I. Steel alloy elements
Steel
Steel is a collective term for iron alloys with carbon content ranging from 0.02% to 2.04% by mass. The chemical composition of steel can vary significantly. Steel containing only carbon is called carbon steel or plain steel.
However, in actual production, steel often incorporates different alloying elements based on its intended use, such as manganese, nickel, and vanadium.
Based on performance and usage, they are divided into structural steel, tool steel and special performance steel.
Carbon
Present in all steels, carbon is the most vital hardening element. Helps increase the strength of steel. Typically, you want tool steel to have more than 0.6% carbon, also known as high carbon steel.
Chrome
Chromium increases wear resistance, hardness and, most importantly, corrosion resistance. If a steel has more than 13% chromium, it is considered stainless steel. However, all steels can rust if not maintained properly.
Manganese
Manganese is a crucial element that helps form grain structure, increasing toughness, strength and wear resistance. It is used to deoxidize steel during heat treatment and rolling processes.
Manganese is present in most types of steel used in knives and scissors, except A-2, L-6 and CPM 420V.
Molybdenum
As a carbide former, molybdenum prevents steel from becoming brittle and maintains the steel's strength at high temperatures. It is found in many steels.
Air hardening steels (such as A-2, ATS-34) always contain 1% or more molybdenum, allowing them to air harden.
Nickel
Nickel maintains strength, corrosion resistance and toughness. It is present in L-6, AUS-6 and AUS-8.
Silicon
Silicon helps increase resistance. Like manganese, it is used in the steel production process to maintain the steel's strength.
Tungsten
Tungsten increases wear resistance. It is mixed with a suitable proportion of chromium or manganese to produce high-speed steel. M-2 high-speed steel contains a significant amount of tungsten.
Vanadium
Vanadium increases wear resistance and ductility. A vanadium carbide is used in the manufacture of steel bars. Many types of steel contain vanadium, including M-2, Vascowear, CPM T440V and 420VA, which have high vanadium content.
The main difference between BG-42 and ATS-34 is the former's vanadium content.
II. Types of steel
( 1) Common steel
The. Carbon structural steel:
(a)Q195;
(b) Q215 (A, B);
(c) Q235 (A, B, C);
(d) Q255 (A, B);
(e) Q275.
B. Low Alloy Structural Steel
w. Common Structural Steel for Specific Purposes
( 2) Quality steel (including high-quality steel)
The. Structural steel:
(a) High quality carbon structural steel;
(b) Alloy structural steel;
(c) Spring steel;
(d) Free cutting steel;
(e) Bearing steel;
(f) High quality structural steel for specific purposes.
B. Tool steel:
(a) Carbon tool steel;
(b) Alloy tool steel;
(c) High speed tool steel.
w. Special Performance Steel:
(a) Acid-resistant stainless steel;
(b) Heat-resistant steel;
(c) Alloy steel for electric heating;
(d) Electrical steel;
(e) Wear-resistant steel with high manganese content.
III. What is carbon steel?
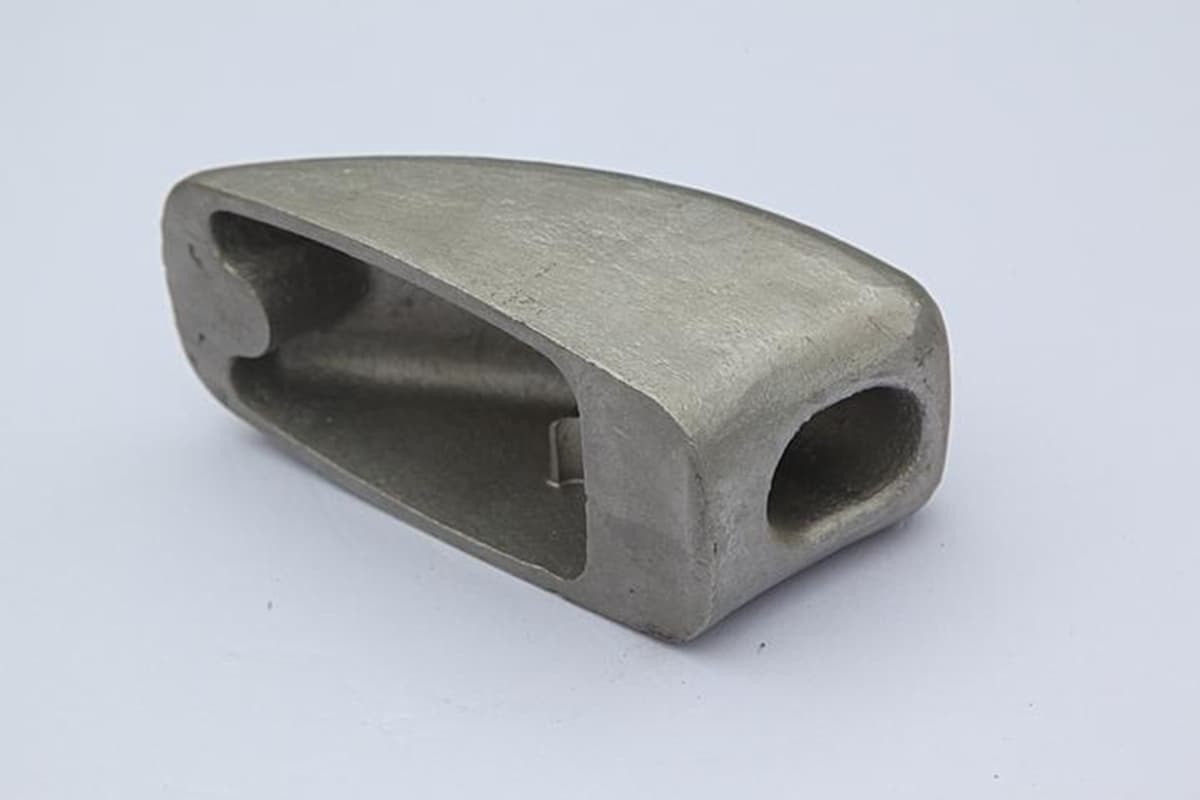
The main mechanical properties of steel depend on its carbon content. Steel that does not contain a large amount of alloying elements is sometimes called plain carbon steel or carbon steel.
Carbon steel, also known as plain carbon steel, refers to iron-carbon alloys with a carbon content (WC) of less than 2%.
In addition to carbon, carbon steel often contains small amounts of silicon, manganese, sulfur and phosphorus.
Carbon steel can be classified into three types based on its application: carbon structural steel, carbon tool steel, and free-cutting structural steel. Carbon structural steel can be divided into building structural steel and machine structural steel.
According to the casting method, carbon steel can be divided into open furnace steel, converter steel and electric furnace steel.
According to the deoxidation method, carbon steel can be classified as boiling steel (F), dead steel (Z), semi-dead steel (b) and special dead steel (TZ).
Based on carbon content, carbon steel can be categorized into low carbon steel (WC ≤ 0.25%), medium carbon steel (WC 0.25% -0.6%), and high carbon steel (WC > 0.6%).
Based on phosphorus and sulfur content, carbon steel can be divided into ordinary carbon steel (higher phosphorus and sulfur content), high-grade carbon steel (lower phosphorus and sulfur content), superior high-grade steel (even lower phosphorus and sulfur content) and high quality special steel.
Generally, as the carbon content increases in carbon steel, the hardness and strength also increase, but the ductility decreases.
4. What is stainless steel?
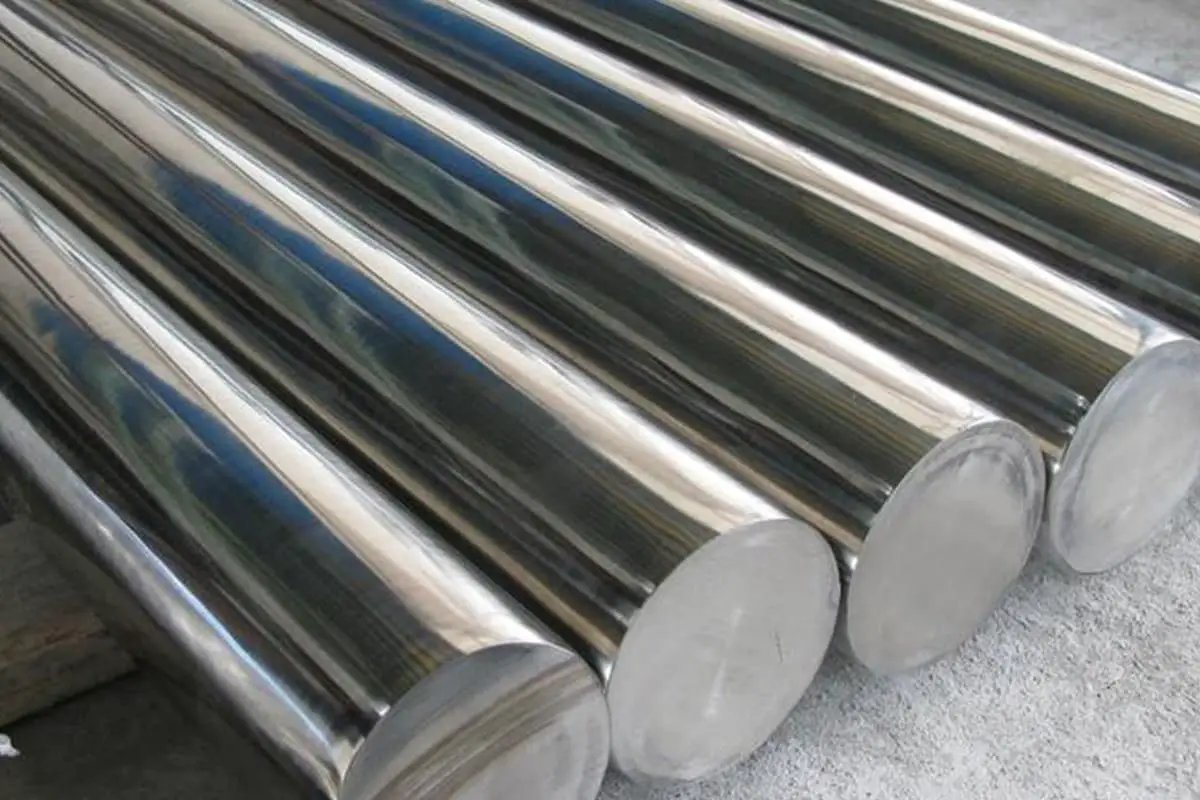
Stainless steel, also known as acid-resistant steel, is made up of two main components: stainless steel and acid-resistant steel. In simple terms, steel that can resist atmospheric corrosion is called stainless steel, while steel that can resist corrosion by chemical means is called acid-resistant steel. Stainless steel is a high-alloy steel with more than 60% iron as a base, incorporating alloying elements such as chromium, nickel and molybdenum.
When steel contains more than 12% chromium, it is resistant to corrosion and rust from the atmosphere and dilute nitric acid. This is because chromium can form a chromium oxide film that firmly adheres to the surface of the steel, effectively protecting it from corrosion. The chromium content in stainless steel is generally greater than 14%, but stainless steel is not completely immune to rust.
In coastal areas or places with severe air pollution, when the air contains a large amount of chloride ions, the exposed surface of stainless steel may develop some rust spots. However, these rust stains are limited to the surface and do not corrode the internal matrix of the stainless steel.
Generally, steel with a chromium content (Wcr) greater than 12% has the characteristics of stainless steel. Stainless steel can be classified into five categories based on its microstructure after heat treatment: ferritic stainless steel, martensitic stainless steel, austenitic stainless steel, austenitic-ferritic (duplex) stainless steel, and precipitation hardening stainless steel.
Stainless steel is commonly categorized based on its matrix structure:
Ferritic stainless steel: Contains 12% to 30% chromium. Its corrosion resistance, toughness and weldability improve with increasing chromium content. It has better resistance to chloride stress corrosion cracking than other types of stainless steel.
Austenitic Stainless Steel: Contains more than 18% chromium, along with approximately 8% nickel and small amounts of molybdenum, titanium, nitrogen and other elements. It has excellent comprehensive properties and can resist corrosion in various media.
Austenitic-Ferritic Stainless Steel (Duplex): Combines the advantages of austenitic and ferritic stainless steel and presents superplasticity.
Martensitic Stainless Steel: It has high strength, but low ductility and weldability.
V. Carbon Steel vs Stainless Steel
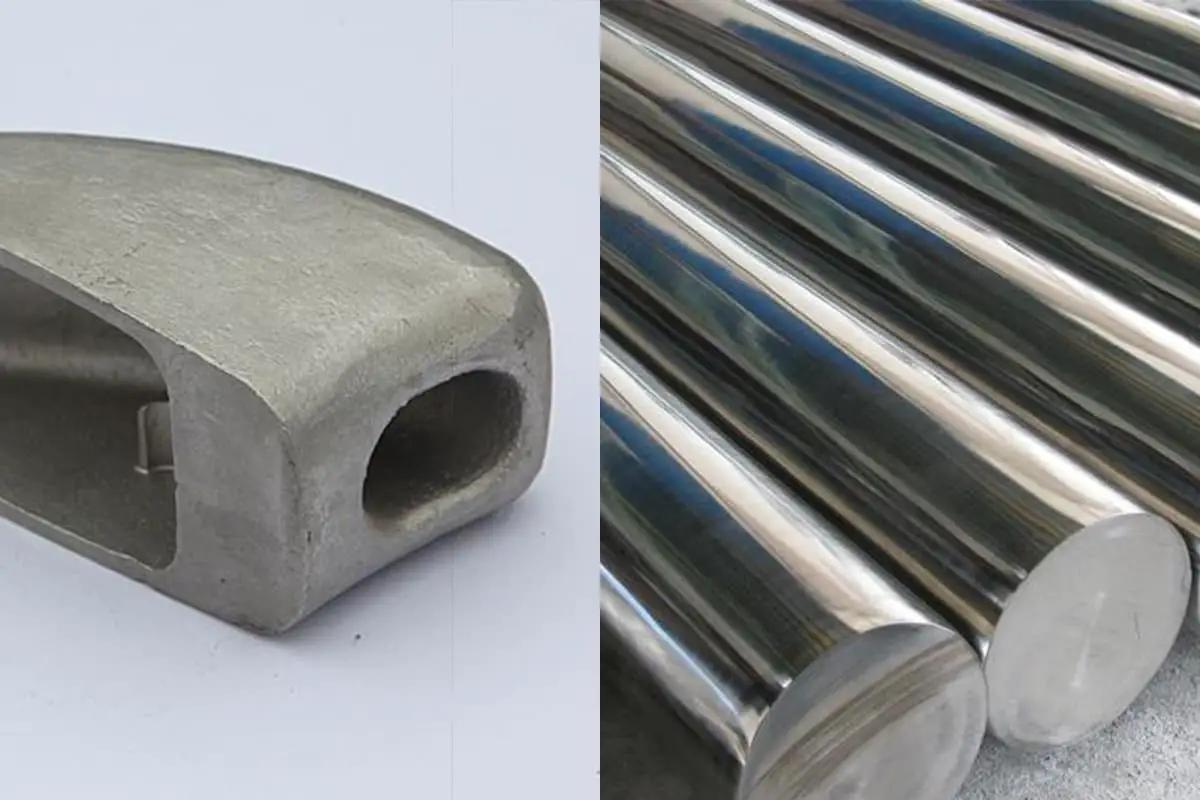
Color: Stainless steel contains more chromium and nickel, resulting in a silver appearance. Carbon steel consists mainly of carbon and iron, with fewer other metallic elements, giving it a predominantly iron and darker color.
Surface texture: Stainless steel, with a higher content of other metallic elements, has a smooth surface. Carbon steel, containing more iron and carbon, has a rougher surface and lacks the smoothness of stainless steel.
Magnetism: Carbon steel has magnetic properties on its surface and can be attracted to a magnet. Stainless steel is generally non-magnetic under normal conditions and is not attracted to magnets.
Carbon content: The mechanical properties of carbon steel depend on its carbon content, with the steel containing less than 2% carbon and generally not adding a significant amount of alloying elements. In contrast, stainless steel, to maintain its resistance to corrosion, has a relatively low carbon content, normally not exceeding 1.2%.
Alloy content: Carbon steel contains a small amount of alloying elements such as silicon, manganese, sulfur and phosphorus. Stainless steel has a higher content of alloying elements, mainly chromium and nickel, exceeding 12%.
Corrosion resistance: Carbon steel, with its low alloy content, has weaker corrosion resistance. Stainless steel, with a higher content of chromium and nickel, has greater resistance to corrosion.
The distinction between carbon steel and stainless steel lies mainly in their resistance to corrosion. However, stainless steel, with its superior properties, performs functions that other types of steel cannot replace in practical applications.
For example, some heat-resistant stainless steels and stainless steels with excellent surface characteristics are widely used as decorative materials.
Furthermore, the exceptional mechanical properties of stainless steel make it indispensable in various industrial sectors.
Common steel, also known as carbon steel, is an iron-carbon alloy. It is categorized into low carbon steel, medium carbon steel and cast iron based on carbon content.
Generally, steel with less than 0.2% carbon is called low-carbon steel, also known as soft iron or pure iron; steel with carbon content between 0.2-1.7% is called steel; and steel with more than 1.7% carbon is called pig iron.
1. Steel with a chromium content of more than 12.5% has high resistance to corrosion from external media (acid, alkaline salt) and is therefore called stainless steel.
Depending on the internal structure of the steel, stainless steel can be divided into martensitic, ferritic, austenitic, ferritic-austenitic and precipitation hardening types, with a total of 55 types specified by the national standard GB3280-92.
In everyday life, we often encounter austenitic stainless steel (some call it stainless steel with nickel) and martensitic stainless steel (some refer to it as “stainless iron”, which is scientifically incorrect and prone to misunderstanding).
Typical grades of austenitic stainless steel include 0Cr18Ni9 or “304” and 1Cr18Ni9Ti. Martensitic stainless steel, used in making scissors and knives, mainly includes grades 2Cr13, 3Cr13, 6Cr13, 7Cr17, etc.
2. Differences in the compositions of these two types of stainless steel result in different internal metallic microstructures.
3. Austenitic stainless steel, due to the high chromium and nickel content (approximately 18% chromium and more than 4% nickel), has an austenitic internal structure.
This structure is non-magnetic and cannot be attracted to a magnet. It is commonly used for decorative materials such as stainless steel pipes, towel racks, tableware, stoves, etc.
4. Martensitic stainless steel is used to make knives and scissors. As cutting tools must be sharp, they must have a certain hardness.
This type of stainless steel must undergo heat treatment to change its internal structure and increase its hardness to be used as a cutting tool.
But this type of stainless steel has a hardened martensitic internal structure and is magnetic, which means it can be attracted to a magnet.
Therefore, one cannot simply determine whether a material is stainless steel based on its magnetism.
SAW. Stainless Steel Seamless Tubes Versus Carbon Steel Seamless Tubes
The distinction between stainless steel seamless pipes and carbon steel seamless pipes mainly lies in the different design rules for these two types of steel, which means that their design rules are not interchangeable. The differences can be summarized as follows:
Firstly, stainless steel hardens during cold working due to a phenomenon called work hardening. For example, during bending it presents anisotropy, with different properties in the transverse and longitudinal directions.
The increase in strength from cold work can be used to increase the safety factor, especially when the folded area is small compared to the total area, making the increase insignificant.
Secondly, the stress-strain curve of stainless steel differs from that of carbon steel. The elastic limit of stainless steel is approximately 50% of its yield stress, which, according to standard regulations, is lower than the yield stress of medium carbon steel.
Lastly, stainless steel does not have a defined yield point. Instead, the yield stress is usually represented by σ0.2 and is considered an equivalent value.
VII. Heat Treatment and Mechanical Performance Indicators of Steel
Heat treatment is a process that manipulates the physical properties of a metal using heating and cooling. Through heat treatment, the microstructure of steel can be improved to meet specific physical requirements.
Some of the characteristics achieved through this process include toughness, hardness and wear resistance. These properties are obtained using heat treatment techniques such as hardening, tempering, annealing and surface hardening.
Hardening , also known as quenching, involves uniformly heating the metal to an appropriate temperature and then quickly immersing it in water or oil for abrupt cooling, or cooling it in air or a freezing area to achieve the desired hardness.
Tempering is necessary after hardening, as the steel becomes brittle and susceptible to fracture due to the stress induced by rapid cooling.
To eliminate this brittleness, tempering is performed by reheating the steel to an appropriate temperature or color, followed by rapid cooling.
Although this process slightly reduces the hardness of the steel, it increases its toughness and reduces its brittleness.
Annealing is a method used to eliminate internal tensions in steel and homogenize it. The process involves heating the steel above its critical temperature and then placing it in dry ash, lime, asbestos or sealing it inside a furnace to allow it to cool slowly.
Hardness refers to the ability of a material to resist penetration by an external object. A common method of testing the hardness of steel is to use a file on the edge of the piece, where the depth of the file marks indicates the degree of hardness.
However, this method is not highly accurate. Modern hardness testing is typically done with a hardness tester. The Rockwell hardness test is one of the most commonly used tests.
The Rockwell hardness tester measures the depth of penetration of a diamond indenter into metal; the deeper the penetration, the lower the hardness. The depth of penetration can be accurately read on a dial, and this reading is called the Rockwell hardness number.
Forging is a process in which metal is shaped by hammering. When steel is heated to forging temperature, it can be forged, bent, drawn and shaped. Most steel is easy to forge when heated to a bright cherry red color. A common method for increasing the hardness of steel is through quenching.
Brittleness refers to the tendency of a metal to fracture easily. Cast iron, for example, is highly fragile and can even crack when dropped. There is a close relationship between brittleness and hardness; Typically, materials with high hardness also have high brittleness.
Ductility (also known as malleability) refers to the ability of a metal to permanently deform without fracturing when subjected to external forces. Ductile metals can be spun into fine wires.
Elasticity refers to the property of a metal to deform under external forces and return to its original shape when the forces are removed. Spring steel is a highly elastic material.
Malleability also known as forgeability, is another description of the ductility or softness of a metal. Malleability is the property of a metal to deform without fracturing when subjected to hammering or rolling.
Hardness is the ability of a metal to resist vibrations or impacts. Tenacity is the opposite of fragility.