Casting is the most flexible method for manufacturing complex parts.
The application of advanced casting technology has brought new vitality to the manufacturing industry.
With the advent of numerous software programs and the rapid development of computer technology, it is now possible to provide accurate and reliable information for the production of castings that meet requirements in terms of geometry, size and service performance.

About 15% to 20% of automotive parts are manufactured using different casting methods, which mainly include key power system components and important structural parts.
At present, developed countries in the automotive industry employ advanced production technology for automobile castings, resulting in high-quality products, production efficiency and minimal environmental pollution.
The raw and auxiliary materials used in the foundry were standardized and serialized, and the entire production process was mechanized, automated and intelligent.
As automotive technology continues to advance rapidly, rapid molding technology, CAE technology, 3D modeling, CNC technology and other technologies are being adopted to provide reliable support to shorten the production preparation period of castings and reduce the risk of developing new products.
Automobile casting technology
1. Casting process
Foundry mainly covers sand casting and specialized casting.
Ordinary sand mold casting
Sand casting is a process that uses sand as a mold material. It consists of three types of molds: wet sand mold, dry sand mold and chemically hardened sand mold. It is important to note that not all sand can be used for casting.
The advantage of sand casting is its low cost, as the sand used in the mold can be reused. However, casting mold production can be time-consuming and the mold itself cannot be reused. Once casting is complete, the mold must be destroyed to recover the finished product.
Special casting
Special casting is further categorized into two types based on the molding materials used. The first type uses natural mineral sand and stone as primary molding materials and includes methods such as precision casting, mud mold casting, shell mold casting, negative pressure casting, full mold casting and ceramic mold casting. The second type of special casting uses metal as the main molding material and covers techniques such as metal mold casting, pressure casting, continuous casting, low pressure casting and centrifugal casting.

Fig. 1 Classification of the casting process
In the automotive industry, the primary casting processes used fall into the following two categories:
1.1G ravity casting (GDC)
Gravity casting, also known as gravity casting, refers to the process in which molten metal is poured into a mold and fills the cavity under the influence of Earth's gravity.
In cases where the final product requires a hollow space, a sand core is placed inside the mold cavity.
To ensure proper flow of molten metal, the pouring device can be tilted, which is known as “tilted GDC”.
Gravity casting covers various techniques such as sand mold casting, metal mold casting, precision casting, lost foam casting and mud mold casting.
Of these techniques, sand mold casting is the most commonly used in the automotive industry.
1.1.1 S and casting
Currently, the most commonly used cast iron automotive parts are produced by wet sand molding, mainly through the use of static pressure or air impact molding with pre-compressed air flow. This method has numerous advantages, including low energy consumption, low noise, reduced pollution, high efficiency and reliable operation.
Foreign equipment manufacturers have continuously improved their molding machines by incorporating various improvement methods such as air impact compaction, air impact plus compaction with increased airflow, static pressure plus compaction, active multi-contact compaction and extrusion compaction molding process to obtain a more uniform product. sand mold hardness.

Fig. 2 sand casting process
With advances in high-power semiconductor components, computers and microelectronic technology, electrical servo systems are being used to replace hydraulic and pneumatic drives in molding lines, thereby accelerating the pace of production and significantly increasing operational reliability.
At the same time, the hydraulic control system is significantly simplified, reducing maintenance requirements.
Using a double-barrel sand tumbling machine, the casting and gate can be pre-cleaned simultaneously.
The pouring process on molding lines can often limit the overall production rate, therefore, the use of automatic pouring equipment is recommended.
Some manufacturers use air pressure cookers and contact pouring techniques to save cast iron, maintain quality, and protect the sandbox.
In the casting process, flow inoculation is commonly used and some employ a combination of mold inoculation and filtration.
In the casting process, different factories use different methods to produce sand cores. Cold core box, hot core box or shell core can be used depending on the conditions.
Sand cores such as crankcase sand core, cylinder, top sand core and front and rear face sand core are generally made with the cold core box to ensure dimensional accuracy and save energy.
Cold core box is becoming more and more popular.
Cold core is mainly produced using the ISO cure triethylamine hardening method, and an advanced method known as ISO Max has been developed in the United States.
To improve the internal surface quality and cleanliness of the internal cavity of the casting, water-based coatings are used instead of alcohol-based coatings to prevent pollution.
Microwave drying after coating is a highly efficient and energy-saving method, and the quality of the sand core produced is better than that obtained through traditional gas or natural gas drying.
The KCY-CORE process is employed, where process holes are opened in the sand core for filling and secondary solidification of the sand, resulting in the integration of multiple sand cores into a combined sand core. The combined sand core is then coated and dried, significantly improving the dimensional accuracy of the casting with an overall dimensional error of less than 0.3mm.
The sand molding system includes old sand magnetic separation equipment, sand block crushing equipment, screening equipment and old sand cooling equipment to ensure the quality of recycled old sand.
New sand, coal dust, bentonite and other added materials are accurately and quantitatively fed into the system according to a predetermined proportion, and water addition is adjusted in real time based on control data to maintain sand performance of molding.
There is also real-time closed-loop control of the molding sand performance of the entire system or an online specialized system to control molding sand quality.
It should be noted that the molding sand system has large turnover and strong inertia, so the adjustment of molding sand performance should be based on the trend, with predictable measures taken to ensure the stability of molding sand quality.
Common castings include: engine block, cylinder head, gearbox, intake manifold, etc.
1.2 D i.e. cast
When the required casting has a complex cross-section or thin walls in specific areas (as shown in Figure 3), gravity alone may not be sufficient to ensure that the molten metal completely fills the mold cavity.
In these cases, pressure can be applied to the metallic liquid to ensure complete filling of the mold cavity.
This can be achieved through high pressure die casting (HPDC) or low pressure die casting (LPDC).
Castings produced by the HPDC process have good dimensional consistency and similar tolerances, around +/- 0.2 mm, which cannot be achieved by gravity casting (GDC) or even pressure casting (LPDC).
With the rapid advancement of automotive technology, high-pressure die casting technology has become a focus in automotive casting.

Fig.3 complex thin-walled parts
1.2.1 High pressure casting
High pressure casting is a process in which liquid or semi-liquid metal is rapidly injected into a mold under high pressure, solidifying and crystallizing under pressure to form the casting.
The high pressure casting process can be divided into three stages: mold closing, injection and ejection.

Fig. 4 High pressure casting process flow
In the die casting process, injection parameters have a great impact on the porosity of die casting parts and must be adjusted accordingly.
Using a closed injection finish time control system, it is possible to achieve burr-free pressure casting.
The quality of castings can be checked through X-ray flaw detection and ultrasonic testing.
Vacuum casting and oxygen die casting, which are based on high pressure casting technology, aim to eliminate casting defects, improve internal quality and expand the application of pressure casting.
Compression casting involves filling and solidifying the casting under pressure, offering stability, reduced metal spatter, minimal oxidation loss of molten metal, energy savings, safe operation and reduced casting hole defects.
This process has been widely used in the development and application of high-performance aluminum alloy castings such as aluminum alloy subframes.
Vacuum Casting
To minimize or eliminate porosity in castings caused by the rapid mixing of gas with molten metal during the pressure casting process, it is common to use vacuum casting of the mold prior to pressure casting.
Based on the degree of vacuum in the pressure chamber and cavity, vacuum die casting can be divided into regular vacuum die casting and high vacuum die casting.

Fig. 5 Vacuum pressure die casting process flowchart
The key to high vacuum pressure casting is to achieve a high level of vacuum in a short amount of time.
Figure 6 shows the working principle diagram of suction type high vacuum pressure casting machine.
It uses vacuum to draw the metallic liquid into the pressure chamber and then quickly injects it to achieve a high degree of vacuum in the pressure casting process.
The principle of high vacuum die casting involves pumping air from the entire pressure chamber and cavity through a vacuum tube before pressure casting.
The vacuum pumping process must be completed as quickly as possible, creating a large pressure difference between the metallic liquid in the crucible and the pressure chamber, causing the metallic liquid to flow into the pressure chamber through the liquid riser and , then the pressure injection punch starts to apply pressure for injection.

Fig. 6 High vacuum and suction die casting machine
Oxygen-filled pressure casting
Oxygen-filled pressure casting involves filling dry oxygen into the pressure chamber and cavity of the pressure casting mold to replace the air and other gases present.
The oxygen-filled pressure casting process is shown in Figure 7.
This casting method is only applicable to aluminum alloys.
When aluminum alloy liquid is injected into the pressure chamber and casting mold cavity, it reacts with oxygen to form Al 2 Ó 3 which results in small, evenly distributed Al2O3 particles (with a diameter of less than 1um) , reducing or eliminating porosity and improving the compaction of the casting.
These small particles are dispersed throughout the casting, representing around 0.1% to 0.2% of the total mass and do not affect machining.

Fig. 7 Schematic diagram of oxygen-filled pressure casting
2. Casting equipment
Equipment used in the automotive casting industry must be fast, efficient and reliable, capable of operating continuously.
Given the strict quality standards for automobile castings, these casting machines must also have high precision.
Some of the main foundry equipment include: molding machines, sand mixers, core making machines, molding equipment, dust extraction equipment, casting furnaces, pressure casting machines, machining tools, shot blasting machines, cleaning machines and testing equipment.
In particular, the pressure casting machine and the casting furnace stand out.
2.1S melting furnace
The smelting furnace employs medium frequency power supply to establish a medium frequency magnetic field, thereby inducing an eddy current within the ferromagnetic material and generating heat, thus achieving the purpose of heating the material.
The medium frequency electric furnace uses a 200-2500 Hz medium frequency power supply for induction heating, melting and temperature maintenance.
This smelting furnace is mainly used to smelt carbon steel, alloy steel and special steel, as well as to smelt and increase the temperature of non-ferrous metals such as copper and aluminum.
Related Reading: Ferrous vs Non-Ferrous Metals
The equipment is compact, lightweight and highly efficient, with low energy consumption, fast melting and heating speeds, easy temperature control and high production efficiency.
The complete set of smelting furnace equipment consists of an intermediate frequency power cabinet, compensation capacitor, two furnace bodies, water-cooled cables and a reducer.
The furnace body consists of four parts: the furnace housing, the induction coil, the furnace liner and the tilt reduction gear.
The oven housing is made of non-magnetic materials.
The induction coil is a spiral cylinder constructed from hollow rectangular tubes, through which cooling water is circulated during the casting process. The copper bar coming out of the coil is connected to the water-cooled cable.
The furnace lining, located near the induction coil, is made of quartz sand.
The furnace body is tilted by direct rotation of the tilt reducer gear.
This gear features a two-stage turbine speed change and offers reliable and stable rotation with excellent self-locking performance. In the event of a power failure, the tilt mechanism will automatically stop to avoid any potential danger.
Both furnaces' tilt reduction gear motors can be controlled via the furnace selection switch, with a four-core rubber wire and distribution box, allowing the operator to stand in a convenient location while controlling the tilt and readjusting the oven body.
Currently, many foundry factories remain in an industrial 2.0 state and are in urgent need of updates with regards to environmental protection, automation, intelligence and security.
With the advent of Industry 4.0, all casting parameters will be recorded through sensors capable of operating in environments with extremely high temperatures.
Data such as the filling level of the heating furnace and the pollution level in the weld pool will become crucial information for building a smart, networked smelting furnace.
In the future, a foundry furnace factory may use a robot for cleaning operations.
The robot will have access to all oven parameters and will be able to take immediate action before pollution reaches critical levels.
2.2 D i.e. casting machine
Die casting machine is a machine that uses pressure casting. It consists of a hot compression chamber and a cold compression chamber, and is further divided into two types: straight and horizontal.
Under the pressure of the die casting machine, the molten metal is hydraulically injected into the mold, where it cools and solidifies.
After opening the mold, a solid metal casting can be recovered.
The die casting machine is composed of a clamping mechanism, injection mechanism, hydraulic system and electrical control system.
In addition, the machine also includes various components and bases, auxiliary devices and other parts.

Fig. 8 Basic structure of die casting machine
Over the past 30 years, the die casting machine has undergone significant advancements in terms of size, automation, modularity and flexibility.
In recent times, the integration and weight reduction of automotive die casting has generated new and higher requirements for die casting machines, with body-integrated forming technology being a particularly hot topic.
This has put heavy-duty pressure casting machines at the forefront of innovation. For example, Tesla recently purchased an 8,000-ton die-casting machine from Italian company DRA, which is 30% larger than the 6,000-ton die-casting machine used in the Model Y.
I predict this record will be continually broken as the industry evolves.
Let's examine why heavy-duty die casting machines are the future of the industry and what advantages they offer.
Advantage 1: Single-station material forming cost advantage
Figure 9 shows the Tesla Model Y frame structure. The yellow component represents a large integrated part of the rear body and wheel arch on top of the rear axle tower.
With the help of a large-scale die casting machine, this complex component that normally requires multiple stations and processes can be completed in a single operation.
As a result, it offers a significant cost advantage.
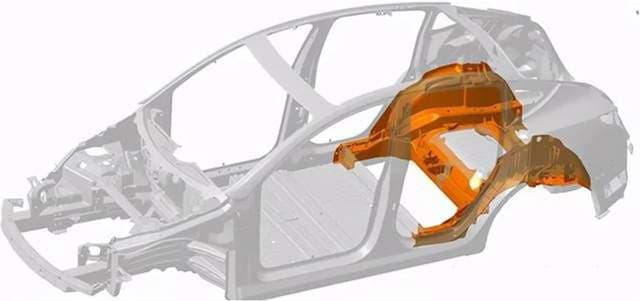
Fig. 9 structural diagram of the Y model frame
Advantage 2: Integration of Stamping and Welding and Optimization of the General Production Pace
Tesla aims to become the Toyota or Volkswagen of the new energy industry, making the pace of production a critical factor.
To increase the rate of the 8,000-ton pressure die casting machine, the technology can be used to create a cavity between the molten half-films on both sides during the pressure sealing process of the castings and to inject protective molten metal of temperature in the cavity.
As the cavity is in a negative pressure state, it effectively eliminates air bubbles generated by casting turbulence, contributing to material consistency and casting speed during pressure casting.
According to Tesla data, each casting operation involves injecting about 80 kg of aluminum alloy liquid into the cold chamber mold at a speed of 10 meters per second.
The production cycle time is around 85 seconds, with a production rate of 42 pieces per hour, representing an optimization of the current cycle time.
However, these advantages are accompanied by some challenges, such as exercise mechanics and mold design, that will need to be addressed as the industry continues to develop large-scale die casting machines.
3. Casting materials
3.1 C cylinder block
Traditionally, the material used in automotive engine blocks was cast iron, which still holds a dominant position in the industry today.
However, with the continuous improvement of engine performance and the demand for weight reduction, engine block material is undergoing rapid innovation.
There are three main areas of development:
- Improve the quality of cast iron to increase cylinder strength and performance.
- Using vermicular graphite cast iron to produce engine cylinder blocks, which offer greater strength and better fatigue performance, support thin-walled designs, withstand greater burst pressure, reduce cylinder deformation and increase horsepower by 10% to 20%. %.
- Aluminum alloy cylinder blocks, which are developing rapidly and represent the main direction for passenger car cylinder blocks.
Generally, the use of aluminum alloy is favored to reduce the weight and energy consumption of vehicles.
However, the limitations of aluminum alloy's thermal fatigue resistance and performance make its application in high-power engine blocks difficult and its cost is relatively high.
3.2C cylinder head
The engine cylinder head is an important application area for aluminum alloys, especially in the passenger car cylinder head market, which is largely dominated by aluminum alloy materials.
In the truck market, the use of cast iron for high-power engine heads is rare, and vermicular iron heads have become the preferred option, capable of solving the problem of cracks in gray cast iron heads.
3.3 C axis classification
The application of engine supercharging technology is a critical process in improving automobile performance for energy efficiency and emissions reduction.
Whether for gasoline or diesel engines, mainly in the truck market, the use of Pearlite Nodular Iron Crankshafts, widely used in the past, does not meet the requirements due to the increased explosion pressure of the engine, and has been replaced by steel materials forged as 40Cr.
However, with advances in technologies such as fillet rolling and induction hardening of Pearlite nodular iron crankshafts, nodular iron crankshafts continue to hold significant market share in the mid-horsepower passenger car and truck markets. low.
In addition, engine crankshafts made of isothermally hardened ductile iron have also been studied at home and abroad.
3.4 O others
Other automotive castings, such as support parts and structural components of engines and chassis, including various brackets, discs, casings and steering parts, are made of cast iron materials to meet performance requirements.
As automotive environmental protection requirements continue to evolve, the use of gray cast iron and cast steel is gradually declining, while high-performance ductile iron, magnesium alloy, aluminum alloy and special cast iron materials are becoming increasingly increasingly predominant.
3.5D development trend
Currently, cast iron is the main material used in automotive castings. In particular, the use of ductile iron has replaced many steel and gray iron castings, and the use of malleable iron in automotive parts has declined. Its superior strength and toughness, as well as ease of production, have increased its application.
Research and development of high strength and toughness ductile iron will be fundamental to its continued use in industry. Another promising material, isothermally quenched ductile iron, has excellent mechanical properties and has seen rapid development and successful application abroad, particularly in the production of crankshafts, gears, supports and structural parts.
Vermicular graphite cast iron, invented in 1948, has a narrow production range and limited performance, so its use has been limited. However, with advances in production control technology, vermicular graphite cast iron may have a future in the production of complex castings. It has higher tensile strength, modulus of elasticity and fatigue resistance than cast iron and aluminum, making it an ideal material for engine cylinder blocks and heads.
The trend towards reducing vehicle weight has led to the use of magnesium and aluminum alloys in automotive castings. For every 10% reduction in vehicle weight, fuel consumption is reduced by 5.5% and emissions are reduced by around 10%. Aluminum alloys have a lighter density (1/3 that of iron) and resistance equivalent to that of gray cast iron, which makes them ideal for manufacturing engine blocks and heads.
Aluminum alloys have seen rapid growth in recent years, and magnesium alloys, with their lighter density, have been applied to automobile steering wheels, seat frames, instrument panels, covers and other parts, as research and development application continues to advance.
Automobile Foundry Development Directorate
1. Casting parts development direction
Integrated design of automotive castings
With increasing demands for energy efficiency and environmental protection in the automotive industry, as well as the need to reduce production costs, the benefits of die-cast molding are being leveraged to achieve part integration through optimized design and structure. This involves combining several parts formed by stamping, welding, forging and casting, which results in reduced weight of the parts and fewer processing steps, resulting in lighter, high-performance components.
The trend towards integration of casting in the automotive industry is particularly pronounced in the casting of non-ferrous alloys.
To fully utilize the casting process for the production of complex structural castings, there has been an increase in the use of high-pressure castings with integrated design, such as interior door panels, seat moldings, instrument panel moldings, front moldings and firewalls. .
These castings are significantly larger in size compared to those currently produced and require a 4,000 to 5,000 ton or even larger die casting machine for production.

Fig. 10 Tesla Model Y integrated die-cast body
Lightness of automotive castings
To improve power performance, reduce fuel consumption and reduce exhaust gas pollution, whilst maintaining vehicle strength and safety, it is important to minimize the vehicle's total weight as much as possible.
For every 100 kg reduction in vehicle weight, fuel consumption per 100 km can be reduced by 0.3 to 0.6 liters.
A 10% reduction in vehicle weight can result in a 6% to 8% increase in fuel efficiency.
Due to growing concerns about environmental protection and energy conservation, weight reduction has become a trend in the global automobile industry, with lightweight automobile castings becoming a crucial development direction.
The achievement of weight reduction will be achieved mainly through the following three points:
1) Lightweight design
One of the main disadvantages of the equal thickness design is that it cannot fully exploit the structural performance and leads to an increase in the weight of the casting.
To optimize the design of parts and components, CAE analysis, topology optimization and other methods are employed so that the stress values of each part are equalized, resulting in inconsistent wall thickness. The material thickness of low stress parts is reduced to reduce the weight of the part.
Casting molding has the advantage of producing complex structural castings and various irregular cross-sections. During the design process, CAE or topology optimization is used to analyze the stress of components.
Based on the distribution of forces, the shape of the parts and the specific thickness of the local material are determined. The weight of the parts can be significantly reduced through reinforcement, opening holes and changing the section.
2) Application of alloy materials
The use of lightweight alloy materials such as aluminum and magnesium is the main weight-saving measure adopted by car manufacturers around the world.
Aluminum has a density that is only one-third that of steel and has excellent corrosion resistance and ductility. Magnesium has an even lower density, just two-thirds that of aluminum, and has excellent fluidity under high-pressure casting conditions.
Both aluminum and magnesium have high specific strength (the ratio of strength to mass), which makes them crucial for reducing vehicle weight and improving fuel efficiency.
However, it is worth noting that the cost of raw materials for light alloys such as aluminum and magnesium is significantly higher than that of steel materials, which limits their wider application in the automotive industry.
Despite the high cost of raw materials, the use of magnesium and aluminum castings in each vehicle continues to increase year after year. On the one hand, this increase in costs is offset by technological advances and, on the other hand, competition in the market is forcing car manufacturers to reduce their margins and adopt more light alloys.
However, the development of advanced forming technology is key to significantly increasing the use of light alloys and reducing the cost of magnesium and aluminum ingots.
3) High performance casting materials
Improving the performance of materials and allowing parts to withstand greater loads per unit weight is one of the effective methods to reduce the weight of castings.
Structural support castings make up a significant portion of automotive castings, making the development of your castings a key focus.
Through heat treatment and other techniques, the microstructure of the material can be changed to improve the strength, stiffness or toughness of the parts and effectively reduce their weight.
Isothermally quenched ductile iron has greater strength than ordinary cast steel and lower density. Its density is 7.1 g/cm 3 while that of cast steel is 7.8 g/cm 3 . This material has been widely recommended in recent years.
By adopting isothermally tempered ductile iron, castings can be 10% lighter than steel castings of the same size.
Table 1 Lightness effect of replacing isothermally quenched ductile iron material
Spare parts | Weight of isothermally quenched ductile iron (kg) | Cast steel weight/kg | Weight reduction rate /% |
Front suspension upper cross | 10:25 am | 25 | 59.00 |
Front suspension lower crosshead | 32.46 | 64 | 49.28 |
Upper front suspension spring support | 9:28 p.m. | 34.6 | 38.50 |
Lower rear suspension spring support | 20.74 | 33.16 | 37.45 |
Rear suspension lower cross member | 9:32 am | 50.16 | 84.58 |
In terms of aluminum and magnesium alloy castings, high strength and toughness materials are also used as substitutes.
Building on the weight savings achieved with the original lightweight alloys, the use of high-performance materials leads to further weight savings.
For example, General Motors in the United States uses high-performance AE44 alloy to replace the original aluminum alloy and employs high-pressure casting to produce the frame. This results in an additional weight reduction of 6 kg, in addition to the weight reduction achieved with the aluminum alloy.
Digital development of automotive castings
The integration of automobile casting development and digital technology greatly increases the level of casting technology and shortens the cycle of product design and prototype production.
Currently, digital manufacturing technology is widely used in the development of automotive castings.
During the design stage of casting structures and processes, 3D design software such as Pro/E, CATIA and UG are commonly used, and some advanced casting companies have implemented paperless designs.
Software such as Magma, ProCAST and Huazhu CAE are used to simulate the solidification process, microstructure, component segregation and material properties of automotive castings. These simulations also include the velocity field, concentration field, temperature field, phase field and stress field in the casting process, allowing for an optimized process scheme before mass production.
To keep up with the fast pace of automotive castings development, Rapid Prototyping Technology (RP) is widely used for rapid prototyping of automotive castings based on CAD/CAE design and development.
The original CAD/CAE data is used to create a casting prototype or mold prototype through layer-by-layer stacking through bonding, fusing or sintering. The former can be used for prototype casting samples through investment casting or plaster casting, while the latter can be used as a mold for sand core manufacturing and casting casting through core assembly molding.
Furthermore, the powder laser sintering (SLS) method can be used to directly produce sand cores and molds for trial production of castings.
For external molds with a relatively simple structure, a CNC machine tool can also be used for machinable plastic cam processing to obtain the core box and pattern required for experimental casting production, or the sand block can be processed directly to produce the sand mold for the outer mold.
In general, digital technology permeates the design, development and trial production of castings, resulting in a significant improvement in the speed and efficiency of castings development.
Currently, the main challenge is that digital technologies for design, analysis and rapid manufacturing are separated. Converting data from one step to another still requires a lot of tedious work.
In the future, it is expected that a unified data interface platform for the digital technologies applied at each stage of foundry development can be developed, a standardized data conversion standard can be established, and a seamless data conversion between different software can be achieved, further improving the squad's development speed.
2. Development direction of automobile casting technology
Thin-wall complex structure casting production technology
As the automotive industry evolves and the need for energy efficiency and emissions reduction increases, car parts become increasingly lighter.
Achieving lightness through a thin-walled design is a crucial development direction for engine blocks.
The 3mm thin-wall design of the cylinder block imposes strict requirements for core manufacturing and assembly in the core assembly and vertical casting process.
The core manufacturing center can achieve high intelligence and automation in core production.
The entire process, from adding raw sand and resin to sand mixing, core making, core repair, assembly, coating, drying, molding, core assembly and countersinking, can be highly automated, ensuring stable manufacturing quality of cores and assembly. , dimensional accuracy and coating drying quality, thus avoiding quality and dimensional risks caused by human factors and meeting the needs of large-scale cylinder core production.
This effectively solves the problem of unstable and high wastage rate during mass production.
Furthermore, the improvement in the dimensional accuracy of the sand core greatly reduces the workload and cleaning cost, effectively guaranteeing the 3mm wall thickness requirement.
Manufacturing technology for large structural parts made of aluminum and magnesium alloy
Large-scale structural casting of aluminum and magnesium alloy has become a crucial trend in response to the growing demand for energy efficiency, environmental protection and cost reduction in components. Its manufacturing technology has also become a focal point of current development.
At present, the main production methods of large-scale aluminum magnesium alloy structural parts include high-pressure casting, compression casting and low-pressure casting.
High pressure casting is the dominant production process due to its high efficiency and excellent product quality.
Efforts to improve the manufacturing technology of large-scale aluminum and magnesium alloy structural parts mainly focus on reducing air entrapment during high-pressure casting, minimizing the formation of air pockets, and addressing heat treatment issues. .
One solution to the problem of air entrapment is high vacuum pressure casting, which can effectively prevent the formation of air pockets.
This vacuum die casting technology has been successfully applied to the mass production of automotive structural castings, providing advanced forming techniques and processes for the production of high-quality alloy castings.
Precision casting technology for castings
With the advancement of automobile casting technology, precision casting molding has become a popular casting method. Castings produced using this method can be used without much cutting or even any cutting at all.
In recent years, the development of casting precision molding technology has been rapid due to improvements in the dimensional accuracy of castings. Various casting forming methods have emerged, including precision sand casting, lost foam casting, controllable pressure casting and die casting.
To eliminate casting defects, improve internal quality and expand the application of pressure casting, various process methods have been developed based on high pressure casting technology, such as vacuum casting, oxygen-filled pressure casting, rheological matrix or thixotropic of semi-solid metal. foundry.
Compression casting, in which the casting is filled and solidified under pressure, is widely used in the production of high-performance aluminum alloy castings such as aluminum alloy subframes. Compression casting has the advantages of stability, no metal spatter, reduced oxidation loss of molten metal, energy efficiency, safe operation and reduced casting hole defects.
The growing demand for automobile production requires castings to be of high quality, excellent performance, near-final shape, multiple varieties, low consumption and low cost. Casting parts make up about 15% to 20% of a complete vehicle, which means that the casting industry must continually adopt new technologies and materials to improve the overall level of casting.
Precision casting technology meets the requirements of automotive castings, and its application will cover various production processes of automotive castings.