Introducción
En 2013, el taller de componentes estructurales de la empresa presentó dos máquinas de corte por láser de CO2 Trumpf, modelo CP3000.
Debido a la falta de experiencia en mantenimiento y reparación de este tipo de equipos, la mayoría de las averías dependían del servicio postventa del fabricante, lo que se traducía en largos ciclos de reparación y elevados costes de mantenimiento.
Al analizar las causas de las fallas, se formularon medidas correctivas y preventivas y se creó un Informe de fallas de equipos A4 para prevenir fallas futuras.
Durante este proceso se acumuló continuamente experiencia en mantenimiento y se mejoraron las habilidades del personal de mantenimiento de equipos, logrando paulatinamente una transición de un mantenimiento tercerizado a un modelo autosuficiente + mantenimiento tercerizado.
1 Reparación de averías “Caída de tensión alta”
1.1 Descripción del fallo:
Durante el proceso de corte, el monitor láser mostró repentinamente una alarma “2104”, que indicaba que había una “alta caída de voltaje”.
Después de reiniciar el equipo, funcionó normalmente, pero posteriormente ocurrieron alarmas intermitentes durante el proceso de corte y la frecuencia de las alarmas aumentó.
1.2 Análisis de Causas:
Según el principio de funcionamiento del láser, existen cinco causas posibles para esta alarma.
(1) Impurezas en gases de alta pureza, especialmente exceso de agua. La humedad que ingresa a la cavidad resonante hará que disminuya la resistividad del plasma en la cavidad, lo que resultará en un aumento anormal en la corriente de suministro de energía de alto voltaje.
(2) Fuga en la cavidad resonante, con aire ambiental entrando en la cavidad. Cuando la cavidad resonante funciona normalmente, se trata de un entorno de presión negativa. Si hay un punto de fuga, el aire ambiente entrará en la cavidad.
(3) Fuga del intercambiador de calor o de su anillo de sellado, lo que permite que el agua de refrigeración entre en la cavidad resonante.
(4) Proporción incorrecta de mezcla de gases. Una proporción de mezcla incorrecta puede provocar una disminución de la potencia del láser, y el láser aumentará la potencia al aumentar adecuadamente la corriente de alto voltaje de la fuente de alimentación. Cuando la corriente de alto voltaje excede un cierto rango, se producirá una alarma.
(5) Retorno de la bomba de vacío. Si la válvula unidireccional de la bomba de vacío no está sellada herméticamente, el gas residual con vapor de aceite regresará a la cavidad resonante, contaminando componentes ópticos como lentes sucias y provocando una disminución en la potencia.
1.3 Solución de problemas:
(1) El gas se cambió a otro láser y se usó normalmente, descartando impurezas en el gas como causa.
(2) Se evacuó la cavidad resonante por debajo de 1 kPa (10 mbar), se cerraron todas las válvulas solenoides y después de 20 minutos la presión aumentó en 40 Pa (0,4 mbar), cumpliendo con los requisitos del fabricante del equipo, descartando fugas y fugas en el intercambiador de calor. como la causa.
(3) Se verificó y reajustó la proporción de mezcla de gases. Después del ajuste, la falla persistía y la frecuencia no disminuyó, descartándose como causa una proporción incorrecta de la mezcla de gases.
(4) Se ha retirado y limpiado de manchas de aceite la tubería entre la bomba de vacío y la cavidad resonante. Antes de desmontar el espejo delantero, el espejo trasero y el espejo plegable, se limpiaron, reinstalaron y ajustaron. Sin embargo, la falla aún existía, lo que eliminó el reflujo de la bomba de vacío como causa.
1.4 Solución de problemas adicionales:
Se realizaron análisis y solución de problemas del estado operativo del equipo. Durante el proceso de corte real, se observó que antes de que ocurriera la alarma de "caída de alto voltaje", la potencia aumentó repentinamente a aproximadamente 1200 W, luego se produjo la alarma.
Se activó el modo “calefacción” y se aumentó gradualmente la potencia de calefacción. Cuando el ajuste de potencia alcanzó los 1500 W, la potencia de salida medida fue de sólo 1200 W y hubo un fenómeno de "filamentación" en la cavidad resonante 1#.
Después de funcionar durante unos 20 segundos, el láser dio una alarma de "alta caída de voltaje" y la fuente de alimentación dio una alarma de "sobrecorriente". Se revisó la electrónica de la fuente de alimentación del láser y se encontró que estaba normal.
La salida de voltaje de detección de la cavidad resonante 1# se midió en la placa de circuito de monitoreo de energía (Figura 1), que fue de 8,4 V, mientras que el voltaje de la cavidad resonante 2# fue de aproximadamente 7,6 V, lo que indica que la fuente de alimentación de refuerzo sumergida en aceite de la cavidad resonante 1# ha sido dañada.

Se desmontó la unidad de fuente de alimentación sumergida en aceite (Figura 2) y se midieron los componentes electrónicos como el transformador, el condensador de refuerzo y el diodo de refuerzo de la fuente de alimentación de refuerzo de cavidad resonante 1#, y todos se consideraron normales.
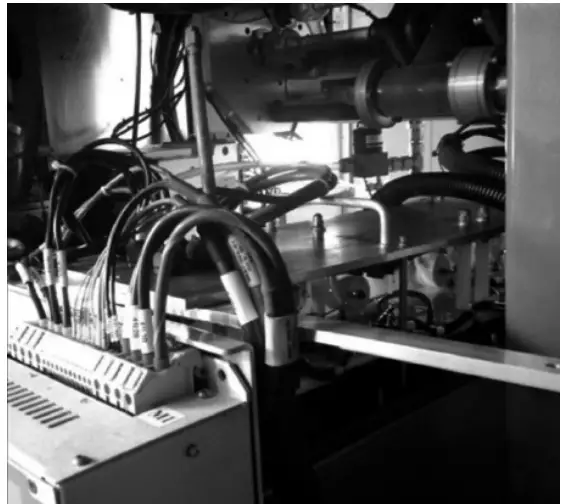
Se midió el circuito de detección de reducción de voltaje y se encontró que una de las resistencias redundantes de 100 k tenía un valor medido de 116 kΩ. Se juzgó preliminarmente que el motivo de la alarma de "alta caída de voltaje" se debió al daño de esta resistencia.
1.5 Medidas de emergencia:
Se quitó una resistencia de 100 kΩ y 2 W de otra placa de circuito vieja y se usó para reemplazar la resistencia dañada. Se activó el modo “calefacción” y se fue aumentando gradualmente la potencia hasta alcanzar la potencia máxima de 3000W.
Se observó el estado de funcionamiento del láser, no se produjo ninguna alarma de "caída de alto voltaje" y tampoco hubo ningún fenómeno de "filamentación".
1.6 Análisis de las verdaderas causas:
(1) Se probaron las 16 resistencias reductoras de voltaje en dos máquinas láser y sus valores de resistencia fueron un 5% más altos de lo normal. Estas resistencias son resistencias de película de carbono, que tienen baja potencia y se oxidan fácilmente con choques de voltaje, aumentando gradualmente su valor de resistencia.
Por lo tanto, se consideró que el uso de resistencias de película de carbono en el diseño de placas de circuito no era razonable y se deberían utilizar resistencias de película metálica más estables y resistentes a los impactos.
(2) Otros problemas descubiertos durante el proceso de resolución de problemas incluyeron una gran desviación entre la proporción de la mezcla de gases y la configuración de fábrica, así como una sustitución y uso inadecuados de gas de alta pureza.
1.7 Medidas correctivas y preventivas:
(1) Compre resistencias de película metálica de 100 kΩ y 2 W para reemplazar las defectuosas y evitar este tipo de fallas.
(2) Modificar el manual de operación y mantenimiento, agregar verificaciones periódicas de voltaje y corriente para el suministro de energía, ajustar la proporción de mezcla de gas y agregar elementos de inspección y ajuste regulares. Los procedimientos operativos de ventilación estándar y los requisitos de uso deben desarrollarse y difundirse mediante capacitación.
(3) Inspecciones por parte de terceros de los gases de alta pureza (N2, CO2, He2) utilizados en la máquina láser, y el proveedor debe rectificar cualquier problema de incumplimiento dentro de un plazo específico.
Resolviendo el problema de la frecuente colisión entre el cabezal de corte y la chapa.
2.1 Descripción del problema:
(1) Debido a la frecuente deformación de la chapa, el cabezal de corte de la máquina de corte por láser choca con la chapa deformada, causando daños a componentes como el cabezal capacitivo, el cuerpo cerámico, la boquilla de corte y el componente de cuatro enlaces.
Después de la colisión, la sustitución de piezas de repuesto y el ajuste de equipos provocan una pérdida de tiempo considerable que retrasa la producción.
(2) En 2018, se produjo una pérdida total de 103 000 RMB debido a daños por colisión de componentes, que se detallan en la Tabla 1 (no se incluyen las pérdidas por tiempo de inactividad).
Tabla 1: Estadísticas de pérdidas provocadas por dos colisiones de láser en 2018.
Componente dañado | Cantidad /partes |
Precio unitario /10.000 yuanes |
Cantidad total /10.000 yuanes |
Comentarios |
Cabeza del condensador | 6 | 0.3 | 1.8 | Para ser utilizado después de la reparación por parte de terceros. |
Cabeza del condensador | dos | dos | 4 | No se puede reparar, necesito comprar. |
Junta de aislamiento | 1 | 0 | 0 | repuesto nuevo |
Cuerpo cerámico | 20 | 0,02 | 0,4 | Salir adelante por sí mismo |
2.2 Análisis de causa raíz
Analizar las posibles causas de los cinco elementos: personas, máquina, material, método y entorno.
(1) Personas: el nuevo empleado no domina la operación y no puede manejar ni lidiar con la deformación de la chapa a tiempo. El operador tiene poco sentido de responsabilidad y no se ocupa de situaciones en las que pueden producirse colisiones. Después de la colisión, el coaxial no se reajustó, lo que provocó la desviación del rayo láser y la quema del cabezal del condensador; el seguimiento no se ajustó a tiempo, lo que provocó otra colisión.
(2) Máquina: la respuesta del movimiento del cabezal de corte ante una colisión no es lo suficientemente sensible y no se puede detener a tiempo cuando se produce una colisión, lo que conduce a una expansión de los accidentes.
(3) Materiales: La tensión interna de la placa es grande y la placa se deforma debido a la liberación de tensión causada por el calentamiento durante el corte.
(4) Método: no se presta suficiente atención al ajuste de la trayectoria de corte y no se consideran las piezas propensas a deformarse para evitarlas en la medida de lo posible; No se utilizan microconexiones.
(5) Medio ambiente: Los estantes de almacenamiento de placas cortos, el largo tiempo de almacenamiento y el pisoteo del personal hacen que las placas se doblen, lo que las hace fáciles de deformar durante el corte.
2.3 Medidas de Investigación y Rectificación
(1) Capacitar y evaluar a todos los operadores y establecer el correspondiente sistema de recompensa y castigo.
(2) Ajuste la sensibilidad de la respuesta del movimiento de colisión al nivel más alto sin afectar el uso.
(3) Alise la placa antes de colocar la máquina para liberar parte de la tensión interna.
(4) Optimizar la ruta de corte durante la programación y el diseño, evitando piezas que puedan deformarse; Utilice microconexiones para reducir la probabilidad de deformación de la pieza.
(5) Extienda la rejilla para guardar platos para evitar que se hunda y se doble en ambos extremos; rediseñar el área de almacenamiento de placas, instalar barreras para evitar que el personal camine y pise.
Después de implementar las medidas anteriores, la frecuencia de los problemas de colisión ha disminuido ligeramente, pero el problema no se ha resuelto por completo.
2.4 Análisis de vídeos y fotografías para investigación
(1) La causa fundamental del problema que no se ha resuelto durante mucho tiempo es que el personal profesional no está en el lugar cuando ocurren las colisiones y es imposible restaurar la situación en ese momento.
Posteriormente, al instalar monitoreo en el equipo y tomar fotografías después de cada colisión, analizando datos de video y fotografías, se encontró que las colisiones ocurrieron durante la ruta vacía desde el final de un corte hasta el punto de inicio del siguiente corte.
Antes de la operación en vacío, el cabezal de corte se elevará una cierta distancia (altura de elevación).
Intentando aumentar la altura de elevación, el problema se puede solucionar.
(2) Estudiar el programa de control. Al observar el programa de corte, se descubrió que la elevación del cabezal de corte durante la operación sin carga está controlada por las subrutinas 1012 y 1022. Abra la subrutina para analizar el principio de control.
(3) Principio de control de la altura del cabezal de corte. Utilice un sensor para detectar y calcular la distancia a la altura de la placa. Cuando se requiere una operación sin carga, el eje Z se mueve en dirección negativa hasta que se detiene cuando la altura de detección es de 10 mm y luego realiza una acción de operación sin carga.
2.5 Análisis de causa raíz
(1) Existen las siguientes deficiencias en este método de control: el sensor solo puede detectar con precisión una distancia de 10 mm. Cuanto mayor es la distancia, mayor es el error. No puede evitar colisiones y solo puede dejar de funcionar después de que se produce una colisión.
Al utilizar el control PID, existe el problema del retraso en la respuesta cuando ocurre una colisión, lo que conduce a una expansión de los accidentes por colisión. Solo puede detectar la situación en la que la caída de altura de la placa cambia uniformemente, pero no puede detectar la situación en la que la caída de altura de la placa cambia repentinamente.
(2) Según las fotografías de la escena de la colisión tomadas por el operador (Figura 3), se establece un modelo numérico (Figura 4) para analizar la ocurrencia de colisiones: la colisión ocurrirá cuando el punto se mueva en cualquier dirección, y el La colisión ocurrirá cuando el punto b se mueva hacia la izquierda.
(3) Según el modelo numérico, el cálculo muestra que la altura máxima de elevación o hundimiento de la pieza es de 30 mm y la altura de elevación se establece en 10 mm, lo que no puede evitar completamente las colisiones. Sin embargo, actualmente este método de control no puede establecer la altura de elevación en más de 10 mm.
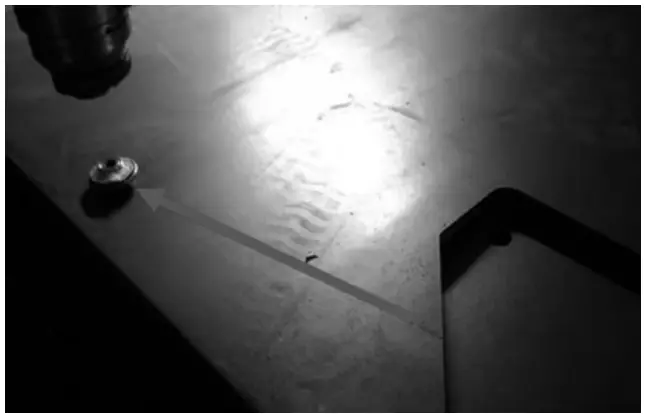
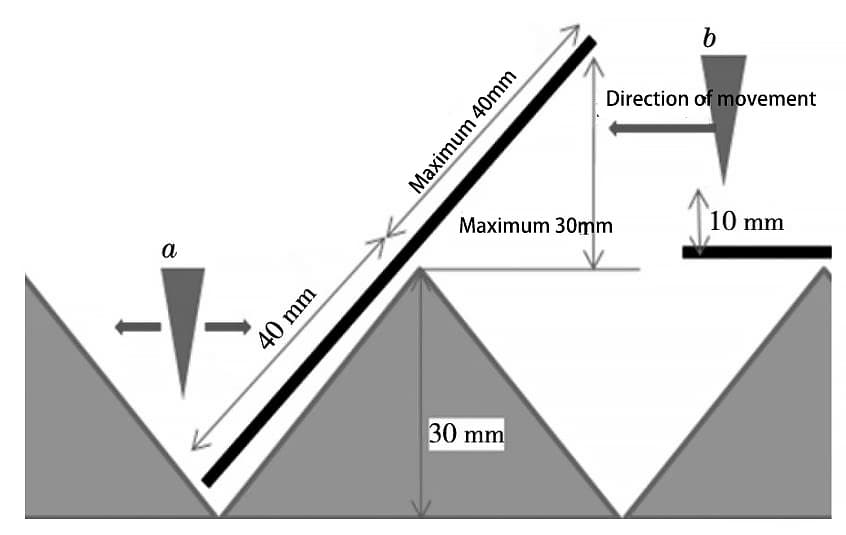
2.6 Medidas Correctivas y Preventivas
(1) Desarrollar un plan de ajuste. Ajuste la subrutina Máquina n.° 1, elimine el movimiento del eje Z a la posición de detección del sensor de 10 mm y cámbielo a: El eje Z se mueve 35 mm en dirección negativa, ya no usa el control seguidor del sensor y funciona sin anomalías durante la ejecución de prueba. Después de 24 horas de operación continua sin colisiones ni anormalidades, ajuste el programa para la Máquina #2.
(2) Validar la viabilidad. Registre la tasa de carga del servomotor del eje Z antes y después del ajuste, la diferencia máxima de la tasa de carga antes y después del ajuste es muy pequeña y ambas no superan el 30%.
(3) Verificación. Ha estado funcionando continuamente hasta la fecha (4 meses) sin fallas ni anomalías.
Conclusión
La falla de "alta caída de voltaje" y la colisión del cabezal de corte de la máquina de corte por láser de CO2 afectan gravemente la eficiencia de la producción y causan pérdidas sustanciales. Analizando la causa del fallo, descartando fallos, identificando la causa real e implementando medidas correctoras y preventivas, se evitan por completo fallos similares. Al estudiar la estructura y el principio del equipo y resumir las experiencias de reparación, hemos logrado la reparación autónoma de algunas fallas de estos equipos.