1. Main causes of dimensional error of parts caused by flame cutting
The main causes of errors in NC cutting and blanking include thermal deformation of the steel sheet, operator technique, flatness of the supporting platform, equipment accuracy, and the degree of corrosion on the surface of the steel sheet.
2. Analysis of dimensional errors of parts produced by flame cutting and targeted measurements
Flame cutting of steel sheets always involves hot deformation. However, dimensional errors in hot deformation parts can be significantly reduced. Cutting speed and part quality are affected by operator skills.
The leveling of the support platform and the accuracy of the equipment have the greatest impact on the size of the parts. Inaccuracies can often result in parts being discarded directly. Furthermore, surface corrosion of the steel plate can affect both cutting quality and cutting speed.
2.1 Dimensional error of parts caused by thermal deformation of steel plate
Thermal deformation in steel sheets is noticeable mainly in thin parts. Based on years of cutting practice and analysis, it has been determined that dimensional errors in parts caused by thermal deformation can be minimized by focusing on the following three aspects:
2.1.1 Drawing part charts
When creating graphics for parts, be sure to include an appropriate amount of thermal expansion compensation in the length direction of the part. The compensation amount should be selected based on the specific characteristics of each individual party.
Advantages : directly compensates for the dimensional error of parts caused by thermal expansion;
Disadvantages : It is only applicable to square pieces and other shapes are not easy to compensate.
2.1.2 D detailed discharge process
Starting from the discharge aspect, refine the discharge process and formulate a special discharge process for volatile parts.
2.1.2 you get from common edge
The use of a common edge can reduce cutting time, minimize heat input through the steel plate, reduce the expansion of the steel plate and consequently reduce the dimensional errors of the parts.
As illustrated in Figure 1, when a common edge is not created, AB and CD on two adjacent sides of two parts need to be cut separately.
On the other hand, after using a common edge, only the AB edge needs to be cut and the CD edge does not require cutting.
This not only reduces part errors, but also increases cutting efficiency and sheet metal utilization.
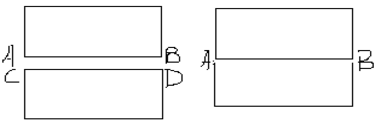
2.1.2 R reasonable cutting direction
Determine the reasonable cutting direction of the part according to the actual situation, first cut the hole, then cut the shape, and first cut the edge close to the edge of the steel plate.
Try to ensure that there should be sufficient connection rigidity between the workpiece and the steel plate before the workpiece is cut close to the completion point, so as to ensure the cutting size and accuracy of the workpiece.
For example, in Fig. 2, first cut the inner hole (1-6) and then cut the outer contour in the order A, B, C, D and A.
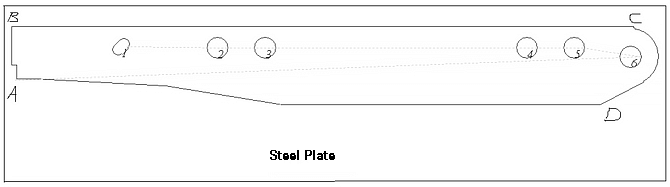
2.1.3 Easy part layout and cutting path
The error caused by the deformation of the steel plate can be minimized through proper layout of the parts and adjustment of the cutting path.
As illustrated in Figure 3, T-shaped parts that are susceptible to warping should be combined with smaller parts that are less likely to warp. This helps reduce excessive heating in localized areas, minimizes thermal deformation and ensures accurate part dimensions.
To minimize deformation in thin parts, offset cutting should be used when unloading them.
As shown in Figure 4, after cutting part 2, the second column should be used to cut part 3. After part 2 cools for a certain time, it should be turned over to cut part 4.
Efforts must be made to avoid excessive localized heating of the steel sheet, minimize thermal deformation and ensure the accuracy of the part's dimensions as much as possible.
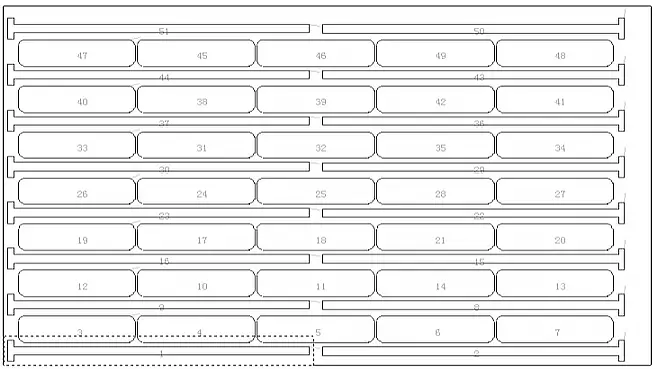

2.1.2S setting interval
To reduce the error caused by the deformation of the steel plate (as shown in Fig. 5), it is recommended to set intervals. Please note that sections A, B, C and D should not be cut temporarily, but rather during platform cleaning.
Advantages : directly and effectively reduces the deformation of the part;
Disadvantages : Interval setting increases the number of cutting perforations, increases cutting time and increases cutting nozzle consumption.
Cutting the gap (as shown in Fig. 6) may result in scars left by platform cleaning personnel.
Subsequent repairs, welding and grinding will be required.
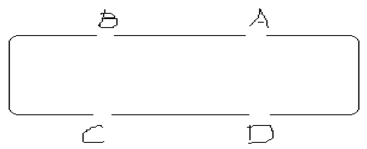
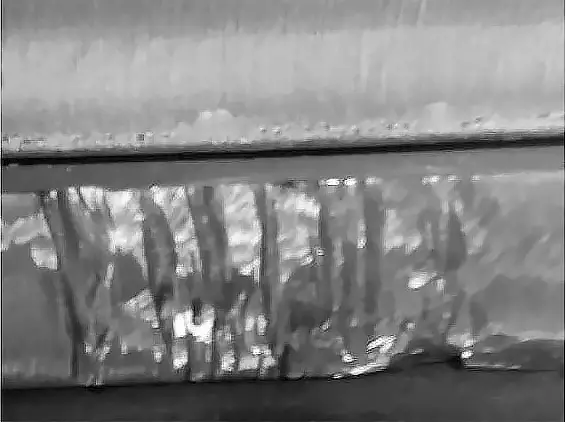
According to different situations, the choice and use of suitable methods or a combination of several methods to control the deformation of the steel plate can play an obvious role.
2.2. Dimensional error of parts caused by NC operator technology
In theory, when using the same equipment and NC program, the parts to be cut should be identical. However, in reality, this is not always the case.
Even with the correct procedure, parts cut by different operators may present variations in size and errors, and some may even need to be scrapped.
To ensure that parts are cut correctly, the appropriate cutting nozzle must be chosen based on the thickness of the steel plate. The flame must be adjusted properly and the corresponding gap compensation must be set to ensure that the parts are of high quality.
For reference, see the table below which provides gas cutting process parameters.
Cutting process parameters |
|||||||
Cutting nozzle number |
Cut oxygen hole diameter/mm |
Cutting thickness /mm |
Cutting speed mm/min |
Preheating time/s |
Oxygen Pressure Mpa |
Gas pressure Mpa |
Crack compensation value /mm |
1 |
1.0 |
5-10 |
700-500 |
5-12 |
0.6-0.7 |
>0.03 |
two |
two |
1.2 |
10-20 |
600-380 |
15-25 |
0.6-0.7 |
>0.03 |
2.5 |
3 |
1.4 |
20-40 |
500-350 |
25-30 |
0.6~0.7 |
>0.03 |
3 |
4 |
1.6 |
40~60 |
420-300 |
35-50 |
0.6-0.7 |
>0.03 |
3.5 |
5 |
1.8 |
60-100 |
320-200 |
50-80 |
0.6-0.7 |
>0.03 |
3.5 |
6 |
2.0 |
100-150 |
260~140 |
80-120 |
0.7-0.8 |
>0.04 |
3.5 |
Note: Oxygen purity is above 99.5%.
2.3. Dimensional error of parts caused by support platform
The main reason for dimensional errors in parts caused by the support platform is due to the plane of the support platform not being parallel to the guide rail surface of the NC cutting machine.
The supporting steel plate working platform is often impacted and knocked on the loading and unloading platform, causing its plane to become uneven and not parallel to the guide rail surface of the NC cutting machine.
If the unevenness is significant, it may cause the cutting torch of the cutting machine to be non-perpendicular to the steel plate, resulting in the thickness direction of the entire part being tilted.
Due to long-term flame cutting, the insertion plate of the support platform may suffer from cutting damage and slag adhesion, leading to local unevenness of the support platform.
During the part cutting process, the part may be partially suspended, resulting in partial tilting of the part thickness direction.
When the thickness of the steel plate is relatively large, the size of the part will have a significant error.
2.4. Dimensional error of parts caused by equipment accuracy
The accuracy of the equipment's guide rail has a direct impact on the accuracy of the cut parts. To minimize errors caused by the accuracy of the guide rail, it is essential to maintain and regularly check the parallelism and flatness of the guide rail.
Protecting equipment parameters is crucial. Any changes made to the vertical and horizontal parameters of the equipment may result in the scrapping of a significant number of parts.
Operators must perform a thorough self-inspection of parts, especially large ones, and immediately report any problems found. This approach will effectively help in identifying such issues.
3. Conclusion
Various methods can be combined to effectively reduce errors and improve product quality based on the causes of errors in different parts.