Before cutting any sheet, the distance between the laser focal point and the material to be cut must be properly adjusted.
Different focal point positions can result in varying levels of accuracy in the cross-section of the cut material, as well as differences in bottom slag and even material cutting failure.
The choice of the focal point position of the laser cutting machine will depend on the part and material to be cut.
To make the right choice, it is important to inspect the laser cutting machine before using it to ensure high-quality cuts and proper machine operation.
Positive focus cut
Positive focus cutting refers to positioning the focal point above the material being cut, with the focal point located at the top of the workpiece.
For oxygen cutting of carbon steel, a positive focus is preferred.
The cutting width at the bottom of the part is greater than at the top, which helps remove slag and allows oxygen to reach the bottom of the part to facilitate full oxidation.
Within a given focal range, a larger positive focal spot leads to a larger spot size on the plate surface, which results in better preheating and heat supplementation around the cut, and results in a smoother cut surface and shiny carbon steel.
For 10,000 watt laser pulse cutting of stainless steel thick plates, positive focus cutting provides stable quality, which is beneficial for slag removal and reduces the risk of reverse blue light, as shown in Figure 1.
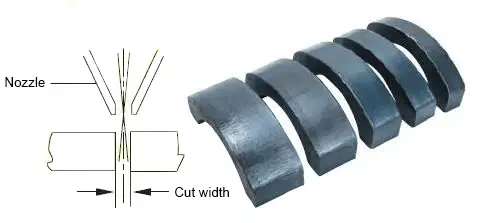
Fig. 1 The effect of a 12,000 W laser cutting carbon steel with a positive focal point
Negative focus crop
Negative focus cutting refers to the positioning of the focal point within the workpiece.
In this mode, the focal point is further away from the cutting surface, resulting in a relatively larger cutting width within the part compared to positive focus cutting. However, a higher cutting air flow and sufficient temperature are required.
Negative focus cutting is suitable for cutting stainless steel, resulting in a uniform cutting surface pattern and a good cross section.
When drilling the board prior to cutting, a negative focus is preferred to ensure minimum drill point size and maximum energy density.
The deeper the drilling position, the larger the negative focus point will be, as shown in Figure 2.
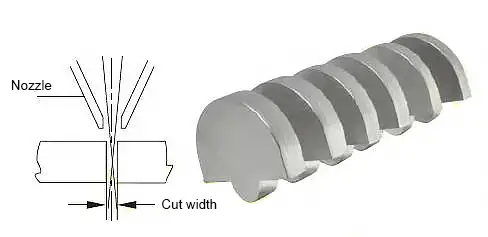
Fig. 2 The effect of a 6000 W laser with negative focus on stainless steel
Zero Focus Crop
Zero focus cutting refers to the positioning of the focal point on the surface of the workpiece. In this case, the cutting surface near the focal point is relatively smooth, while the bottom surface away from the focal point appears rough.
Zero focus cutting is mainly used in cutting thin sheets with continuous lasers and cutting layers of metal sheets with pulsed lasers through peak power vaporization.
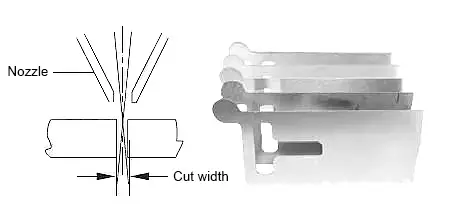
Fig. 3 2000 W laser cutting of thin carbon steel sheets with zero focus
A Complete inspection provides a better cut
1) Cleaning the lens.
The lens of the 10,000 watt cutting head is crucial for the 10,000 watt laser cutting machine. Its cleanliness directly impacts the processing performance and cutting quality of the machine.
If the lens is dirty, it can not only negatively impact cutting results, but also cause damage to the internal components of the cutting head and laser output head.
Carrying out a pre-check before cutting can prevent serious damage.
The red light detection method is shown in Table 1.
Table 1 Red light detection method
Nozzle | Single nozzle over 2mm | Clean lens | Dirty lens |
Methods | 1. Red light is indicated when the laser is on; | ![]() |
![]() |
2. The white paper is about 300mm away from the cutting head nozzle to view the red light; | |||
3. If there are black dots or irregular black objects in the red light, the lens is dirty and needs to be cleaned before cutting and debugging. |
2) Coaxial debugging.
The coaxiality of the nozzle exit hole and the laser beam is a crucial factor that affects the cutting quality. Inconsistencies caused by misalignment of the nozzle and laser beam can result in an uneven cutting surface. In severe cases, the laser beam can hit the nozzle, causing the nozzle to overheat and burn out.
The coaxial debugging method is shown in Table 2.
Table 2 Coaxial debugging method
Nozzle | Nozzle 1.2mm | Normal coax | Abnormal coax |
Tools |
Adhesive tapes | Three coaxial
![]()
|
![]()
|
Methods | 1. Coaxial adjustment at focal point 0, so that the laser is in the center of the nozzle; | ||
2. Light at focal point ±6mm; | |||
3. If the focus 0 and ±6mm reaching the light spot are in the center of the nozzle, this is normal.
Otherwise, you will need to replace the cutting head or shift the laser light path. |
(3) Check the point distribution.
The shape of the laser spot directly reflects the distribution of laser energy in the lateral direction. The roundness of the point indicates the uniformity of energy distribution in different directions.
A highly rounded point with uniform energy distribution in all directions can ensure a smooth cutting surface and consistent cutting speed in all directions, ensuring the quality of cutting products.
Table 3 is the point distribution verification method.
Table 3 Coaxial debugging method
Nozzle |
Single nozzle over 2 mm | Normal laser point | Abnormal laser spot |
Tools |
Black laser paper |
![]()
|
![]()
|
Methods |
1. The black laser dot paper is about 300mm away from the cutting head nozzle to make a dot; | ||
2. If there are black dots there, the lens is dirty; | |||
3. If the laser spot is not round and the center is offset, the laser spot is poorly distributed |
(4) Nozzle heat range test.
One of the main problems with using 10,000 watt lasers to cut thick carbon steel sheets is nozzle overheating. To resolve this, it is important to test the nozzle temperature for various nozzle sizes and focal points at full power before beginning the cutting process.
Before carrying out the tests, it is necessary to align the coaxiality so that the light point is centered at the nozzle exit. In addition, a gas cutting cooling system must be installed in the nozzle.
Test method:
Iron buckets filled with an appropriate amount of water should be placed below the cutting head.
The auxiliary gas (gas type and air pressure should be adjusted based on specific cutting requirements) should be blown out first, and the laser should be operated at full power for 30 seconds to monitor any changes in nozzle temperature.
The nozzle size must then be changed and the testing process repeated.
The heat generation of the different nozzles must be recorded and used as a reference for subsequent configuration of the cutting process.
If the nozzle temperature does not remain within a narrow range, this may indicate a problem with the cutting head, nozzle, lens, or laser, and additional troubleshooting must be performed before proceeding to the next step in process setup. cutting.
Conclusion
The choice between using a positive or negative focal point for laser cutting does not depend on the metal material being cut (such as stainless steel or carbon steel), but rather on the cutting method used (such as oxidation cutting or fusion cutting).
Different parts processed by the laser cutting machine may require different focal patterns.
Considering the different effects of positive and negative focus on cutting stainless steel and carbon steel, and taking into account their individual processing needs, users can select the appropriate focus cutting method to fully utilize the performance benefits of the cutting machine laser.
When it comes to 15 kW lasers from different brands, they generally have similar cutting results and processing efficiency for carbon steel and stainless steel.