1. Introduction
With the development of the science of refractory metal materials such as steel, aluminum, titanium and other metal industries, the development of molybdenum and molybdenum alloys has gradually formed a relatively complex and complete structural system.
I have reviewed a large amount of domestic and foreign relevant materials, and based on this, I propose views and methods for classifying molybdenum alloys, as well as predictions for the direction of development of molybdenum alloys, hoping to assist researchers and producers involved in molybdenum alloys. studies and production.
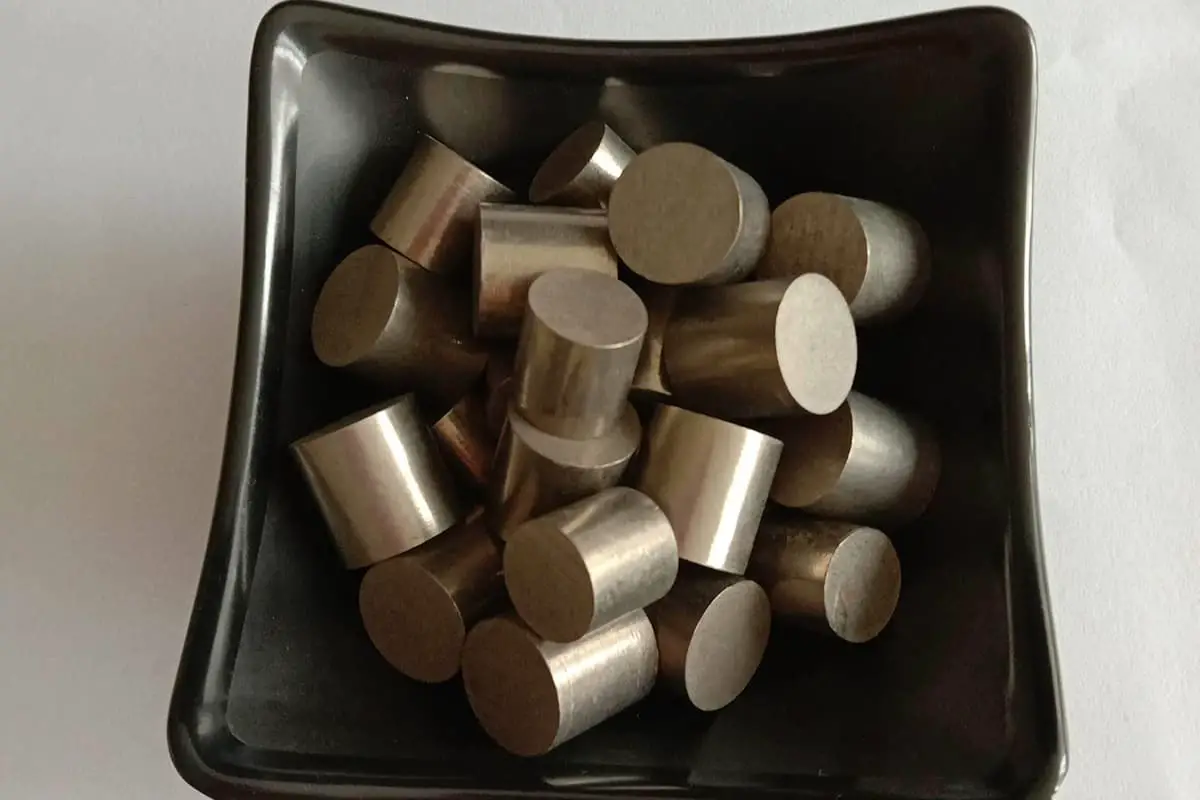
2. Brief History of the Development of Molybdenum Alloy
Since the discovery of molybdenum metal in 1778, it has been widely used in metallurgy, electric light sources, electronics industry, chemical industry, glass and fiberglass industry, medical industry and so on.
However, due to its inherent performance defects (such as low plastic-brittle transition temperature, limited strength, hardness, etc.), various methods have been tried to improve it, thus promoting its path to alloy formation. .
Initially, trace elements such as titanium and zirconium were added to molybdenum to form trace element alloys (such as Mo-0.5Ti, Z-6, etc.), aiming to improve its performance by strengthening solid trace element solutions, eliminating grain limit brittle phase and using their reaction products (TiC, ZrC) as dispersion phases to strengthen the alloy.
At the same time, molybdenum was combined with tungsten, rhenium and other metals in certain proportions to form corresponding alloys (such as Mo-5Re, Mo-25W, etc.) to improve their heat resistance through extensive solid solution alloying, thus forming series of molybdenum-tungsten and molybdenum-rhenium alloys.
Based on the basis of microalloyed alloys, adding a certain amount of alloying elements can improve the room temperature brittleness of molybdenum alloys after high temperature use.
This evolved into the Mo-Ti-Zr-C series alloys. The TZM and TZC alloys in this series have become the most important molybdenum alloys currently in use and are an important part of the molybdenum alloy family.
In recent years, it has been found that using hafnium to replace titanium as an additive element, its reaction product HfC has a stronger strengthening effect than TiC, which can further improve the performance of molybdenum alloys.
Based on this, the Mo-Hf-C (MHC) and Mo-Hf-Zr-C (ZHM) series of alloys were established.
At the same time, people are trying to combine the solid solution dispersion strengthening effect of trace elements with the solid solution strengthening effect of a large amount of molybdenum and tungsten alloy, in order to achieve a fundamental breakthrough in the comprehensive performance of molybdenum alloys.
This led to the Mo-W-Zr-Hf-C and Mo-W-Hf-C series of alloys, which are still under development.
Using a wet doping method, the addition of potassium, silicon, aluminum and other trace elements to molybdenum forms doped molybdenum, which is currently reported to be the molybdenum alloy with the best performance at high temperatures.
Its recrystallization temperature can reach 1800 and even after recrystallization, it still has a certain strength, plasticity and broad development prospects. At the same time, adding rhenium metal to doped molybdenum alloys can produce alloys with even higher comprehensive performance.
Currently, there are reports of addition of rare earth oxides to pure molybdenum and various types of molybdenum alloys. This has become more mature various types of molybdenum alloy. At this point, a complex evolutionary diagram of molybdenum alloys has been formed (see figure).
3. Classification of molybdenum alloys
This article classifies molybdenum alloys in two ways: according to the alloy elements and the types of alloy reinforcement. Attached is a detailed classification table for molybdenum and molybdenum alloys.
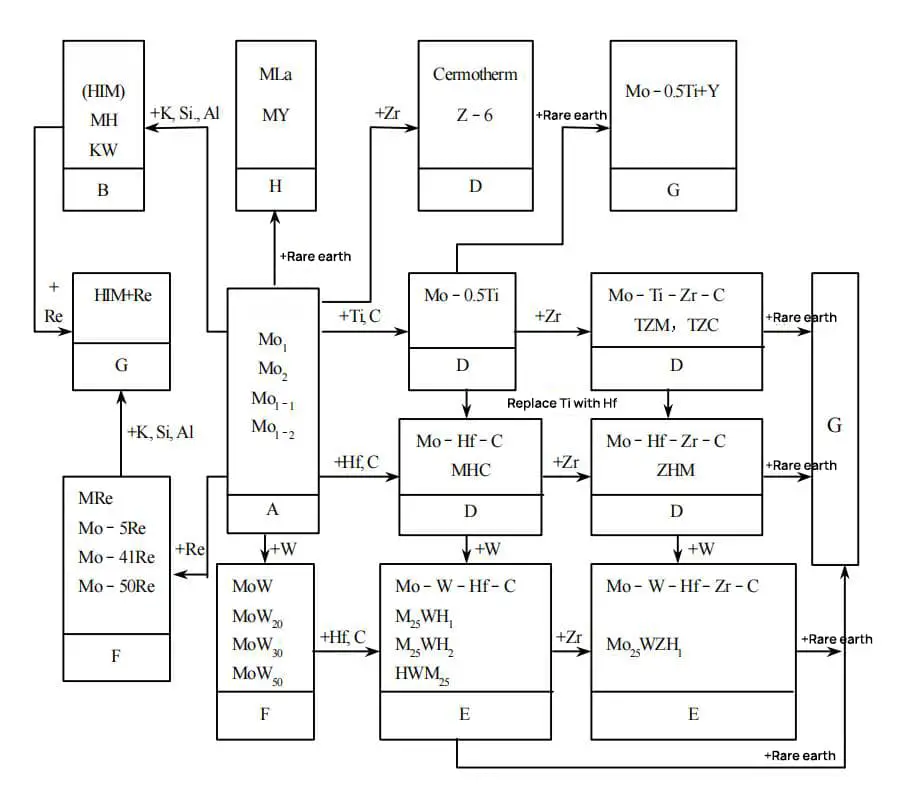
Observation :
- A: Pure Molybdenum
- B: Enhanced Doped Dispersion
- C: Doped Dispersion + Strengthened Solid Solution
- D: Reinforced Solid Solution + Reinforced Carbide Dispersion
- E: Strengthened Solid Solution + Strengthened Solid Solution + Carbide Dispersion
- F: Strengthened Solid Solution
- G: Reinforced Solid Solution + Enhanced Carbide Dispersion + Enhanced Rare Earth Oxide Dispersion
- H: Strengthened rare earth oxide dispersion
3.1 Classification by Alloy Elements
(1) Binary League
Binary alloys refer to molybdenum alloys with a single alloying element added to the molybdenum. This type of alloy can be divided into two types. One of them is a molybdenum alloy with tungsten and rhenium as alloying elements.
In this type of alloy, the amount of added alloying elements is large and the performance of the alloy is mainly characterized by good hardness and heat resistance. The other type is a molybdenum alloy with titanium, zirconium and hafnium as alloying elements.
The characteristic of this type of alloy is that the amount added is small and the performance of the alloy is slightly improved compared with pure molybdenum. The main ones are Mo0.5Ti, Z-6 and MHC.
(2) Multicomponent alloy
Multicomponent molybdenum alloys are based on binary molybdenum alloys. In order to further improve alloy performance, a second or several alloy components are added to form alloys with excellent performance. The main ones include the following series:
Mo-Ti-Zr-C series: This type of alloy is based on Mo0.5Ti, with the addition of a certain amount of zirconium and carbon elements. It is currently the most mature and widely used excellent molybdenum alloy, often seen in plate, strip and sheet materials, and less used in wire rod materials. The main notes are TZC and TZM.
Mo-Hf-Zr-O Series: This type of alloy is based on the MoTi-Zr-C series. To further improve the performance of the alloy, hafnium is used to replace titanium. Due to researchers' different hafnium ratios, various grades such as ZHM, ZHM4, ZHM6, ZHM7, ZHM8 were formed. These alloys are also excellent, but there are currently no reports of widespread use either nationally or internationally.
Mo-W-Hf-C and Mo-W-Hf-Zr-C series alloys are developed to combine the strengthening effects of large amounts of alloy in the matrix solution with the strengthening of trace element carbide dispersion, thereby producing alloys with excellent comprehensive properties (high strength, hardness and good high temperature performance) and overcoming room temperature brittleness after high temperature use. Currently, there are several grades such as M25WH1, M25WH2, HWM25, M25WZH1, but none are mature.
Doped molybdenum alloys are made by wet or dry doping, where a certain amount of potassium, silicon and aluminum elements are added to pure molybdenum. This can significantly increase the recrystallization temperature of molybdenum, maintaining good plasticity even after recrystallization.
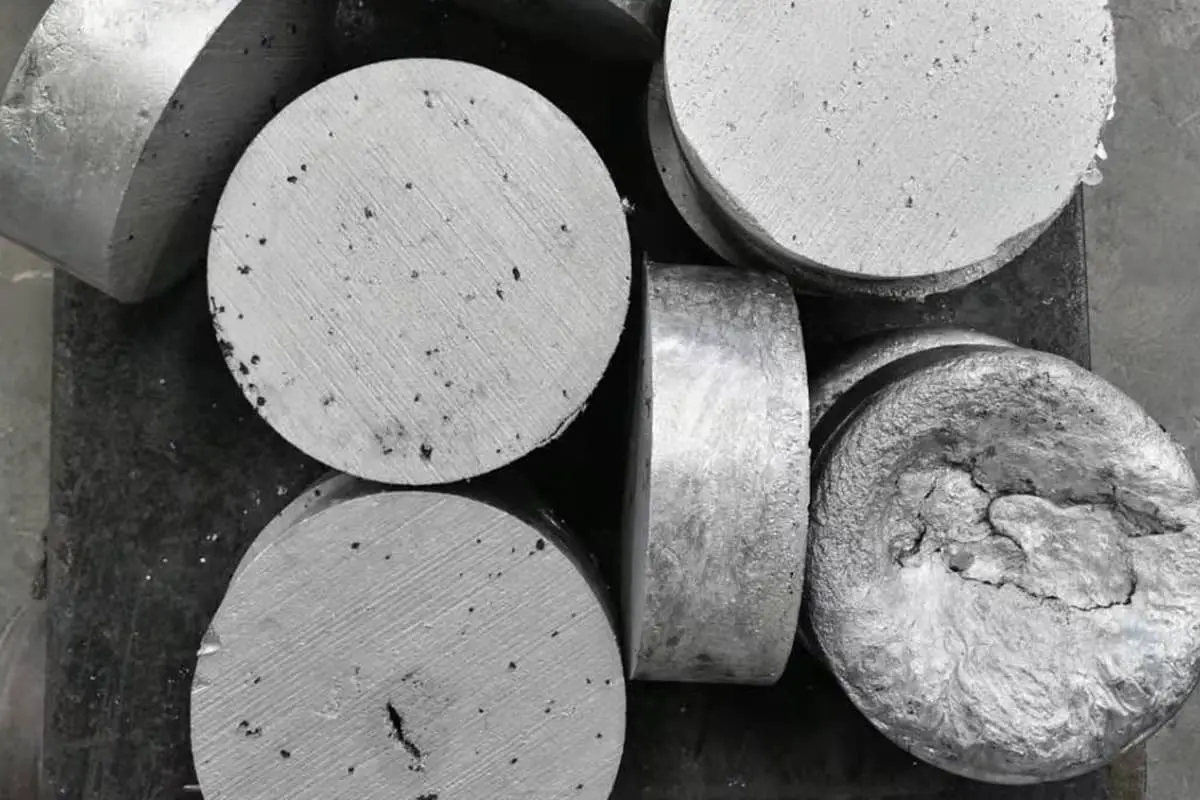
This type of molybdenum alloy has the highest reported recrystallization temperature, reaching 1800. It is not only used in rods and wires, but also has a wide range of applications in sheets, strips and sheets.
In certain military applications, the doping effect of potassium, silicon and aluminum is combined with the solid solution strengthening effect of rhenium to produce products that meet special high performance requirements.
Rare earth molybdenum alloys have been extensively tested in single-component and multi-component alloys due to the recrystallization temperature and anti-sagging properties of molybdenum. Mature ones include MLa and MY alloys, which add 1% ~ 2% La2O3 or Y2O3 to pure molybdenum.
These alloys have good high temperature performance and a wide application prospect. Mo-0.5Ti+Y adds Y2O3 to form a dispersion alloy based on a single element alloy, which is expected to secure a place in the field of sheets, strips and sheets.
Work on adding rare earth oxides to TZM, TZC, ZHM alloys is currently in the research and development phase. The addition of rare earth oxides can significantly improve the stable chemical structure and good strengthening effect.
3.2 Classification by Type of Reinforcement
From the diagram of the evolution process and strengthening method of molybdenum alloy, it can be seen that alloys can be divided into the following categories according to the type of alloy strengthening:
(1) Solid solution reinforcement type alloys
Chart solid solution strengthening alloys: This type of alloy mainly refers to the Mo-0.5Ti Z-6 single element system molybdenum alloy, which mainly depends on adding a small amount of alloying elements to the solid solution to improve league performance.
This strengthening effect is very weak, and the performance of the alloy can only be slightly higher than that of pure molybdenum. Therefore, a certain amount of carbon is often added to the alloy while adding traces of solid solution elements, allowing carbon and alloy elements to form carbides to play a role in strengthening the dispersion.
Large amount of solid solution strengthening alloys: This type of alloy refers to the molybdenum-tungsten and molybdenum-rhenium series alloys. They mainly rely on adding a large number of alloying elements to form a solid solution alloy with molybdenum to increase the heat resistance and hardness of the alloy, but the machinability worsens.
(2) Dispersion-strengthened alloys
Carbide dispersion reinforced alloys: In addition to the strengthening effect of trace elements in multi-element molybdenum alloys, carbide strengthening cannot be adopted.
Active elements such as titanium, zirconium and hafnium, added to molybdenum alloys, react with carbon to generate refractory carbides (TiC, ZrC, HfC) that exist in the form of fine dispersed phases, playing a role in strengthening the dispersion at high temperatures.
The alloys TZM, TZC of the Mo-Ti-Zr-C series and the ZHM of the Mo-Hf-Zr-C series all belong to this category of alloys.
Rare Earth Oxide Dispersion Strengthened Alloys: These alloys increase the strength of the alloy through the dispersion strengthening effect of fine rare earth oxide particles. Compared with carbide strengthening, its dispersion strengthening effect is stronger. Examples of such alloys include ML10, MY and Mo-0.5Ti+Y.
(3) Doped reinforced alloys
This category refers to alloys with different amounts of molybdenum doping. They not only rely on the solid solution strengthening effect of doping elements, but also mainly rely on the presence of potassium bubbles at high temperatures to further improve the performance of the alloy.
(4) Fully reinforced alloys
Generally speaking, there is a close relationship between the various strengthening mechanisms of molybdenum alloys. The strengthening effect of trace elements occurs mainly at temperatures between 1100 and 1300.
When the temperature rises further, it fails. The strengthening effect of carbide dispersion is most evident in 1400-1500. Between 1500 and 1800, carbides soften and become unstable. At this temperature, the strengthening effect of high-melting rare earth oxides is significant.
Above 2000, the rare earth oxides begin to soften, while the strengthening effect of the doped potassium and silicon bubbles is evident. The search for high-performance materials has always been ongoing, and fully reinforced alloys are currently one of the important points in the research and development of molybdenum alloys.
4. Opinions on the development prospects of molybdenum alloys
(1) Because the production process of molybdenum alloy and pure molybdenum is very similar, with the development of refractory materials, pure molybdenum materials will gradually be replaced by high-performance molybdenum alloy materials.
(2) For a considerable period, the Mo-Ti-Zr-C series of TZM, TZC alloys, with their excellent performance and mature technology, will remain predominant in the application of plates, strips and sheets. Rare earth molybdenum with good bending resistance and high temperature performance will gradually replace pure molybdenum in rods and wires.
(3) Doped molybdenum and doped molybdenum with addition of rhenium elements, these two types of molybdenum alloys, with their excellent comprehensive performance, will gradually develop and grow into civil and military products, having a promising development prospect.
(4) Strengthened and comprehensive molybdenum alloys will be the new target that people are pursuing.
Classification | League Series | Note | Nominal Composition | Recrystallization temperature |
Pure Molybdenum | Molybdenum for powder metallurgy | Mo 1 Mo 2 | Pure Molybdenum | 1000℃-1100℃ |
Molten molybdenum | Mo 1-1 Mo 1-2 | |||
It belongs to ceramic material | Molybdenum-tungsten alloy | Cut 20 | Mo-25%W | ~1200℃ |
Cut 25 | Mo-25%W | |||
Cut 30 | Mo-30%W | |||
Cut 5th | Mo-50%W | |||
Molybdenum-rhenium alloy | Mo-5Re | Mo-5%Re | 1200℃-1300℃ | |
Mo-41Re | Mo-41%Re | |||
Mo-50Re | Mo-50%Re | |||
Molybdenum-Zirconium Alloy | Z-6 | Mo-0.5ZrO | ~1250℃ | |
Cermatherm | 40%-90%Mo-60%-10%ZrO | It belongs to ceramic materials | ||
Molybdenum-Titanium Alloy | Mo-0.5Ti | Mo-0.5Ti-0.01-0.04C | 1100℃-1300℃ | |
Molybdenum-hafnium alloy | MHC | Mo-1.2Hf-0.005C | 1550℃ | |
Molybdenum Doping | Liga ELE | MH(HD) | Mo-0.0015K-0.002Si | -1800℃ |
K.W. | Mo-0.002K-0.003Si-0.001A1 | |||
Rare Earth Molybdenum Alloy | Molybdenum-Titanium-Yttrium Alloy | Mo-0.5Ti-Y | Mo-0.5Ti-1.6%Y | 1500℃ |
molybdenum alloy | MLA | Mo-1%-2%La2O3 | 1400℃-1500℃ | |
Molybdenum-Yttrium Alloy | Hey | Mo-0.5%-1.5%Y | 1500℃-1600℃ | |
Multi-Element Molybdenum Alloy | Mo-Ti-Zr-C | TMZ | Mo-0.5Ti-0.07~0.12%Zr-0.01~0.04C | 1300℃~1500℃ |
TZC | Mo-1.0~1.5Ti-0.1~0.3Zr-0.02~0.04C | |||
Mo-Hf-Zr-C | ZHM | Mo-0.5Zr-1.5Hf-0.2C | 1550℃ | |
ZHM 4 | Mo-1.2Hf-0.4Zr-0.15C* | |||
ZHM 6 | Mo-1.5Hf-0.5Zr-0.19C* | |||
ZHM 7 | Mo-1.8Hf-0.6Zr-0.23C* | |||
ZHM 8 | Mo-2.1Hf-0.7Zr-0.27C* | |||
Mo-W-Hf-C | HWM25 | Mo-1.0Hf-25W-0.07C | ~1650℃ | |
M 25 QU 1 | Mo-23.72W-1.2Hf-0.08C* | |||
M 25 QU 2 | Mo-23.9W-1.0Hf-0.006C* | |||
Mo-W-Hf-Zr-C | Mo 25 WZH 1 | Mo-23.3W-1.2Hf-0.4Zr-0.1C* | ||
Note: * indicates that the research has not yet been fully established domestically. |