With the steady growth of heavy industry, laser cutting technology has advanced from cutting thin plates to cutting large and thick plates.
Laser cutting has now entered the high-power era.
This new era demands greater precision, speed and thickness when cutting industrially manufactured metal sheets. As a result, the power of laser cutting machines is continually increasing.
From an industrial perspective, high-power laser cutting machines are not only a natural progression in its development, but also align with the general trend of industrial development.
01 Preface
In the sheet metal processing industry, the advantages of laser cutting machines are highly significant. Its high precision, speed and quality have led to the gradual replacement of traditional processing methods and the establishment as the main equipment for cutting sheet metal.
Since the advent of laser cutting machines, the use of fiber laser cutting machines has surpassed that of YAG and CO2 machines, and the trend towards high-power laser cutting machines has emerged. These high-powered machines have become the norm for cutting thick sheet metal and increasing cutting efficiency.
Recently, high-power laser cutting machines have become a popular topic in the field of laser cutting, with many companies introducing fiber laser cutting equipment with power levels above 10,000 watts.
For the sheet metal processing industry, the introduction of high-power cutting machines has significantly improved the thickness and cutting efficiency of sheet metal. These machines are constantly pushing the limits of material cutting thickness.
This, combined with the reduction in the cost of processing thick plates, creates a positive cycle and drives the expansion of laser cutting applications.
02 Brief introduction of high power laser cutting machine
(1) Introduction of high power cutting machine
Laser cutting machines can be classified into three categories based on their power: low power, medium power and high power.
Low power laser cutting machines are suitable for cutting stainless steel and carbon steel with general thickness.
High-power laser cutting machines are ideal for cutting thick sheets and maximizing cutting efficiency.
As a result, laser cutting machines with a laser power of 10,000 watts or higher are commonly called high-power laser cutting machines. (See Figure 1)
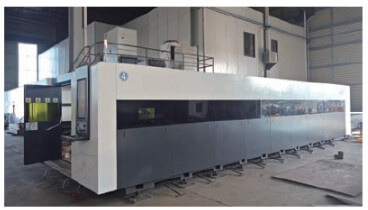
Fig. 1 High power laser cutting machine
(2) Fiber laser power specifications
According to the varying thickness of the metal plates undergoing laser cutting, the power specifications of the fiber laser used in the high-power cutting machine must also vary.
The current trend in the metal processing market shows that large, medium and small companies are gradually upgrading to various specifications, as indicated in Table 1.
Table 1 High Power Fiber Laser Specifications
Power/Kw | 10 | 12 | 15 | 20 | 25 | 30 | 35 |
Observation | Normal | Normal | Normal | Crude | Crude | Crude | Crude |
(3) Specification of the gas used
When the high-power laser cutting machine operates, it is crucial to maintain cutting accuracy, speed and quality. To achieve these benefits, the oxygen used must have a high degree of purity, generally 99.99%.
03 Features of high power laser cutting machine
3.1 Technological advancement
(1) High-speed cutting machine with enhanced dynamic performance
This machine tool, equipped with a 10,000-watt fiber laser, features a new triangular beam structure that offers the following benefits:
① Weight has been reduced by 30%, resulting in better dynamic performance.
② It can reach a maximum movement speed of 200m/min and has an acceleration of 4G.
③ The weight of the base has been increased by approximately 20% to change the way the machine tool is clamped and eliminate any impact that high acceleration may have on its performance.
(2) New software system
A machine tool's software and control system act as its brain and command center. Upgrading the hardware can bring additional benefits, but the main difference in machine performance is in the software and control system, which can vary greatly.
(3) It can perform stable cutting at a speed of 100M/min
① The response time of the capacitive sensor is three times faster than that of a traditional cutting head.
② The z-axis speed has been increased, resulting in smoother and more uninterrupted operation. This led to an increase of more than 30% in sheet cutting efficiency, improved feed function and improved acceleration adaptation function.
③ The functions of fast drilling, precise drilling and remote diagnosis have been improved, and an intelligent interface has been added to facilitate the implementation of “Industry 4.0” features.
3.2 Features of the cutting head
The high-power cutting head is the key component to ensure stability during continuous high-power operation. It has:
① Improved sealing and improved cooling system, as well as wider focusing range and high temperature resistant lenses.
② To overcome the problem of focus drift caused by high-power thermal lens effect during long-term use, the high-power cutting head adopted a new gas path design structure and replaced the nozzle with a new design, improving cutting speed and stability.
3.3 High power laser cutting capability
(1) The cutting thickness of thick plates is increasing
The high-power cutting head is the key component to ensure stability during continuous high-power operation. It has:
① Improved sealing and improved cooling system, as well as wider focusing range and high temperature resistant lenses.
② To overcome the problem of focus drift caused by high-power thermal lens effect during long-term use, the high-power cutting head adopted a new gas path design structure and replaced the nozzle with a new design, improving cutting speed and stability.
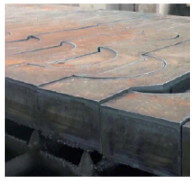
Fig. 2 Part for cutting thick sheet metal
(2) Multiplication of thin sheet cutting efficiency
① When cutting stainless steel plates with a thickness of 3 to 10 mm, the cutting speed of a 10,000 W laser cutting machine is more than twice that of a 6,000 W machine.
② In the application of carbon steel cutting, a 10,000W laser cutting machine can achieve fast and bright surface cutting at a speed of 18 to 20mm/s, which is twice the common standard cutting speed.
③ Carbon steel plates up to 12 mm thick can be cut with compressed air or nitrogen, resulting in cutting efficiency 6 to 7 times higher than that with oxygen.
3.4 Bed characteristics
(1) The equipment is equipped with a super resistant mechanical structure
The high power cutting machines have a cast iron base cast as a single piece using flaked graphite cast iron, with a minimum tensile strength of 200MPa. This results in significant improvements in carbon content, compressive strength, vibration damping and wear resistance (as shown in Figure 3).
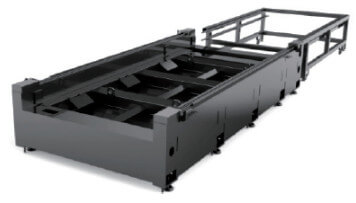
Fig. 3 Machine base
(2) Features of cast iron bed
① The base has excellent lubrication performance, is highly resistant to corrosion and has remarkable dimensional stability, minimizing machining errors caused by base vibrations.
② This results in reducing equipment loss during use and improving the stability coefficient by more than 30%. Quality accuracy has also increased by more than 30% and the service life of the bed has been extended by more than 70 years.
3.5 Automatic nozzle replacement
(1) Manual nozzle change mode
When cutting, the nozzle must be changed according to the thickness and type of material to be cut.
In the past, nozzle replacement was performed manually, which was not only time-consuming and required repeated efforts from technicians, but also a challenge to ensure accuracy and stability after replacement.
Finding an efficient and quick method to replace the nozzle while ensuring that each replacement is safe and accurate is a technical challenge in the laser cutting field.
(2) Automatic nozzle replacement technology
The high-power laser cutting machine has automatic nozzle replacement.
It has several functions, such as automatic nozzle replacement, laser head calibration and nozzle cleaning, reducing the need for manual work.
To replace the nozzle, simply operate the appropriate command on the touch screen.
The benefits of this automatic nozzle replacement technology include:
- Reduced labor intensity and greater positioning accuracy and stability during nozzle replacement.
- An advanced control system that can automatically adjust nozzle model and specifications based on plate material and thickness, streamlining the manual replacement process and increasing production efficiency.
- The fully enclosed protective design of the automatic nozzle replacement system provides a safe environment for both nozzle equipment and operators.
3.6 Radius drilling and limit hole formation
(1) Lightning drilling
It has the benefits of short drilling time, low thermal focusing energy, a stable starting point and the preservation of stability in the servo system, resulting in great cutting performance.
The advantages of flash drilling are shown in Table 2.
Item | Index | Observation |
Drilling time | Reduced by around 90% | Improve processing efficiency |
Residual porosity rate | From around 10% to around 0.3% | Improve workpiece integrity |
Save gas and electricity | Laser and cutting head damage is reduced | Improve the use of materials |
(2) Limit hole
The laser cutting industry has long held that plate thickness determines the minimum cutting hole diameter.
However, with the use of high-power laser cutting machines, it is possible to obtain an even smaller hole diameter, with a ratio as low as 0.15 times the sheet thickness, as shown in Figure 4.
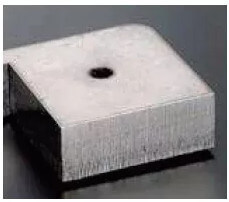
Fig. 4 Minimum hole cutting sample
04 Advantages of high power laser cutting machine
(1) High speed
The laser cutting speed exceeded 20 m/min. The two-axis movement speed of the cutting and processing machine can reach a maximum of 250 m/min, and its acceleration during operation is approximately 10 g.
(2) High precision
A 1 mm thick board can be cut into approximately 500 pieces per minute for a small hole of about 10 mm in diameter. The cutting process results in minimal error between holes.
(3) Develop towards the thick plate
The power of high-power laser cutting machine is gradually increasing, and the size of thick plate is also increasing.
(4) Evolving to a large size
The processing size range of laser cutting technology is also increasing, and laser cutting technology has begun to develop towards large sizes.
(5) Unmanned automatic
It is crucial and pressing to advance automatic and unmanned laser cutting technology.
① The integration of computer network technology has transformed laser cutting into a fully automatic and unmanned process.
② Growing market demand for this technology is driving the need for full automation in laser cutting.
(6) Intellectualization
Keep up with the pace of smart manufacturing according to the technical demands of Industry 4.0. This approach uses accurate graph recognition technology and a user-friendly interface for seamless human-computer interaction.
The combination of laser and computer control, numerical control technology, optical system, high-precision automatic positioning devices and integrated functions such as automatic unloading, cutting process database, remote fault diagnosis and remote control enable efficient processing of mass and complex parts.
Final words
(1) Development of high-power equipment
Laser cutting is considered an ideal method in cutting processing and represents the advancement of modern metal processing technology. At present, high-power laser cutting machines are undergoing important research and development in areas such as high-speed, high-precision, large-format three-dimensional cutting and special materials cutting to drive the technical advancement of high-power laser cutting and meet growing market demands.
(2) Selection of high-power equipment
When selecting high-power laser cutting equipment, companies need to consider several factors carefully: in addition to cutting speed and accuracy, the stability and consistency of continuous cutting at full power, the machine tool's ability to match the speed, the Advanced machine tool quality, and precision service life should also be evaluated.
It's not enough to just compare prices when purchasing high-power laser cutting equipment. This type of equipment requires a high investment, which brings with it a higher level of risk.
Therefore, when entering the high-return laser cutting market, companies must recognize and understand the risks involved.