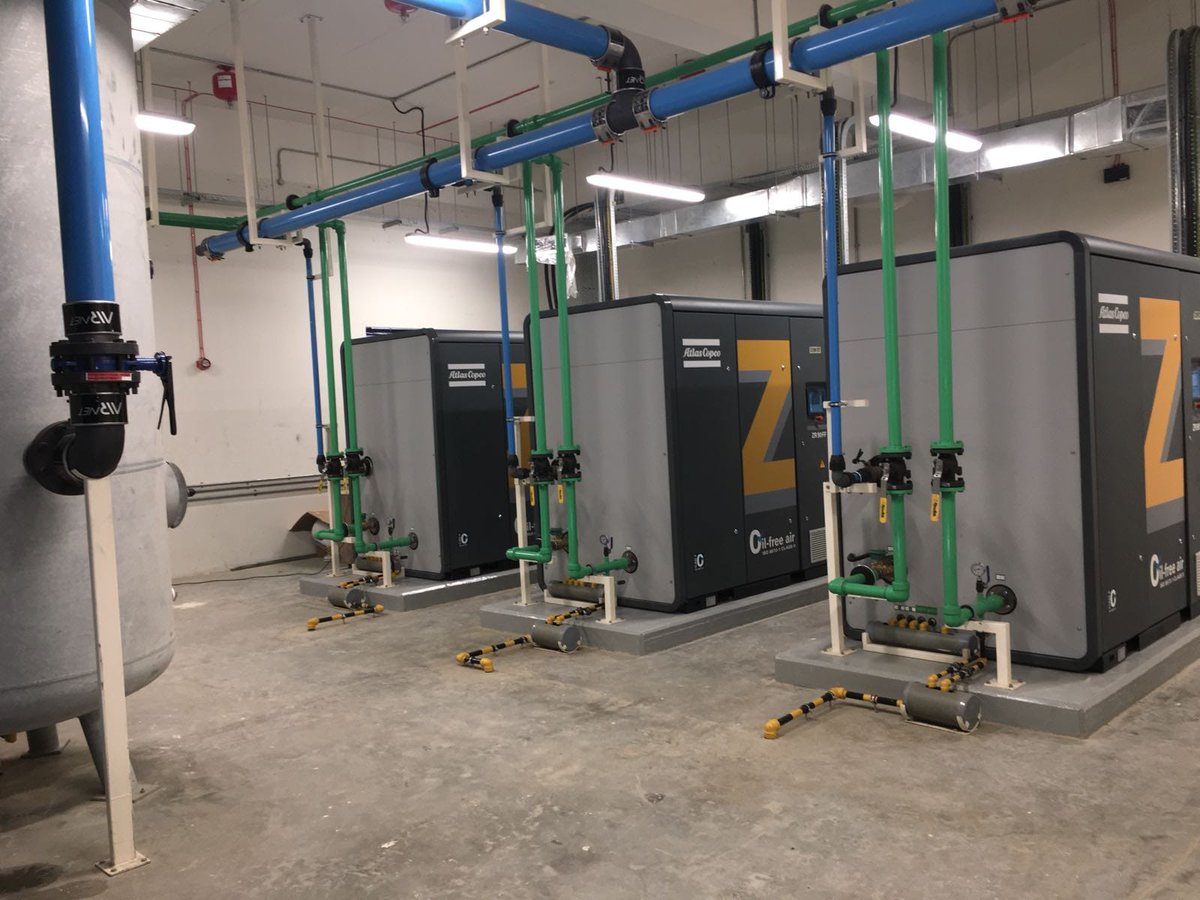
Additionally, aluminum systems may require more frequent cleaning and maintenance to maintain their anti-corrosion properties. This can be time-consuming and require the use of special cleaning products or equipment.
Although aluminum offers many advantages as a material for compressed air systems, it is important to carefully weigh the potential disadvantages to determine if it is the best choice for your application.
There are many industries that use aluminum compressed air systems. here are some examples:
- Automotive: Aluminum compressed air systems are commonly used in the automotive industry because they are lightweight and corrosion resistant. This makes them suitable for use in vehicles where weight is a critical factor and where exposure to corrosive substances such as salt and water can damage other types of materials.
- Aerospace: Aluminum systems are widely used in the aerospace industry due to their light weight and corrosion resistance. These properties make them ideal for use on aircraft where weight is a major concern and where exposure to corrosive substances, such as salt water, can be a problem.
- Food and Beverage Industry: In the food and beverage industry it is important to use materials that are resistant to corrosion and do not contaminate products. Aluminum systems are well suited for this because they are corrosion resistant and easy to clean and maintain.
- Pharmaceutical Industry: In the pharmaceutical industry it is important to use materials that do not contaminate products and do not react with chemicals or other substances. Aluminum systems are a good choice in this industry due to their corrosion resistance and ability to withstand high temperatures.
- Chemical Processing: Aluminum systems are also used in the chemical processing industry because they are corrosion resistant and can withstand high temperatures. This makes them suitable for applications where exposure to harsh chemicals or high temperatures may be a problem.
If you need an aluminum compressed air system, contact Pneumatig. Pneumatig is a company that distributes high-quality aluminum compressed air systems from Atlas Copco, a leading manufacturer of industrial equipment. Pneumatig's specific product is called “Airnet” and is a comprehensive solution for the generation, storage and distribution of compressed air.
Airnet systems are made from high-quality aluminum and designed for durability, corrosion resistance and easy maintenance. They are suitable for use in many industries, including automotive, aerospace, food, pharmaceutical and chemical.
The Pneumatig team has knowledge and experience in selecting and installing compressed air systems and can help you choose the best solution for your specific application.
Compressed air installation in stainless steel – advantages and disadvantages
One of the main benefits of using a stainless steel compressed air system is its strength and durability. Steel is much stronger than other materials such as aluminum or polypropylene, making it suitable for applications involving high pressure or heavy loads. Steel systems are also generally more resistant to mechanical wear, which can make them more durable over time.
In addition to strength and durability, steel has good thermal conductivity, making it suitable for applications where temperature control is important. It is also easy to weld and machine, making it easy to manufacture and maintain.
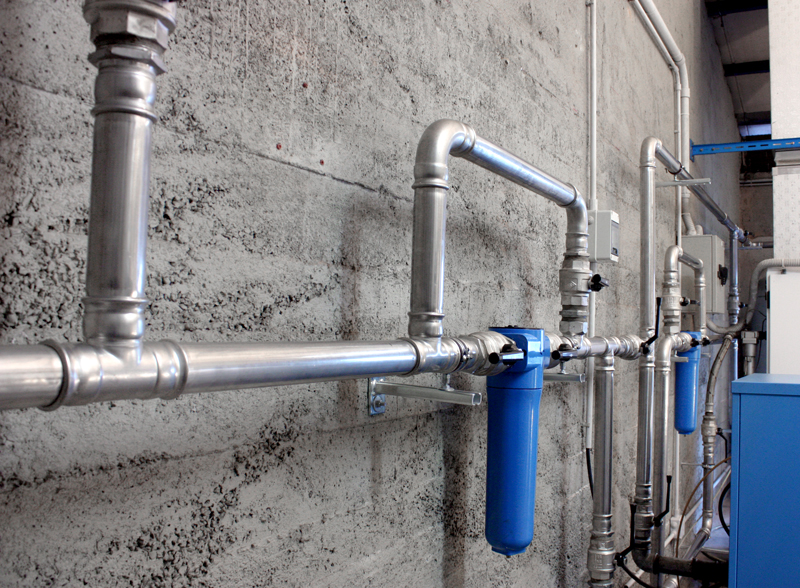
There are several situations in which a steel compressed air system may be a better choice than an aluminum or polypropylene system. They include:
- High pressure or heavy duty applications: Steel is much stronger than other materials such as aluminum or polypropylene, making it suitable for high pressure or heavy duty applications.
- Industries with high mechanical wear: Steel systems are generally more resistant to mechanical wear than other materials, which can make them more durable over time. This makes them a good choice for industries with high mechanical wear, such as mining or construction.
- Applications where temperature control is important: Steel has good thermal conductivity and is therefore suitable for use in applications where temperature control is important. This can be important in industries such as chemical processing or power generation, where temperature fluctuations can affect equipment performance.
There are several potential disadvantages to consider when using a steel compressed air system:
- Weight: Steel is much heavier than other materials such as aluminum or polypropylene, which can make transport and handling difficult. This may be a problem in some industries or applications where weight is a critical factor.
- Corrosion: Steel systems can be more susceptible to corrosion than other materials, which may require more frequent cleaning and maintenance to maintain their anti-corrosive properties. This can be time-consuming and require the use of special cleaning products or equipment.
- Cost: Stainless steel systems can be more expensive than other materials such as aluminum or polypropylene. This can make the initial installation more expensive, although the long-term savings from reduced maintenance and repair costs can offset these initial costs.
Polypropylene installation: Lightweight, chemically resistant and durable, but less resistant to high temperatures
Polypropylene compressed air systems are characterized by their low weight, chemical resistance and high durability. They are a perfect solution wherever it is important to keep the weight of the entire system as low as possible, but at the same time resistance to aggressive chemicals is required, for example in the pharmaceutical or food industries.
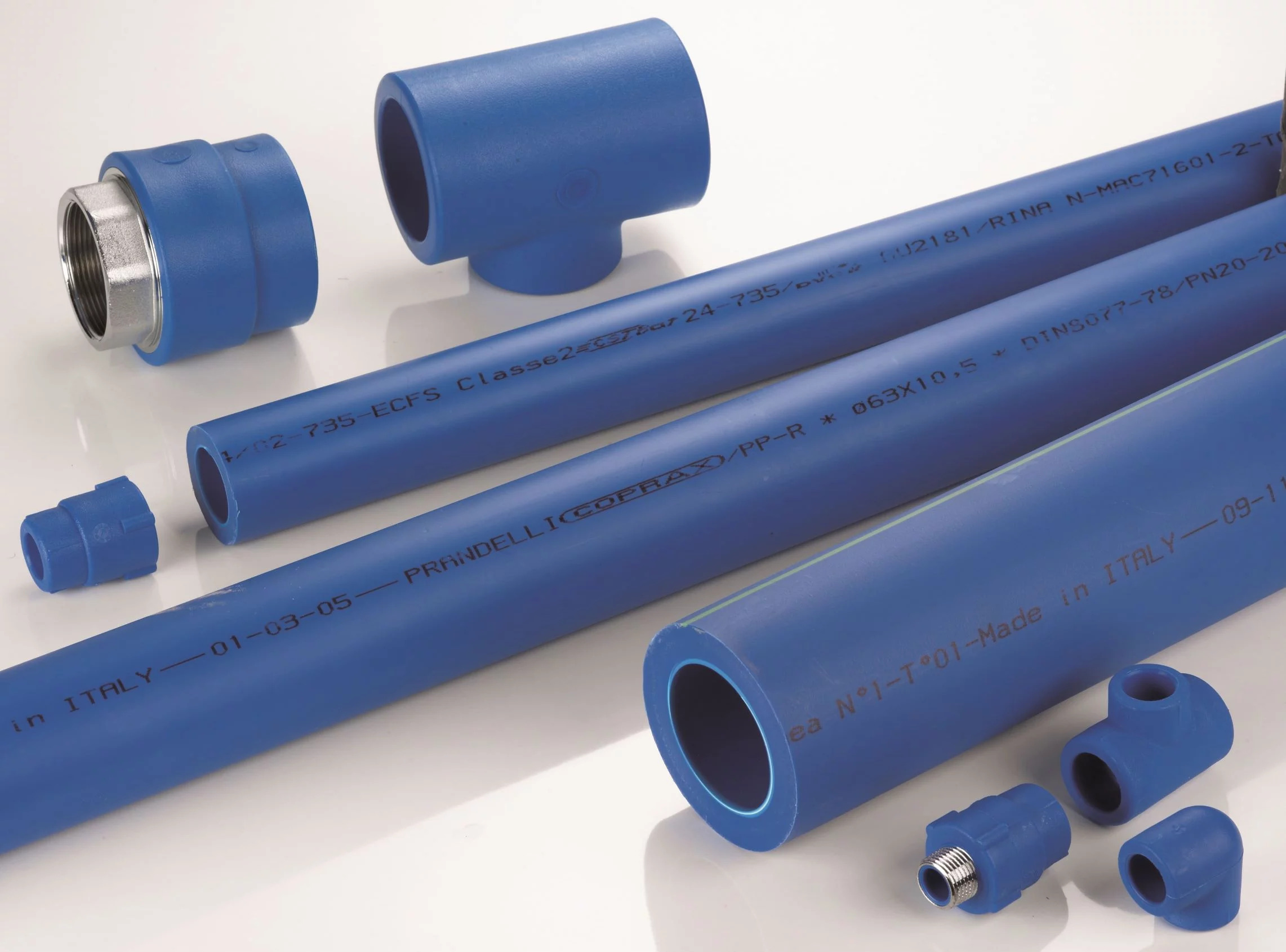
The company “Pneumatig” offers “Coprax” pipes made of polypropylene, which are characterized by high quality and reliability. These tubes are the ideal solution for compressed air installations where resistance to aggressive chemical environments and low weight of the entire system are required.
However, despite their advantages, polypropylene installations are less temperature resistant than those made of aluminum or bolted steel. Therefore, its use is limited to applications where temperatures do not exceed a certain limit.
Polypropylene plants are often used in the following industries:
- Pharmaceutical industry: Polypropylene is resistant to many aggressive chemicals, so equipment made with this material is the ideal solution for the pharmaceutical industry where cleanliness and sterility are important.
- Food industry: Just like in the pharmaceutical industry, it is also important in the food industry to keep food clean and safe. Polypropylene is safe for consumption and does not emit harmful substances, which is why equipment made from this material is widely used in the food industry.
- Chemical industry: Polypropylene is resistant to many chemicals, which is why equipment made from this material is often used in the chemical industry to transport and distribute various chemical products.
- Construction: Polypropylene is weather resistant, which is why systems made with this material are often used in construction to transport compressed air in ventilation and air conditioning systems.
In summary, compressed air installations made of aluminum, turned steel or polypropylene differ in terms of properties, advantages and disadvantages. When choosing the right material, you must carefully consider your needs and expectations, as well as the specific requirements of a specific application.
For example, if weight is a deciding factor, aluminum or polypropylene may be a better choice. If flexibility and adaptability are more important, a steel mesh installation may be more suitable. On the other hand, if the system is exposed to high temperatures or harsh chemicals, aluminum or polypropylene may be a safer option.
It is also worth considering the long-term maintenance and repair needs of the system. Aluminum and polypropylene installations tend to be more durable and require less maintenance, while steel mesh installations may require more frequent repairs and seal replacement.
Ultimately, the best choice depends on your project's specific needs and budget.
Choose the right material for your compressed air installation.
In summary, the choice of material for a compressed air system is an important decision that can have a significant impact on the performance and safety of the system. Aluminum, steel mesh and polypropylene installations have their own characteristics, advantages and disadvantages. Careful consideration of the specific requirements and needs of a specific application, as well as long-term maintenance and repair needs, can help ensure that the right material is selected for the job.