Differences between hydraulic motors and hydraulic pumps
The hydraulic pump is a conversion device that transforms the mechanical energy of an electric motor into hydraulic energy.
It produces flow and pressure and is designed to have high volumetric efficiency.
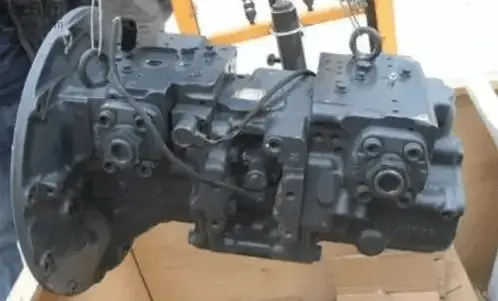
The hydraulic motor is a conversion device that converts fluid pressure energy into mechanical energy, generating torque and speed. It was designed to have high mechanical efficiency.
As a result, the hydraulic pump is considered an energetic device, while the hydraulic motor is considered an actuator.
The output shaft of the hydraulic motor must be able to rotate both forward and backward so that its structure is symmetrical.
On the other hand, some hydraulic pumps (such as gear pumps and vane pumps) have specific regulations regarding direction, allowing only rotation in one direction and not allowing arbitrary changes in direction.
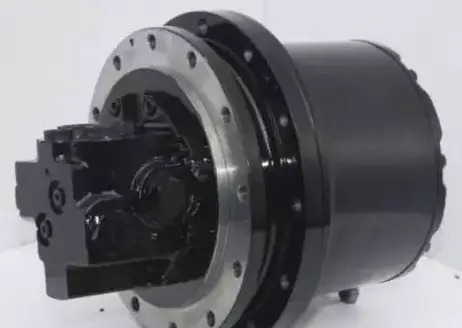
In addition to the oil inlet and outlet ports, hydraulic motors have separate oil leakage ports.
Hydraulic pumps, with the exception of axial piston pumps, typically only have oil inlet and outlet ports, and any oil leakage is connected to the oil inlet.
The volumetric efficiency of hydraulic motors is lower compared to hydraulic pumps.
Normally, the working speed of hydraulic pumps is relatively high, while the output speed of hydraulic motors is low.
Furthermore, gear pumps have a large oil suction port and a small oil discharge port, while hydraulic gear motors have equal-sized suction and discharge ports.
The number of teeth of a gear motor is more compared to that of a gear pump.
The vane of a vane pump must be installed diagonally, while the vane of a vane motor is installed radially.
The vane motor blades are pressed against the stator surface with the help of a root spring whereas the vane pump blades are pressed against the stator surface with the help of pressurized oil and centrifugal force.
Both hydraulic motors and hydraulic pumps work by changing the volume of the sealed working chamber, but due to their different uses, they have many differences in structure and generally cannot be used interchangeably.
Hydraulic pumps and motors are crucial components in all excavators and share similar structure and operating principle. Some people are often confused between these two elements and want to understand the difference between a hydraulic motor and a pump. Let's delve deeper into this.
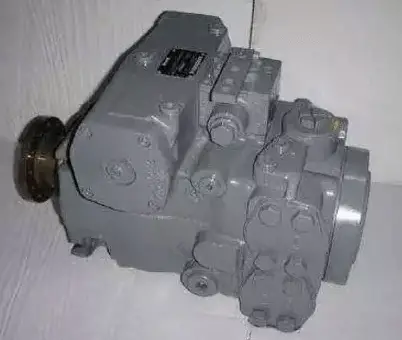
A hydraulic pump transforms mechanical energy (such as the rotation of an engine) into pressure energy and directs pressurized oil to areas where work is needed throughout the system.
On the other hand, a hydraulic motor converts pressure energy into mechanical energy, using pressurized oil to turn the blades inside the hydraulic motor, driving machinery connected to the hydraulic motor shaft to do the work.
Types of hydraulic pumps and hydraulic motors
Hydraulic pump classification
Divided by structure:
- plunger pump
- gear pump
- vane pump
Divided by whether the offset can be adjusted:
- fixed displacement pump
- variable displacement pump
Divided by oil discharge direction:
- unidirectional pump
- bidirectional pump
Divided by pressure level:
- low pressure pump
- medium pressure pump
- medium high pressure pump
- ultra high pressure pump
Gear Pump:
Relatively small in size, simple in structure, with low oil cleaning requirements and an affordable price, gear pumps are widely used in various industries, such as mining equipment, metallurgical equipment, construction machinery, engineering machinery, agricultural machinery and forestry.
However, the pump shaft is susceptible to unbalanced forces, severe wear and large leaks.
Vane pump:
- double acting vane pump
- single acting vane pump
The pump has uniform flow, stable operation, low noise, higher operating pressure and high volumetric efficiency, although it has a more complex structure compared to a gear pump. High pressure vane pumps are commonly used in hydraulic systems of lifting and transport vehicles as well as in engineering machinery.
Plunger Pump:
High volumetric efficiency, low leakage, ability to operate under high pressure and wide use in high power hydraulic systems are the main features of plunger pumps. However, its complex structure, high demands for material quality and processing precision, and high cost, together with the requirement for highly clean oil, can be disadvantages.
Plunger pumps are widely used in automotive diesel engines to supply fuel at high pressure.
Classification of hydraulic motors
Classified by Structure:
- Gear type motor
- Vane type engine
- Plunger type motor
Classified by speed and torque range:
- High speed motor
- Low speed motor
Geared hydraulic motor:
- The simple structure and relatively low cost make it ideal for applications requiring high speeds, low torques and low motion stability. Examples include grinders and fans.
Vane type hydraulic motor:
- With a small moment of inertia, these motors offer sensitive response, low volumetric efficiency and smooth mechanical characteristics, making them suitable for applications with medium speeds, low torques and frequent starts and stops.
Axial plunger motor:
- Featuring high volumetric efficiency and a wide tuning range, these motors offer good low-speed stability but may lack impact resistance. Ideal for high pressure systems with strict cleaning requirements.
Hydraulic pumps and motors are energy conversion elements in hydraulic transmission systems.
What is the difference between the two? How can they be distinguished?
In theory, hydraulic motors and pumps are reversible.
- If driven by a motor, the output will be pressure energy (pressure and flow), becoming a hydraulic pump.
- If there is oil input under pressure and mechanical energy (torque and speed) output, then it is a hydraulic motor.
Structurally, the two are similar in design.
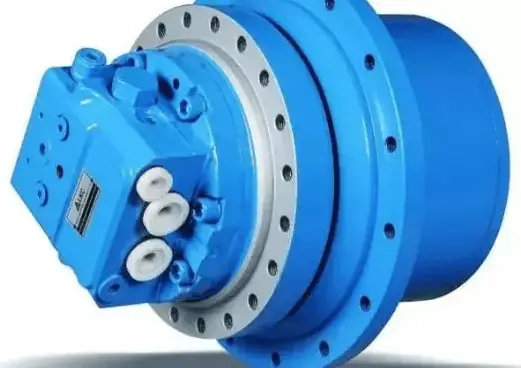
Hydraulic motors and pumps have similar basic components: a closed chamber that can periodically change its volume and an oil distribution mechanism.
Both hydraulic motors and pumps operate on the principle of suction and discharge, exploiting changes in the sealed working volume.
In the case of hydraulic pumps, oil is sucked in when the working volume expands and high-pressure oil is expelled when the working volume decreases.
For hydraulic motors, high-pressure oil is introduced when the working volume expands, and low-pressure oil is released when the working volume decreases.