Being one of the most important sources of energy in industry, workshops, medicine and many other applications, compressed air is almost indispensable.
Analysis of air consumption generally shows that only half is used to carry out processes and operate pneumatic devices.
Unfortunately, the rest is wasted because:
- Leaks (approx. 20-30%)
- improper use (approx. 10 -15%)
- artificial demand (approx. 5-10%).
It is important to know your air consumption Strategic implementation your drawdown. The production of compressed air (converted into work performed) is on average five times more expensive than the cost of electricity.
You may be interested in the article “All about pneumatic pressure”.
Electricity represents the largest percentage of total compressed air production costs, between 65 and 85%.
The other cost components are:
- operational cost such as inspections, services, monitoring costs, possible repairs or electricity costs
- Investment costs such as depreciation of compressed air systems, network modernization costs, pneumatic connection installation costs, etc.
We start by optimizing compressed air costs by selecting the most effective source production, i.e. compressors, correct design Transfer system, i.e. piping and air treatment elements (filter, separator or treatment station).
More about pneumatic systems: Information about pneumatic systems
However, remember that the efficiency of the entire application (system) depends on this weakest link . That is why it is very important correct design and constant supervision of the entire pneumatic system, including monitoring parameters and the amount of air used.
The entire cost reduction process must be considered complete because only this action guarantees that we will be able to achieve the desired objective.
Rules to reduce compressed air costs
By following these rules, you have the opportunity to reduce the operating costs of your pneumatic system in the long term.
1. An effective source of compressed air, i.e. an efficient compressor.
One of the most important decisions that has a direct impact on the performance of the entire pneumatic system is the selection of the compressor (e.g. which compressor for the workshop?), with the right size (i.e. capacity) to meet your needs.
The size must be optimal A compressor that is too large is not recommended, as it entails unnecessary costs and we do not take advantage of its full performance. Furthermore, the costs of purchasing a larger compressor are obviously higher.
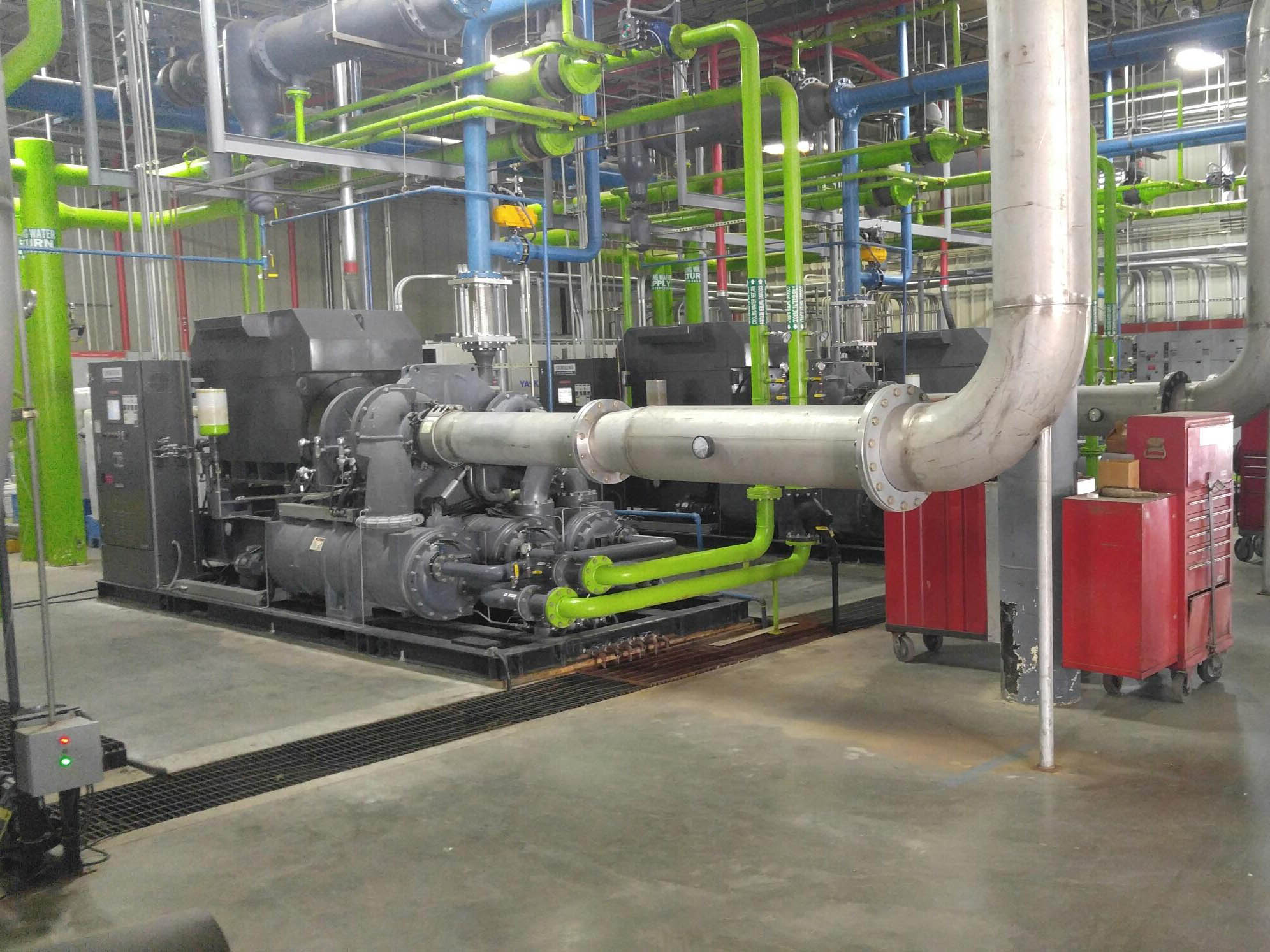
You should also think about which type of compressor will be most effective for your needs. The most effective types of compressors include variable speed screw compressors.
The best example is Atlas Copco's GA VSD Series compressors.
2. Reduction of losses in the pneumatic system.
Compressed air as a medium is a very expensive source of energy, so it is always worth paying attention to whether each pneumatic device is correctly selected for the work to be carried out.
The point is (as with compressor overestimation) that, for example, a certain tool should not be too large (which leads to greater air consumption), but should be selected optimally for the type of activity performed .
Big losses, therefore costs, as I already wrote Create air leaks. For older transmission systems, air leakage can be as high as 30% (depending on materials and installation method).
Most of us don't realize that up to 75% of leaks cannot be heard – they can be detected using special equipment such as ultrasonic detectors or leak testers (aerosol in foam form).
That's why it's so important to eat them remove or at least limit them .
3. Reducing the pressure in the compressed air system.
It often happens that the entire system operates at a higher pressure, only to provide just one receiving point with the highest pressure, while the rest operate at a much lower pressure.
This leads to direct costs, especially if the air requirements of individual collection points are different. To avoid this, it is worth considering purchasing a separate compressor or investing in a pressure boosting system.
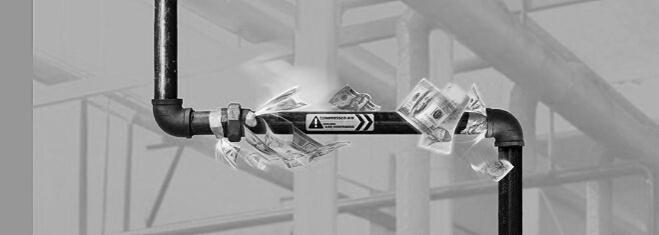
This allows the rest of the system to operate with lower pressure air, significantly reducing energy consumption and costs and contributing to the longevity of the entire pneumatic application.
It should be noted that the pressure in the network only increases several times 0.14 bar causes costs to increase by 1%.
4. System performance monitoring.
It would be worth considering the introduction of the Compressor Performance Monitoring System and the compressed air requirements of our application.
This will make it possible to quickly react and make the right decisions. It also helps to ensure that the entire pneumatic system functions optimally and that losses are at a low and acceptable level.
How to check the tightness of the pneumatic installation? To read!
Proper monitoring is only possible if our decisions are based on information from appropriate measuring devices.
Only then will all process parameters be accurate and reliable.
5. Possible correction of the pneumatic system.
Correct selection of diameters and cable routing (e.g. laying the cable in a so-called loop) as well as additional compressed air containers in locations away from the compressor housing significantly reduce pressure losses and improve the efficiency of the entire system, resulting in the proper functioning of the compressor and reducing costs.
6. Thermal energy recovery
A compressor is used to generate compressed air and generates a lot of heat , which can be used to recover thermal energy. An example of this is a screw compressor with a heat exchanger, which allows heat to be transferred from the compressor to the heating system or to heat domestic hot water.
7. Replace the filter cartridges
Regular and systematic replacement of filter cartridges in air treatment systems such as: Filters, separators and stations This allows you to avoid a drop in pressure and, consequently, an increase in costs.
You can learn more about daily maintenance of pneumatic systems here
Remember that dirty filters can cause a loss of pressure in the installation even 0.3-0.5bar which will certainly lead to greater energy consumption.
It is worth investing in filters with differential clogging indicators.
An important but often overlooked topic is the principle The level of filtration was appropriate for a specific receiver, as the more filters, the greater the pressure drop and the greater the cost.
In other words, it has higher air quality (Purity), including a higher acquisition cost .
That's why it doesn't make sense to purify the air more than necessary for devices that don't need it.