Bearings are an important component in modern machines. Its main function is to support the rotating parts of the machinery, reduce the friction coefficients during their movement and guarantee their rotational precision.
As manufacturing technology advances, there is an increasing demand for bearings. However, problems such as premature damage and short lifespan have become more apparent.
Today I want to share with you some methods and techniques to extend the life of bearings.
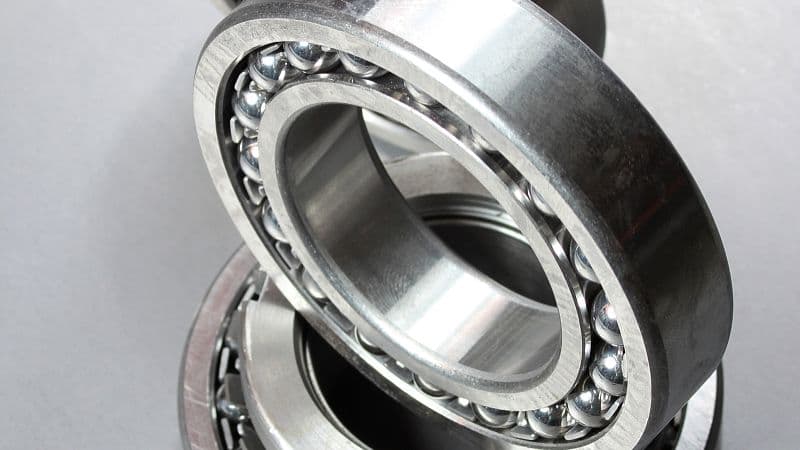
How to improve bearing life?
The number of rotations or hours that a bearing can withstand before spalling occurs under a given load is known as bearing life.
Within this life, the bearing should only suffer initial fatigue damage to any of its races or rolling elements.
However, in practical use, it can be observed that bearings with the same appearance and operating conditions have significantly different useful lives.
What causes this? Here are some points I summarized:
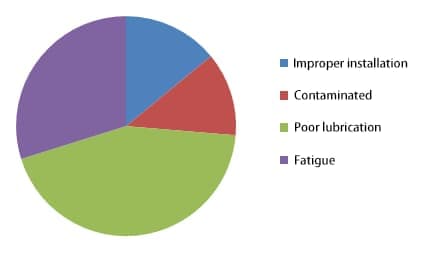
1. Incorrect installation (about 16%)
1) Excessive force during installation and hitting the bearing with a hammer will cause greater damage and deformation.
2) Installation deviation or failure to install the bearing correctly may result in poor bearing clearance. The inner and outer rings are not at the same rotational center, resulting in eccentricity.
Recommendation: Use suitable or professional bearing installation tools and use specialized equipment to check after installation.
During assembly or installation, if the bearing internal clearance is too large or too small, or in some cases, if the preload is too high, it can cause premature damage and reduced bearing life. Improper assembly and installation of bearings can not only cause downtime and costly repairs, but also have additional negative effects, such as impacting the operation of other parts and reducing their service life.
Following the equipment manufacturer's user manual for assembly, installation and regular maintenance is the best way to avoid problems. If time is of the essence, adjustments can be made by advancing the adjusting device or removing shims to correct a loose tapered roller bearing unit.
On the other hand, if the bearing is adjusted too tightly, it may overheat and become damaged, necessitating bearing replacement. Bearing assembly and installation processes must be accurate, repeatable and verifiable upon completion.
It is also essential to consider the parameters of other parts to optimize system performance. Additionally, using equipment in accordance with OEM requirements and defining appropriate predictive maintenance tasks, such as lubricant or grease monitoring, which should include root cause analysis of failures, can significantly extend the operational life of problematic equipment. Proper lubrication and maintenance are essential, as is proper installation and use, complemented by full use of existing condition monitoring equipment.
Failure to comply with installation and maintenance requirements may lead to equipment failure, posing a significant safety risk. Performing a thorough inspection after bearing installation is crucial as it directly affects the life and accuracy of the machine.
Improper installation can cause vibrations, excessive noise, low precision, increased temperature and even the risk of seizures and burns; on the other hand, proper installation not only ensures accuracy but also significantly extends the service life.
2. Contamination (about 14%)
Contamination can also cause premature bearing failure, which refers to the entry of sand, dust, metal chips, etc. into the bearing.
The main reasons include:
1)Open the bearing packaging too soon before use, causing contamination;
2)The installation environment is not clean, causing contamination;
3) The bearing working environment is not clean and the working medium is contaminated, etc.
Recommendation: If possible, do not open the bearing packaging before use; maintain a clean installation environment and clean the bearing before use; improve the bearing sealing device.
3. Poor lubrication (about 50%)
According to research, poor lubrication is one of the main causes of premature bearing failure, which includes:
1)Failure to add lubricants or lubricating oil in a timely manner;
2)Lubricants or lubricating oil not added correctly;
3)Inadequate selection of lubricants or lubricating oil;
4)Incorrect lubrication method, etc.
Recommendation: Select the correct lubricant or lubricating oil and use the appropriate lubrication method.
Selecting the appropriate lubrication system and high-quality lubricants is critical. The lubricating oil film separates the contact surfaces, providing essential protection against corrosion and wear.
Therefore, for all rotating or reciprocating parts, especially bearings and gears, to function normally, the oil film is indispensable. In splash or circulating lubrication systems, the oil film also facilitates heat transfer.
Factories often face unnecessary downtime and equipment deterioration due to inadequate lubrication. Insufficient lubrication can lead to increased wear and increased temperature, causing excessive wear and/or premature bearing failure and damage.
Excessive lubrication, especially in high-speed equipment, can generate excessive heat due to oil agitation, leading to chemical degradation of the lubricant and bearing damage. Correct lubrication and regular maintenance can prevent bearing damage caused by lubrication problems.
To ensure adequate lubrication, you must:
1) Follow the usage guidelines defined by the equipment manufacturer for each device;
2) When adding grease, make sure it is filled between the bearing rolling elements and the housing (or shield) to ensure adequate and complete lubrication of the critical raceway surfaces;
3) Pay attention to when the bearing should be lubricated;
4) Monitor equipment gauges to detect early signs of problems, such as temperature fluctuations and/or abnormally high temperatures;
5) Pay attention to abnormal noises or vibrations from the equipment;
6) Observe any lubricant leaks;
7) Regularly sample the lubricant and check for contamination.
4. Fatigue (about 34%)
Fatigue failure is a common form of bearing failure. Reasons for fatigue failure may include:
1) Bearings operating under long-term overload;
2)Failure to carry out timely maintenance;
3)Inadequate maintenance;
4) Equipment aging, etc.
Recommendation: Select the appropriate bearing type and regularly replace worn bearings in a timely manner.
5. Bearing post-installation inspection
After installing the bearing, it is essential to carry out an inspection.
(1) Inspect the installation position
First, check whether the moving parts collide with the fixed parts after installing the bearing, whether the lubricant can flow smoothly into the bearing, and whether the sealing and axial clamping devices are installed correctly.
(2) Radial clearance inspection
Except for bearings installed with a predetermined interference fit, the radial clearance must be checked. Deep groove ball bearings can be manually rotated for inspection for smooth, flexible movement without vibration or sideways wobble.
Cylindrical and spherical roller bearings can be inspected using a feeler gauge. The gauge must be inserted between the roller and the bearing ring, with an insertion depth greater than half the length of the roller. When radial clearance cannot be measured with a feeler gauge, axial movement of the bearing can be measured as an alternative to reducing radial clearance.
Generally, if the bearing inner ring has a tapered bore, the axial movement at the tapered surface will be approximately 15 times the reduction in radial clearance. Some bearings, such as angular contact ball bearings and tapered roller bearings, allow post-installation adjustment of radial clearance.
Others, such as deep groove ball bearings, self-aligning ball bearings, cylindrical roller bearings, and spherical roller bearings, are pre-adjusted during manufacturing and cannot be adjusted after installation.
If these bearings do not meet the required specifications after installation, indicating that the radial clearance of the assembly is too small, this could mean improper bearing selection or incorrect machining of the mounting area.
In these cases, the bearing must be removed, the cause identified and corrected before reinstallation. Excessive slack is also problematic.
(3) Inspect the bearing tightness against the shaft shoulder
In general, bearings installed with a tight interference fit should press firmly against the shaft shoulder. Inspection methods include the light method, where a lamp is pointed at the junction between the bearing and the shaft shoulder to check for light leakage.
No leaks indicate correct installation; uniform leakage around the shaft shoulder suggests that the bearing is not pressed hard enough, requiring additional pressure; Partial leakage indicates an inclined installation, requiring adjustment with a hammer, brass rod or sleeve.
The thickness gauge method starts with a 0.03mm thickness gauge. Inspect several points around the circumference of the inner ring end face and shaft shoulder for play. Uniform clearances indicate that the bearing is not seated correctly, requiring more pressure on the inner ring to tighten against the shaft shoulder.
If increased pressure does not achieve tightness, the shaft neck fillet radius may be too large, binding the bearing and requiring fillet modification. If the feeler gauge passes only at certain points, the bearing must be removed, adjusted, and reinstalled.
For bearings installed with an interference fit in the bearing seat bore, the tightness of the outer ring end face against the housing shoulder can also be checked with a feeler gauge.
(4) Post-installation inspection of thrust bearings
When installing thrust bearings, check the perpendicularity of the shaft ring and the shaft centerline. This can be done by attaching a dial indicator to the end face of the housing and rotating the bearing while watching the dial.
If the dial indicator needle wobbles, it suggests that the shaft ring and center line are not perpendicular. For deep casing holes, an extended comparator head can be used. Properly installed thrust bearings automatically accommodate the movement of the rolling elements, ensuring that the elements roll correctly between the upper and lower races.
Incorrect installation not only impairs bearing function, but also leads to severe wear on the contact surfaces. As the shaft ring and seat ring are not easily distinguishable, extra care is required during assembly to avoid errors.
In addition, a gap of 0.2-0.5 mm between the thrust bearing seat ring and the bearing seat hole compensates for machining and installation inaccuracies. This clearance allows the bearing ring to automatically adjust during operation, preventing contact and friction for normal operation. Otherwise, serious damage to the bearing could occur.
(5) Check whether bearing noise, temperature rise and vibration meet the requirements
Normally, the bearing operating temperature should remain below 90°C. Temperatures exceeding this limit may cause the bearing to overheat, anneal or burn, reducing its useful life.