The materials required for the 3D printing (3DP) process mainly consist of powder materials and binders.
1. Powder Materials
I. Performance Requirements
Based on the operating principles of 3DP, powder materials need to possess good moldability, high forming strength, small particle size, low tendency to agglomerate, good fluidity, adequate density and porosity, and rapid drying and hardening. Among these properties, particle size is particularly crucial.
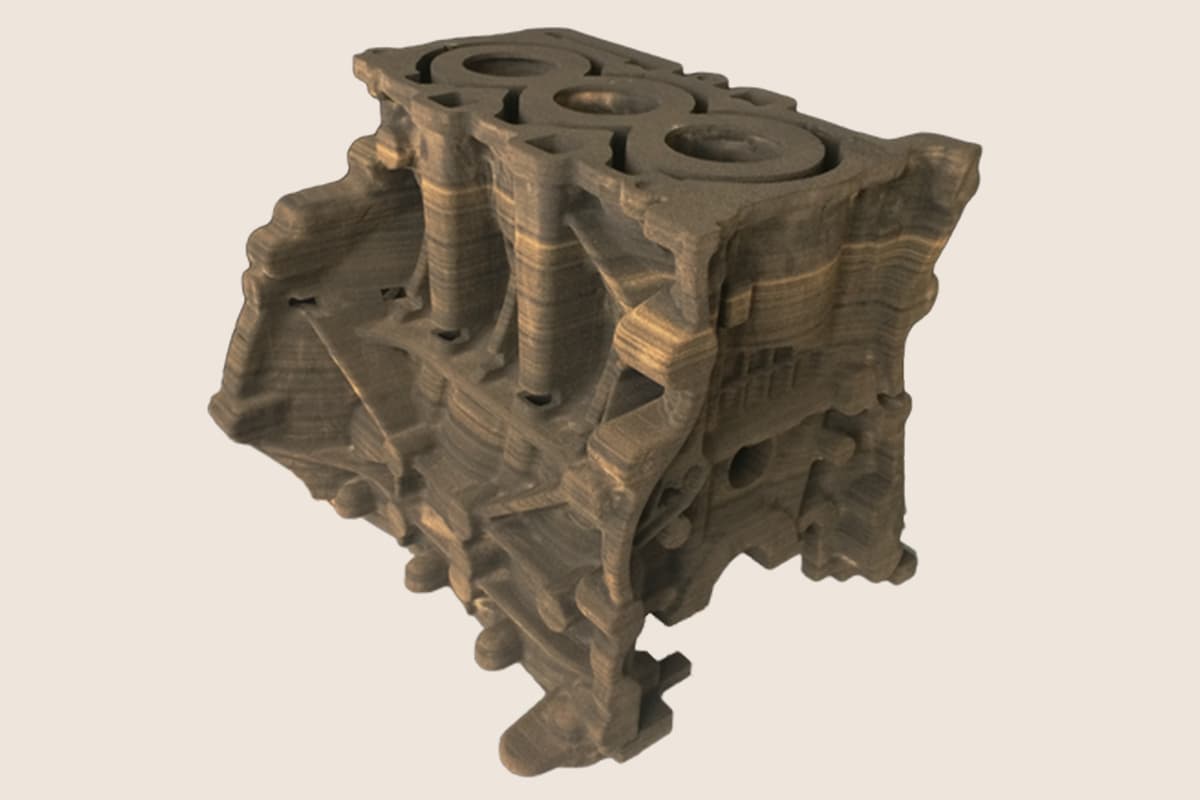
Smaller particles provide stronger van der Waals forces between them, but they have less fluidity and are prone to forming dust, which can clog the print head. Larger particles have better fluidity, but can compromise the mold's printing accuracy. The size of the powder particles can vary from 1μm to 100μm depending on the type of printer used and the operating conditions.
Powders that can be used in the 3DP process include gypsum powder, starch, ceramic powder, metal powder, thermoplastic materials and other powders with suitable particle sizes.
ii. Powder composition
Powder materials comprise fillers, binders and additives.
The. Fillers: Options such as quartz sand, ceramic powder, gypsum powder, polymer powder (e.g. polymethyl methacrylate, polyoxymethylene, polystyrene, polyethylene, paraffin, etc.), metal oxide powder and starch can be used as the main body of the powder material. These fillers increase the strength of parts and help control deformation after binder-induced shaping.
B. Binders: The inclusion of powder binders can increase dust formation resistance. Polyvinyl alcohol, cellulose (such as polymerized cellulose, silicon carbide cellulose, graphite cellulose, aluminum silicate cellulose, etc.) and maltodextrin can serve as reinforcing agents. However, the length of the pulp must be less than the reduction in the height of the powder bed during printing.
The addition of colloidal silica helps the liquid binder gel quickly when it comes into contact with the powder, increasing printing efficiency.
w. Additives: In addition to fillers and binders, various powder additives are required to tune performance. Solid lubricants such as aluminum oxide powder, soluble starch and talcum powder can improve the fluidity of the powder, making it easier to apply thin, even layers. The addition of small, high-density particles such as silica can increase powder density and reduce porosity, preventing excessive binder penetration during printing.
The addition of lecithin can minimize the formation of small particles and maintain the stability of the print format. Furthermore, it is essential to properly disperse the powder to avoid agglomeration due to the small particle size.
d. Preparation: In addition to simple mixing, fillers and binders can also be coated. By coating the charges with a binder (such as polyvinylpyrrolidone) and drying, the two components can be dispersed more evenly in the powder material, allowing uniform penetration of the ejected binder. Alternatively, the fillers can be divided into two portions for coating: one with an acid-based binder and the other with a base-based binder.
When the two meet through a medium, they can react quickly to form a shape. The coating also effectively reduces friction between particles, improving their fluidity. However, it is important that the coating is very thin, ranging from 0.1 to 1.0μm.
2. Adhesive Agents
① Performance requirements
The. Appropriate viscosity.
Adhesive agents must have adequate viscosity to ensure the formation of individual droplets that can detach from the print head nozzle. For SEIKO1020 piezoelectric print head, the recommended viscosity range for adhesive agents is 8 to 12 mPa·s.
B. Adequate surface tension.
The surface tension must be adequate to promote good interaction between the adhesive agent and the powder, ensuring effective wetting.
w. Sufficient bond strength.
Adhesive agents must have sufficient bonding strength to ensure the integrity of the initial printed structure.
d. Non-corrosive.
Typically, liquid adhesives are ejected through metal print heads and should not cause corrosion.
It is. Non-toxic and environmentally friendly.
They must comply with relevant national or organizational environmental regulations, be free of volatile odors, non-toxic side effects, environmentally friendly and particularly suitable for office environments.
f. Clean combustion characteristics.
For metal powder applications, adhesive agents generally require post-processing sintering and removal. They must have clean burning properties, minimal ash residue and no emissions of toxic by-products.
g. Stability.
The aforementioned properties must remain stable to facilitate long-term storage and to ensure consistent product quality between batches.
② Main Components
Clearly, liquid adhesive agents consist mainly of a base medium and solvents. Additionally, they should include humectants, quick-drying agents, lubricants, coagulants, flow enhancers, pH adjusters, and other additives (such as dyes, defoamers), none of which should react with the printhead material.
For example, humectants such as polyethylene glycol and glycerol help retain moisture, facilitating stable long-term storage of adhesive agents, and glycerol also serves as a lubricant to reduce print head clogging. Low boiling point solutions, such as ethanol and methanol, can be added to increase the evaporation rate of excess adhesive.
For powder materials that use colloidal silica or similar substances as gelling agents, additives such as citric acid can be introduced as coagulants to increase bonding effectiveness. Small amounts of other solvents (such as methanol) or the addition of organic compounds of varying molecular weights can be used to adjust surface tension and viscosity to meet print head requirements.
Surface tension and viscosity greatly affect droplet formation during printing; the correct shape and size of the droplets directly affect the accuracy of the printing process. To improve the flowability of liquid adhesive agents, compounds such as diethylene glycol butyl ether, polyethylene glycol, potassium aluminum sulfate, acetone and sodium polyacrylate can be added as flow enhancers to accelerate printing speed.
For those adhesive agents with specific pH requirements, triethanolamine, tetramethylammonium hydroxide, citric acid and others can be used to adjust the pH to ideal levels.
Dyes that disperse evenly may be added for aesthetic purposes or product demands during the printing process. It is important to emphasize that the amount of additives must be limited, generally less than 10% per mass fraction, as an excessive amount can affect the result of the printed powder and the mechanical performance of the print head.
③ Main types
The adhesive agents used in 3DP processes can be classified in several ways.
The. From the point of view of material properties, they can be categorized into organic and inorganic adhesive agents. Organic adhesive agents bond powder materials through curing, while inorganic adhesive agents bond through colloidal gelling.
B. From the perspective of chemical reaction, they can be divided into acidic and basic adhesive agents, metal salt adhesive agents and solvent adhesive agents. Acidic and basic adhesive agents bond powder materials through acid-base chemical reactions, metal salt adhesive agents bond through recrystallization, reduction, or salt displacement reactions, and solvent adhesive agents act primarily on polymer powders. , dissolving the sprayed or deposited areas and forming specific structures. after evaporation of the solvent.
w. From the perspective of bonding mechanism, they can be separated into powder bed adhesive agents, phase change adhesive agents and sinter inhibitor adhesive agents. Powder bed adhesive agents, unlike standard liquid adhesive agents, adhere to the powder bed through the action of liquid sprayed through the nozzle. Phase change adhesive agents bind powders together by solidifying the adhesive, while sinter-inhibiting adhesive agents can control the sintering area by selectively spraying insulating materials.
These three classification methods are shown in Table 5-3.
Table 5-33 Types of binders for DP process
Binder type | Applicable Materials | Benefits | Disadvantages | ||
Classification by material properties | Organic Binder | Polyethylene, Butyraldehyde Resin, Phenolic Resin | Suitable for most non-sintered materials: easy to remove with minimal residue. | Prone to clogging of nozzles. | |
Inorganic Binder | Aluminum nitrate, colloidal silica | Heats the entire powder bed after printing, binding the powder together in parts. | Does not react immediately with dust after deposition. | ||
Classification by type of chemical reaction | Acid-Base Binder | 10% phosphoric acid and citric acid, polyvinylpyrrolidone | Almost no residue after heat treatment. | Limited to a few powders. | |
Metallic salt paste | Nitrates, Silicates, Phosphates | It uses recrystallization, reduction and displacement reactions for bonding. | The loose powder must resist thermal reduction during the salt reduction process. | ||
Solvent-Based Binder | Chloroform | High purity of parts. | Commonly used for polymers. | ||
Classification by Linking Mechanism | Powder Bed Paste | Cement, Plaster | Non-specific for certain powders, completely removed at high temperatures: simple liquid deposition. | Complex optimization steps. | |
Phase Change Paste | Dimethylpropane | Applicable to most powders. | Heating restrictions after printing. | ||
Sintering Inhibitors | Insulating materials, chemical oxidants, etc. | Boundaries of parts sprayed. | Excess dust contaminates the parts. |
Liquid binders can also be classified according to their interaction with powder materials, dividing them into three types:
1. Liquid binders that do not bind themselves, serving only as a means for binding powder materials. These almost completely volatilize after printing, suitable for self-reaction hardening powder materials such as chloroform, ethanol, etc.
2. Liquid binders that react with powder materials, usually with different acidity than powder materials, can achieve bonding through the reaction. For example, powders composed mainly of alumina can be solidified by spraying with an acidic binder.
The most commonly used water-based binders, containing water as the main component, can provide a medium and hydrogen bonds in water, allowing gypsum, cement and other powder materials to gel through hydrogen bonds, volatilizing after formation. For metal powders, metal salts are often added to the binder to induce a reaction.
3. Liquid binders that partially bind by themselves contain substances that bind when added to a liquid solvent, leaving key binding materials after the solvent evaporates. Common bonding additives include butyraldehyde resin, polyvinyl chloride, polycarbosilane, polyvinylpyrrolidone, and other polymers.
Compatible liquid solvents for these binding substances include water, acetone, acetic acid, ethyl acetoacetate, etc., with water-based binders being the most popular today.