Several factors can cause a plasma cutting machine to not generate an arc.
Firstly, voltage instability is a common problem since plasma power sources typically need to be connected to a three-phase voltage of 380V. Missing phase or inadequate voltage capability may result in the inability to start an arc. Secondly, air intake problems are another significant factor.
Lack of intake or insufficient air pressure may affect the normal arc starting of the plasma cutting machine.
Solutions to these problems include checking the power supply, replacing the contactor, repairing internal wiring, and closely monitoring the air compressor outlet pressure display to ensure sufficient pressure.
If you encounter problems with inadequate air pressure, it may be due to insufficient air intake from the air compressor, too low pressure regulation by the air regulating valve, blockages in the solenoid valve, or an unsmooth air path.
Therefore, addressing the issue of a plasma cutting machine not generating an arc requires considering all of these possibilities and taking appropriate measures.
Arcless Plasma Cutter Troubleshooting
The stability of the arc in an NC plasma cutting machine is crucial to the quality of the cuts produced.
If the plasma arc is unstable, it can cause problems such as uneven cuts, edge build-up, decreased performance of control system components and the need for frequent replacement of nozzles and electrodes.
Based on the analysis of this phenomenon, the proposed solutions are as follows:
1. Air pressure too high
If the inlet air pressure exceeds 0.45Mpa, it may have a negative impact on the plasma cutting process.
Excessive airflow will cause the plasma arc to disperse, weakening the concentration and intensity of the arc column and reducing its cutting power.
Causes of high air pressure include:
- Inadequate incoming air conditioning
- Air filter pressure relief valve set too high
- Air filter relief valve failed
The solution to the problem is:
- Check that the air compressor pressure is set correctly.
- Check whether the pressure between the air compressor and the air filter pressure relief valve is adequate and orderly.
- If, after starting, the air filter pressure reducing valve does not respond to adjustments made by turning the key and there is no change in the pressure reading on the pressure gauge, this indicates that the air filter pressure reducing valve is not working properly and needs to be replaced.
2. Air pressure too low
When using a plasma cutting machine, if the working pressure is significantly lower than the required pressure specified in the specifications, it may negatively impact the quality of the cut.
A low working pressure means a weakened plasma arc ejection speed and a reduced inlet airflow, which will prevent the formation of a high-energy, high-speed plasma arc.
This can result in poor quality cutting, incomplete cuts, and unwanted material buildup on the cutting edge.
Causes of low air pressure include:
- The compressor is short of air
- Plasma cutting machine air conditioning valve pressure setting is too low
- There is oil pollution in the electromagnetic valve
- The air channel is obstructed
The solution to the problem is:
Before operating the plasma cutting machine, it is crucial to inspect the air compressor outlet pressure display and make necessary adjustments.
If the air pressure input meets the required standards, it is equally important to confirm that the air filter pressure relief valve is adjusted correctly and that the pressure display meets plasma cutting requirements.
Proper maintenance of the air filter pressure relief valve must be performed regularly to ensure that the incoming air is clean and oil-free.
Contaminated air can cause oil to build up in the solenoid valve, making it difficult to open the valve core and leading to insufficient opening of the valve port.
When the torch nozzle pressure is too low, it may be necessary to replace the electromagnetic valve.
A reduction in the cross-section of the gas channel can also lead to low air pressure. In these cases, the air tube can be replaced following the instructions provided.
3. Poor contact between the ground wire and the workpiece
Proper grounding is an essential step before using a plasma cutting machine.
If the appropriate grounding tool is not used or if the surface of the workpiece is not properly grounded, the connection between the ground wire and the workpiece will be weak.
It is advisable to use specialized grounding tools to detect any insulation that may negatively impact the connection between the ground wire and the surface of the workpiece.
The use of worn or old ground wires should be avoided.
4. Torch nozzles and electrodes burn out
The causes of premature beak damage:
- Improper nozzle installation, such as loosely tightened thread attachment
- Incorrect adjustment of all gears
- Cooling water does not flow as required when the cutting torch that needs to be cooled with water is operating
- Frequent bow
The solution to the problem is:
- Adjust the gear position correctly according to the technical cutting requirements of the workpiece
- Check whether the cutting torch nozzle is installed securely
- Circulate the cooling water in advance if the nozzle needs to pass through the cooling water
- When cutting, the distance between the cutting torch and the workpiece should be adjusted according to the thickness of the workpiece
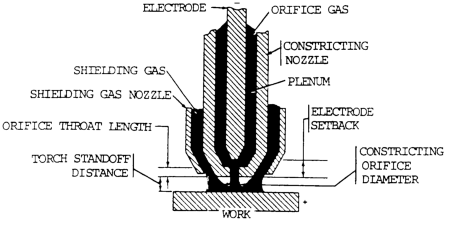
5. The spark generator cannot automatically break the arc
When the plasma cutting machine is in use, the first step is to ignite the plasma arc.
The high-frequency oscillator drives the gas between the electrode and the inner wall of the nozzle to form a high-frequency discharge that partially ionizes the gas and creates a small arc.
This small arc is then expelled from the nozzle by compressed air, igniting the plasma arc.
This is the main function of the spark generator.
Typically, the spark generator only operates for 0.5 to 1 second.
If the arc cannot be broken automatically, it is generally because the control circuit board components are unbalanced or the gap between the spark generator discharge electrode is not optimally adjusted.
The solution to the problem is:
- The spark generator discharge electrode must be checked frequently to maintain its smooth surface
- Timely adjust the spark generator discharge electrode gap (0.8 ~ 1.2mm)
- Replace the control panel if necessary
6. AC input voltage is too low
There are significant electrical installations located at the location where the plasma cutting machine is used.
Malfunction of critical circuit components in the plasma cutting machine can result in insufficient AC input voltage.
To resolve this issue, the following steps must be taken:
It is important to check that the electrical network connected to the plasma cutting machine has adequate load capacity and meets the necessary power line specifications.
The plasma cutting machine should be located in a place away from large electrical equipment and areas with electrical interference.
It is recommended to regularly clean dust and debris from plasma cutter components and check for frayed wires during use.
7. Others
In addition to the causes mentioned above, plasma arc stability can also be affected by factors such as very slow cutting speed, angle of the cutting torch in relation to the workpiece and the operator's level of experience in using the plasma cutter. It is essential that users keep these factors in mind.
How can we accurately evaluate the voltage stability of a plasma cutting machine?
First of all, it is essential to check whether the plasma cutting machine's power supply is working normally, ensuring that the voltage is stable.
Additionally, the plasma cutting machine's grounding should be inspected to confirm that it is well grounded. This is because proper grounding can improve the stability of arc initiation.
On site, if there are large power-consuming installations or internal faults in the cutting machine's main circuit components, this may result in excessively low AC input voltage. Therefore, it is necessary to monitor these situations.
Lastly, further assurance of voltage stability can be obtained by checking the proper functioning of the voltage detector or motor regulator. Through these steps, we can more accurately detect and guarantee the voltage stability of the plasma cutting machine.
What are common problems and solutions for a plasma cutting machine's air intake system?
Common problems with a plasma cutting machine's air intake system mainly include solenoid valve malfunction, improper air pressure adjustments, insufficient air pressure, interrupted or inadequate gas supply, and inlet blockage or moisture. The solutions to these problems are as follows:
Solenoid valve problems: If the plasma cutter is not emitting air, the intake solenoid valve should be checked for damage. If the valve is defective, it will need to be replaced.
Improper air pressure adjustment: Check the air pressure adjustment filter on the back panel of the air plasma cutter, ensuring that the air pressure is neither too high nor too low. Generally, the air pressure should be maintained at about 0.35 MPa to ensure the normal formation and arcing of the plasma.
Insufficient air pressure: Causes for insufficient air pressure may include inadequate air intake from the air compressor, excessively low pressure setting of the cutting machine air control valve, oil contamination inside the solenoid valve or air passage obstructed. The solution is to monitor the air compressor outlet pressure before use, adjust the air control valve pressure setting as needed, clean oil contamination inside the solenoid valve, and ensure an unobstructed air path.
Interrupted or insufficient gas supply: Check and reconnect the gas pipeline, increase gas pressure to ensure continuity and adequacy of gas supply.
Intake or Moisture Blockage: If the inlet is blocked or slightly damp, it needs to be cleaned or replaced to ensure smooth gas entry into the cutting machine.
How to determine whether a plasma cutter's inlet air pressure is appropriate?
To determine whether a plasma cutter's inlet air pressure is appropriate, you first need to understand the range of air pressure required for normal operation of a plasma cutter. According to various sources, the air pressure of an air plasma cutter is generally adjusted between 0.4~0.6 MPa, but it is also suggested to adjust the back pressure to 0.2-0.3 MPa according to the real situation.
This indicates that specific air pressure requirements may vary depending on the type, thickness of the cutting material and cutting speed.
In practical operations, if you encounter situations where the arc does not cut or the cutting effect is weak, it may be due to inadequate inlet air pressure.
For example, if the incoming air pressure is significantly lower than the normal range, the arc may not start. Therefore, checking the air compressor's outlet pressure display to ensure it meets requirements is an important step in determining whether the air pressure is appropriate.
Also, pay attention to whether the air filter pressure reducer adjustment is correct and whether there is any fault that could cause the air pressure to be too high or too low.
The adequacy of a plasma cutter's inlet air pressure can be determined through the following steps:
- Please confirm the recommended air pressure range of the plasma cutter, generally 0.4 ~ 0.6 MPa, but adjust accordingly according to the specific situation.
- Observe the air compressor outlet pressure display to ensure the air pressure meets the recommended range.
- Check that the air filter pressure reducer adjustment is appropriate to avoid excessively high or low air pressure due to improper adjustment.
- Consider factors such as type, thickness and cutting speed of the cutting material, and adjust the air pressure accordingly according to the actual situation.
By following these steps, you can accurately determine whether a plasma cutter's inlet air pressure is appropriate, thus ensuring the smooth running of the cutting process.
Common Causes of Plasma Cutter Torch and Electrode Damage
What are the common causes of plasma cutter torch and electrode damage and what is the guide for their replacement?
These factors can seriously affect the operation of the plasma system, causing damage to the torch and electrode.
Regarding the replacement guide, the first step is to turn off the plasma cutter and disconnect the power supply to ensure that the equipment is in a safe state.
Then, based on the instructions in the equipment manual, determine the type and location of consumable parts that need to be replaced and use appropriate tools, such as wrenches and screwdrivers, for careful disassembly.
Consumables such as electrodes and nozzles that are prone to wear must be replaced regularly for efficient cutting. During the replacement process, you may consider replacing the entire machine torch and cable assembly or replacing individual components. Additionally, using a clean cloth to wipe the inside of the nozzle can eliminate oxides, which is an important measure to prevent damage to the torch.
1 comment
Posso adaptar uma tocha arco piloto em uma maquina que não veio com arco piloto?