1. Overview
The frequency of damage to induction hardened gears during use is high, especially for surface hardened gears such as the second shaft gear of a shear rocker and sun gears with a modulus of 8-10. These gears often suffer damage in the form of corrosion, peeling, and broken teeth.
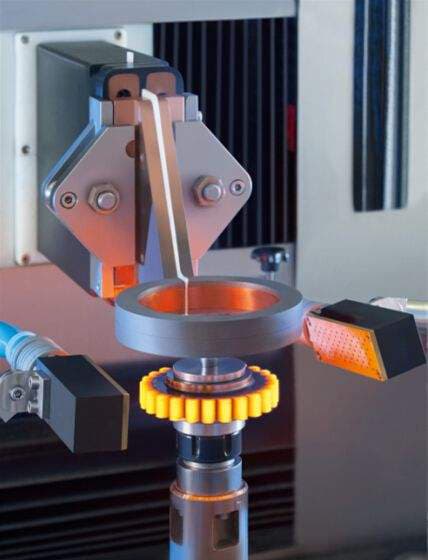
After analysis, we found that there is no hardened layer below the pitch circle of the gear teeth, and the tooth center and tooth root are not hardened, which means that the heat penetration depth during surface hardening does not reach these areas .
Although we can theoretically control the depth of the hardened layer by adjusting the electrical parameters of induction heating equipment, it is difficult to achieve precise control in practice due to several factors that can affect the depth.
Current quality control of the hardening process relies on random inspections and damage testing, which are time-consuming and expensive. Given our company's focus on producing a variety of products in small batches, we need to find more efficient testing methods.
Non-destructive testing has the benefits of being non-destructive, having a high testing rate, being highly efficient, and being cost-effective.
To test the heat penetration depth and the effective depth of the hardened layer of the gears of modules 6, 8, 9 and 10, we used QNET type equipment, a second generation multi-channel non-destructive measuring system for hardened layer depth manufactured by IZFP, Institute of Non-Destructive Testing and Fraunhofer Institute in Germany. Orthogonal tests and comparison tests are performed using physical and chemical anatomy.
2. Theoretical basis of the test
The heat treatment process of induction hardening gears is: carburizing → quenching and tempering → surface hardening.
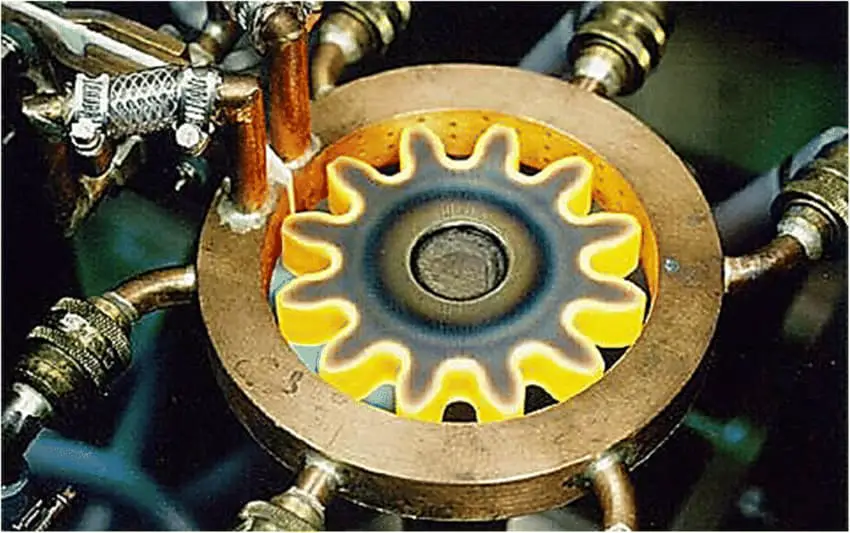
The gear material used is normally 18Cr2Ni4WA or 20Cr2Ni4A, which is a type of fine-grained steel. After induction hardening, the induction heating layer undergoes recrystallization.
The rapid induction heating process results in a thinner, smaller and denser structure on the surface, which makes it difficult for common ultrasonic waves (1-5 MHz) to penetrate the induction layer.
Additionally, the gear undergoes carburization during induction hardening. Fine granular carbides in the infiltrated layer help to stabilize the structure by fixing the grains on the surface of the infiltrated layer, making them even finer. However, the dense surface hardening layer and the heat penetration depth are transparent to 20 MHz ultrasonic waves.
When the 20 MHz ultrasonic wave reaches the interface between the hardened layer and the heat penetration depth, backscattered echoes occur, as shown in Figure 1 and Figure 2.
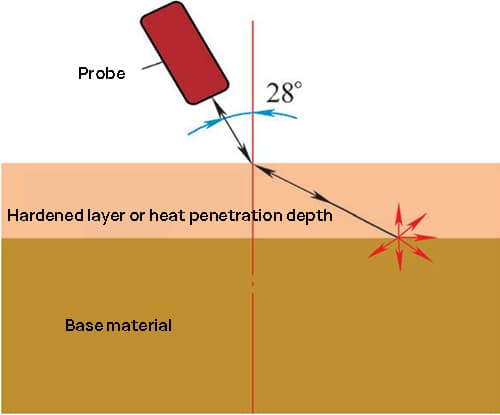
Fig. 1 Ultrasonic backscatter detection method

Fig. 2 Ultrasonic backscatter echo
The heat penetration depth and the hardened layer depth of the surface hardened gear can be obtained using the following formula.
R ht =(vtcos β)/two
Where,
- R ht — hardened layer or heat penetration depth (mm);
- V — speed of sound in the tested material (mm/s);
- t — acoustic wave time(s) from the part surface to the interface;
- β — Ultrasonic refraction angle of the hardened layer (°).
Currently, the 18Cr2Ni4WA and 20Cr2Ni4A gear teeth materials used in production are martensitic steels.
Data and measurements indicate that for gear teeth with modulus 10 or less, as long as the gear teeth are heated to the austenitic temperature range and then air cooled, the core hardness will be at least 36.0 HRC.
Therefore, the heat penetration depth of induction hardened gears can reach the core of the gear teeth, ensuring that the hardness of the core meets the technical requirements.
3. Detection scheme
Given the current situation of the surface hardened gear sample, we have developed the following inspection plan:
(1) Use a high-resolution induction hardening layer thickness detector imported from Germany.
(2) Choose and establish appropriate lower and upper limit values (LN and UN).
(3) See Table 1 for the technical requirements of four types of surface-hardened carbureted gears with shear moduli of 6, 8, 9, and 10.
Table 1 Technical quenching requirements for test gear samples
Gear Number: | Module | Material texture | Penetration depth into the tooth surface / mm | Tooth Core Hardness (HRC) | Matrix hardness (HRC) |
1 | 6 | 18Cr2Ni4WA | 1.0-1.4 | 36.0-42.0 | 27.0~32.0 |
two | 8 | 20Cr2Ni4A | 1.2-1.6 | 36.0-42.0 | 27.0~32.0 |
3 | 9 | 18Cr2Ni4WA | 2.0~2.6 | 38.0~44.0 | 27.0~32.0 |
4 | 10 | 18Cr2Ni4WA | 2.0~2.6 | 38.0~44.0 | 27.0~32.0 |
(4) Choose a high-frequency angled probe (20 MHz) and a straight probe to detect the tooth surface and top respectively.
(5) The effective hardened layer depth and heat penetration depth of the gear samples were determined through microhardness testing and metallographic macroanalysis, respectively.
(6) The accuracy and reliability of the END data were evaluated by comparing the END method with conventional microanalysis and metallography techniques.
4. Test results and analysis
Fraunhofer IZFP's multi-channel non-destructive measuring system, P3213QNET, was used to test five different types of gears. Non-destructive tests and physical and chemical tests were carried out on the top of the tooth, the surface of the tooth and the root of the tooth, using narrow screen blocks on the top of the tooth, the plane of the tooth and the root of the tooth, respectively.
The results are shown in Table 2.
Table 2 Comparison of test results from the two methods
Gear Number: | 1 | two | 3 | 4 | |
Module | 6 | 8 | 9 | 10 | |
Distance between tooth crest and tooth center / mm | 13.5 | 17.8 | 17.1 | 22 | |
END results | Effective hardened layer of tooth surface pitch circle / mm | 2.2 | 2.46 | 3.26 | 2.12 |
Heat penetration depth/mm | 9.44 | 14.88 | 12.62 | 9.96 | |
Tooth Core Hardness (HRC) | 36.0~44.0 | 27.0~32.0 | 27.0~32.0 | 27.0~32.0 | |
Physical and chemical test results | Effective hardened layer of tooth surface pitch circle / mm | 1.53 | 2.55 | 3.05 | 1.77 |
Heat penetration depth/mm | 92 | 152 | 122 | 92 | |
Tooth Core Hardness (HRC) | 7.0~29.0 | 7.0~28.0 | 7.0~29.0 | 7.0~29.0 |
According to the test results, the following conclusions can be drawn:
(1) Values obtained from non-destructive testing and anatomical analysis methods for detecting thermal penetration depth are in agreement.
(2) The results of indirect non-destructive tooth center hardness tests are consistent with those obtained through anatomical analysis.
(3) For effective detection of hardened layer depth:
① When the probe can reach the pitch circle of the gear teeth (m = 8, m = 9), the values obtained in the non-destructive tests are in agreement with those from the anatomical analysis.
② When the probe cannot reach the pitch circle, the data deviation is significant.
(4) Through a comparison of non-destructive testing and physical and chemical testing, the non-destructive testing method can be used to determine the heat penetration depth, the depth of the hardened layer on the surface and the hardness of the hardened gear core on the surface.