Every compressed air installation, regardless of whether it is installed by ourselves or outsourced to an external company, is subject to a leak test. This usually results from the provisions of the contract between the client and the contractor. Without these tests, there is no hope that the installation will be accepted. Therefore, it is important to carry out a leak test of the compressed air installation.
It is not for nothing that it is said that compressed air is the most expensive means. Any defect or leak, no matter how small, leads to losses caused by reduced machine efficiency and tool performance and, ultimately, increases the cost of electrical energy consumption. Since air is a common commodity, it may seem like leaks are not a bad thing, but nothing could be further from the truth.
Read: All about pneumatic pressure
In everyday life this is debatable, but in everyday life the cost of loss can be huge and it is best to avoid it.
Leak testing a compressed air system – what to check?
Installation should be checked for leaks upon completion, preferably with receivers installed. After installing the flawlessly calibrated pressure gauge rigidly, bypassing the quick connector and filling it with compressed air, we close it by closing all taps and ball valves for a certain time. On average, the measurement is carried out after a certain period of time of at least about 24 hours. During this time you can fully assess the tightness of the installation.
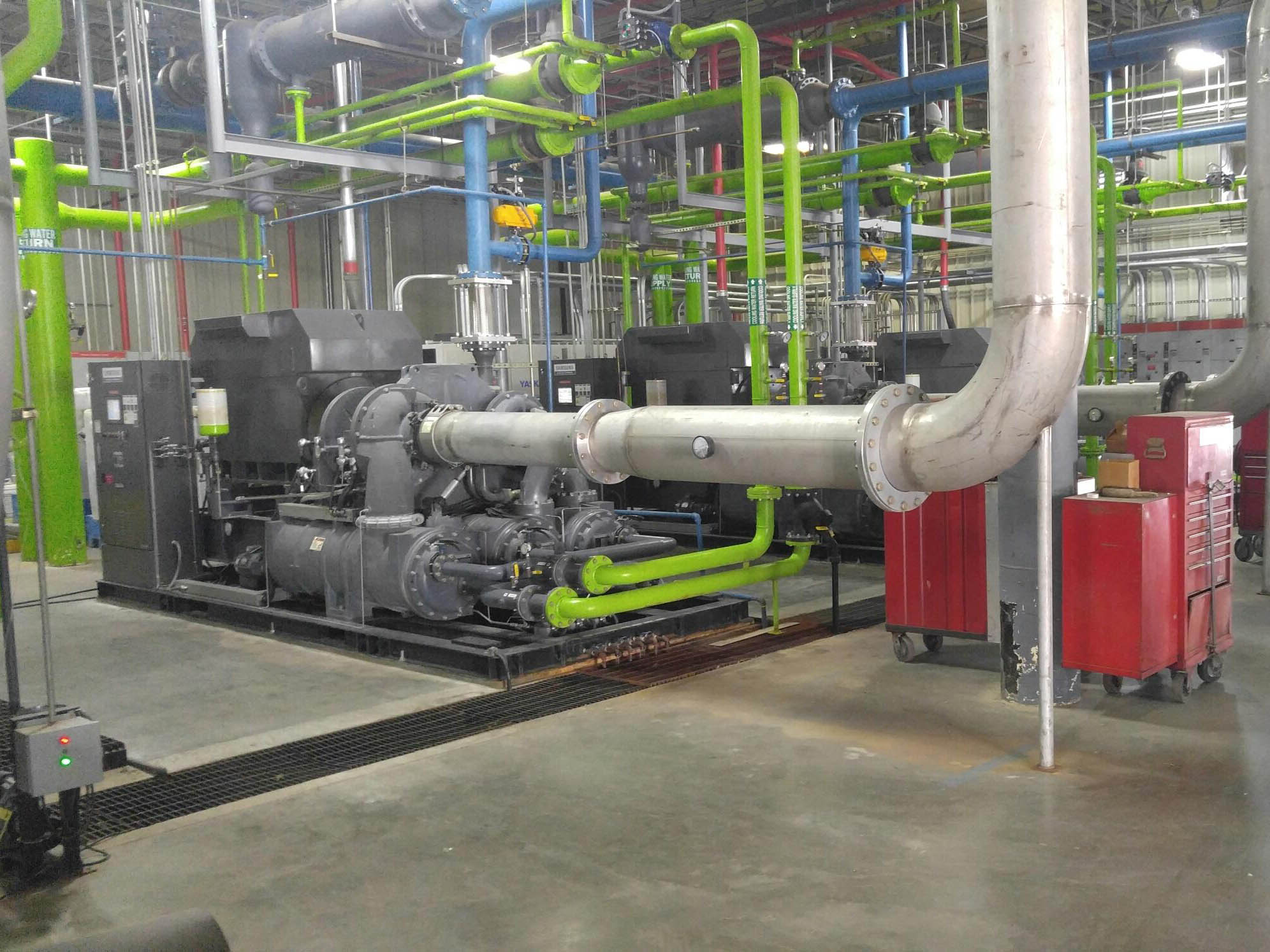
Leak testing a compressed air system is necessary to ensure accurate leak measurements.
If the leak falls below the values predicted in the diagnosis, it must be repaired and the system refilled. In this case, the leak test is repeated and the measurement time is generally shorter. If not, we will write a report.
We can check for leaks in different ways:
- listen while machines and equipment are in operation. This is unpleasant due to acoustic noise in the workplace.
- Use leak testers, both those in spray cans and homemade ones made with dish soap and water. And although the tester is a foam that does not drip or have a destructive effect on the connector or device, using a water-based agent on elements that come into contact with electricity is risky and can result in electric shock.
The advantage of using aerosol testers is that the testers can be used in both positive and negative temperatures. The difference is that those with advanced warning are recommended for use in cold weather.
You may be interested in: Which tubes to choose for pneumatic installations?
Leaks of less than 1 mm produce so-called frequencies that are inaudible to the human ear. In this case, you can organize a leak measurement with detectors in a directional manner, even at a great distance. Of course, due to the high acquisition costs, such a device is usually equipped by specialized companies.
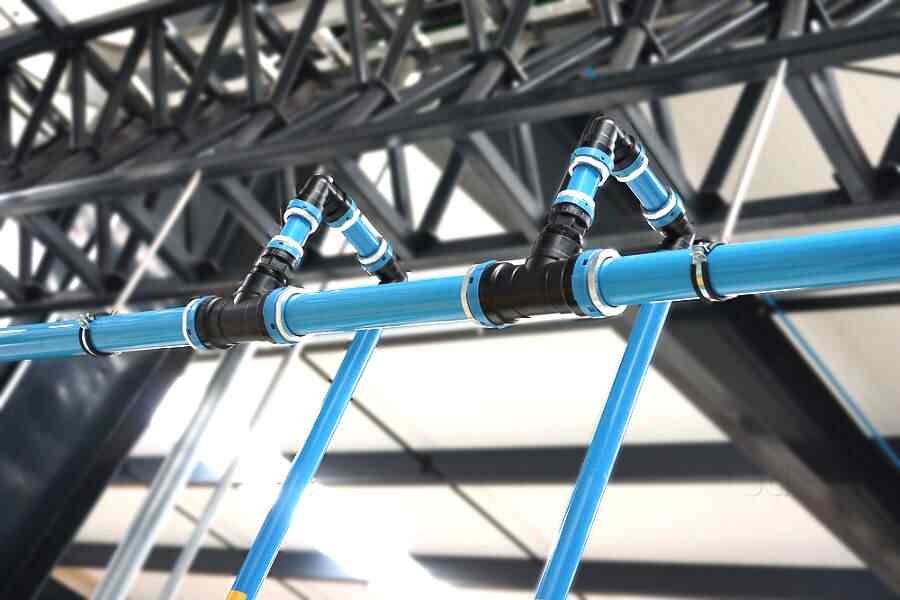
However, if we are struggling with loss of media, loss of equipment efficiency and increased number of compressor starts, and in large halls these engines are powerful, the power losses will be very clearly visible on a monthly or monthly basis. annual, which means that in the final solution to the leak will be incorporated.
Standards and requirements for leak testing of compressed air systems
The standards and requirements for leak testing of compressed air systems are of great importance, as they guarantee the safety and proper functioning of the entire system. To ensure proper execution and reliable results, compressed air system leak testing must be performed in accordance with applicable regulations and standards.
One of the most important regulations for leak testing of compressed air systems is the Minister for Economic Affairs' regulation on occupational health and safety in devices using compressed air. This provision obliges employers to carry out leak tests on compressed air systems at least once a year and after each repair or renovation.
It should be noted that leak testing of compressed air systems must be carried out by a specialized company with appropriate qualifications and certificates confirming knowledge of the regulations and standards for leak testing of compressed air systems. Only this company is capable of carrying out a compressed air system leak test thoroughly and guaranteeing the reliability of the results.
Furthermore, it is important that the documentation for leak testing the compressed air system is properly stored and available to responsible bodies, such as labor inspection or the state fire department. This documentation must contain information about the compressed air system leak test, measurement results and possible system errors and repairs.
In summary, compliance with standards and requirements for leak testing of compressed air systems is crucial to guarantee the safety and proper functioning of the entire system. Leak testing of the compressed air system must be carried out in accordance with applicable regulations and standards and documentation must be properly stored and made available to the relevant departments.
Advantages and benefits of compressed air system leak testing
Carrying out a leak test on a compressed air system brings many advantages for the proper functioning of the entire system and for the safety of employees.
Firstly, a leak test on the compressed air system allows you to identify possible leaks in the installation, which is essential to ensure the correct pressure and volume of air in the system. Leaks can lead to loss of pressure and increased energy consumption, negatively impacting efficiency and operating costs.
Secondly, by carrying out a leak test on the compressed air system, it is possible to detect possible failures or damage to the system, which is crucial for the safety of employees and those nearby.
Thirdly, a leak test of the compressed air system allows you to detect possible irregularities in the operation of the equipment, which can lead to premature wear or failure. This, in turn, allows for quick and effective repairs, which is critical to ensuring business continuity and minimizing downtime.
Fourth, performing a leak test of compressed air systems allows compliance with applicable regulations and standards, which is crucial to avoid potential fines and sanctions.
In summary, carrying out a leak test on the compressed air system is essential for the proper functioning of the entire system and the safety of employees. A compressed air system leak test allows detection of possible leaks and failures, enabling quick and effective repairs and compliance with applicable regulations and standards.
What is a leak report on a pneumatic system?
The leak report is one of the documents we receive after the compressed air installation is completed. After checking for leaks and completing all assembly work, the system must be blown out with compressed air.
This protects us from blockages and failures, especially of reducing valves, control valves and, ultimately, also of common tools that are sensitive to this “dirt”.
After completing all of the above activities within the scope of the calling . Final commitment We can complete documents through:
- Quality of materials used
- Check connections, including soldered connections if present (solder plates).
- Fill in the system and evaluate whether the assumed parameters are achieved.
- Final acceptance report.
The cost of producing an element or service based on compressed air is not only the cost of the employee's work on the material itself, the depreciation of the machine and device, but above all the cost of electrical energy. Leak detection is a guarantee that the system remains in perfect condition, is efficient and reduces production costs.
How can compressed air costs be reduced? To read!
Therefore, keep in mind that a leaky installation will sooner or later lead to higher costs, defects and overall higher operating costs. We should therefore commission regular leak tests from designated bodies or people.