When selecting the gear material and its heat treatment, it is mainly based on the working conditions such as transmission mode, load property and size, transmission speed and gear accuracy requirements.
At the same time, it is also necessary to consider the hardenability of the steel and the hardening requirements of the tooth surface, the matching of the material and the hardness value of the gear pair according to the gear module and section size.
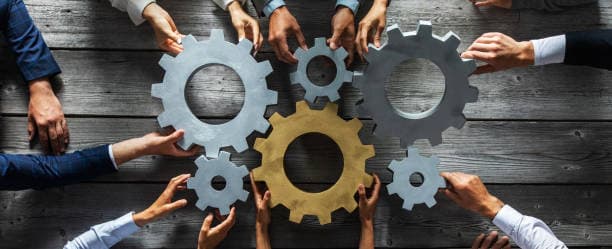
Gears can be made from various materials, including cast iron, steel, powder metallurgy materials, non-ferrous alloys (such as copper alloys), and non-metallic materials.
Steel is the most commonly used material for gears and can be low carbon steel, medium carbon steel, high carbon steel or alloy steel. Proper heat treatment such as normalizing, annealing, quenching and tempering, carburizing, nitriding or surface quenching can improve material performance and cutting ability as well as processing quality and service life of gears.
Below are the characteristics and applicable conditions of various steel materials and heat treatment methods for gears.
1. Quenched and tempered steel
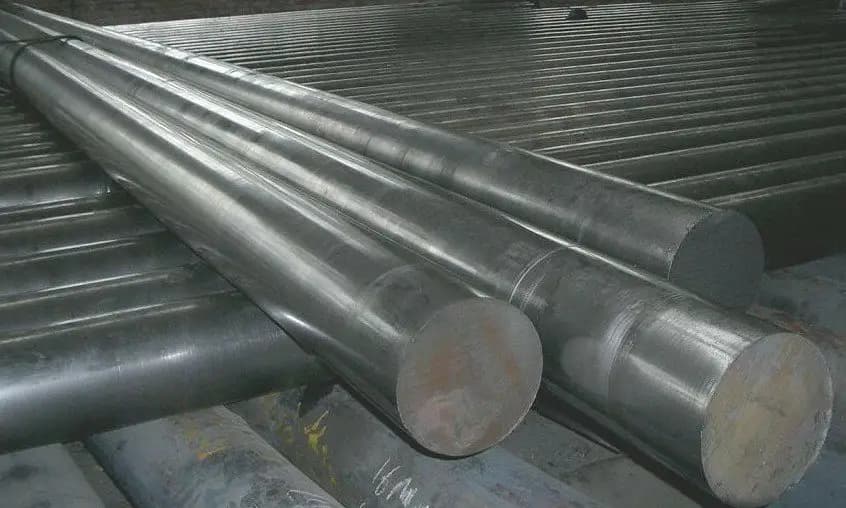
Steel grades: 45, 35SiMn, 42SiMn, 37SiMn2MoV, 40MnB, 45MnB, 40Cr, 45Cr, 35CrMo, 42CrMo, etc.
Process 1: Temperament or Normalization
(1) Quenched and tempered steel gears have good strength and toughness, typically with a hardness range of 220-300 HBW.
(2) If the hardness of a hardened pinion cannot be improved due to tool limitations, a normalized large gear can be used to maintain the hardness difference between the large and small gears. However, normalized gears have lower strength than hardened gears.
(3) Fine cutting can be used to eliminate distortion caused by heat treatment and maintain gear accuracy.
(4) Standardized gears do not require special heat treatment or tooth surface finishing equipment, which makes them relatively cheap to manufacture.
(5) Standardized gears have lower tooth surface hardness, which may limit their load capacity.
Applicable conditions: Normalized gears are widely used for general medium and low speed applications with low strength and precision requirements, as well as for large gears that are difficult to heat treatment and finishing.
Process 2: Surface Hardening (Induction Hardening, Flame Hardening)
(1) Surface hardened gears have high tooth surface hardness, corrosion resistance and wear resistance. The hardened surface produces residual stress, significantly improving tooth root strength. The general range of tooth surface hardness is 45-55 HRC for alloy steel and 40-50 HRC for carbon steel.
(2) Quenching and tempering treatment can be carried out before surface quenching to further improve the strength of the core.
(3) Induction hardening time is short.
(4) The depth and hardness of the hardening layer may vary across the tooth surface.
(5) Rapid heating and cooling may cause cracking.
Applicable conditions: Surface hardened gears are widely used for high load and small volume applications.
2. Carburizing steel
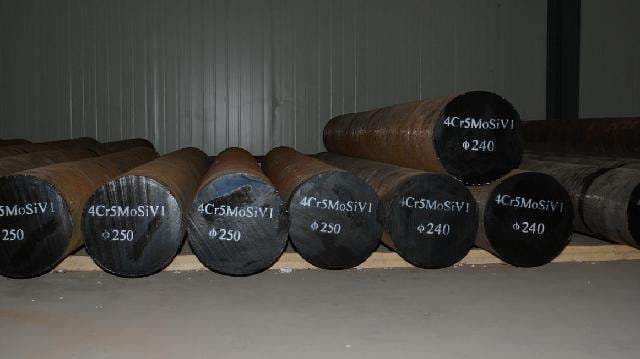
Steel grades: 20Cr, 20CrMnTi, 20CrMnMo, 20CrMo, 22CrMo, 20CrNiMo, 18Cr2Ni4W, 20Cr2Ni4A, etc.
Process: Carburizing and Quenching
(1) Carbureted and hardened gears have high tooth surface hardness, corrosion resistance and wear resistance. The hardened surface produces residual stress, significantly improving tooth root strength. The general tooth surface hardness range is 56-63 HRC.
(2) Carbureted gears have good cutting performance.
(3) Carburizing and quenching cause significant distortion in heat treatment, requiring post-heat treatment grinding to obtain high precision. This increases processing time and cost.
Applicable conditions: Carbureted and hardened gears are widely used for medium and small gears with high load capacity, impact resistance, precision and small volume.
3. Nitriding steel
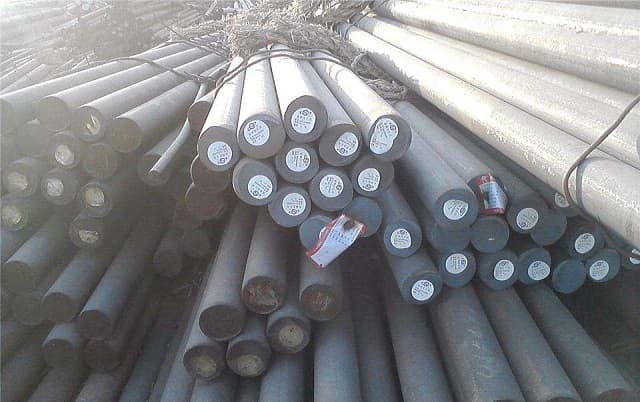
Steel grades: 38CrMoAlA, 30CrMoSiA, 25Cr2MoV, etc.
Process: nitriding treatment
(1) Nitrided gears have very high tooth surface hardness, pitting corrosion resistance and wear resistance. The core has good strength. Medium carbon steel is often quenched and tempered first to improve core strength.
(2) Due to the low heating temperatures, the heat treatment distortion is minimal and the teeth do not require grinding after nitriding treatment.
(3) The hardened layer is thin, making the gear less suitable for impact loads and with lower load capacity than carbureted and hardened gears.
(4) Nitriding treatment takes longer and is more expensive than other heat treatments.
Applicable conditions: Nitrided gears are suitable for large and stable load applications and for situations where tooth surface finishing equipment is not available but hard tooth surfaces are required.
4. Cast steel
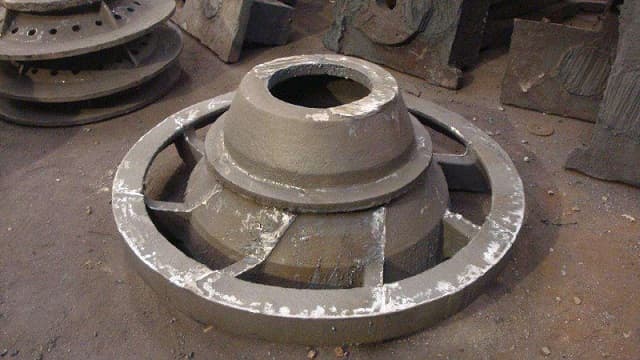
Steel grades: ZG310-570, ZG340-640, ZG42SiMn, ZG50SiMn, ZG40Cr1, ZG35CrMnSi, etc.
(1) This process is suitable for manufacturing large gears with complex shapes.
(2) The strength of gears manufactured using this process is lower than that of quenched and tempered steel of the same type and heat treatment.
(3) This process may result in casting defects.
Applicable conditions: This process is suitable for large gears that cannot be forged.
5. Cast iron
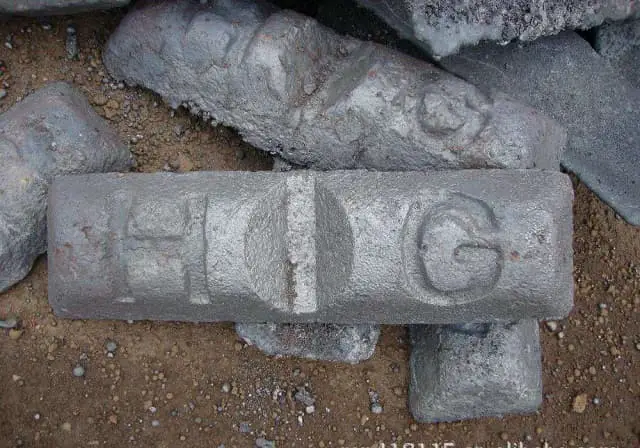
Steel grade: various gray cast iron, ductile iron, malleable cast iron, etc.
(1) Cast iron has low material cost.
(2) Cast iron gears have good wear resistance.
(3) This process is suitable for manufacturing large gears with complex shapes.
(4) Cast iron has good casting and cutting technologies.
(5) Cast iron gears have lower load capacity than other materials.
Applicable conditions: Gray cast iron and malleable cast iron are suitable for low-speed, light-load, non-impact gears. Ductile iron can be used for gears with large loads and impacts.