Laser Cutting Machine Maintenance Checklist
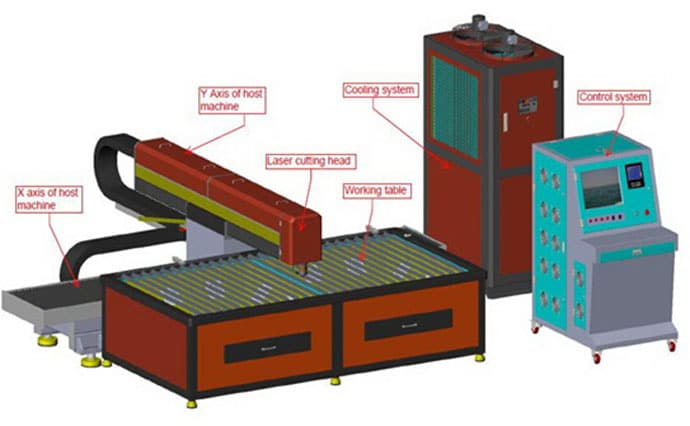
1. Daily inspection and maintenance of laser cutting machine
Before starting the machine every day, carefully check the working gas and laser cutting gas pressure. If the gas pressure is inadequate, it must be replaced immediately.
Check the X-axis zero point, Y-axis zero point, Z-axis zero point, laser readiness status and other buttons for damage (check the indicator light).
Check that the mounting screws for the X-axis, Y-axis, and Z-axis zero points, limit switch, and mounting blocks are tight and that the limit switches for each axis respond.
Make sure the circulating water level in the chiller is adequate. If the water level is insufficient, add water immediately.
Check the circulating waterway of the external optical path for leaks and immediately resolve any leaks; otherwise, the service life of the optical lens may be affected.
After each cutting day, inspect the focus lens for damage.
Inspect the telescoping outer light path skin cavity for burns or damage.
After completing daily work, immediately clean up cutting residue, clean the work area and keep it tidy. Additionally, ensure that all pieces of equipment are clean and free from dirt and avoid getting debris on any piece of equipment.
After daily work is completed, open the air compressor drain valve at the bottom of the air tank to drain the water. Close the drain valve once the wastewater has drained.
After completing daily work, follow the shutdown procedure and turn off the main power supply of the entire machine.
2. Weekly and irregular maintenance of the machine
It is essential to regularly clean the air vent of debris to ensure adequate ventilation.
Regularly check the filters in the gas path to immediately remove any water and debris.
Make sure the shift switch bracket and bumper bracket screws are not loose by checking them regularly.
To facilitate the heat dissipation of internal electrical components, please clean the dust on the fan filter screen of the electrical control cabinet in a timely manner.
Timely cleaning of the guide rail protective cavity is necessary to prevent damage to the guide rail, thereby extending its service life.
After installing the machine tool and using it for a period of time, it is vital to readjust the level of the machine tool to ensure its cutting accuracy.
Check the lubrication fill of the X, Y, Z axis guides and lead screws every two weeks to keep the moving parts lubricated. This can extend the life of the X, Y, Z axis guides and their lead screws.
Depending on the workshop environment, it is important to check irregularly (at least once a month) for pollution on the surface of the reflector and focusing lens and clean the optical lens in time to ensure its service life.
3. Maintenance of external optical path optical lenses
Avoid directly touching the surface of the optical lens (reflector, focusing lens, etc.) with your hands, as this can easily cause scratches on the mirror. If there are oil stains or dust on the mirror surface, clean it immediately to avoid affecting the lens performance.
Under no circumstances should the optical lens be cleaned with water and detergent, as the surface of the lens is coated with a special film. Using water and detergent to clean the lens may damage its surface.
Keep the lens away from dark and humid environments as this may cause the lens surface to age.
Dust, dirt or water vapor on the surface of the lens can easily absorb the laser light and damage the lens coating, which can significantly affect the quality of the laser beam, and in severe cases, there would be no laser beam at all.
If the lens is damaged, immediately contact the laser after-sales service department to repair it. Avoid using damaged lenses as this can accelerate damage to repairable lenses.
When installing or replacing the reflector or focusing lens, avoid using excessive pressure as it may cause lens deformation and affect beam quality.
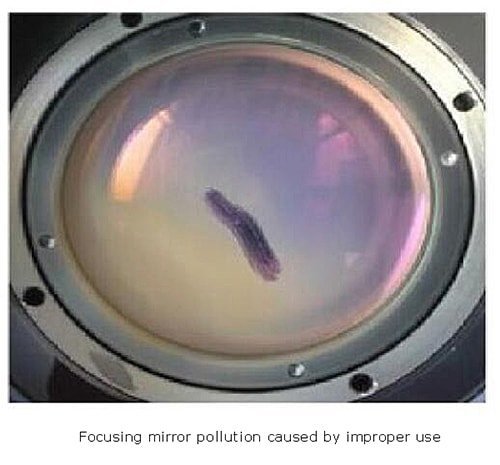
4. Optical lens installation or replacement methods
Pay attention before installing optical lenses:
(1) Wear clean clothes, wash your hands with soap or detergent, and wear clean, light-colored gloves;
(2) Do not touch the lens with any part of your hands;
(3) When removing the lens, wear gloves and hold it by the side of the lens. Do not directly touch the lens coating surface.
When mounting the lens, avoid blowing air against the lens with your mouth. Instead, place the lens on a clean table with a few sheets of lens paper underneath. Be careful when removing the lens to prevent it from being scratched or falling off, and do not apply any force to the coated surface of the lens. Make sure the lens mount in which the lens is installed is clean, and remove any dust or dirt from the mount with a clean air spray gun. Then gently place the lens in the holder.
When mounting the lens to the bracket, do not use excessive force to secure it, as this may cause deformation and affect beam quality.
Precautions to be taken when replacing optical lenses:
- Handle the lenses with the utmost care to avoid any damage when removing them from the case.
- Do not apply any pressure to the lens until the wrapping paper is removed.
- When removing the reflector and focusing lens from the box, wear clean gloves and grab them by the side of the lens.
- When removing the wrapping paper, make sure that no dust or debris falls onto the lens.
- After removing the lens, use a spray gun to remove any dust from the mirror surface, then place the lens on special paper intended for optical lenses.
- Clean the lens support frame and fixed frame to remove any dust or dirt, and ensure that no foreign objects fall onto the lens during mounting.
- When installing the lens into the lens holder, avoid applying excessive force to avoid deformation of the lens.
- Once lens assembly is complete, use a clean air gun to remove any remaining dust or foreign objects from the lens.
5. Steps to clean lenses
Different lenses require different cleaning methods. For flat mirror surfaces without lens support, use lens paper to clean, such as when cleaning a reflector. However, for curved or lens-supported mirror surfaces, it is best to use a cotton swab, such as when cleaning a focusing lens.
Steps to clean a lens with lens paper:
(1) Use a blower to remove any dust from the surface of the lens.
(2) Clean the lens surface with alcohol or lens paper. Do not use dry lens paper to drag directly across the mirror surface. Instead, place the lens paper on the lens surface, add 2-3 drops of high-purity alcohol or high-purity acetone, and slowly pull the lens paper toward the operator. Repeat this process several times until the mirror surface is clean.
(3) If the mirror surface is very dirty, fold the lens paper in half 2 to 3 times and repeat the above steps until the mirror surface is clean.
Steps to clean a lens with a cotton swab:
- Start by using a spray gun to remove dust from the mirror surface. Then use a clean cotton swab to remove any remaining dirt.
- Use a new cotton swab moistened with high-purity alcohol or acetone. Gently move the cotton swab in a circular motion from the center of the lens to rub it. After each circle, use another clean cotton swab and repeat the process until the lens is completely clean. Never reuse a cotton swab that you have already used for cleaning.
- Wash the lens with a clean cloth to remove any residue from the mirror surface. Be careful not to scratch the lens.
- Take the clean lens to a place with enough light to observe its reflection. If the reflection is clear, it means the lens has been properly cleaned. If the reflection is not clear, continue cleaning the lens.
- Finally, place the clean lens into a lens holder according to the appropriate method.
6. Daily laser maintenance
Before turning on the laser, it is important to carry out daily maintenance checks to ensure optimal performance.
- Inspect the laser working gas and cutting gas cylinders.
- Check that the cooling water pressure is in the range of 3.5 to 5 Bar.
- Check the temperature of the cooling water, ensuring it is the proper temperature required by the selected laser.
- Check the oil level in the laser vacuum pump and add more if necessary.
- Check for possible leaks in the laser's oil, water and gas paths, as well as possible leaks in the pneumatic components, vacuum pump tube joints and resonant cavity.
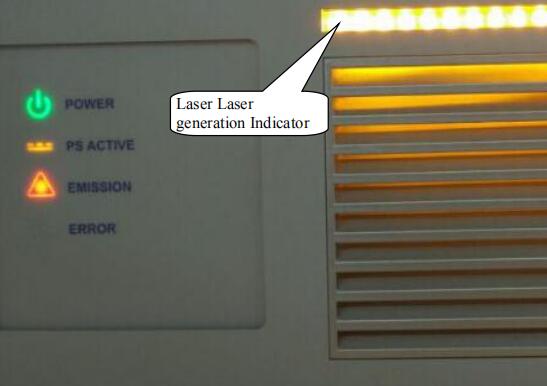
7. Weekly laser maintenance
- Check whether there is oil or water in the laser gas mixing unit. If there are any, clean them immediately. Also, be sure to inspect the laser gas drying filter, and if the color changes more than 1/4 to red or white, it will need to be replaced. Typically, its normal color is blue.
- Check the vacuum pump and Roots pump oil levels and if insufficient, add more oil.
- Inspect the cooler filter for impurities.
- Check the laser cooling water circuit for impurities.
- Be sure to check the condensed water level of the compressed air separator (located in the air supply unit).
- Inspect the vacuum pump oil level, located under the air supply unit. When the pump is cold, the oil level should be between + 5 mm – 0 mm from the midline of the oil window. Add more oil if necessary.
- Lastly, check the Roots pump oil level. You can see the oil level in the Roots pump gearbox through the oil window on the end face of the gearbox. When the pump is off and cold, the oil level should be between + 5mm and 0mm from the center line of the glass. If necessary, add HTCL2100 oil.
8. Semi-annual laser maintenance (or after 2,000 hours of operation)
- Check the laser head cooling water pipe for signs of corrosion. If you find any, replace or process them immediately.
- Check whether the excitation source fuel tank is leaking.
- Check whether the high voltage cable is damaged.
- Clean the inside of the laser cavity and all lenses, including the front window mirror, rear mirror and reflector.
- After the laser's inner lens is clean, adjust the light output mode until the correct mode is achieved.
- Replace the vacuum pump oil.
- Replace the Roots pump oil.
- Carefully tighten all plugs to ensure the Roots pump is airtight.
- Clean the white plastic plug on the outlet end of the Roots pump gas divider and apply a thin layer of silicone-free high vacuum silicone grease to its inner surface. The purpose of this grease is to adsorb and capture physical impurities in the circulating laser gas.
10. Chiller maintenance
Regular maintenance is essential for your chiller to ensure it operates efficiently. In the event of a malfunction, it is essential to seek the help of a professional technician for repairs. It is strictly prohibited to disassemble the machine by yourself.
Here are some important aspects to consider during daily chiller maintenance:
- Regular cleaning of the heatsink is required. The cleaning process involves carefully brushing the heatsink and blowing it with compressed air. If necessary, clean and rinse the heat sink with water and a special air conditioning fin cleaner, commonly known as polyester powder.
- The condenser should also be cleaned regularly using the same process mentioned above.
- Regularly check the water level in the refrigerator water tank. In case of low water level, immediately add pure water or deionized water.
- Check electrical terminals frequently and remove dust (be sure to turn off the power first).
- Regularly check water system joints for leaks and aging piping. In case of leakage, immediately replace the relevant components.
- Regularly check the water quality in the refrigerator water tank. If the quality of the cooling water deteriorates and the turbidity and transparency decrease, the cooling water must be replaced immediately. Discard all spoiled water and replace it with fresh cooling water.
- Regularly clean the filter element of impurities. If the filter element is damaged, replace it immediately. It is essential to use the standard filter element required by the manufacturer.
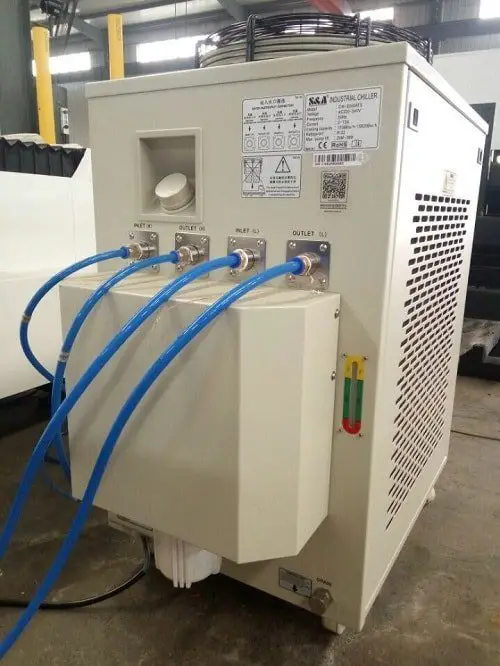
11. Air compressor maintenance
- Before carrying out any maintenance operations, make sure the air compressor is turned off and the compressed air from the gas storage tank is drained.
- It is recommended to drain the water from the system 3 to 8 times a day, depending on the humidity level in the air. After completing the work, it is necessary to drain the air and water from the gas tank.
- Clean the air filter every two weeks or reduce the cleaning cycle if the work environment is harsh.
- Replace the filter element after 1200 hours of operation. It is also necessary to check and clean all parts and replace the valve disc if necessary.
- After every 1000 hours of operation, the oil-free air compressor must be filled with grease for the crankshaft bearing in the compressor head.
- Always consult the air compressor manual for guidance.
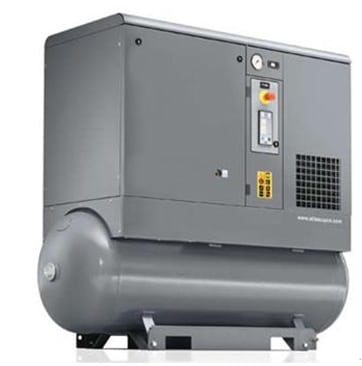
12. Air dryer maintenance
- Depending on the humidity in the air, it is necessary to drain the refrigeration dryer 3 to 8 times a day and remove the accumulated air and water after work.
- Clean the air filter element once a month to ensure proper function.
- Once a month, remove and clean the condenser cooling fins to prevent dust or debris from accumulating.
- Replace the air filter element every six months to maintain filtered air quality.
13. Regulated Power Supply Maintenance
- After one month of operation of the new regulated power supply, turn off the main power supply and tighten all regulator connection terminals, paying special attention to the main circuit.
- Check the elasticity of the sliding carbon brush every three months and use dry compressed air to remove any toner or dust that has adhered to the regulator components.
What are the detailed steps for daily inspection and cleaning of a laser cutting machine?
The steps for daily inspection and cleaning of a laser cutting machine include the following aspects:
Daily laser maintenance:
Before starting each day, laser maintenance is required, including checking the working gas and laser cutting gas cylinders, ensuring that the cooling water pressure is maintained between 3.5 to 5 bar, checking that the temperature of the cooling water meets the requirements of the selected laser by inspecting the oil level in the laser vacuum pump and checking for leaks in the laser oil, water and gas lines as well as the vacuum pump, pneumatic components resonator and tube joints.
Lens cleaning:
For laser cutting machine lenses, especially focusing lenses and reflective lenses, it is recommended to clean the focusing lenses after each daily use and clean the reflective lenses and laser beam combiner lenses at least once a week.
The correct cleaning method includes blowing off the surface particles of the original parts with a blow balloon, gently wiping the lens with analytically pure acetone, and if acetone cannot remove all the dirt, vinegar can be used for cleaning. When lens contaminants and damage cannot be eliminated and removed, lens replacement is the only way to restore optimal performance.
Inspection of other machine parts:
Before starting the machine, it is also necessary to carefully inspect the entire bed, check the cleanliness of the lenses, perform coaxial debugging of the laser cutting machine, and check the condition of the cooler.
In addition, after completing daily work, the drain valve at the bottom of the air compressor gas storage tank must be opened for drainage, the drain valve must be closed after discharging the wastewater, and the machine must be turned off by following the shutdown procedure, then the total power of the entire machine must be turned off.
Cleaning guide rails and linear axes:
It is recommended to clean the guide rails and linear axes once every six months, which must be done with the machine turned off.
How to properly maintain the rails and guide rails of a laser cutting machine to ensure their straightness and verticality?
To properly maintain the rails and guide rails of a laser cutting machine and ensure their straightness and verticality, the following steps and care must be followed:
Regular inspection:
First, it is essential to regularly check that the X, Y and Z axes of the machine tool can return to the origin and that the steel belt remains under tension. This helps to promptly identify and resolve any issues that may cause deviations from straightness and verticality.
Use of professional tools:
For detection of straightness errors of guide rails, an optical collimator can be used to detect the straightness error of the guide rail in the vertical and horizontal planes. Although this method is highly accurate, it is complex to set up and adjust, so it is advisable to have professional measurement personnel operate it.
Additionally, tools such as adjustment screws, magnetic adjusters and laser measuring instruments can be used to adjust parameters such as installation position, parallelism and verticality of the guide rail.
Calibration process:
When adjusting the angle of the linear guide rail, the adjusted guide rail should be based on the guide rail that has been ground to minimize the least squares error between the adjusted guide rail and the base guide rail.
During the calibration process, the actual parameters of the guide rail must be measured and recorded for subsequent accurate adjustments.
Maintenance and debugging:
If any abnormalities are found in the straightness of the track or the verticality of the machine during the inspection process, timely maintenance and debugging should be carried out.
Comprehensive use of various measurement methods:
To obtain a comprehensive straightness characteristic, equipment with high measuring resolution can be used, such as the Swiss RAYTEC laser collimator. It can capture the displacements in the X and Y directions simultaneously.
What are the best practices for managing a laser cutting machine's cooling system and water tank?
Best practices for managing a laser cutting machine's cooling system and water tank include the following points:
Regularly clean the water tank and replace the circulating water:
To maintain the normal operation of the laser cutting machine and extend its service life, it is necessary to regularly clean the water tank and replace the circulating water.
Specific operations include turning off the power, disconnecting the water inlet tube, letting the water from the laser tube automatically flow into the water tank, and then opening the water tank to take out the water pump, remove the dirt in the water pump and replace the circulating water after cleaning the water tank.
Use a closed-loop cooling system with dual temperature control system:
To maintain the optimal performance of the fiber laser cutting machine, a closed-loop cooling system with a dual temperature control system can be adopted, which has excellent performance in keeping the fiber laser cutting machine cool.
Pay attention to the ion exchange column in the refrigeration system:
During prolonged use, you should always observe the status of the ion exchange column in the cooling system to ensure the effective operation of the cooling system.
Winter maintenance:
In the event of a strong cold snap or prolonged non-use of the laser cutting machine, attention should be paid to the overcurrent components in the cooling system to ensure that the equipment can operate optimally even in severe cold environments.
Empty the cooling water:
Before turning off the laser cutting machine, you must actively empty the cooling water with the water chiller to avoid problems caused by water freezing.
What are the specific methods and cycles for maintaining the laser head and lens of the laser cutting machine?
The methods and cycles for maintaining the laser head and laser cutting machine lens mainly include the following points:
Fiber head installation method:
It must be operated in a clean environment, and the fiber head must be installed horizontally on the cutting head and locked to prevent dust from rising. The correct installation method can delay lens aging and minimize lens wear.
Check before daily use:
Check whether the laser is emitted from the center of the nozzle to ensure the normal output and cutting accuracy of the laser.
Maintenance cycle:
The lenses must be cleaned daily to maintain the cleanliness and good working condition of the optical lenses.
Furthermore, to replace the cooling water and clean the water tank, it is recommended to do so every six months or before replacing equipment that has not been used for a long time.
What special maintenance measures should be taken for the laser cutting machine in special seasons (such as summer)?
Special maintenance measures for laser cutting machine in special seasons such as summer mainly include the following points:
Check and maintain the cooling system:
Due to the increase in temperature in summer, the working pressure of the laser cutting machine's cooling system increases. It is recommended to check the refrigerator's internal pressure before heat arrives and consult the equipment manufacturer for specific parameters.
In addition, the chiller must be checked and maintained regularly to prevent laser condensation in summer.
Use normal distilled water or pure water:
In summer, due to the higher temperature, the deterioration rate of the cooling water will also accelerate, so it is recommended to use ordinary distilled water or pure water, and clean the scale regularly to prevent the laser power from being affected by the fixed scale inside the laser and the pipeline.
Replace and clean the cooling water:
It is recommended that customers clean the water tank scale, replace water and filter regularly, especially in summer, to keep the cooling system clean and efficient.
Prevent the laser from condensing:
To prevent the main component of the laser cutting machine – the laser from condensing, the water temperature of the chiller can be set to 28℃ and ensure that the independent space environment where the laser is placed is below 35℃ and the environment humidity is below 60℃.