A indústria de fabricação de máquinas abrange uma ampla gama de setores, incluindo transporte, máquinas-ferramentas, máquinas agrícolas, máquinas têxteis, máquinas elétricas e instrumentos de precisão. Em geral, o processo produtivo envolve oficinas de fundição, forjamento, tratamento térmico, usinagem e montagem.
O fluxo básico de produção consiste em fundição, forjamento, tratamento térmico, usinagem e montagem. No processo de fabricação de máquinas, as peças metálicas são normalmente criadas por meio de fundição, forjamento, soldagem, estampagem e outros métodos, seguidos de corte para produzir peças qualificadas e, finalmente, montadas em uma máquina.
Usinagem é o uso de várias máquinas-ferramentas para realizar operações como torneamento, aplainamento, furação, retificação, fresamento e outros processamentos a frio em peças metálicas.
A avaliação e detecção de riscos ocupacionais são cruciais na indústria de máquinas, particularmente no setor de fabricação de máquinas. Existem muitos perigos potenciais nesta indústria e os pontos a seguir destacam alguns dos fatores que requerem atenção.
Ófatores de risco ocupacional
1. Forjamento
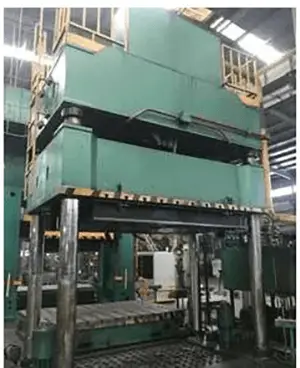
Forjamento é um processo no qual uma força externa é aplicada a uma peça bruta, causando deformação plástica e resultando em forjamento.
Riscos físicos:
O ruído é o risco ocupacional mais prejudicial no processo de forjamento. Martelos de forjamento (martelos pneumáticos e martelos de pressão) podem gerar ruídos e vibrações fortes e intensos, geralmente na forma de ruído impulsivo, com intensidade superior a 100dB (A). Uma detecção de ruído realizada na oficina de forjamento de uma fábrica de máquinas apresentou resultados variando de 83 a 100,2dB(A), com média de 92,08dB(A). Máquinas de puncionamento e máquinas de corte também podem produzir ruído de alta intensidade, mas a intensidade é normalmente menor do que a dos martelos de forjamento.
A temperatura no forno de aquecimento pode chegar a 1200°C, enquanto a temperatura de forjamento está entre 500-800°C. Durante a produção, altas temperaturas e forte calor radiante podem ser produzidos no local de trabalho.
Riscos de poeira e veneno:
Pó de metal e pó de carvão podem ser gerados durante a carga, descarga e forjamento no forno de forjamento e no martelo de forjamento, particularmente nos fornos da indústria de combustíveis. Os fornos de combustão podem emitir gases nocivos, como monóxido de carbono, dióxido de enxofre e óxidos de nitrogênio.
2. Fundição
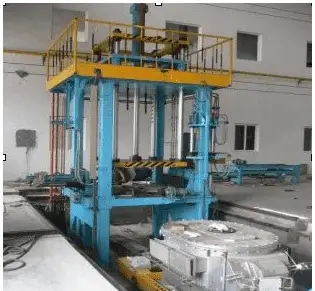
A modelagem pode ser dividida em moldagem manual e mecânica. A moldagem manual envolve a conclusão do aperto da areia, remoção do molde, corte e fechamento da caixa manualmente. Esse processo tem alta intensidade de trabalho e expõe os trabalhadores diretamente à poeira, venenos químicos e fatores físicos, levando a riscos ocupacionais significativos. Por outro lado, a moldagem mecânica apresenta alta produtividade, qualidade estável, baixa intensidade de trabalho para os trabalhadores e menos chances de os trabalhadores entrarem em contato com poeira, venenos químicos e fatores físicos, resultando em riscos ocupacionais relativamente pequenos.
Perigo de poeira:
Uma quantidade significativa de pó de areia é produzida durante a moldagem, queda da areia de fundição e limpeza. A natureza e os danos do pó são determinados principalmente pelo tipo de areia de moldagem utilizada. Por exemplo, quando se utiliza areia de quartzo, ela é mais prejudicial devido ao seu alto teor de sílica livre. Uma detecção de concentração de poeira realizada na oficina de moldagem de uma fábrica de máquinas encontrou resultados variando de 27,5 a 62,3mg/m3com média de 39,5mg/m3.
Venenos e perigos físicos:
A secagem, fusão e vazamento do carvão do molde de areia e do núcleo de areia resultam em alta temperatura e radiação de calor. Se carvão ou gás for usado como combustível, ele produz monóxido de carbono, dióxido de enxofre e óxidos de nitrogênio. Se fornos de indução de alta frequência ou fornos de micro-ondas forem usados para aquecimento, serão produzidos campos eletromagnéticos de alta frequência e radiação de micro-ondas.
3. Tratamento térmico
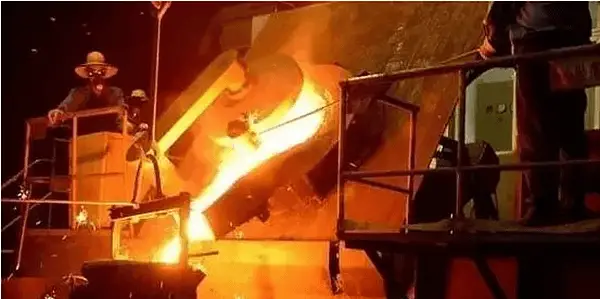
O objetivo principal do processo de tratamento térmico é alterar as propriedades físicas do metal, como dureza, tenacidade, elasticidade, condutividade, entre outras, preservando ao mesmo tempo a forma das peças. Isso visa atender aos requisitos do processo e melhorar a qualidade do produto.
O processo de tratamento térmico abrange normalização, têmpera, recozimento, revenido e cementação.
O tratamento térmico pode ser classificado em três categorias: tratamento térmico geral, tratamento térmico superficial (que inclui têmpera superficial e tratamento térmico químico) e tratamento térmico especial.
Gás tóxico
Os processos de tratamento térmico de peças mecânicas, incluindo normalização, recozimento, cementação, têmpera e outros, requerem uma ampla gama de materiais auxiliares, como ácidos, álcalis, sais metálicos, nitratos e cianetos.
Esses ingredientes são substâncias altamente corrosivas e tóxicas que podem representar uma ameaça significativa ao meio ambiente e à saúde humana.
Por exemplo, quando o cloreto de bário é utilizado como meio de aquecimento e a temperatura atinge 1300°C, uma grande quantidade de cloreto de bário evapora, criando poeira de cloreto de bário que contamina o ar da oficina.
O processo de cloração também libera uma quantidade substancial de amônia no ar da oficina.
O ferrocianeto de potássio e outros cianetos são utilizados nos processos de cementação e cementação, enquanto os óxidos de nitrogênio são produzidos através da interação do nitrato fundido e da mancha de óleo com a peça em um forno de banho de sal.
Além disso, agentes orgânicos como metanol, etanol, propano, acetona e gasolina são frequentemente empregados no processo de tratamento térmico.
Riscos físicos
A normalização e o recozimento de peças mecânicas são processos de tratamento térmico realizados em altas temperaturas. Fornos de aquecimento, banhos de sal e peças aquecidas na oficina são fontes de calor.
Estas fontes de calor podem criar um ambiente de alta temperatura com forte radiação térmica.
Além disso, vários motores, ventiladores, bombas industriais e outros equipamentos mecânicos podem gerar ruído e vibração. No entanto, o nível de ruído na maioria das oficinas de tratamento térmico é baixo e são raros os casos em que o ruído excede os padrões.
4. Usinagem
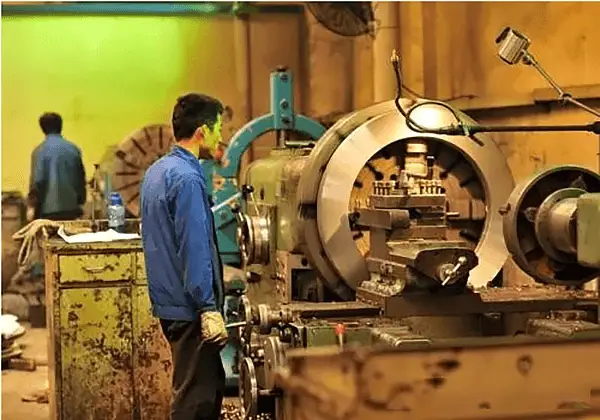
No processo de fabricação mecânica, as peças metálicas são fabricadas por meio de fundição, forjamento, soldagem, estampagem e outras técnicas. Em seguida, várias máquinas-ferramentas, como tornos, plainas, furadeiras, retificadoras, fresadoras e outras, são utilizadas para realizar o processamento a frio nas peças metálicas, incluindo torneamento, aplainamento, furação, retificação e fresamento. Por fim, as peças qualificadas são cortadas e montadas em máquinas.
Usinagem geral
Os riscos ocupacionais no processo produtivo são mínimos, principalmente devido ao uso de emulsões de corte e ao impacto do corte nos trabalhadores.
As emulsões de corte comumente usadas consistem em óleo mineral, ácido naftênico ou ácido oleico e álcali (soda cáustica). A transferência em alta velocidade de máquinas-ferramentas pode causar respingos de emulsão, que podem facilmente poluir a pele e causar doenças de pele como foliculite ou acne.
Durante o processo de usinagem, também há uma quantidade significativa de pó metálico e mineral gerado no desbaste grosseiro e fino. As pedras de amolar sintéticas são compostas principalmente de esmeril (cristal de alumina), com baixo teor de dióxido de silício, enquanto as pedras de amolar naturais contêm grande quantidade de dióxido de silício livre, o que pode resultar em pneumoconiose e silicose por alumínio.
A maioria das máquinas-ferramentas produz ruído mecânico que varia entre 65 dB (A) e 80 dB (A), e casos de ruído excessivo são raros.
Usinagem especial
Os fatores de risco ocupacional na usinagem especializada estão relacionados principalmente às ferramentas de usinagem utilizadas.
Por exemplo, a EDM produz pó metálico, o processamento a laser gera altas temperaturas e radiação ultravioleta, o raio X por feixe de elétrons gera pó metálico, o processamento por feixe de íons produz pó metálico, radiação ultravioleta e radiação eletromagnética de alta frequência, e se um eletrodo de tungstênio for utilizado , a radiação ionizante também pode estar presente.
Por outro lado, a usinagem eletroquímica, a usinagem a jato líquido e a usinagem ultrassônica apresentam riscos relativamente menores.
Além disso, a operação do equipamento também pode gerar ruído e vibração.
5. Montagem mecânica
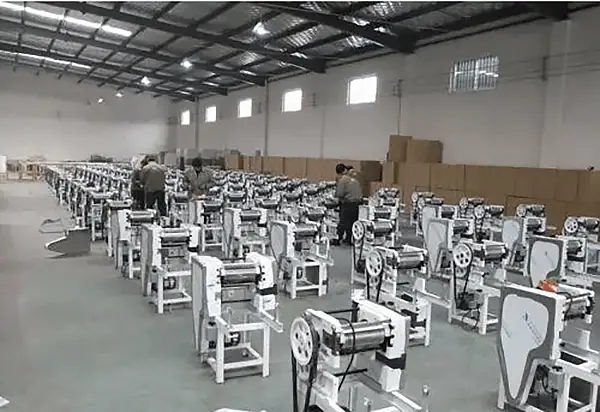
Os fatores de risco ocupacional em processos de montagem mecânica simples são poucos e semelhantes aos da usinagem geral.
No entanto, em processos de montagem complexos, os riscos ocupacionais estão principalmente relacionados com as técnicas específicas de montagem utilizadas.
Por exemplo, a utilização de diversas técnicas de soldadura pode resultar em riscos profissionais relacionados com a soldadura, enquanto a utilização de adesivos pode resultar em riscos profissionais relacionados com os adesivos. Se for necessário um processo de revestimento, também podem existir riscos ocupacionais associados ao processo de revestimento.
Medidas protetoras
Os riscos ocupacionais na indústria de fabricação de máquinas incluem principalmente os perigos do pó de silício na produção de fundição, solventes orgânicos como o benzeno e seus derivados na produção de revestimentos e pó de soldagem (fumaça) em operações de soldagem. Para enfrentar esses perigos, as seguintes medidas devem ser tomadas:
- Layout razoável da oficina: Na concepção da oficina, devem ser feitos esforços para minimizar a poluição cruzada de riscos ocupacionais. Por exemplo, o forno de fundição deve estar localizado ao ar livre ou longe de áreas movimentadas, e os processos de rebitagem, soldagem e pintura devem ser separados.
- Controle de poeira: Areia de moldagem com baixo teor de sílica livre deve ser usada sempre que possível, e a moldagem manual e a limpeza da areia devem ser reduzidas. A limpeza de areia é o processo com maior concentração de poeira na produção de fundição e deve receber atenção especial. Isto pode ser conseguido através da instalação de sistemas de ventilação e remoção de poeira de alta potência e da realização de operações de pulverização úmida para reduzir a concentração de poeira no ar do local de trabalho. Os trabalhadores também devem usar máscaras contra poeira que atendam aos padrões nacionais relevantes.
- Antivírus e resposta de emergência: Devem ser instaladas medidas de vedação ou dispositivos de ventilação local para equipamentos que possam produzir toxinas químicas nos processos de tratamento térmico e fundição de metais. Em locais de trabalho que produzem gases altamente tóxicos, como monóxido de carbono, cianeto de hidrogênio, formaldeído e benzeno (por exemplo, certos processos de têmpera, pintura e colagem), devem ser implementados planos de resposta de emergência para intoxicações ocupacionais agudas, devem ser afixados sinais de alerta e máscaras de gás ou respiradores devem ser fornecidos.
- Controle de ruído: O ruído é um risco ocupacional significativo na indústria de fabricação de máquinas e pode ser controlado reduzindo o ruído de alta intensidade de equipamentos como martelos pneumáticos, compressores de ar, retificadoras, polidoras, máquinas de estampagem e equipamentos de corte. As fontes de ruído de alta intensidade devem ser centralizadas e devem ser utilizadas proteções de isolamento acústico. As fontes de ruído aerodinâmico devem ser abafadas na entrada ou na saída. Tratamentos de isolamento acústico e absorção devem ser aplicados em salas de controle e salas de pós-operatório. Os trabalhadores que entrem em locais de trabalho com intensidade sonora superior a 85dB(A) deverão utilizar tampões auriculares ou protetores auriculares antirruído.
- Controle de vibração: A vibração é um risco ocupacional comum na indústria de fabricação de máquinas. Devem ser tomadas medidas para reduzir a vibração ou implementar operações rotacionais para equipamentos como máquinas de rebitagem, prensas de forjamento, compactadores de areia para moldagem, sistemas de queda de areia e máquinas de limpeza de areia.
- Proteção de radiofrequência: Materiais de blindagem apropriados devem ser usados para proteger equipamentos que produzam radiações de alta frequência, micro-ondas e outras radiações de radiofrequência. Isolamento de distância e proteção de tempo também devem ser fornecidos.
- Prevenção de insolação: Devem ser tomadas medidas eficazes de prevenção e resfriamento do calor no verão para trabalhadores em ambientes de alta temperatura, como fundição, forjamento e tratamento térmico. Isto pode ser conseguido através de uma combinação de tecnologia de engenharia, cuidados de saúde e medidas de organização e gestão do trabalho, tais como a disposição racional de fontes de calor, fornecimento de bebidas frescas e salgadas, operações rotativas e ar condicionado em salas de controlo e salas de operação.