Definition
Chamfering and filleting refer to the process of cutting the edges of a part on a given sloped or rounded surface.
Chamfering and filleting purposes
The purposes of chamfering and filleting are:
- To remove burrs from parts due to machining, making the product blunt and avoiding cuts to the user.
- To facilitate the assembly of parts.
- During the heat treatment of the material, it helps to relieve stress. With chamfering, the likelihood of cracks appearing is reduced, distortion is minimized and stress concentration problems are resolved.
Fillets and Chamfered
A fillet connects two objects through a 2D tangent arc or creates a circular transition between neighboring faces of a 3D solid.
The term “fillet” refers to the inner corner, while the outer corner is known as “round.” Both can be generated using the FILLET command.
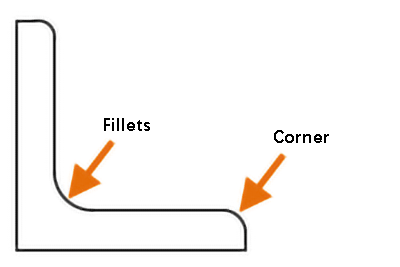
You can choose from the following types of objects to create fillets or fillets:
- 2D Polylines
- 3D Solids and Surfaces (not available in AutoCAD LT)
- Bows
- Circles
- Ellipses and elliptical arcs
- Lines
- Rays
- Splines
- Construction lines
These objects can be selected to define fillets or rounding.
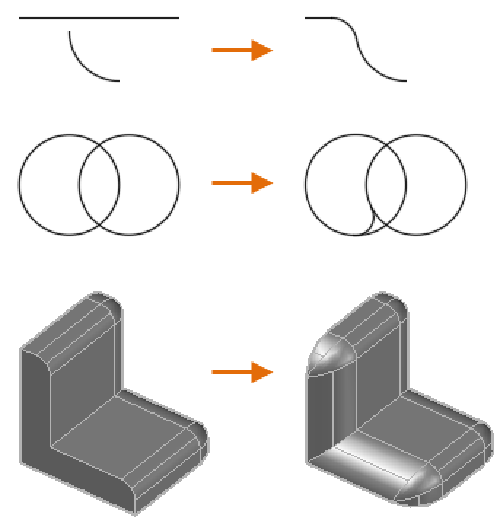
Note: Instead of inserting an arc, you can also use the BLEND command to connect two objects through a tangent spline.
Adding fillets or fillets to 2D polylines
You can use a single command to fillet or fillet a single vertex or all vertices of a 2D polyline. The “polyline option” allows you to add fillets or fillets to each vertex of the polyline.
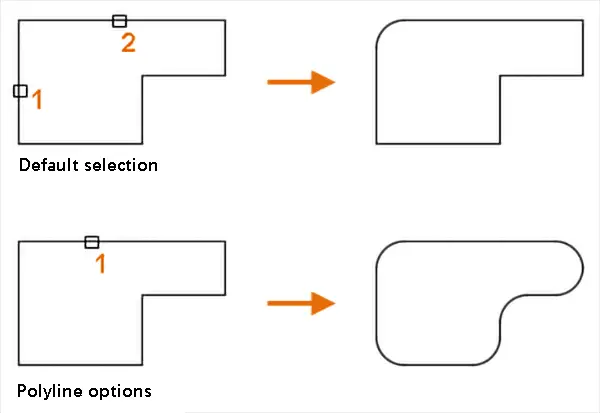
Note: You can also use the “multiple” option to add fillets or fillets to multiple sets of objects without leaving the command.
Adding fillets or fillets to polylines
To add fillets or fillets to polylines, you need to set the radius of the current fillet to a non-zero value and then select two intersecting segments. The distance between the selected segments must be long enough to accommodate the fillet radius, otherwise it will not be possible to insert the arc.
If there is an arc segment separating the selected segments, it is deleted and replaced with a new arc segment.
If the current fillet radius is set to 0 and the two selected segments are separated by an arc, the arc segment is deleted and the two segments are extended until joined.
Note: If you add fillets or fillets to the start and end segments of an open polyline, it is converted to a closed polyline.
Fillet parallelism
Creating fillets tangent to parallel lines, radii, or reference lines
You can create fillets tangent to two parallel lines, radii, or reference lines. In this case, the radius of the current fillet will be disregarded and adjusted to the distance between the two selected objects. The selected objects must be in the same plane.
The first object selected must be a line or ray, while the second object can be a line, ray or reference line.
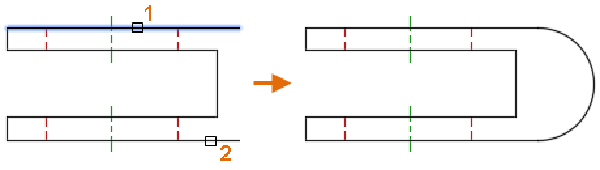
Crop and extend objects
By default, objects selected to fillet or fillet will be trimmed or stretched to fit the resulting arc. However, you have the option to use the “cut” feature to specify whether you want to modify the selected objects or not.
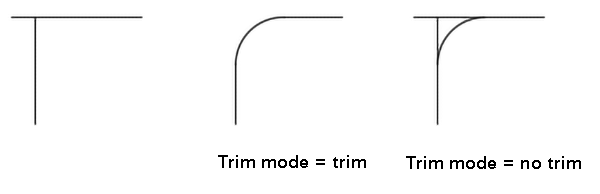
When the cut option is enabled and both segments of the polyline are selected, the added fillets or fillets will be connected to the polyline as arc segments.
Chamfers and chamfers
A chamfer or chamfer connects two 2D objects with an angled line or creates angled faces between neighboring 3D solids. The CHAMFER command can be used to create these angular connections.
The following object types can be selected to define chamfers or chamfers:
- 2D Polylines
- 3D Solids and Surfaces (not available in AutoCAD LT)
- Lines
- Rays
- Construction lines
These objects can be chosen to create the desired chamfers or chamfers.
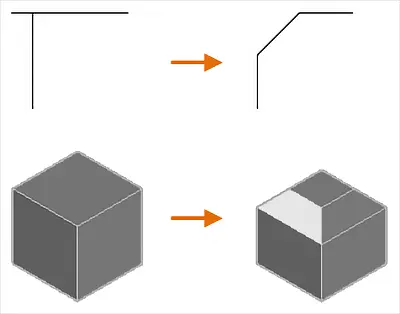
Length and angle of chamfer or chamfer
A chamfer or bevel can be specified using one of two methods: distance or angle.
The method for defining chamfers or chamfers is currently defined using the “method option”.
With the “distance” method, the angular line is determined by two distance values.
These values are used to crop or extend the selected objects so that they intersect the resulting angle line.
The first distance value applies to the first selected object, while the second distance value applies to the second selected object.
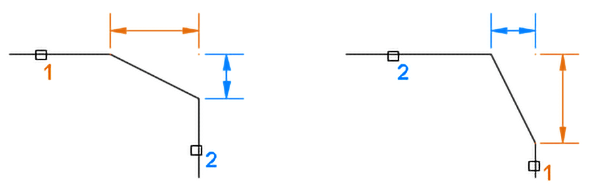
Angle: The angle line is determined by the distance and angle values.
The distance and angle values are used to crop or extend the selected objects so that they intersect the resulting angle line. The distance value has a direct impact on the first selected object.
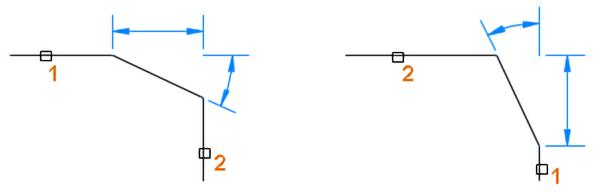
Note: If the distance and angle values are set to zero, selected objects will be cut or extended until they intersect without forming angled lines.
Adding chamfers and chamfers to 2D aggregates allows you to insert chamfers or chamfers on a single vertex or all vertices of a 2D polyline with a single command.
You can use the “polyline option” to add a chamfer or chamfer to each vertex of the polyline.
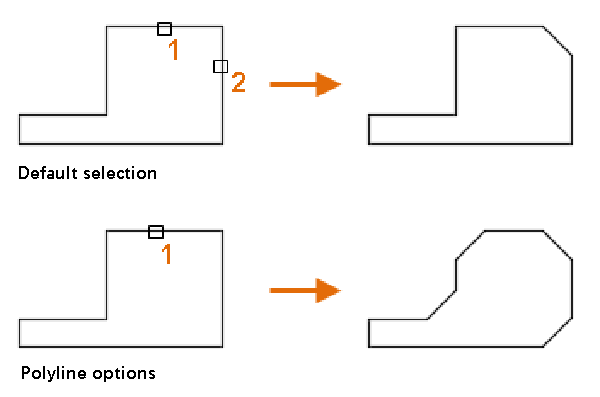
Note: You can also use the “multiple” option to add chamfers and chamfers to multiple groups of objects without having to exit the command.
To add a chamfer or chamfer to a polyline, set the current distance or angle value to a nonzero value and select two intersecting 2D polyline segments.
The distance between the selected segments must be sufficient to accommodate the angle line, otherwise the angle line cannot be inserted.
If the selected segments are separated by only one arc segment, the arc segment is deleted and replaced with a new segment that represents the chamfer or chamfer.
If the current distance and angle values are set to zero and the two selected segments are separated by an arc segment, the arc segment is deleted and the two segments are extended to intersect.
Note: Creating chamfers for the start and end segments of an open polyline will result in a closed polyline. Selected objects will be cut or stretched to form angled lines.
By default, objects selected to define chamfers or chamfers will be trimmed or extended to create angled lines.
You can use the “cut option” to specify whether the selected objects should be modified or not.
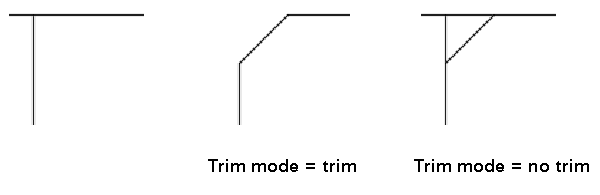
If the “cut option” is enabled and two segments of a polyline are selected, the added chamfer or chamfer will be connected to the polyline to form a new segment.
5 main design principles
(1) Principle of inner circle and outer chamfer (machined part)
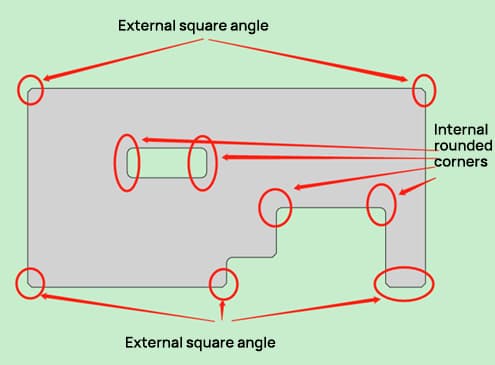
- The machined parts are processed with rotary tools, with internal filleted corners and chamfered external corners.
- Within the same part, the outer chamfer and inner fillet must be a consistent size to reduce tool changes. Note: Here, “chamfer” means “square”.
(2) Inner circle and outer circle principle for sheet metal parts
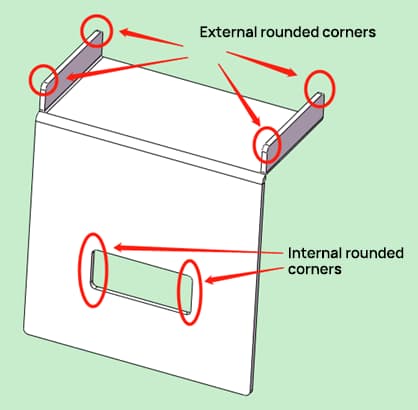
- Sheet metal parts undergo laser processing, different from conventional cutting.
- Both the inner and outer edges of the workpiece have consistent fillets.
- The fillet range is R=2~5.
(3) Principle of cleanliness and assembly aesthetics
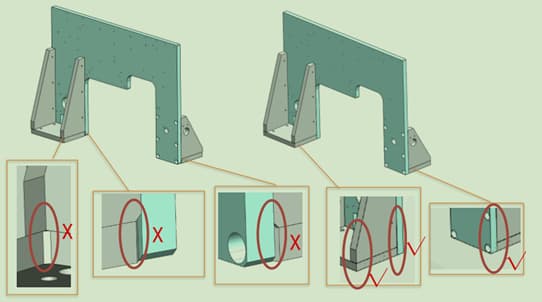
- Chamfering ensures an organized and attractive assembly between parts.
- No prominent sharp edges, ensuring safety during handling, assembly and use.
- If not specified, the default chamfer is C0.5.
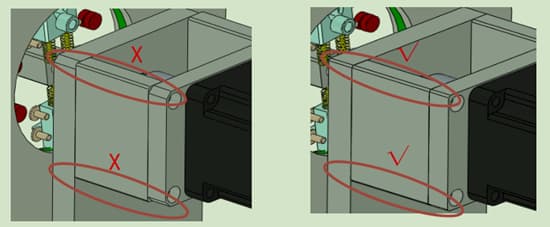
Note: Sometimes the decision to chamfer a part is not just based on the part itself, but also its assembly relationship to other parts.
(4) Principle of stress relief and strength enhancement
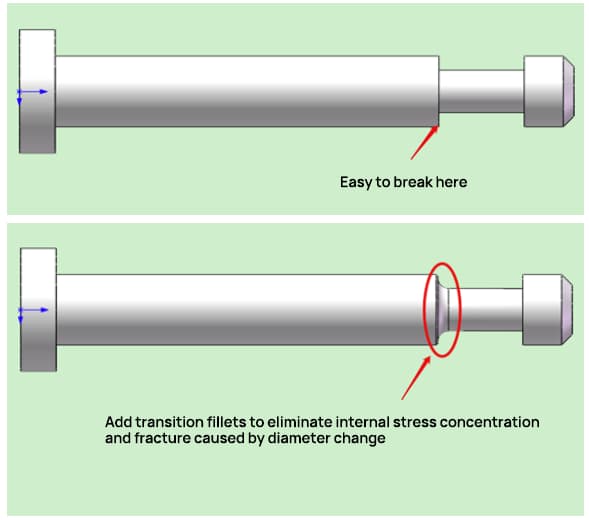
- During heat treatment of the material, internal stresses can concentrate; the introduction of transition fillets can mitigate deformations and fractures caused by these stresses.
- For cantilever parts, adding a fillet helps increase their strength.
(5) Guiding Principle
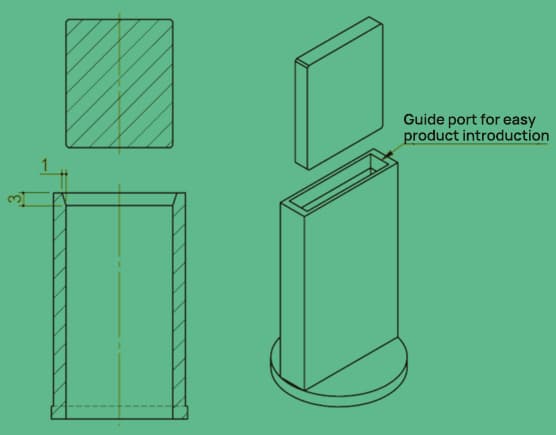
- When defining product cavities, angled chamfering is required to facilitate insertion.
- To facilitate assembly, the parts that fit together require angled chamfers.